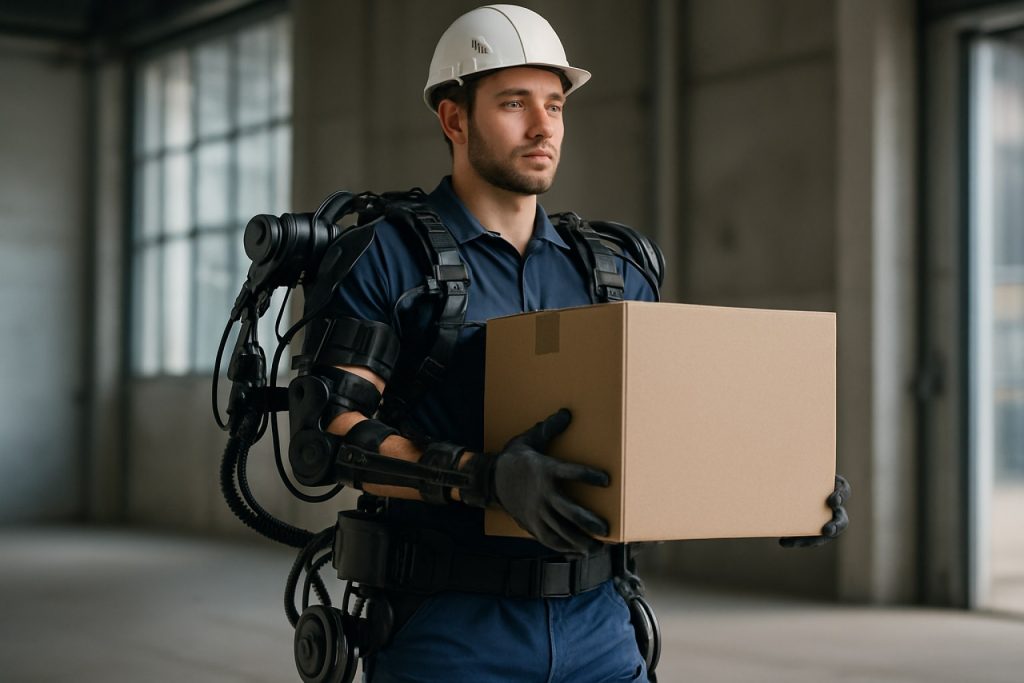
Revolutionizing Mobility: How Wearable Exoskeleton Actuation Systems Will Transform Industries in 2025 and Beyond. Explore the Technologies, Market Growth, and Future Impact of Next-Gen Human Augmentation.
- Executive Summary: 2025 Market Snapshot and Key Trends
- Market Size, Growth Rate, and Forecasts Through 2030
- Core Actuation Technologies: Electric, Hydraulic, and Pneumatic Systems
- Leading Manufacturers and Industry Initiatives (e.g., suitx.com, ekso.com, rewalk.com)
- Applications Across Sectors: Healthcare, Industrial, Military, and Consumer
- Innovation Pipeline: Lightweight Materials and Smart Sensors
- Regulatory Landscape and Industry Standards (e.g., ieee.org, asme.org)
- Challenges: Power Supply, Ergonomics, and Cost Barriers
- Regional Analysis: North America, Europe, Asia-Pacific, and Emerging Markets
- Future Outlook: Human-Machine Synergy and the Path to Mass Adoption
- Sources & References
Executive Summary: 2025 Market Snapshot and Key Trends
The wearable exoskeleton actuation systems market in 2025 is characterized by rapid technological advancements, increased commercialization, and expanding application domains. Actuation systems—comprising electric motors, hydraulics, pneumatics, and emerging soft actuators—are the core components that enable exoskeletons to augment human movement for medical, industrial, and defense purposes. In 2025, the sector is witnessing a shift toward lighter, more energy-efficient, and highly responsive actuation technologies, driven by the need for improved user comfort, safety, and autonomy.
