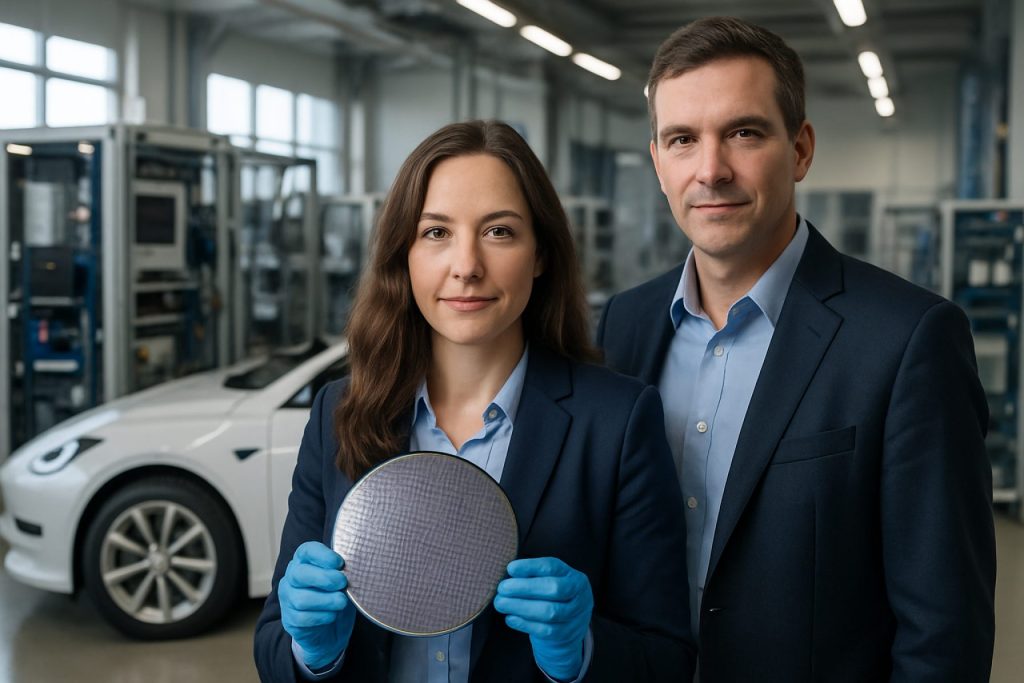
- Fraunhofer IISB and AIXTRON are collaborating to advance 150 mm Silicon Carbide (SiC) wafer technology, crucial for the future of power electronics.
- The new 8×150 mm G5WW VPE system enables high-efficiency, large-scale SiC epitaxy, increasing productivity and reducing manufacturing costs.
- SiC wafers offer superior performance over traditional silicon by operating efficiently at higher voltages and temperatures, crucial for devices like Schottky diodes and MOSFETs in green energy and electronics.
- Advanced defect-detection techniques ensure high-quality, low-defect SiC layers—critical for consistent semiconductor manufacturing.
- This partnership aims to mass-produce reliable, affordable SiC wafers, paving the way for more energy-efficient, compact, and sustainable power devices.
A surge of promise electrifies the halls of Fraunhofer IISB in Erlangen, Germany—a place where the relentless pursuit of excellence in semiconductor research hums at the edge of innovation. The latest catalyst for this momentum: a strategic collaboration between Fraunhofer’s accomplished researchers and AIXTRON, a global leader in advanced deposition equipment. Together, they aim to transform the future of power electronics by elevating 150 mm Silicon Carbide (SiC) wafer technology to new heights.
Picture rows of ultra-clean laboratories, where SiC wafers glimmer like futuristic coins, each just a whisper thick but carrying immense electrical potential. Here, Fraunhofer IISB’s experimental prowess combines with AIXTRON’s new 8×150 mm G5WW Vapor Phase Epitaxy (VPE) system—an engineering marvel designed for the precise art of SiC epitaxy. The system, arriving soon in the IISB cleanroom, promises to double down on both efficiency and scale. No longer limited to smaller wafers, the shift to 150 mm enables a quantum leap in productivity and paves the path toward affordable, high-performance power devices.
