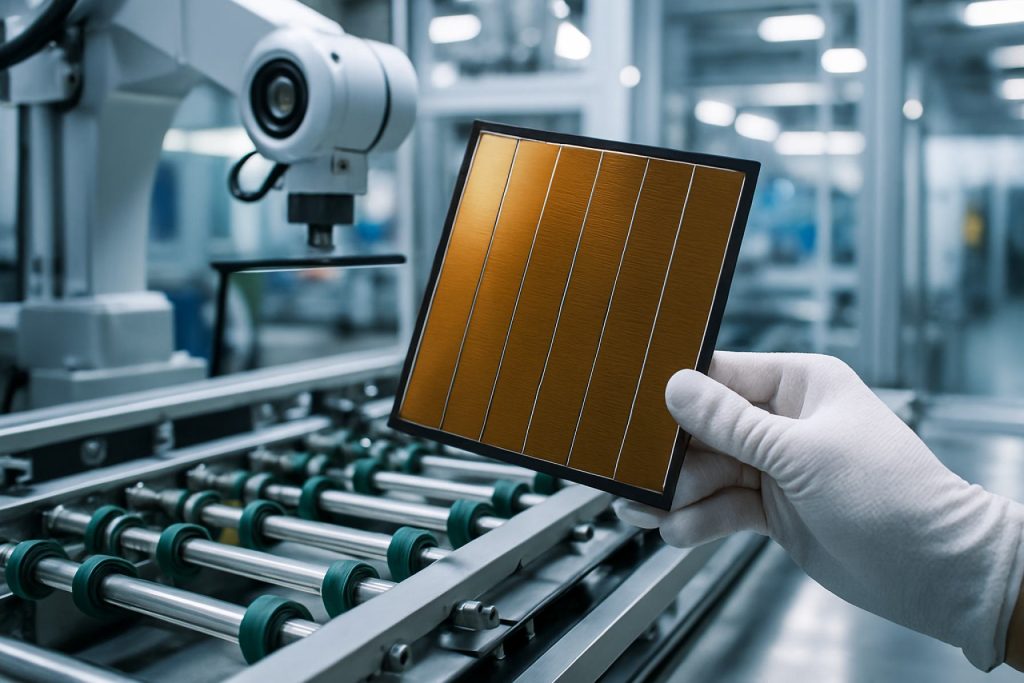
Perovskite Photovoltaic Thin-Film Manufacturing in 2025: Unleashing Next-Gen Solar Efficiency and Market Expansion. Explore How Advanced Materials and Scalable Production Are Shaping the Future of Clean Energy.
- Executive Summary: 2025 Market Landscape and Key Drivers
- Technology Overview: Perovskite Thin-Film Photovoltaics Explained
- Manufacturing Innovations: Scalable Processes and Automation
- Major Players and Industry Alliances (2025 Update)
- Cost Competitiveness and Efficiency Benchmarks
- Supply Chain Dynamics and Raw Material Sourcing
- Regulatory Environment and Industry Standards
- Market Forecasts: 2025–2030 Growth Projections
- Emerging Applications and Integration with Existing PV
- Future Outlook: Challenges, Opportunities, and R&D Directions
- Sources & References
Executive Summary: 2025 Market Landscape and Key Drivers
The perovskite photovoltaic (PV) thin-film manufacturing sector is poised for significant transformation in 2025, driven by rapid technological advancements, increased investment, and the urgent global demand for cost-effective, high-efficiency solar solutions. Perovskite solar cells, known for their tunable bandgaps, lightweight nature, and potential for low-cost production, are transitioning from laboratory-scale innovation to commercial-scale manufacturing. This shift is catalyzed by the need to accelerate renewable energy deployment and meet ambitious decarbonization targets set by governments and industry stakeholders worldwide.