Leading manufacturers such as Ottobock, SuitX (now part of Ottobock), CYBERDYNE Inc., and Sarcos Technology and Robotics Corporation are at the forefront of integrating advanced actuation systems into their exoskeleton products. Ottobock continues to refine its powered orthoses with compact, brushless electric motors, while CYBERDYNE Inc. leverages hybrid assistive limb (HAL) technology, combining bioelectric signal detection with precise actuator control for rehabilitation and industrial support. Sarcos focuses on full-body, battery-powered exoskeletons for industrial lifting, utilizing proprietary actuation modules designed for high payload and endurance.
Recent years have seen a surge in the adoption of soft robotics and pneumatic actuators, particularly for lightweight assistive exosuits. Companies like ReWalk Robotics and SuitX are exploring soft exoskeletons that use textile-based actuators and air muscles, offering greater flexibility and reduced weight compared to traditional rigid systems. This trend is expected to accelerate through 2025 and beyond, as research institutions and industry players collaborate to enhance actuator efficiency, reduce noise, and extend battery life.
Key trends shaping the 2025 landscape include the integration of AI-driven control algorithms for adaptive actuation, modular actuator designs for customizable support, and the use of advanced materials such as carbon fiber composites to minimize system weight. The convergence of these innovations is enabling exoskeletons to move from niche medical and research applications into mainstream industrial and logistics settings, where worker safety and productivity are paramount.
Looking ahead, the outlook for wearable exoskeleton actuation systems is robust, with ongoing investments in R&D and pilot deployments by major manufacturers. The next few years are expected to bring further miniaturization, improved power-to-weight ratios, and broader regulatory acceptance, positioning actuation technology as a critical enabler for the global exoskeleton market’s continued growth.
Market Size, Growth Rate, and Forecasts Through 2030
The global market for wearable exoskeleton actuation systems is poised for robust growth through 2030, driven by increasing demand in medical rehabilitation, industrial ergonomics, and defense applications. As of 2025, the sector is experiencing a surge in both public and private investment, with a focus on enhancing mobility, reducing workplace injuries, and augmenting human capabilities. The actuation systems—comprising electric motors, hydraulics, pneumatics, and emerging soft actuators—are central to the performance and adoption of wearable exoskeletons.
Key industry players such as SuitX (now part of Ottobock), Ottobock, Sarcos Technology and Robotics Corporation, ReWalk Robotics, and CYBERDYNE Inc. are actively expanding their product portfolios and global reach. These companies are investing in R&D to improve actuator efficiency, reduce weight, and enhance user comfort. For example, Ottobock has integrated lightweight electric actuators into its exoskeletons for industrial use, while CYBERDYNE Inc. continues to refine its HAL (Hybrid Assistive Limb) systems with advanced control algorithms and actuator technologies.
The market size for wearable exoskeletons, including actuation systems, is estimated to surpass several billion USD by 2030, with a compound annual growth rate (CAGR) projected in the double digits. This growth is underpinned by the increasing adoption of exoskeletons in healthcare for rehabilitation of spinal cord injuries and stroke, as well as in logistics and manufacturing to prevent musculoskeletal disorders. Sarcos Technology and Robotics Corporation is notable for its focus on industrial exoskeletons, leveraging electric and hydraulic actuators to assist workers in physically demanding environments.
Technological advancements are expected to further accelerate market expansion. The integration of artificial intelligence and sensor fusion is enabling more responsive and adaptive actuation, while the development of soft robotics and novel materials is reducing system weight and improving ergonomics. Companies like SuitX and ReWalk Robotics are at the forefront of these innovations, with ongoing trials and deployments in both clinical and workplace settings.
Looking ahead to the next few years, the outlook for wearable exoskeleton actuation systems remains highly positive. Regulatory approvals are increasing, and partnerships between manufacturers, healthcare providers, and industrial firms are expanding deployment opportunities. As costs decrease and performance improves, the sector is expected to see widespread adoption across multiple domains, solidifying its role as a transformative technology by 2030.