But why SiC, and why now? Silicon Carbide possesses remarkable qualities—a robustness under high voltage and temperature conditions, a stubborn resistance to breakdown that outperforms traditional silicon. SiC devices such as Schottky diodes and MOSFETs already orchestrate the silent symphony powering everything from energy-efficient TVs and computer server farms to solar inverters, medical equipment, and even the high-speed trains threading modern cities. The material’s superior properties allow for devices that are more compact, waste less energy, and produce less heat.
The challenge until now has been cost and consistency. Imagine assembling a puzzle with missing pieces: slight defects in wafer growth spell disaster for the precision world of semiconductors. Fraunhofer IISB’s mastery in cultivating SiC layers, honed with advanced defect-detection techniques like room-temperature photoluminescence imaging and selective etching, offers a solution. Their processes yield SiC films low in imperfections—exactly what global manufacturers hunger for.
Working hand-in-hand, the two teams have a clear mission: to demonstrate not just lab-grade excellence, but industrial-scale reliability. The outcome? Mass-manufactured 150 mm SiC wafers that will empower next-generation power electronics—making green energy devices cheaper and more accessible while slashing electrical waste worldwide.
This partnership signals more than technical progress; it foreshadows a turning point in how the world consumes energy. As demand for sustainable technology intensifies, every improvement in core materials like SiC ripples outward—enabling slimmer devices, expanding renewable energy’s reach, and quietly rewriting the blueprint for our digital lives.
The message is clear: breakthroughs in SiC technology will soon touch everyday life in a thousand unseen ways, fueling a future that’s not only more powerful but significantly cleaner and smarter.
For readers eager to glimpse what comes next, keep a watchful eye on the work of AIXTRON and Fraunhofer IISB—where the next chapter of semiconductor evolution is being written, layer by meticulous layer.
Why Silicon Carbide Wafers Will Revolutionize Green Tech & Power Electronics in 2024
Silicon Carbide (SiC) Semiconductors: The Next Frontier in Sustainable Tech
The breakthrough collaboration between Germany’s Fraunhofer IISB and global deposition equipment leader AIXTRON isn’t just about cutting-edge science—it’s poised to redefine the global power electronics landscape. As they scale up 150 mm SiC wafer technology with the new G5WW VPE system, here’s the full story, including deep-dive facts, expert insights, and actionable tips, shaped for both industry leaders and tech-curious readers.
—
Key Facts & Specifications Not Fully Explored
1. Why the Jump to 150 mm Wafers Matters
– Increased Yield: Larger wafers mean more chips per batch, reducing production cost per device and boosting capacity for mass manufacturing.
– Lower Defect Density: Advanced imaging and etching at Fraunhofer IISB further minimize imperfections, crucial for high-voltage and reliability standards ([EE Times](https://www.eetimes.com)).
– Eco-Efficiency: More efficient chips contribute to less material waste and less energy consumption in both manufacturing and device operation.
2. Silicon Carbide vs. Traditional Silicon: Game-Changing Advantages
– Higher Breakdown Voltage: SiC can handle up to ten times higher voltages, making it ideal for high-power industrial and automotive applications ([IEEE Spectrum](https://www.ieee.org)).
– Thermal Conductivity: SiC operates at temperatures exceeding 200°C, vital for compact devices and harsh environments.
– Lower Switching Losses: Transistors made with SiC switch faster and with less energy loss—crucial for renewables and electric vehicles.
3. Real-World Applications & Use Cases
– Electric Vehicles (EVs): SiC-based inverters increase driving range and lower charging times ([Tesla and BYD are already using SiC power modules in production EVs](https://www.reuters.com)).
– Solar & Wind Energy: Power conversion efficiency is improved, maximizing green energy output.
– Consumer Electronics: TVs, power supplies, and even fast-charging adapters are leveraging SiC for cooler, smaller, more reliable operation.