In 2025, several pioneering companies are scaling up perovskite PV manufacturing. Oxford PV, a UK-German company, is at the forefront, operating one of the world’s first volume manufacturing lines for perovskite-on-silicon tandem solar cells. Their Brandenburg facility is expected to ramp up production, targeting module efficiencies above 25%, which surpass conventional silicon-only modules. Similarly, Saule Technologies in Poland is commercializing flexible perovskite modules, focusing on building-integrated photovoltaics (BIPV) and IoT applications, with a pilot line already operational and plans for further capacity expansion in 2025.
Asian manufacturers are also entering the market. TCL, a major Chinese electronics conglomerate, has announced investments in perovskite PV research and pilot production, leveraging its expertise in thin-film processing and large-scale electronics manufacturing. Meanwhile, Hanwha Solutions in South Korea is exploring perovskite-silicon tandem technologies, aiming to integrate them into its Q CELLS solar product line.
Key drivers for the sector in 2025 include the potential for perovskite PV to deliver higher efficiencies at lower costs compared to traditional silicon, the compatibility of perovskite films with roll-to-roll and inkjet printing processes, and the ability to produce lightweight, flexible modules for new market segments. However, challenges remain in scaling up production while ensuring long-term stability and environmental safety of perovskite materials.
Looking ahead, the perovskite PV thin-film manufacturing landscape is expected to see further capacity expansions, new joint ventures, and increased integration with established silicon PV lines. Industry roadmaps suggest that by the late 2020s, perovskite-based modules could achieve commercial lifetimes and bankability, positioning them as a disruptive force in the global solar market.
Technology Overview: Perovskite Thin-Film Photovoltaics Explained
Perovskite thin-film photovoltaics represent a transformative technology in the solar energy sector, offering the potential for high efficiency, low-cost, and flexible solar modules. The core of this technology is the perovskite crystal structure, typically based on hybrid organic-inorganic lead or tin halides, which enables strong light absorption and efficient charge transport. Manufacturing perovskite photovoltaic thin films involves depositing these materials onto substrates using scalable techniques such as solution processing, slot-die coating, inkjet printing, and vapor deposition.
As of 2025, the industry is witnessing rapid advancements in both laboratory and pilot-scale manufacturing. Companies like Oxford Photovoltaics are at the forefront, having developed tandem perovskite-on-silicon solar cells that have achieved certified efficiencies above 28%. Their manufacturing approach leverages vacuum deposition and scalable coating methods to integrate perovskite layers onto existing silicon wafers, aiming for commercial module production at their facility in Germany. Similarly, Saule Technologies specializes in flexible perovskite solar films, utilizing inkjet printing to produce lightweight, semi-transparent modules suitable for building-integrated photovoltaics (BIPV) and consumer electronics.
Another notable player, Microquanta Semiconductor, is scaling up roll-to-roll manufacturing processes for large-area perovskite modules, targeting both rooftop and utility-scale applications. Their pilot lines in China are designed to demonstrate the feasibility of continuous, high-throughput production, a key step toward cost competitiveness with conventional silicon photovoltaics.
The manufacturing process for perovskite thin films typically involves the following steps:
- Preparation of the substrate, often glass or flexible polymers, with a transparent conductive oxide layer.
- Deposition of the perovskite precursor solution or vapor onto the substrate, followed by controlled crystallization to form a uniform, defect-minimized film.
- Application of charge transport layers and metal electrodes to complete the device stack.
- Encapsulation to protect the sensitive perovskite material from moisture and oxygen, which remain challenges for long-term stability.
Looking ahead, the outlook for perovskite thin-film manufacturing is promising. Industry roadmaps anticipate further improvements in stability, upscaling, and environmental safety, with several companies planning to ramp up commercial production by 2026–2027. The sector is also seeing increased collaboration with established photovoltaic manufacturers, such as Hanwha Solutions, which is exploring perovskite-silicon tandem integration. As manufacturing processes mature and module lifetimes extend, perovskite thin-film photovoltaics are poised to play a significant role in the global transition to renewable energy.
