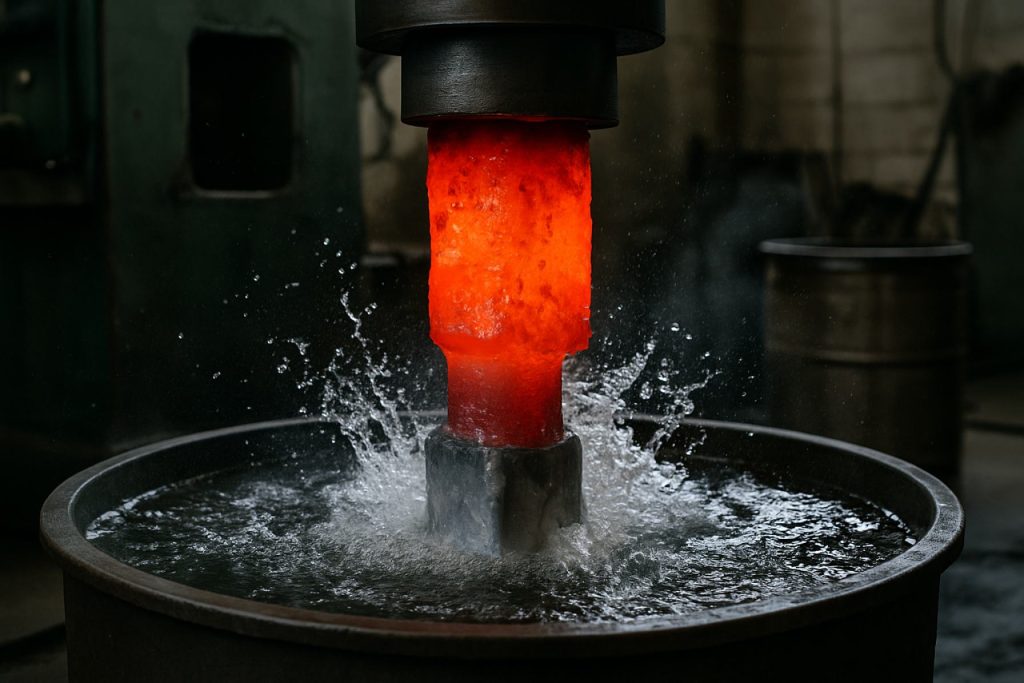
2025’s Quench-Forged Titanium Alloys Surge: How Disruptive Fabrication Advances Are Redefining Aerospace and Beyond. Discover the Emerging Leaders, Market Forecasts, and Technology Trends Set to Dominate the Next 5 Years.
- Executive Summary: Key Findings for 2025–2030
- Global Market Size & Growth Forecasts
- Major Applications: Aerospace, Defense, Medical, and Automotive
- Innovations in Quench-Forged Titanium Alloy Fabrication Processes
- Leading Companies and Industry Organizations (e.g., boeing.com, titanium.org)
- Supply Chain and Raw Material Trends
- Competitive Landscape and Strategic Partnerships
- Regulatory Landscape and Industry Standards (e.g., asme.org, sae.org)
- Emerging Markets and Regional Opportunities
- Future Outlook: Technology Roadmap and Investment Hotspots
- Sources & References
Executive Summary: Key Findings for 2025–2030
The period from 2025 to 2030 is poised to witness significant advancements and industrial scaling in the fabrication of quench-forged titanium alloys. This next-generation processing method—combining rapid quenching with high-pressure forging—continues to gain traction due to its promise of improved microstructural control, enhanced mechanical performance, and reduced manufacturing costs compared to conventional titanium alloy processing. Major aerospace, automotive, and biomedical stakeholders are increasing their investments in quench-forged titanium technology, aiming to address both performance and sustainability imperatives for high-value applications.
