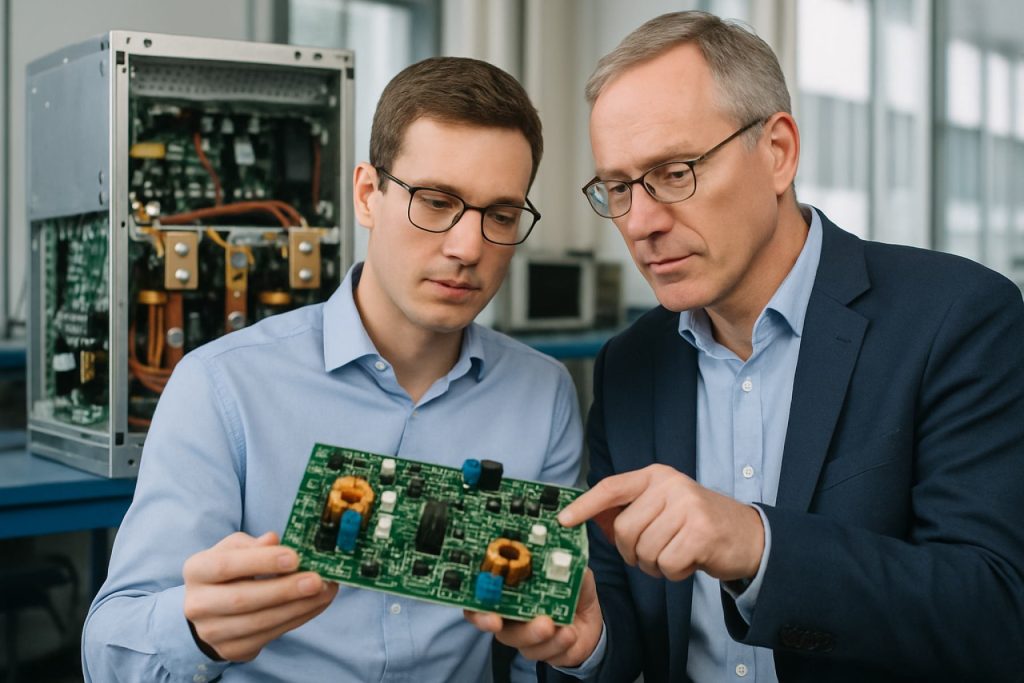
- Silicon carbide (SiC) enables next-generation power electronics, offering improved energy efficiency for data centers, solar grids, medical equipment, and high-speed trains.
- The shift to large 150 mm SiC wafers reduces manufacturing costs, boosts device yield, and facilitates wider adoption of SiC technology in mainstream applications.
- AIXTRON’s advanced VPE epitaxy system and Fraunhofer IISB’s expertise in defect reduction and characterization are crucial to producing high-quality, reliable SiC power devices.
- This collaboration is overcoming scalability challenges, making SiC more affordable and accessible for industries aiming for smarter, greener, and more reliable operations.
- The partnership signals a major step toward making SiC power devices standard, driving a transformation in global energy use and electronics performance.
Silicon carbide—a material as unyielding as it sounds—now carves its presence at the heart of a technological renaissance. The meticulous hands and sharp minds of AIXTRON and Fraunhofer IISB have joined forces, aiming to transform not just the manufacturing landscape, but the very ambitions that power our most essential devices.
Picture a shimmering cleanroom in Erlangen, Germany: engineers in pristine white suits shepherding silicon carbide wafers the size of a dessert plate. They are far more than technicians; they are sculptors shaping the future of energy efficiency. Their tools? The world-class AIXTRON 8×150 mm G5WW Vapor Phase Epitaxy (VPE) system and decades of semiconductor wisdom.
Why all the intrigue around 150 mm silicon carbide (SiC) wafers? It comes down to power—and the potential to dramatically alter how electricity flows in everything from data centers and solar grids to medical diagnostics and high-speed trains. SiC power devices, including high-performance Schottky diodes and MOSFETs, are already key players in cutting-edge applications. But the challenge confronting the industry has never been technology alone—cost and scalability are king.