Manufacturing Innovations: Scalable Processes and Automation
The landscape of perovskite photovoltaic thin-film manufacturing is undergoing rapid transformation in 2025, driven by the imperative to scale up production while maintaining high efficiency and stability. The transition from laboratory-scale spin-coating to industrially viable, scalable processes is a central focus, with several companies and research consortia spearheading innovations in this domain.
One of the most significant advancements is the adoption of roll-to-roll (R2R) and slot-die coating techniques, which enable continuous deposition of perovskite layers on flexible substrates. These methods are being actively developed and piloted by industry leaders such as Oxford PV, a UK-German company recognized for its pioneering work in perovskite-silicon tandem cells. Oxford PV has reported progress in scaling up their manufacturing lines, targeting gigawatt-scale production capacities and integrating automation to ensure uniformity and reproducibility across large-area modules.
Similarly, Saule Technologies, based in Poland, has commercialized inkjet printing for perovskite solar cells, enabling customizable and scalable production. Their pilot lines demonstrate the feasibility of automated, high-throughput manufacturing, with a focus on lightweight and flexible modules suitable for building-integrated photovoltaics (BIPV) and consumer electronics. Saule Technologies’ approach exemplifies the shift towards digital manufacturing, where process control and automation are integral to quality assurance.
In Asia, Microquanta Semiconductor in China is advancing scalable vapor deposition and blade-coating processes, aiming to bridge the gap between laboratory efficiency records and industrial-scale module production. Their efforts are complemented by investments in in-line monitoring and process automation, which are critical for minimizing defects and ensuring long-term device stability.
Automation is increasingly central to perovskite manufacturing, with robotics and machine learning being deployed for real-time process optimization and defect detection. This trend is supported by collaborative initiatives such as the European Perovskite Initiative, which brings together manufacturers, equipment suppliers, and research institutions to standardize scalable processes and accelerate commercialization.
Looking ahead, the next few years are expected to witness further integration of scalable coating techniques, advanced encapsulation methods, and digital process control. The goal is to achieve high-throughput, low-cost manufacturing while meeting stringent reliability standards. As perovskite technology matures, the convergence of scalable processes and automation will be pivotal in transitioning from pilot lines to mass production, positioning perovskite photovoltaics as a competitive force in the global solar market.
Major Players and Industry Alliances (2025 Update)
The perovskite photovoltaic thin-film manufacturing sector in 2025 is characterized by a dynamic landscape of established companies, innovative startups, and strategic alliances aimed at accelerating commercialization and scaling production. Several major players have emerged as leaders, leveraging proprietary technologies and forging partnerships to address challenges in efficiency, stability, and manufacturability.
Among the most prominent is Oxford Photovoltaics, a UK-based company recognized for its pioneering work in perovskite-on-silicon tandem solar cells. In 2024, Oxford PV announced the ramp-up of its first volume manufacturing line in Germany, targeting commercial module shipments in 2025. The company’s technology has achieved certified efficiencies above 28%, positioning it at the forefront of the industry’s push toward higher-performance solar modules.
Another key player is Meyer Burger Technology AG, a Swiss manufacturer with a strong background in photovoltaic equipment. Meyer Burger has entered the perovskite field through collaborations and investments in tandem cell production, aiming to integrate perovskite layers into its existing silicon module lines. The company’s strategy includes leveraging its established manufacturing expertise to scale up perovskite-silicon tandem modules for the European market.
In Asia, TCL and its subsidiary TCL China Star Optoelectronics Technology have made significant investments in perovskite R&D and pilot production. TCL’s efforts are focused on developing roll-to-roll manufacturing processes and large-area perovskite modules, with pilot lines operational in China as of 2025. These initiatives are supported by collaborations with academic institutions and government-backed research programs.
