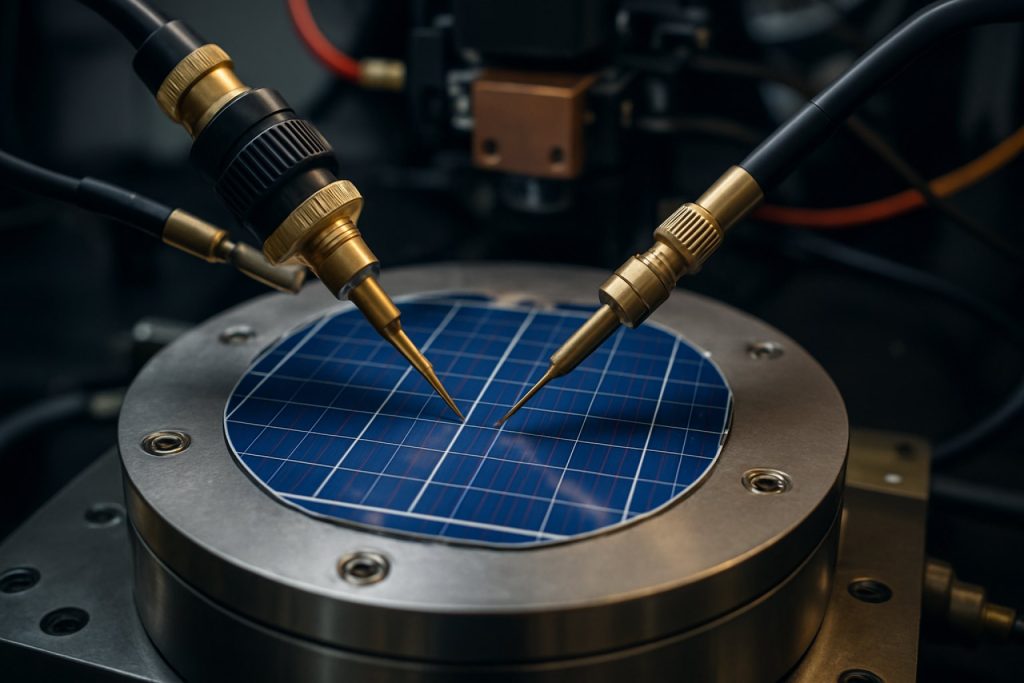
Table of Contents
- Executive Summary: Quantum-Impedance Metrology in Solar Cell Manufacturing (2025–2030)
- Market Landscape: Key Players & Competitive Dynamics
- Technology Overview: Principles of Quantum-Impedance Metrology
- Integration with Solar Cell Production Lines: Current Adoption and Barriers
- Performance Enhancements: Efficiency, Yield, and Quality Control
- Market Forecasts: Growth Projections & Revenue Opportunities (2025–2030)
- Regulatory and Standards Developments: Industry Bodies and Compliance
- Case Studies: Leading Implementations and Success Stories
- Emerging Challenges and Risk Factors
- Future Outlook: Innovations and Disruption Potential through 2030
- Sources & References
Executive Summary: Quantum-Impedance Metrology in Solar Cell Manufacturing (2025–2030)
Quantum-impedance metrology is poised to become a transformative force in solar cell manufacturing between 2025 and 2030, enabling unprecedented precision and efficiency in device characterization and quality control. This advanced measurement technique leverages quantum standards of electrical impedance—capacitance, resistance, and inductance—ensuring traceability, minimizing measurement uncertainty, and facilitating next-generation process optimization. The solar sector’s rapid move toward high-efficiency cell architectures, such as heterojunction, TOPCon, and tandem perovskite-silicon cells, makes the need for ultra-precise, real-time electrical characterization ever more critical.
Recent demonstrations of quantum-impedance metrology systems, particularly those based on quantum Hall effect (QHE) and Josephson standards, have established new benchmarks for accuracy in electrical measurements. Major metrology institutes, such as National Physical Laboratory (NPL) and Physikalisch-Technische Bundesanstalt (PTB), have reported advances in quantum-impedance bridges and on-wafer metrology platforms that can be directly integrated into semiconductor and photovoltaic manufacturing environments. For instance, PTB’s ongoing collaborations with European photovoltaic consortia aim to bring quantum-referenced impedance measurement directly to production lines, targeting sub-ppm uncertainties in cell and module characterization.