Key industry leaders such as TIMET (Titanium Metals Corporation) and VSMPO-AVISMA have expanded their R&D efforts and pilot production lines for advanced titanium alloy processing. These companies are focusing on optimizing quench-forged products for critical aerospace components—like landing gear and engine parts—where weight reduction and superior fatigue resistance are essential. TIMET is leveraging its vertically integrated supply chain to scale up new quench-forging solutions, while VSMPO-AVISMA, the world’s largest titanium producer, is collaborating with major airframers and engine manufacturers to validate the technology for serial production.
Industrial data from 2025 show that quench-forged titanium alloys can achieve up to 20% higher ultimate tensile strength and up to 30% greater fatigue life over conventionally processed counterparts, according to technical disclosures by primary manufacturers. This performance boost is critical for aerospace OEMs and tier-1 suppliers, such as Rolls-Royce and GE Aerospace, both of whom have partnered with titanium producers to qualify new alloys for aero-engine and airframe applications. The automotive sector, led by innovators like Tata Motors and BMW Group, is also evaluating quench-forged titanium for lightweight structural and powertrain components, seeking to balance improved strength-to-weight ratios with cost constraints.
Looking ahead, the outlook for 2025–2030 is characterized by an acceleration in commercial adoption, driven by a convergence of factors: stricter emissions regulations, surging demand for lightweighting, and increasing sustainability requirements. Titanium industry associations anticipate that quench-forged alloys will capture a growing share of the high-performance titanium market, particularly in aerospace and medical fields. The ongoing investments by primary producers and end-users are expected to result in further process innovations, enhanced alloy chemistries, and standardized quality benchmarks for quench-forged products.
In summary, the fabrication of quench-forged titanium alloys is entering a pivotal growth phase, with industrial-scale deployments, performance validation, and market penetration set to define the sector’s trajectory through 2030.
Global Market Size & Growth Forecasts
The global market for quench-forged titanium alloys fabrication is projected to experience steady growth in 2025 and the following few years, driven by escalating demand from aerospace, automotive, energy, and medical device sectors. Quench-forging, a process that combines rapid cooling (quenching) with high-pressure forging, enhances the mechanical properties of titanium alloys, making them especially attractive in applications requiring superior strength-to-weight ratios and corrosion resistance.
Major aerospace manufacturers such as Boeing and Airbus are increasing their use of advanced titanium alloys in both commercial and defense aircraft, directly stimulating demand for quench-forged components. These alloys are pivotal in producing landing gear, fasteners, and structural airframe elements, where durability and weight savings translate into performance and fuel efficiency gains. In 2025, the civil aviation sector is expected to remain the single largest consumer of quench-forged titanium alloys, a trend reinforced by ongoing fleet renewals and the push for more sustainable air travel technologies.
Automotive industry adoption of quench-forged titanium alloys is also rising, especially among high-performance vehicle manufacturers such as Tesla and BMW Group, who are integrating these materials into chassis and engine parts to meet stringent emissions regulations and enhance electric vehicle performance. The energy sector, with companies like GE and Siemens, is expanding the use of titanium alloys in turbines and offshore equipment due to their resilience in harsh operating environments.
Key producers and fabricators include TIMET (a subsidiary of Precision Castparts Corp.), VSMPO-AVISMA (the world’s largest titanium producer), and ATI (Allegheny Technologies Incorporated). These companies are investing in new quench-forging capabilities and expanding their global footprint to address growing demand, with significant capacity expansions announced for 2025 and beyond.
Looking ahead, Asia-Pacific—particularly China and Japan—continues to emerge as a key region for growth, supported by government-backed aerospace and industrial programs. Companies such as BAOTI and Toyota Motor Corporation are increasing investments in titanium alloy research and fabrication capabilities.
Overall, the outlook for quench-forged titanium alloys fabrication is robust, with forecasted annual growth rates in the mid-to-high single digits through the late 2020s, underpinned by technology advances and expanding applications across high-value industries.