Traditional semiconductor wafers, often 100 mm across, face bottlenecks as demand soars. Larger wafers mean more devices per batch, lower manufacturing costs, and wide-reaching adoption. Yet, with silicon carbide’s intrinsic hardness and tendency for microscopic defects, scaling up to the robust 150 mm format is no trivial feat.
Fraunhofer IISB, celebrated for its prowess in material science, brings to the partnership its mastery in defect reduction and advanced characterization techniques, such as room-temperature photoluminescence imaging. This precision ensures that SiC layers grown are flawless—crucial for the reliable performance of high-voltage devices.
AIXTRON, with a global reputation for innovation in deposition equipment, injects the collaboration with the muscle and technical finesse needed for industrial-scale manufacturing. Together, their synergy is not just optimizing processes but redefining what is possible in composite semiconductor production.
The true impact, though, will ripple beyond laboratories and factory floors. AIXTRON and Fraunhofer IISB are paving the way for SiC to leap from niche to norm. Think of computers that waste less power, solar farms that convert energy with razor-sharp efficiency, and a next-gen grid resilient enough to meet tomorrow’s challenges.
As the industry migrates toward 150 mm SiC technology, the promise is clear: lighter, faster, more efficient power electronics. Costs will drop, adoption will soar, and everyday technology—in homes, hospitals, trains, and more—will quietly become smarter, greener, and more reliable.
Key takeaway: Innovation flourishes where expertise converges. The AIXTRON-Fraunhofer alliance is not just advancing wafer size; it is laying the groundwork for a revolution in how we harness and transmit electrical energy, with global benefits poised to touch every facet of modern life.
For more insights on semiconductor advancements, explore Fraunhofer.
The Silicon Carbide Revolution: How 150 mm Wafers Are Shaping Tomorrow’s Electronics
Unlocking Silicon Carbide’s True Power: Everything You Need to Know About the 150 mm Wafer Breakthrough
Silicon carbide (SiC) is fast becoming the backbone of next-generation power electronics. While the source article highlights the groundbreaking alliance between AIXTRON and Fraunhofer IISB, let’s dive deeper into all the key facts, market trends, technical specs, and actionable recommendations around this technology. Here’s the deeper story that industry insiders and tech enthusiasts need to know.
—
What Is Silicon Carbide—and Why Does the Wafer Size Matter?
Silicon carbide is a semiconductor material prized for its exceptional thermal conductivity, high breakdown electric field, and immense mechanical hardness. These properties allow SiC-based devices to:
– Operate at higher voltages, frequencies, and temperatures than standard silicon devices
– Deliver superior efficiency (less energy lost as heat)
– Shrink the size of modules, leading to lighter, more compact power systems
Wider wafers—like the new industrial 150 mm format—mean:
– More chips produced in every manufacturing batch
– Dramatically lower costs per device
– Increased scalability and mainstream adoption for automotive, renewable energy, industrial, and consumer tech
—
Additional Facts Not Fully Explored in the Article
1. Market Forecasts & Industry Trends
– Exponential Market Growth: Fortune Business Insights projects the global silicon carbide market will surge from $2.6 billion in 2023 to $6.8 billion by 2030. Power electronics, especially for electric vehicles (EVs), renewable energy, and data centers, are fueling this demand.
– Automotive Acceleration: Tesla’s use of SiC MOSFETs in Model 3 inverters slashed energy losses by around 10%, setting a new standard for electric vehicles. Most major automakers are now investing in SiC power devices for EVs.
– Global Expansion: As China, the US, and Europe vie for semiconductor supply chain dominance, expect investments in domestic SiC wafer production facilities to rapidly increase.
2. Features, Specs & Pricing
– 8×150 mm G5WW VPE System: Designed by AIXTRON, this reactor can process 8 wafers at a time, enabling mass production with high quality and reduced “edge” losses.