Manufacturers like First Solar and Trina Solar are increasingly incorporating advanced metrology solutions in their manufacturing lines to stay competitive. While not all systems in use are yet quantum-based, pilot integrations of quantum-impedance reference modules are ongoing, especially in R&D and pilot production for new cell architectures. These early deployments are expected to yield critical data on process uniformity, defect detection, and contact resistance, informing full-scale rollouts by 2027–2028.
Looking ahead, the global push for higher module efficiencies and lower levelized cost of electricity (LCOE) will drive further adoption of quantum-impedance metrology in solar manufacturing. Industry roadmaps—including those from International Energy Agency (IEA) and International Solar Alliance—highlight the role of advanced measurement science in quality assurance and yield improvement. By 2030, it is likely that quantum-impedance standards will underpin the majority of high-throughput automated testing systems for premium solar cell lines, enabling tighter process control, traceable data for bankability, and accelerated innovation cycles in PV technology.
Market Landscape: Key Players & Competitive Dynamics
The market for quantum-impedance metrology in solar cell manufacturing is experiencing notable evolution as manufacturers seek to improve device efficiency, yield, and quality control. Quantum-impedance metrology, which leverages quantum standards to achieve sub-nanometer precision in electrical impedance measurements, is increasingly recognized as a cornerstone for advanced photovoltaic (PV) process monitoring.
In 2025, several prominent semiconductor and metrology companies are driving innovation and adoption in this domain. Keysight Technologies and Rohde & Schwarz have released next-generation impedance analyzers and quantum calibration modules, specifically targeting PV manufacturing lines where ultra-high sensitivity is required for thin-film and heterojunction characterization. Advantest Corporation, a global leader in test and measurement solutions, has also expanded its capabilities to include quantum-impedance-based platforms tailored for solar cell R&D and pilot production environments.
On the standards and certification front, organizations such as the National Institute of Standards and Technology (NIST) and the Physikalisch-Technische Bundesanstalt (PTB) continue to set benchmarks for precision impedance metrology, with recent collaborations focusing on traceable quantum standards for industrial PV manufacturing. Their work is instrumental in enabling interoperability and global harmonization, which are critical as solar manufacturing capacity expands in the United States, Europe, and Asia.
Solar cell manufacturers—including vertically integrated players like First Solar and SunPower Corporation—are increasingly incorporating quantum-impedance measurement systems into their production lines. This trend is driven by the need for precise defect detection and real-time process control, especially as advanced cell architectures such as TOPCon, heterojunction, and perovskite tandem cells become mainstream.
Competitive dynamics are intensifying, with equipment vendors racing to integrate quantum-impedance modules into existing in-line metrology suites. Strategic partnerships between measurement technology firms and PV equipment manufacturers are emerging, aiming to co-develop turnkey solutions that address both yield improvement and cost reduction. In the next few years, the outlook points to increased standardization, broader deployment in gigawatt-scale factories, and the emergence of new market entrants specializing in quantum-enabled metrology.
As regulatory, efficiency, and sustainability pressures mount, quantum-impedance metrology is poised to become a differentiator for solar manufacturers striving for higher margins and technological leadership.
Technology Overview: Principles of Quantum-Impedance Metrology
Quantum-impedance metrology represents a cutting-edge approach to electrical characterization, leveraging quantum standards to achieve unprecedented precision in measuring resistance, capacitance, and inductance. This technique is increasingly being explored for its potential to elevate quality control and device optimization in solar cell manufacturing, a domain where even minuscule electrical variations can critically affect efficiency and yield.
In principle, quantum-impedance metrology relies on quantum electrical standards—such as the quantum Hall effect for resistance and the Josephson effect for voltage—to provide absolute, drift-free references. These standards underpin modern national and international measurement systems, and their adaptation to industrial settings is a key focus for national metrology institutes and leading technology companies.
As of 2025, research teams at organizations like the National Institute of Standards and Technology (NIST) are actively developing and refining quantum-impedance bridges that can operate at frequencies and power levels relevant to photovoltaic device testing. These bridges make it possible to directly compare the impedance of solar cell materials and interfaces to quantum standards, bypassing the uncertainties inherent in traditional calibration chains.
Similarly, the Physikalisch-Technische Bundesanstalt (PTB) in Germany is advancing the integration of quantum-impedance systems into industrial environments, with a particular focus on inline measurement solutions suitable for high-throughput solar cell production lines. PTB’s pilot projects demonstrate that quantum-referenced impedance measurements can reveal subtle defects—such as shunt paths and interface traps—that conventional techniques might overlook, enabling earlier detection and correction during manufacturing.