Major Applications: Aerospace, Defense, Medical, and Automotive
Quench-forged titanium alloys fabrication stands at the forefront of advanced materials engineering in 2025, with significant momentum in aerospace, defense, medical, and automotive sectors. This technique, which combines rapid quenching after forging, produces refined microstructures resulting in superior strength-to-weight ratios, fatigue resistance, and corrosion resilience. These properties are increasingly crucial as industries seek materials that meet rigorous performance and sustainability standards.
In aerospace, quench-forged titanium alloys are becoming pivotal for next-generation aircraft and spacecraft. Major manufacturers such as Boeing and Airbus continue to expand their use of titanium alloy components in airframes and engine parts to reduce weight and improve fuel efficiency. International Titanium Association reports that demand for advanced forged titanium is projected to rise steadily, driven by new commercial aircraft programs and increased satellite launches. Additionally, companies like Rolls-Royce are leveraging these alloys for turbine blades and structural components, capitalizing on their high-temperature performance.
The defense sector’s reliance on quench-forged titanium alloys is also intensifying. Titanium’s high strength and light weight make it ideal for armored vehicles, naval vessels, and missile systems. In 2025, suppliers such as TIMET and VSMPO-AVISMA are scaling up capacity to meet increased demand for military-grade forgings, especially as global defense budgets remain elevated. These alloys are critical for next-generation fighter jets, including the F-35 and emerging unmanned aerial vehicles, where performance and survivability are paramount.
Medical device manufacturers are another major end-user, leveraging quench-forged titanium for orthopedic implants, dental fixtures, and surgical instruments. Companies like Smith & Nephew and Zimmer Biomet adopt these materials to deliver biocompatibility, fatigue strength, and longevity demanded by modern healthcare standards. With an aging global population and growth in elective surgeries, demand for high-performance titanium implants is expected to continue rising.
In the automotive industry, the drive for electric vehicle (EV) innovation and lightweighting is prompting greater adoption of quench-forged titanium alloys for components such as suspension systems, connecting rods, and exhaust systems. Leading automotive suppliers like Magna International and TI Fluid Systems are exploring titanium-based solutions to improve efficiency and reduce emissions. The outlook for 2025 and beyond indicates a steady increase in titanium alloy adoption as manufacturers balance performance, durability, and regulatory compliance.
Overall, the outlook for quench-forged titanium alloys fabrication is robust across major industries, with ongoing innovations in processing and supply chain expansion ensuring that these advanced materials will play a central role in high-performance, safety-critical applications in the coming years.
Innovations in Quench-Forged Titanium Alloy Fabrication Processes
The fabrication of quench-forged titanium alloys has seen significant innovation as the industry addresses demands for higher performance, cost efficiency, and sustainability. In 2025, breakthroughs are being driven by the aerospace, automotive, and medical sectors, all of which require lightweight, strong, and corrosion-resistant materials. Quench-forging—a process combining rapid cooling (quenching) and forging—enables refined microstructures in titanium alloys, resulting in enhanced mechanical properties and shape complexity, while minimizing defects.
A key trend is the integration of advanced thermomechanical processing and precise temperature controls. Leading manufacturers, such as TIMET (Titanium Metals Corporation), are optimizing quench-forging cycles for popular alloys like Ti-6Al-4V. Industry reports and technical updates indicate that innovations focus on in-situ monitoring of temperature and deformation during forging, allowing for real-time adjustment of process parameters. This results in improved consistency and tailored properties for critical components, notably in jet engine discs and automotive suspension parts.
Another important development is the use of near-net-shape forging, reducing material waste and machining requirements. Companies such as PCC Forged Products (a division of Precision Castparts Corp) have expanded their capabilities to offer large-scale, quench-forged titanium parts for aerospace and energy sectors. These efforts are complemented by advancements in die design and lubrication technology, which further improve surface finish and dimensional accuracy.
Automation and digitalization are increasingly integral to titanium alloy fabrication. Major suppliers, including VSMPO-AVISMA Corporation, are investing in Industry 4.0 platforms that connect process data across forging lines, enabling predictive maintenance and process optimization. These digital tools not only enhance quality assurance but also support the development of new alloy formulations and forging routes tailored to emerging market requirements.