– Defect Density: Fraunhofer IISB’s advanced imaging and defect-mapping can reduce killer crystal defects (like micropipes) below industry thresholds, which is critical; even a single defect can render a high-voltage power device unreliable.
– Relative Pricing: As of 2024, 150 mm SiC wafer prices are still 5–10x higher than equivalent silicon, though this gap is closing rapidly as yields improve and more fabs come online.
3. Security & Sustainability
– Eco-Advantage: SiC devices reduce electricity losses, supporting both global emissions targets and lower operational costs (source: IEEE Power Electronics Magazine).
– Resource Efficiency: The ability to fabricate more chips per batch conserves raw materials and water, reducing the semiconductor industry’s ecological footprint.
4. Compatibility & How-To Steps
– Device Compatibility: Existing fabs often need upgrades (not complete rebuilds) to handle 150 mm SiC wafers. Transitioning to SiC involves:
1. Installing upgraded wafer carriers and handling robots.
2. Tuning etching and deposition recipes for the new wafer thickness/hardness.
3. Training staff on new defect inspection and yield management protocols.
5. Real-World Use Cases
– Energy Grids: SiC power modules in smart grids boost efficiency and stability during peak loads and renewable integration.
– Medical Imaging: SiC diodes are used in PET scanners for improved accuracy, thanks to their speed and low noise.
– Railways: High-speed train electrics with SiC inverters are lighter and more efficient, allowing higher speeds and lower energy consumption.
6. Reviews, Comparisons, and Limitations
– SiC vs. GaN (Gallium Nitride): Both are wide bandgap materials, but SiC excels at higher voltages and larger modules, while GaN is optimal for low-voltage, high-frequency consumer power adapters.
– Main Limitation: Mechanical hardness (Mohs 9.5) makes SiC extremely tough to cut, polish, and inspect—major cost and processing hurdles versus conventional silicon.
– Yield Risks: Even with advanced defect reduction, high-voltage SiC wafers can have lower manufacturing yields than silicon, impacting costs until industry maturity improves.
—
Most Pressing Reader FAQs: Answered
Q1: Will 150 mm SiC wafer technology lower the price of EVs and solar inverters soon?
– Yes. Wider wafers will drive per-device costs down—potentially by 40–60% within the next 3–5 years as more production lines scale up. Expect this to accelerate the adoption of affordable EVs and grid-scale renewables.
Q2: Is SiC manufacturing environmentally friendly?
– Increasingly so. While initial processing can be energy-intensive, the downstream savings in electricity and carbon emissions are substantial. The technology also supports device miniaturization, further reducing material waste.
Q3: How does this benefit consumers directly?
– Better device performance, longer lifespans, and lower energy bills due to higher efficiency in everything from home appliances to electric vehicles to public infrastructure.
For more details, check leading research at Fraunhofer.
—
Actionable Recommendations & Quick Tips
– Invest in Knowledge: If you’re in engineering, prioritize learning about wide bandgap materials—this is the future of power electronics.
– Follow Industry Announcements: Monitor press releases and updates from leading SiC equipment makers and research institutes for partnership, pricing, and roadmap updates.
– Adopt Early (for Businesses): If your industry relies on power management (EV, renewables, medical devices), be proactive in trialing SiC-based modules—the cost/performance ratio is set to rapidly overtake traditional silicon.
– Request Certifications: When sourcing SiC devices, ensure suppliers use advanced defect reduction techniques certified by institutes like Fraunhofer.
—
Conclusion: Silicon Carbide’s 150 mm Leap Is Just the Beginning
AIXTRON and Fraunhofer IISB’s collaboration isn’t just about making bigger wafers—it is setting a new standard for speed, efficiency, and reliability across the tech landscape. Keep an eye out: over the next decade, SiC will quietly but profoundly reshape everything from your EV’s battery to the local electricity grid.
Stay updated on semiconductor innovation by visiting the official pages of AIXTRON and Fraunhofer.