The sector is also witnessing the rise of specialized startups such as Saule Technologies in Poland, which has commercialized flexible perovskite solar films for building-integrated and IoT applications. Saule’s roll-to-roll production line, launched in 2021, continues to expand, with new partnerships in the construction and electronics sectors announced in 2025.
Industry alliances are playing a crucial role in standardizing processes and accelerating market entry. The SolarPower Europe association has established a dedicated perovskite working group, bringing together manufacturers, equipment suppliers, and research institutes to address supply chain, certification, and recycling challenges. Additionally, cross-industry collaborations—such as those between Oxford Photovoltaics and major glass manufacturers—are facilitating the integration of perovskite layers into architectural glass and building materials.
Looking ahead, the next few years are expected to see further consolidation, with leading players scaling up gigawatt-scale production and new entrants leveraging advances in materials and process engineering. Strategic alliances and joint ventures will likely intensify, as companies seek to secure supply chains and accelerate the path to bankable, high-efficiency perovskite photovoltaic products.
Cost Competitiveness and Efficiency Benchmarks
Perovskite photovoltaic thin-film manufacturing is rapidly advancing toward commercial viability, with 2025 marking a pivotal year for cost competitiveness and efficiency benchmarks. The sector is characterized by a race to achieve high power conversion efficiencies (PCE) while reducing production costs, positioning perovskite solar cells (PSCs) as strong contenders against established silicon-based photovoltaics.
Recent data from leading manufacturers indicate that perovskite modules are now routinely achieving certified efficiencies above 20%, with several companies reporting laboratory-scale tandem cells exceeding 25%. For instance, Oxford PV, a UK-German company specializing in perovskite-silicon tandem technology, announced in 2024 that its commercial-sized modules surpassed 25% efficiency, a significant leap over conventional silicon modules. Similarly, Microquanta Semiconductor in China has reported stable perovskite module efficiencies above 20% on pilot production lines, with ongoing efforts to scale up.
Cost competitiveness is being driven by the inherently low material and energy requirements of perovskite thin-film manufacturing. Unlike silicon, perovskite layers can be deposited at low temperatures using scalable techniques such as slot-die coating and inkjet printing. Saule Technologies, based in Poland, has pioneered roll-to-roll production of flexible perovskite modules, targeting building-integrated photovoltaics (BIPV) and consumer electronics. Their approach leverages lightweight substrates and ambient processing, which significantly reduces capital and operational expenditures compared to traditional silicon wafer production.
Industry outlook for 2025 and the following years suggests that perovskite module manufacturing costs could fall below $0.20/Watt as production scales, approaching or even undercutting the lowest-cost silicon modules. This projection is supported by pilot line data from Oxford PV and Microquanta Semiconductor, both of which are ramping up capacity and targeting gigawatt-scale output by 2026. The International Energy Agency and industry consortia have highlighted perovskite’s potential to disrupt the market, provided that long-term stability and bankability are demonstrated at scale.
In summary, 2025 is set to be a landmark year for perovskite photovoltaic thin-film manufacturing, with efficiency records being broken and cost structures rapidly improving. As leading companies transition from pilot to mass production, perovskite technology is poised to become a mainstream, cost-competitive alternative in the global solar market.
Supply Chain Dynamics and Raw Material Sourcing
The supply chain for perovskite photovoltaic (PV) thin-film manufacturing in 2025 is characterized by rapid evolution, driven by the scaling ambitions of leading companies and the need for reliable, high-purity raw materials. Perovskite PV technology relies on a unique set of precursor chemicals—primarily lead or tin halides, organic cations such as methylammonium or formamidinium, and halide salts—alongside specialized substrates and encapsulation materials. The sourcing and quality control of these materials are critical for both device performance and long-term stability.