Sustainability is another focus area, with companies aiming to reduce the carbon footprint of titanium production. Toho Titanium Co., Ltd. is exploring energy-efficient quenching methods and recycling initiatives to reclaim titanium scrap from forging operations. Such steps are aligned with broader industry goals for circularity and environmental responsibility.
Looking ahead, the outlook for quench-forged titanium alloy fabrication is robust, with ongoing investment in process innovation, digital integration, and sustainability measures. As demand from aerospace, medical, and hydrogen economy sectors grows, manufacturers are poised to deliver higher-quality, more sustainable titanium solutions in the next few years.
Leading Companies and Industry Organizations (e.g., boeing.com, titanium.org)
The quench-forged titanium alloys fabrication sector is witnessing notable advancements and strategic investments from key players in the aerospace, defense, and advanced manufacturing industries. As of 2025, several leading companies and industry organizations are shaping the future of quench-forged titanium alloy production, with a focus on scaling capacity, improving material performance, and meeting stringent application requirements.
Among the foremost corporations, Boeing remains a central figure, continually expanding its expertise in titanium alloy integration for both commercial and defense aerospace applications. Boeing’s long-term partnerships with titanium suppliers and its in-house development of next-generation forging processes underpin its commitment to lightweight, high-strength airframe components. The company is actively collaborating with global suppliers to secure sustainable titanium sources and optimize quench-forging protocols for newer alloys, aiming for enhanced fatigue resistance and manufacturability.
TIMET (Titanium Metals Corporation), a subsidiary of Precision Castparts Corp., stands as one of the world’s largest dedicated titanium producers, supplying mill products and forged titanium components for aerospace, chemical processing, and medical sectors. TIMET has invested in advanced quench-forging facilities, leveraging process automation and real-time thermal control to ensure the consistency and reliability of high-performance titanium alloys. Their ongoing R&D efforts target superior metallurgical properties and cost-effective production at scale.
Another important contributor is VSMPO-AVISMA, the world’s largest titanium producer, headquartered in Russia. VSMPO-AVISMA supplies titanium ingots, slabs, and forged parts to major OEMs and tier-one suppliers worldwide. The company is further developing quench-forging techniques to produce fine-grain, high-strength titanium alloys for both civil and military aerospace programs. Despite geopolitical challenges, VSMPO-AVISMA continues to play a crucial role in the global titanium supply chain, particularly for aerospace and energy industries.
Industry organizations such as the International Titanium Association (ITA) also play a pivotal role. The ITA fosters collaboration among manufacturers, end-users, and researchers by organizing technical symposia and publishing best practices related to titanium alloy fabrication, including advancements in quench-forging. Their resources help standardize processes and disseminate insights on alloy development, regulatory compliance, and supply chain resilience.
Looking ahead, these industry leaders and organizations are expected to drive significant progress in quench-forged titanium alloys fabrication. Emphasis is likely to intensify on sustainability, digitalization of forging processes, and the development of new alloys tailored for emerging applications in aerospace, space exploration, and advanced medical devices. The period through 2025 and beyond should see accelerated innovation, tighter supplier collaboration, and the broadening of titanium’s strategic role in high-performance engineering sectors.
Supply Chain and Raw Material Trends
The supply chain for quench-forged titanium alloys is experiencing both opportunities and pressures in 2025, as industry demand accelerates across aerospace, defense, and high-performance sectors. Titanium’s unique blend of strength, weight savings, and corrosion resistance continues to drive interest in advanced forging methods, especially quench-forging, which enables refined microstructures and superior mechanical properties. The fabrication supply chain begins with the sourcing of high-purity titanium sponge or ingot, a process still dominated by a few major producers globally. VSMPO-AVISMA, headquartered in Russia, remains the world’s largest fully integrated titanium producer, though ongoing geopolitical uncertainties and export controls have led manufacturers to diversify sourcing.