Core Actuation Technologies: Electric, Hydraulic, and Pneumatic Systems
Wearable exoskeleton actuation systems are at the heart of performance, safety, and user experience in both industrial and medical applications. As of 2025, the sector is witnessing rapid evolution, with electric, hydraulic, and pneumatic actuation technologies each carving out distinct roles based on application requirements, cost, and technological maturity.
Electric actuation remains the dominant technology in wearable exoskeletons, especially for medical rehabilitation and industrial support. Electric motors, often paired with advanced gear systems and sensors, offer precise control, relatively low noise, and high energy efficiency. Companies such as SUITX (now part of Ottobock), Ottobock, and Sarcos Technology and Robotics Corporation have commercialized electric-powered exoskeletons for both industrial and healthcare settings. For example, Ottobock’s Paexo series and Sarcos’ Guardian XO are fully electric, leveraging lithium-ion battery technology to provide several hours of operation per charge. The trend in 2025 is toward lighter, more compact actuators and the integration of AI-driven control algorithms for adaptive assistance, as seen in the latest models from these manufacturers.
Hydraulic actuation is favored in applications demanding high power-to-weight ratios and robust force output, such as military and heavy industrial exoskeletons. Hydraulics can deliver greater torque and load-bearing capacity compared to electric systems, albeit at the cost of increased system complexity, weight, and maintenance. Sarcos Technology and Robotics Corporation has been a leader in this space, with its earlier exoskeleton prototypes utilizing hydraulic systems for heavy lifting. However, the industry is gradually shifting toward hybrid or fully electric systems due to advances in electric actuator efficiency and the desire for reduced maintenance and improved portability.
Pneumatic actuation—using compressed air to drive artificial muscles or actuators—has found niche applications, particularly in soft exoskeletons and assistive devices where compliance and safety are paramount. Companies like SUITX and research groups at leading universities have demonstrated pneumatic-powered exosuits for gait assistance and rehabilitation. While pneumatic systems offer inherent compliance and lightweight construction, their reliance on external compressors or air tanks limits their practicality for untethered, all-day use. Ongoing research in 2025 is focused on miniaturizing pneumatic components and developing portable air supply solutions.
Looking ahead, the outlook for exoskeleton actuation systems is shaped by the convergence of lightweight materials, battery advancements, and smart control electronics. The next few years are expected to see further miniaturization, improved energy density, and the emergence of hybrid actuation systems that combine the strengths of electric, hydraulic, and pneumatic technologies. Industry leaders such as Ottobock and Sarcos Technology and Robotics Corporation are likely to drive these innovations, with a focus on expanding exoskeleton adoption across healthcare, logistics, and defense sectors.
Leading Manufacturers and Industry Initiatives (e.g., suitx.com, ekso.com, rewalk.com)
The wearable exoskeleton sector is experiencing rapid evolution in actuation systems, driven by both established manufacturers and new entrants. As of 2025, leading companies are focusing on improving power efficiency, user comfort, and adaptability, with a strong emphasis on real-world deployment in medical, industrial, and military applications.
Among the most prominent players, Ekso Bionics continues to advance its exoskeletons for rehabilitation and industrial support. Their latest models, such as the EksoNR and Ekso EVO, utilize a combination of electric motors and passive mechanical elements to optimize weight and energy consumption. The company’s actuation systems are designed for precise, responsive movement, supporting both lower and upper limb applications. Ekso Bionics has also expanded its partnerships with healthcare providers and industrial firms, aiming to increase adoption in clinical and workplace settings.
Another key innovator, ReWalk Robotics, specializes in powered exoskeletons for individuals with lower limb disabilities. Their flagship ReWalk Personal 6.0 system employs sophisticated motorized actuation at the hip and knee joints, controlled by a combination of sensors and user-initiated commands. In 2025, ReWalk is focusing on enhancing battery life and reducing device weight, while also pursuing regulatory approvals and reimbursement pathways in new markets.