4. Market Forecasts & Industry Trends
– Market Growth: The global SiC device market is projected to exceed $6 billion by 2027, growing at a CAGR of over 30% ([Yole Group Reports](https://www.yolegroup.com)).
– Automotive Boom: Electrification trends and grid modernization are main growth drivers.
– Supply Chain Shifts: Strategic partnerships like Fraunhofer-AIXTRON will accelerate European and global SiC adoption.
—
Expert Insights & Industry Reviews
What Sets Fraunhofer IISB and AIXTRON Apart?
– AIXTRON’s 8×150 mm G5WW VPE: Capable of precise, uniform SiC deposition on eight 150 mm wafers per batch—setting a new industrial throughput standard.
– Fraunhofer IISB’s Defect Control: Combining selective etching with room-temperature photoluminescence ensures defect rates far below industry average.
Pricing, Compatibility, and Security
– Cost Curve: SiC wafers cost 2-3 times more than silicon presently but are expected to decrease as manufacturing scales.
– Compatibility: New power modules are increasingly designed to be drop-in replacements for legacy silicon counterparts, easing upgrade paths.
– Security & IP: SiC technology is a strategic resource; many countries, including the EU, are investing to secure domestic supply chains ([European Commission](https://www.europa.eu)).
—
Limitations & Controversies
– Wafer Scaling Challenges: Moving to even larger 200 mm wafers is ongoing but not yet mature—cost and defect control remain technical obstacles.
– Raw Material Constraints: SiC crystal growth is energy- and time-intensive, necessitating continued materials innovation ([Nature Materials](https://www.nature.com)).
– Environmental Impact: While SiC devices boost efficiency, their fabrication still has a nonzero carbon footprint, making closed-loop recycling and green chemistry pivotal.
—
How-To: Maximize SiC Technology Benefits in Your Business
1. Evaluate Your Power Needs: If you design high-voltage or high-efficiency electronics, assess the return on investment for SiC vs. traditional silicon.
2. Engage Supply Chain Partners: Begin dialogue with SiC wafer suppliers and foundries.
3. Prototype with Hybrid Solutions: Many power electronics platforms allow for silicon or SiC chips—test both side-by-side.
4. Stay Updated: Follow AIXTRON and Fraunhofer IISB releases for developer kits, sample availability, and pilot opportunities.
—
Pros & Cons Overview
Pros
– Superior electrical and thermal performance.
– Key enabler for green and next-gen technologies.
– Slashes size and weight for power devices.
– Builds future-proof supply chains.
Cons
– Current higher cost compared to legacy silicon.
– Technical complexity in defect reduction and scaling.
– Limited global supply chain outside Asia.
—
Most Pressing Questions Answered
Q: Will SiC completely replace silicon in electronics?
A: Not entirely. SiC dominates in high-power and high-voltage arenas, while silicon remains cost-effective for lower-end applications.
Q: How soon will my household devices use SiC?
A: They’re already here—many efficient adapters, high-end TVs, and new EVs use SiC modules today.
Q: Who are the leading SiC players?
A: Alongside Fraunhofer IISB and AIXTRON, companies like Wolfspeed, STMicroelectronics, and Infineon are key innovators.
—
Actionable Recommendations & Quick Tips
1. Follow Industry News: Regularly check updates from Fraunhofer IISB and AIXTRON.
2. Participate in SiC Workshops: Many institutes now offer online and onsite seminars for engineers and decision makers.
3. Pilot Green Upgrades: Plan pilot projects in EVs, renewables, or infrastructure—early adoption attracts subsidies and grants.
4. Think Supply Chain Security: Secure multiple sources for wafers as the market heats up.
—
Conclusion
Silicon carbide’s rise—fueled by technological partnerships and relentless research—signals a rapid evolution in power electronics and sustainable technology. Keep an eye on this sector; the cleaner, faster, and smarter devices of tomorrow are already being built today.
For further updates, industry deep-dives, and expert commentary, stay tuned to trusted domain sources and global technology leaders.