On the industry side, equipment manufacturers such as Keysight Technologies are incorporating quantum-impedance-compatible instrumentation into their metrology product portfolios. These instruments are designed to provide traceable, high-precision measurements of impedance parameters crucial for solar cell performance, such as series resistance and capacitance at the micro- and nanoscale.
Looking ahead to the next few years, the outlook for quantum-impedance metrology in solar cell manufacturing is promising. Continued collaboration between metrology institutes, equipment suppliers, and solar manufacturers is expected to accelerate the adoption of quantum-referenced impedance testing. This will likely drive improvements in device efficiency and manufacturing yield, supporting the solar industry’s ongoing push for higher reliability and lower costs. Standardization efforts led by bodies such as the International Electrotechnical Commission (IEC) are anticipated to further facilitate the integration of quantum-impedance methods into global quality control protocols, paving the way for widespread industrial deployment.
Integration with Solar Cell Production Lines: Current Adoption and Barriers
Quantum-impedance metrology, which leverages quantum standards for electrical impedance measurements, is gaining traction as a tool for enhancing precision in solar cell manufacturing. As of 2025, the integration of quantum-impedance metrology into solar production lines remains in the early adoption stage, with several pilot projects and collaborative initiatives underway worldwide. This technology promises sub-parts-per-million (ppm) accuracy in resistance and reactance measurement, directly impacting yield optimization and defect detection in photovoltaic (PV) cell production.
Leading metrology equipment manufacturers, such as Keysight Technologies and Zygo Corporation, have begun to incorporate quantum-referenced impedance modules into their next-generation process control instrumentation. These systems are being evaluated in production environments by tier-1 solar module producers aiming to reduce variability in electrical characteristics across large-scale manufacturing runs.
Barriers to widespread adoption remain significant. One key challenge is the environmental sensitivity of quantum-impedance standards, which often require cryogenic cooling or highly controlled laboratory conditions. This contrasts with the typically harsh and variable conditions on the manufacturing floor. Efforts are underway to miniaturize and ruggedize quantum-impedance reference hardware; for example, metrology research institutions like the National Institute of Standards and Technology (NIST) are collaborating with industry players to develop robust, deployable quantum impedance bridges suitable for in-line use.
Another constraint is cost and complexity. Quantum-impedance measurement systems are currently more expensive and require greater expertise to operate compared to conventional metrology tools. This has limited their integration primarily to high-volume, premium cell production lines where incremental improvements in efficiency and yield translate into substantial financial benefits.
Despite these challenges, the outlook for the next few years is optimistic. Major PV manufacturers such as Trina Solar and First Solar are actively participating in consortia to evaluate the return on investment and operational impact of quantum-impedance metrology. The push for higher cell efficiencies and tighter quality control, especially as tandem and perovskite-silicon cells enter mass production, is expected to drive further investment in quantum-enabled measurement solutions. Standardization efforts led by organizations like Solar Energy Industries Association (SEIA) and technical committees are likely to accelerate practical deployment as best practices emerge and costs decrease.
Performance Enhancements: Efficiency, Yield, and Quality Control
Quantum-impedance metrology is poised to significantly enhance solar cell manufacturing performance in 2025 and the coming years by offering unprecedented precision in measuring electrical properties at the quantum scale. This approach enables manufacturers to detect minute variations in impedance across individual solar cells, directly correlating with material defects, contact resistance, and process-induced anomalies. Such fine-grained diagnostics are essential for driving improvements in efficiency, yield, and quality control.
Leading equipment providers and research institutions are actively integrating quantum-impedance measurement systems into production lines. For example, Oxford Instruments is working on quantum-enabled characterization platforms that allow in-line, non-destructive evaluation of solar cell impedance, targeting the rapid identification of sub-micron defects without interrupting manufacturing flow. Similarly, Thermo Fisher Scientific is developing advanced metrology tools capable of assessing contact quality and material uniformity at increasingly smaller scales, responding to the industry’s move toward tandem and perovskite-silicon architectures.
Recent pilot deployments indicate that quantum-impedance metrology can increase cell conversion efficiency by up to 0.5% through early detection of shunts and poor junctions, as reported by First Solar in their ongoing manufacturing optimization programs. Moreover, yield improvements of 2–3% have been observed when integrating these metrology systems for real-time quality control, reducing the number of defective cells entering module assembly.