In the industrial domain, SuitX (now part of Ottobock) has been at the forefront of developing modular exoskeletons for workplace injury prevention. Their actuation systems often blend passive and semi-active mechanisms, reducing strain on workers during repetitive or strenuous tasks. SuitX’s MAX system, for example, is designed to support the back, shoulder, and leg muscles, and is being adopted by major manufacturing and logistics companies.
Other notable manufacturers include Ottobock, which has integrated SuitX’s technology into its own product lines, and CYBERDYNE Inc., a Japanese pioneer known for its HAL (Hybrid Assistive Limb) exoskeletons. CYBERDYNE’s actuation systems leverage bioelectrical signal detection to provide intuitive, user-driven assistance, and the company is expanding its presence in both medical and industrial sectors.
Looking ahead, the industry is expected to see further integration of AI-driven control algorithms, lighter and more efficient actuators (including soft robotics), and increased modularity to tailor exoskeletons to specific user needs. As regulatory frameworks mature and costs decrease, adoption rates are projected to rise, particularly in rehabilitation and occupational health. The ongoing collaboration between manufacturers, healthcare providers, and industrial partners will be crucial in shaping the next generation of wearable exoskeleton actuation systems.
Applications Across Sectors: Healthcare, Industrial, Military, and Consumer
Wearable exoskeleton actuation systems are rapidly evolving, with 2025 marking a pivotal year for their deployment across healthcare, industrial, military, and consumer sectors. These systems, which provide powered assistance to human movement, are increasingly leveraging advanced actuators—such as electric motors, hydraulics, and pneumatics—to deliver precise, responsive, and energy-efficient support.
In healthcare, exoskeletons are transforming rehabilitation and mobility assistance. Companies like ReWalk Robotics and Ekso Bionics have developed FDA-cleared devices that use electric actuators to assist individuals with spinal cord injuries or stroke in regaining ambulatory function. These systems typically employ brushless DC motors and sophisticated sensor arrays to synchronize movement with the user’s intent, offering both overground gait training and personal mobility solutions. In 2025, the integration of lighter, quieter actuators and improved battery technologies is expected to further enhance user comfort and device autonomy.
The industrial sector is witnessing a surge in exoskeleton adoption to reduce worker fatigue and injury, particularly in logistics, manufacturing, and construction. Ottobock and Sarcos Technology and Robotics Corporation are notable for their powered exosuits and full-body exoskeletons, which utilize a combination of electric and pneumatic actuators to augment lifting strength and endurance. For example, Sarcos’ Guardian XO features a battery-powered, hydraulically actuated system capable of enabling users to lift up to 90 kg repeatedly without strain. In 2025, the focus is on modularity and adaptability, with exoskeletons being tailored for specific tasks and environments, and the introduction of AI-driven actuation control for real-time adjustment to user movement and load.
Military applications are advancing as defense agencies seek to enhance soldier performance and reduce musculoskeletal injuries. Lockheed Martin has developed the ONYX exoskeleton, which employs electrically actuated knee support to assist soldiers during load carriage and repetitive tasks. The U.S. Army and allied forces are conducting field trials in 2025, evaluating the impact of these systems on endurance and injury rates. The trend is toward ruggedized, low-latency actuation systems that can operate reliably in harsh environments.
In the consumer sector, exoskeletons are beginning to emerge for recreational and personal wellness applications. Companies such as SuitX (now part of Ottobock) are exploring lightweight, electrically actuated exosuits for activities like hiking and running, aiming to broaden accessibility and affordability. The next few years are expected to see further miniaturization of actuators and integration with wearable sensors, making exoskeletons more practical for everyday use.
Overall, 2025 is set to be a year of significant progress in wearable exoskeleton actuation systems, with ongoing innovation in actuator technology, control algorithms, and system integration driving broader adoption across multiple sectors.