Japan’s Toyota Tsusho Corporation and Osaka Titanium Technologies are expanding their role as reliable suppliers of titanium sponge and alloys, especially for Asian and Western customers seeking alternatives. The United States, meanwhile, has prioritized domestic titanium alloy production, with TIMET (Titanium Metals Corporation) and Alphatec Alloy boosting investment in melt capacity and downstream forging operations. These companies are refining quench-forging lines for aerospace-grade products, focusing on tighter process control, reduced energy consumption, and improved traceability.
Quench forging itself relies on specialized high-speed presses and precise thermal management. Equipment suppliers such as Schuler Group are collaborating with titanium fabricators to deliver advanced forging systems that integrate in-line rapid quenching, essential for achieving the desired microstructures. There is a growing trend towards vertical integration, with major titanium alloy producers acquiring or partnering with forging specialists to secure their supply chains and reduce lead times. For example, Precision Castparts Corp. (a Berkshire Hathaway company) operates both melt and advanced forging facilities, ensuring end-to-end control of titanium alloy component production.
Raw material price volatility remains a concern. Prices for titanium sponge and scrap have been elevated due to strong demand and intermittent disruptions in mining and refining, particularly in China and Russia. This has pushed manufacturers to invest in recycling and scrap reclamation programs. Organizations such as International Titanium Association report that closed-loop recycling within the quench-forged alloys sector is rising, with scrap now constituting up to 30% of feedstock at some Western facilities.
Looking ahead to 2026 and beyond, the outlook suggests continued investment in domestic and allied titanium supply capacity, innovations in forging automation, and tighter integration between raw material producers and fabricators. These efforts are expected to stabilize supply, improve efficiency, and support the expanding applications of quench-forged titanium alloys in next-generation aerospace, energy, and medical technologies.
Competitive Landscape and Strategic Partnerships
The competitive landscape for quench-forged titanium alloys fabrication is rapidly evolving in 2025, driven by the convergence of aerospace, defense, automotive, and industrial sectors requiring high-performance, lightweight materials. The segment is characterized by established titanium producers intensifying their investments in advanced forging and thermal processing capabilities, alongside emerging players leveraging proprietary quenching technologies for improved alloy properties. Strategic partnerships, joint ventures, and collaborations with end-users and technology providers remain pivotal in accelerating innovation and market penetration.
Key players such as TIMET (Titanium Metals Corporation) and VSMPO-AVISMA continue to hold dominant positions due to their vertically integrated operations and global supply chains. TIMET has focused on expanding its quench-forging capacity in North America and Europe, aiming to meet surging demand from the aerospace OEMs and Tier 1 suppliers. VSMPO-AVISMA, recognized as the world’s largest titanium producer, is reinforcing its partnerships with major aircraft manufacturers and exploring joint research into next-generation quench-forged alloys with improved fatigue resistance and manufacturability.
In Asia, Baoji Titanium Industry Co., Ltd. (BAOTI) stands out as a leading manufacturer ramping up its advanced forging lines and automation for high-purity titanium alloy production. The company is actively engaging with both domestic and international aerospace and medical device firms to co-develop application-specific quench-forged alloys. Additionally, Japanese producers like Toyota Tsusho Corporation are expanding their titanium supply networks and collaborating on R&D initiatives focused on automotive-grade titanium forgings.
Strategic partnerships are playing a crucial role in driving innovation. For example, several leading aerospace and defense primes have entered multi-year agreements with titanium fabricators to secure long-term supplies of quench-forged components. These alliances often include joint investment in process digitization, sustainable energy integration, and circular economy initiatives for titanium scrap recycling. Notably, alliances with technology providers specializing in high-speed forging presses and advanced quenching systems are enabling fabricators to achieve tighter tolerances and enhanced microstructural control.