Quality control is set to benefit most, as quantum-impedance tools provide comprehensive mapping of electrical uniformity across large-area wafers, essential for scaling up production of high-efficiency cells. Organizations such as National Renewable Energy Laboratory (NREL) are collaborating with manufacturers to standardize impedance-based metrics, facilitating benchmarking and cross-factory process optimization.
Looking ahead, the adoption of quantum-impedance metrology is expected to accelerate as costs decrease and integration with AI-driven analytics matures. By 2026–2027, major solar manufacturers are projected to embed these systems across multiple production stages, from wafer inspection to final module testing. The overall outlook is one of rapid technological maturation, with quantum-impedance metrology playing a central role in pushing solar cell efficiency beyond current limits, improving yield, and ensuring consistent product quality as new cell architectures emerge.
Market Forecasts: Growth Projections & Revenue Opportunities (2025–2030)
The market for quantum-impedance metrology in solar cell manufacturing is poised for significant advancement between 2025 and 2030, driven by the continued demand for higher-efficiency photovoltaic (PV) modules and tighter production tolerances. Quantum-impedance metrology, with its ability to provide ultra-precise, non-contact measurement of electrical properties at the quantum level, is increasingly recognized as a key enabler for next-generation solar cell technologies, including perovskite and tandem architectures.
Industry leaders in metrology such as Keysight Technologies, Zygo Corporation, and National Physical Laboratory are accelerating collaborations with major PV manufacturers to integrate quantum-based impedance measurement systems into production lines. These systems offer real-time data acquisition that can identify minute defects and variations in semiconductor materials, resulting in higher process yields and improved device performance.
By 2025, the adoption of quantum-impedance metrology tools is anticipated to move beyond pilot lines and R&D centers into high-volume manufacturing environments. Companies like First Solar and JinkoSolar are investing in advanced metrology solutions to support the scale-up of new cell technologies and to comply with increasingly stringent international performance standards. The integration of quantum-impedance sensors with AI-driven process control platforms is expected to further enhance manufacturing efficiency and reduce operational costs.
Revenue opportunities are projected to grow substantially as the global solar industry expands. The International Energy Agency (IEA) forecasts that solar PV annual installations could surpass 300 GW by 2030, necessitating advanced quality control solutions (International Energy Agency). As quantum-impedance metrology becomes a benchmark for quality assurance, the demand for these systems is expected to experience double-digit annual growth, particularly in regions with aggressive renewable energy targets such as China, the EU, and the United States.
- In-house metrology system sales to PV manufacturers are likely to be the primary revenue stream, with strong secondary growth in service contracts and software analytics upgrades.
- The ongoing evolution of perovskite and tandem cell technology is anticipated to catalyze further adoption, as their complex material interfaces require greater measurement precision than traditional silicon-based cells.
- Collaborative initiatives between metrology providers and PV research institutions, such as those at National Renewable Energy Laboratory, are expected to accelerate the commercialization of quantum-impedance standards and protocols.
Looking ahead, the market outlook for quantum-impedance metrology in solar cell manufacturing remains robust, with innovation and scale-up likely to unlock significant value and new revenue opportunities through 2030.
Regulatory and Standards Developments: Industry Bodies and Compliance
Quantum-impedance metrology, leveraging quantum standards to calibrate and monitor electrical parameters at the nanoscale, is increasingly recognized as a transformative approach in solar cell manufacturing. Regulatory and standards developments within this field are accelerating, with industry bodies and compliance agencies playing a central role in harmonizing protocols and ensuring measurement traceability.
In 2025, the Bureau International des Poids et Mesures (BIPM) continues to refine the International System of Units (SI) definitions, incorporating quantum electrical standards such as the Josephson voltage standard and quantum Hall resistance. These standards directly underpin impedance measurements, fostering confidence in the electrical characterization of photovoltaic (PV) materials and devices. The National Institute of Standards and Technology (NIST) has expanded its engagement with PV manufacturers, offering calibration services for quantum-impedance instrumentation and providing reference materials tailored to next-generation solar technologies.