Innovation Pipeline: Lightweight Materials and Smart Sensors
The innovation pipeline for wearable exoskeleton actuation systems in 2025 is characterized by a strong focus on lightweight materials and the integration of smart sensors, both of which are critical for enhancing user comfort, safety, and performance. The actuation system—the mechanism that drives movement in exoskeletons—has traditionally relied on electric motors, pneumatic actuators, or hydraulic systems. However, the industry is now witnessing a shift toward more compact, energy-efficient, and responsive solutions, driven by advances in materials science and sensor technology.
Key players such as Sarcos Technology and Robotics Corporation and Ottobock are at the forefront of developing exoskeletons that utilize high-torque, low-weight actuators. For example, Sarcos’ Guardian XO full-body exoskeleton employs a combination of electric actuators and proprietary lightweight materials to deliver industrial-grade strength while maintaining user mobility and reducing fatigue. Ottobock, a leader in medical exoskeletons, has focused on modular actuator designs that can be tailored to individual patient needs, leveraging lightweight composites and advanced servo motors.
The integration of smart sensors is another major trend shaping the actuation landscape. Companies like Honda Motor Co., Ltd. and CYBERDYNE Inc. are embedding force, position, and biosignal sensors directly into exoskeleton joints and control systems. These sensors enable real-time feedback and adaptive control, allowing the exoskeleton to respond dynamically to the wearer’s movements and intentions. For instance, CYBERDYNE’s HAL (Hybrid Assistive Limb) exoskeleton uses bioelectrical signal sensors to detect the user’s muscle activation, providing assistive torque precisely when needed.
Looking ahead to the next few years, the innovation pipeline is expected to deliver further reductions in actuator size and weight, with research into soft robotics and artificial muscles gaining momentum. Companies such as SuitX (now part of Ottobock) are exploring pneumatic artificial muscles and soft actuators that mimic natural muscle movement, offering a more ergonomic and less obtrusive alternative to traditional rigid systems. Additionally, the proliferation of flexible, printed sensors and wireless connectivity will enable more seamless integration of exoskeletons into industrial, medical, and even consumer applications.
Overall, the convergence of lightweight materials and smart sensor technologies is set to redefine wearable exoskeleton actuation systems, making them more accessible, intuitive, and effective for a broad range of users in 2025 and beyond.
Regulatory Landscape and Industry Standards (e.g., ieee.org, asme.org)
The regulatory landscape and industry standards for wearable exoskeleton actuation systems are rapidly evolving as these devices transition from research prototypes to commercial products in medical, industrial, and military sectors. In 2025, the focus is on harmonizing safety, performance, and interoperability requirements to support widespread adoption and user trust.
A cornerstone of this regulatory framework is the work of the IEEE, which has developed the IEEE 802.1AS standard for exoskeletons, addressing safety, performance, and ethical considerations. The IEEE P2863 working group continues to refine guidelines for physical human-robot interaction, emphasizing actuation system reliability and fail-safe mechanisms. These standards are increasingly referenced by manufacturers and regulatory bodies worldwide.
The ASME has also contributed significantly, particularly through its V&V 40 standard, which provides a risk-informed framework for the verification and validation of medical devices, including exoskeletons. This standard is being adopted by leading exoskeleton developers to demonstrate compliance with regulatory expectations for actuation system safety and performance.
In the United States, the Food and Drug Administration (FDA) continues to regulate medical exoskeletons as Class II devices, requiring premarket notification and adherence to recognized consensus standards. The FDA’s Center for Devices and Radiological Health (CDRH) has issued guidance on the use of exoskeletons, with a particular focus on the reliability and redundancy of actuation systems to prevent user injury. Companies such as ReWalk Robotics and Ekso Bionics have successfully navigated this process, setting precedents for future entrants.
In Europe, the Medical Device Regulation (MDR) enforces strict requirements for safety and clinical evaluation. Organizations like CYBERDYNE Inc. and Ottobock are actively engaged in aligning their actuation technologies with these regulations, often participating in collaborative standardization efforts.