Looking forward to the next few years, the competitive landscape is expected to remain dynamic as established and emerging players invest in intellectual property, automation, and advanced analytics to optimize quench-forged titanium fabrication. Intensifying regulatory and sustainability demands are also prompting strategic partnerships aimed at reducing carbon footprints, further consolidating the roles of key industry leaders and innovative newcomers in shaping the future of high-performance titanium alloy manufacturing.
Regulatory Landscape and Industry Standards (e.g., asme.org, sae.org)
The regulatory landscape governing quench-forged titanium alloys fabrication is evolving rapidly as the demand for high-performance materials grows across aerospace, automotive, and energy sectors. In 2025, industry standards are largely set and maintained by organizations such as ASME (American Society of Mechanical Engineers) and SAE International. These bodies provide the technical frameworks and certification benchmarks necessary for the safe and consistent production of titanium alloys, particularly those subjected to quenching and forging processes.
ASME’s Boiler and Pressure Vessel Code (BPVC) continues to be a cornerstone for pressure-containing components fabricated from titanium alloys, including those made using quench-forging. The latest 2025 edition incorporates updates for additive and advanced manufacturing, explicitly referencing heat treatment parameters and mechanical property requirements for forged titanium parts. This ensures that quench-forged components used in critical applications like power generation and chemical processing meet rigorous safety and performance criteria. Manufacturers seeking ASME certification must now provide detailed process documentation and material traceability for titanium alloy products.
SAE International maintains several key standards, such as AMS 4928 and AMS 4911, which specify chemical composition, mechanical properties, and processing routes for titanium alloys, including those subjected to quenching and forging. In 2025, SAE is in the process of harmonizing these standards with international equivalents (e.g., ISO 5832-3 for biomedical applications) to streamline global supply chains. An emphasis is placed on repeatable microstructural characteristics, fracture toughness, and resistance to hydrogen embrittlement—properties that are directly influenced by quench-forging parameters. SAE’s active committees are expected to release further revisions within the next two years, reflecting ongoing advances in process control and non-destructive evaluation techniques.
Major industry participants, including TIMET (Titanium Metals Corporation) and VSMPO-AVISMA, play a collaborative role in shaping and adopting these standards. Both companies operate large-scale forging and heat treatment facilities and are instrumental in providing technical feedback to standards organizations. They also maintain their own internal quality systems, often exceeding baseline industry requirements to address the specific needs of aerospace OEMs and defense clients. These internal protocols are frequently audited in conjunction with ASME and SAE certifications.
Looking ahead, regulatory bodies are expected to increase their focus on digital process monitoring and lifecycle traceability as part of the certification process. With sustainability and supply chain transparency growing in importance, new standards may soon include requirements for environmental impact reporting and recycled content disclosure for titanium alloys. As the market for high-strength, quench-forged titanium expands, the interplay between evolving standards and advanced fabrication technologies will remain a critical factor in enabling innovation while ensuring safety and quality.
Emerging Markets and Regional Opportunities
The global market for quench-forged titanium alloys fabrication is experiencing a notable shift in 2025, as emerging economies ramp up investments in advanced manufacturing and aerospace industries. Historically dominated by North American, European, and Japanese producers, the sector is witnessing increased activity from Asia-Pacific countries, particularly China, India, and South Korea. This expansion is driven by rising demand in aerospace, automotive, medical, and energy sectors, as well as governmental policies supporting domestic titanium supply chains.
In China, the accelerated growth of the aerospace sector and renewed focus on self-sufficiency have propelled local companies such as BAOTI Group—the nation’s largest titanium producer—into developing quench-forged alloy capabilities. BAOTI has invested in state-of-the-art forging and quenching lines, aiming to capture a larger share of global and domestic aircraft component supply. Similarly, CITIC Group has expanded its metal fabrication division, with targeted R&D efforts to enhance titanium alloy processing for high-performance applications.
India is positioning itself as a regional fabrication hub, buoyed by government initiatives such as “Make in India” and investments in defense and space exploration. Companies like Mishra Dhatu Nigam Limited (MIDHANI) are scaling up titanium alloy forging capacity, with a particular focus on precision quenching techniques to meet stringent aerospace and medical standards. MIDHANI’s 2025 plans include new advanced heat treatment lines to support both domestic and export markets.