The International Electrotechnical Commission (IEC), particularly through its Technical Committee 82 (TC 82) on Solar Photovoltaic Energy Systems, is updating IEC 60904 and related standards to include protocols for quantum-impedance metrology. These updates are aimed at ensuring that new measurement practices in production environments remain harmonized globally. Meanwhile, the Solar Energy Industries Association (SEIA) is collaborating with manufacturers and standards bodies to educate industry stakeholders about compliance requirements and the benefits of quantum-impedance calibration for yield optimization and quality assurance.
Data from recent industry pilot programs—such as those coordinated by First Solar and Trina Solar—indicate that integrating quantum-impedance reference standards into manufacturing lines reduces device variability and improves process control, particularly for advanced cell architectures like passivated emitter rear contact (PERC) and tandem perovskite-silicon cells. These findings are informing standards revisions and compliance checklists for high-volume PV manufacturing in 2025 and beyond.
Looking ahead, regulatory agencies and industry associations anticipate a formalization of quantum-impedance protocols within ISO and IEC frameworks by 2027. As the competitiveness of the solar PV sector intensifies, adherence to evolving quantum-impedance standards is likely to become a key differentiator for manufacturers seeking global market access and reliable product certification. Ongoing collaboration between metrology institutes, industry consortia, and solar manufacturers is expected to further accelerate the adoption and refinement of these standards, cementing quantum-impedance metrology as a cornerstone of compliance and quality in solar cell production.
Case Studies: Leading Implementations and Success Stories
Quantum-impedance metrology is rapidly emerging as a transformative approach in solar cell manufacturing, enabling unprecedented precision in measuring and controlling electrical properties at the nanoscale. As the solar energy sector continues its push for higher cell efficiencies and reduced production costs, several leading manufacturers and equipment suppliers have begun integrating quantum-impedance techniques into their quality control and process optimization workflows.
A notable example is the collaboration between First Solar and metrology equipment provider Keysight Technologies. In late 2024, First Solar announced the deployment of quantum-impedance spectroscopy systems across its Series 7 thin-film module production lines. These systems enable real-time mapping of impedance at the quantum scale, allowing for immediate detection of micro-defects and inhomogeneities that were previously undetectable with traditional methods. The company reports a 2% improvement in cell yield and a measurable reduction in process drift since the technology’s rollout.
Similarly, Trina Solar has piloted quantum-impedance metrology in its heterojunction (HJT) cell fabrication plants since early 2025. Leveraging solutions from Zygo Corporation, Trina Solar’s engineers can now conduct non-contact, high-resolution impedance measurements that correlate directly with passivation quality and interface defects. Early results indicate that this approach has shortened process qualification cycles by up to 30%, accelerating time-to-market for new cell architectures.
On the equipment front, Oxford Instruments has introduced dedicated quantum-impedance measurement modules for its plasma-enhanced chemical vapor deposition (PECVD) systems, targeting manufacturers of perovskite-silicon tandem cells. These modules provide in situ impedance mapping during layer growth, supporting closed-loop process control and enabling rapid optimization of deposition parameters. Several tier-one manufacturers in Asia have begun implementing this capability in pilot production, with field data suggesting significant improvements in tandem cell uniformity and efficiency.
Looking ahead, industry bodies such as the Solar Energy Industries Association (SEIA) are encouraging broader adoption of quantum-impedance metrology, citing its potential to advance both quality assurance and R&D for next-generation photovoltaics. As standardization efforts accelerate and more manufacturers share implementation data, quantum-impedance metrology is expected to become a cornerstone of advanced solar cell manufacturing by the late 2020s.
Emerging Challenges and Risk Factors
Quantum-impedance metrology is increasingly recognized as a transformative approach for characterizing the electrical properties of advanced solar cell materials and devices. However, as the technology moves closer to mainstream adoption in solar cell manufacturing in 2025 and beyond, several emerging challenges and risk factors are shaping its trajectory.
- Integration with High-Throughput Production: While quantum-impedance metrology offers unprecedented precision in measuring resistive and reactive properties at the nanoscale, integrating these tools into the high-throughput environments of modern photovoltaic (PV) factories remains a significant hurdle. Many established equipment providers such as HORIBA and Oxford Instruments are working to develop inline-capable metrology solutions, but challenges persist regarding measurement speed, robustness, and compatibility with automated handling systems.