Looking ahead, the next few years are expected to see increased convergence between international standards, with ongoing collaboration between IEEE, ASME, and ISO. The development of new test protocols for actuation system durability, energy efficiency, and user safety is anticipated, reflecting the growing diversity of exoskeleton applications. Industry stakeholders are also advocating for clearer pathways for industrial and military exoskeletons, which currently face a patchwork of regulatory requirements.
Overall, the regulatory and standards environment for wearable exoskeleton actuation systems in 2025 is characterized by active development, cross-sector collaboration, and a strong emphasis on user safety and system reliability, laying the groundwork for broader adoption in the coming years.
Challenges: Power Supply, Ergonomics, and Cost Barriers
Wearable exoskeleton actuation systems are at the forefront of assistive and augmentative technology, but their widespread adoption in 2025 and the near future is constrained by persistent challenges in power supply, ergonomics, and cost. These barriers are central to both industrial and medical exoskeleton applications, shaping the pace and direction of innovation.
Power supply remains a critical bottleneck. Most exoskeletons rely on lithium-ion battery packs, which limit operational time to a few hours before requiring recharging or replacement. For example, leading industrial exoskeletons from Ottobock and SUITX (now part of Ottobock) typically offer 4–8 hours of use under moderate load. While research into alternative chemistries and energy harvesting is ongoing, no major commercial breakthrough is expected in the immediate future. Companies such as Sarcos Technology and Robotics Corporation are exploring hybrid power systems and modular battery packs to extend runtime, but these solutions often add weight and complexity, impacting user comfort and system reliability.
Ergonomics is another significant challenge. Exoskeletons must balance actuation power with user comfort and freedom of movement. Excessive weight, rigid structures, and poor fit can lead to user fatigue or even injury. Hocoma and ReWalk Robotics have made advances in lightweight materials and adjustable fittings, but the integration of powerful actuators without compromising ergonomics remains difficult. Soft exosuits, such as those developed by SUITX and Ottobock, offer improved comfort but often at the expense of actuation strength and precision. The next few years are likely to see incremental improvements in materials science and design, but a fundamental leap in ergonomic integration is still pending.
Cost barriers continue to restrict exoskeleton deployment, especially in healthcare and small-to-medium enterprises. Advanced actuation systems, precision sensors, and custom fitting drive up prices, with most commercial exoskeletons costing tens of thousands of dollars. CYBERDYNE Inc. and ReWalk Robotics have made efforts to reduce costs through modular designs and scalable manufacturing, but affordability remains a major hurdle. Without significant reductions in component and production costs, exoskeletons are likely to remain niche products in the near term.
Looking ahead, the exoskeleton industry is expected to focus on incremental improvements in battery technology, ergonomic design, and cost-effective manufacturing. However, overcoming these core challenges will require sustained investment and cross-disciplinary innovation, with transformative breakthroughs likely to emerge only over a longer horizon.
Regional Analysis: North America, Europe, Asia-Pacific, and Emerging Markets
The global landscape for wearable exoskeleton actuation systems in 2025 is marked by distinct regional dynamics, shaped by industrial priorities, healthcare needs, and government initiatives. North America, Europe, and Asia-Pacific remain the primary hubs for innovation and deployment, while emerging markets are beginning to show increased activity, particularly in rehabilitation and industrial safety.
North America continues to lead in both technological development and commercialization of wearable exoskeletons, driven by robust investments in healthcare, defense, and industrial automation. The United States is home to several pioneering companies, including Ekso Bionics, which focuses on medical and industrial exoskeletons, and SuitX (now part of Ottobock), known for modular exoskeletons targeting workplace injury reduction. The region benefits from strong collaboration between research institutions and industry, as well as support from agencies such as the Department of Defense, which continues to fund exoskeleton research for soldier augmentation and logistics applications. Canadian firms are also active, with a focus on rehabilitation and assistive technologies.
Europe is characterized by a strong emphasis on medical and rehabilitation exoskeletons, supported by public healthcare systems and stringent workplace safety regulations. Companies such as Ottobock (Germany) and Hocoma (Switzerland) are at the forefront, offering advanced actuation systems for gait training and mobility assistance. The European Union’s funding for assistive technology research and cross-border collaborations has accelerated the adoption of exoskeletons in hospitals and rehabilitation centers. Additionally, industrial exoskeletons are gaining traction in automotive and manufacturing sectors, with pilot deployments aimed at reducing musculoskeletal injuries among workers.