Meanwhile, South Korea’s POSCO, traditionally a steel giant, has expanded into titanium alloys, leveraging its metallurgical expertise and advanced production infrastructure. POSCO’s titanium division is targeting energy and chemical processing equipment manufacturers, capitalizing on regional demand for corrosion-resistant and high-strength materials.
In the Middle East, the United Arab Emirates is emerging as a specialized producer of high-value titanium products, supported by strategic investments in aerospace and industrial manufacturing. Joint ventures and partnerships with established global players are fostering technology transfer and local expertise development.
The outlook for 2025 and beyond suggests continued growth in quench-forged titanium alloys fabrication across these regions. As global supply chains diversify and the need for lightweight, high-performance materials intensifies, emerging markets are expected to play a pivotal role in shaping the industry landscape. Strategic collaborations, technology upgrades, and government backing will be key drivers, while established firms from the US, Europe, and Japan are anticipated to seek joint ventures and local partnerships to maintain their competitive edge.
Future Outlook: Technology Roadmap and Investment Hotspots
The outlook for quench-forged titanium alloys fabrication in 2025 and the subsequent years is shaped by a combination of technological advancements, increased industry demand, and robust investment interest, particularly from aerospace, defense, and medical device manufacturers. The global drive for lighter, stronger, and more corrosion-resistant materials positions quench-forged titanium alloys at the forefront of next-generation manufacturing strategies.
As of 2025, several leading titanium producers and fabricators are accelerating R&D to refine quench-forging processes. TIMET (Titanium Metals Corporation), a major supplier of titanium alloys, is actively exploring advanced quenching techniques aimed at enhancing mechanical properties and production yields. Their focus includes optimizing cooling rates and forging sequences to tailor microstructures for high-performance applications. Similarly, VSMPO-AVISMA Corporation, the world’s largest titanium producer, has announced investments in modernizing its forging lines and heat treatment facilities, with a keen interest in scaling up alloy grades specifically engineered for aerospace and energy sectors.
Technological roadmaps for the next few years emphasize the integration of digital process control, sensor-driven quality assurance, and hybrid manufacturing. Baoji Boegger Industrial Co., Ltd. and other Chinese titanium specialists are deploying automated quench-forging systems to reduce cycle times and energy consumption, while also ensuring batch-to-batch consistency—a critical factor for medical and aerospace certifications. Industry bodies such as the International Titanium Association are facilitating collaborative forums and standards development to accelerate adoption of these advanced fabrication methods.
From an investment standpoint, hotspots are emerging in regions with strong aerospace and medical technology clusters. The United States and Western Europe remain central, driven by defense modernization and commercial aviation renewal programs. However, significant capital is also flowing into Asia-Pacific, where rapid industrialization and government-led initiatives are fostering local titanium alloy supply chains.
Looking ahead, the successful commercialization of quench-forged titanium alloys will depend on continued innovation in alloy chemistries, process automation, and sustainable manufacturing practices. Companies leading in intellectual property and production scalability—such as TIMET and VSMPO-AVISMA Corporation—are expected to capture early market share, while new entrants may focus on niche applications or regional supply. Industry analysts anticipate strong growth through 2030, as quench-forged alloys enable performance breakthroughs in aerospace, medical implants, and future mobility solutions.
Sources & References
- VSMPO-AVISMA
- Rolls-Royce
- GE Aerospace
- Boeing
- Airbus
- Siemens
- TIMET
- ATI
- Toyota Motor Corporation
- TIMET
- Smith & Nephew
- Zimmer Biomet
- Magna International
- PCC Forged Products
- Toyota Tsusho Corporation
- Osaka Titanium Technologies
- Schuler Group
- Precision Castparts Corp.
- ASME (American Society of Mechanical Engineers)
- POSCO