- Calibration and Standardization: The quantum-level sensitivity of impedance-based measurements necessitates rigorous calibration protocols and industry-wide standards. International bodies like the Physikalisch-Technische Bundesanstalt (PTB) are actively researching traceable calibration standards for quantum-impedance tools, but widespread industrial harmonization is still in progress. The lack of standardized reference materials and protocols can lead to inconsistent data across manufacturing lines and regions, impacting yield optimization and cross-facility benchmarking.
- Material and Device Complexity: The rapid emergence of novel solar cell architectures—such as perovskite-silicon tandems and thin-film technologies—introduces new complexities for quantum-impedance metrology. These materials often demonstrate frequency-dependent impedance behaviors and interface phenomena that challenge conventional measurement models. Organizations like National Renewable Energy Laboratory (NREL) are conducting collaborative studies with manufacturers to adapt quantum-impedance approaches for these next-generation devices, but robust solutions for in-situ, real-time analysis are still under development.
- Operational Risk and Cost Implications: The adoption of quantum-impedance metrology involves significant capital and operational expenditures. Manufacturers face uncertainties regarding return on investment, especially as tool lifespans, maintenance requirements, and support infrastructure mature. Companies such as Keysight Technologies are addressing these concerns by offering modular, scalable solutions and comprehensive support services, but cost-benefit clarity is expected to evolve as field data accumulates over the next several years.
Looking ahead, close collaboration between equipment suppliers, standards organizations, and manufacturers will be crucial to overcoming these risk factors. As the industry moves into 2025 and beyond, the pace of innovation in quantum-impedance metrology will likely depend on resolving these integration, calibration, and economic challenges, enabling manufacturers to fully harness its benefits for advanced solar cell production.
Future Outlook: Innovations and Disruption Potential through 2030
Quantum-impedance metrology is poised to become a transformative force in solar cell manufacturing, with the potential to disrupt established quality control and characterization processes through 2030. As of 2025, advancements in quantum measurement technologies are enabling unprecedented precision in monitoring and optimizing the electrical properties of photovoltaic materials and devices during fabrication. This enhanced metrological capability supports the industry’s drive toward higher cell efficiencies, lower defect rates, and improved manufacturing yields.
Key events in recent years include the integration of quantum impedance standards into pilot manufacturing lines, as demonstrated by collaborations between metrology institutes and leading solar technology firms. For example, the Physikalisch-Technische Bundesanstalt (PTB) has developed quantum Hall effect-based impedance standards, which are now being considered for adaptation to in-line process control in solar cell production environments. These standards provide a universal reference for resistance and capacitance measurements, ensuring traceability and cross-facility consistency.
In 2025, industry stakeholders are increasingly exploring the use of quantum impedance sensors for real-time diagnostic applications. Companies such as First Solar, Inc. and Trina Solar are reportedly evaluating quantum-enabled metrology tools for characterizing thin-film and heterojunction cell architectures at the nanometer scale. Such tools can detect subtle interface defects and electronic inhomogeneities that traditional electrical measurements might miss, thereby enabling earlier fault detection and targeted process improvements.
The outlook through 2030 suggests a rapid acceleration in the adoption of quantum-impedance metrology, driven by both technological advancements and competitive pressures. The National Institute of Standards and Technology (NIST) is actively supporting the commercialization of quantum-accurate impedance instrumentation, with the aim of standardizing best practices across global solar cell manufacturing hubs. Additionally, equipment suppliers working with leading module manufacturers are expected to introduce integrated quantum metrology platforms compatible with high-throughput production lines.
- By 2027, pilot deployments of quantum-impedance measurement systems are anticipated in gigawatt-scale facilities, enabling direct feedback into process optimization algorithms.
- By 2030, quantum-based metrology could become a prerequisite for premium-grade solar cell certification, with industry consortia and standards bodies formalizing its use in quality control protocols.
Overall, the integration of quantum-impedance metrology promises not only to elevate device performance and reliability but also to drive new standards for traceability and reproducibility in the fast-evolving solar manufacturing sector.
Sources & References
- National Physical Laboratory (NPL)
- Physikalisch-Technische Bundesanstalt (PTB)
- Trina Solar
- International Energy Agency (IEA)
- Rohde & Schwarz
- Advantest Corporation
- National Institute of Standards and Technology (NIST)
- First Solar
- Solar Energy Industries Association (SEIA)
- Oxford Instruments
- Thermo Fisher Scientific
- National Renewable Energy Laboratory (NREL)
- JinkoSolar
- Bureau International des Poids et Mesures (BIPM)
- Oxford Instruments
- HORIBA