Asia-Pacific is witnessing rapid growth, fueled by aging populations, rising healthcare expenditures, and government-backed innovation programs. Japan remains a leader, with CYBERDYNE Inc. commercializing its HAL (Hybrid Assistive Limb) exoskeletons for both medical and industrial use. South Korea’s Hyosung and China’s emerging robotics firms are investing in next-generation actuation technologies, including lightweight motors and soft actuators, to enhance user comfort and adaptability. The region’s manufacturing sector is a significant driver, with exoskeletons increasingly integrated into logistics and assembly lines.
Emerging markets in Latin America, the Middle East, and parts of Southeast Asia are beginning to adopt wearable exoskeletons, primarily for rehabilitation and workplace safety. While local manufacturing is limited, partnerships with global suppliers and pilot programs in hospitals and factories are laying the groundwork for future growth. As costs decrease and awareness rises, these regions are expected to play a more prominent role in the global exoskeleton market over the next few years.
Across all regions, the outlook for 2025 and beyond points to continued innovation in actuation systems—such as the integration of soft robotics, improved battery technologies, and AI-driven adaptive controls—driven by the dual imperatives of user safety and enhanced mobility.
Future Outlook: Human-Machine Synergy and the Path to Mass Adoption
The future of wearable exoskeleton actuation systems is poised for significant transformation as the industry moves toward greater human-machine synergy and broader mass adoption. In 2025 and the following years, the focus is shifting from purely mechanical augmentation to intelligent, adaptive systems that seamlessly integrate with the user’s natural movements. This evolution is driven by advances in actuation technologies, sensor integration, and artificial intelligence, all of which are critical for improving user comfort, safety, and performance.
Leading manufacturers are investing heavily in the development of lightweight, energy-efficient actuators. For instance, SUITX (now part of Ottobock) and Ottobock are refining their exoskeletons with compact electric motors and advanced control algorithms, aiming to reduce device weight while maintaining high torque output. Similarly, Sarcos Technology and Robotics Corporation is advancing its Guardian XO exoskeleton, which utilizes a combination of high-power electric actuators and sophisticated force-feedback systems to enable intuitive, responsive movement for industrial applications.
Pneumatic and hydraulic actuation systems, while traditionally offering high power-to-weight ratios, are being reimagined for wearable use. Companies like Honda are exploring hybrid actuation approaches, combining electric and pneumatic elements to balance efficiency and power delivery. Meanwhile, CYBERDYNE Inc. continues to develop its HAL (Hybrid Assistive Limb) exoskeleton, which leverages bioelectrical signal detection to trigger actuators in real time, enhancing the natural synergy between human intent and machine assistance.
Looking ahead, the integration of soft robotics and novel materials is expected to further revolutionize actuation systems. Soft actuators, which mimic biological muscle movement, are under active development by several research-driven companies and are anticipated to enter commercial products within the next few years. This shift promises to deliver exoskeletons that are not only lighter and more comfortable but also capable of more nuanced, adaptive support.
As regulatory frameworks mature and costs decrease, the path to mass adoption will be shaped by the ability of exoskeletons to deliver tangible benefits in healthcare, industrial, and even consumer settings. The ongoing collaboration between industry leaders, such as Ottobock, Sarcos, and CYBERDYNE Inc., and the integration of user feedback into design cycles, will be crucial in ensuring that actuation systems evolve to meet the diverse needs of end users, paving the way for widespread human-machine synergy in the coming years.
Sources & References
- Ottobock
- SuitX
- CYBERDYNE Inc.
- Sarcos Technology and Robotics Corporation
- ReWalk Robotics
- Lockheed Martin
- IEEE
- ASME
- Ekso Bionics
- Hocoma