Several companies have emerged as key players in the perovskite PV supply chain. Oxford PV, headquartered in the UK and Germany, is a pioneer in perovskite-silicon tandem cell commercialization. The company has established partnerships with chemical suppliers to secure high-purity perovskite precursors and has invested in vertical integration to mitigate supply risks. Similarly, Microquanta Semiconductor in China is scaling up perovskite module production, leveraging domestic chemical manufacturing capabilities to ensure a stable supply of raw materials.
The supply chain is also influenced by the geographic distribution of precursor production. China remains the dominant supplier of many halide salts and organic cations, benefiting from its established chemical industry infrastructure. However, European and North American manufacturers are increasingly seeking to localize supply chains to reduce geopolitical risks and ensure compliance with environmental and safety standards. For example, Saule Technologies in Poland has focused on sourcing materials from within the European Union where possible, aligning with EU sustainability directives.
A significant challenge in 2025 is the need for ultra-high-purity lead and tin compounds, as impurities can drastically affect perovskite film quality and device longevity. Suppliers are responding by developing purification processes tailored to the photovoltaic sector. Additionally, the industry is closely monitoring the regulatory landscape regarding lead usage, with some companies exploring lead-free perovskite alternatives, though these are not yet widely commercialized.
Looking ahead, the perovskite PV supply chain is expected to become more robust and diversified. Strategic partnerships between module manufacturers and chemical suppliers are likely to intensify, with a focus on securing long-term contracts and developing recycling pathways for end-of-life modules. As production scales, the demand for specialized encapsulation materials and transparent conductive substrates is also set to rise, prompting further innovation and investment from established materials companies and new entrants alike.
Regulatory Environment and Industry Standards
The regulatory environment for perovskite photovoltaic (PV) thin-film manufacturing is rapidly evolving as the technology approaches commercial scale in 2025. Regulatory frameworks are being shaped by the need to ensure product safety, environmental sustainability, and market reliability, while also supporting innovation in this emerging sector.
In the European Union, perovskite PV modules are subject to the CE marking process, which requires compliance with directives such as the Low Voltage Directive (LVD), Electromagnetic Compatibility (EMC) Directive, and the Restriction of Hazardous Substances (RoHS) Directive. The RoHS Directive is particularly relevant, as it restricts the use of lead and other hazardous materials—an important consideration given that many high-efficiency perovskite formulations contain lead. The European Commission is actively reviewing the regulatory status of perovskite PV, with industry stakeholders such as Oxford PV and Saule Technologies participating in consultations to ensure that new standards reflect the unique characteristics of perovskite materials.
In the United States, perovskite PV modules must comply with safety and performance standards set by organizations such as Underwriters Laboratories (UL) and the International Electrotechnical Commission (IEC). The National Renewable Energy Laboratory (NREL) is collaborating with industry to develop accelerated testing protocols and reliability standards tailored to perovskite thin films, recognizing that traditional silicon PV standards may not fully capture the degradation mechanisms specific to perovskites.
Globally, the International Electrotechnical Commission (IEC) is in the process of drafting new standards for perovskite PV, with working groups focused on issues such as long-term stability, encapsulation, and environmental impact. Industry leaders like Meyer Burger Technology AG and Hanwha Solutions are actively involved in these standardization efforts, aiming to facilitate international market access and harmonize certification requirements.
Looking ahead, regulatory scrutiny is expected to intensify as perovskite PV manufacturing scales up. Key areas of focus will include lifecycle management, recycling, and the safe handling of lead-containing waste. Industry associations and manufacturers are proactively developing voluntary codes of practice and recycling initiatives to address these concerns and build public trust. As perovskite PV moves toward gigawatt-scale production, alignment with evolving regulatory and industry standards will be critical for widespread adoption and long-term market success.
Market Forecasts: 2025–2030 Growth Projections
The period from 2025 to 2030 is poised to be transformative for perovskite photovoltaic (PV) thin-film manufacturing, as the technology transitions from pilot-scale to commercial-scale production. Several leading companies and consortia are actively scaling up their manufacturing capabilities, with a focus on improving efficiency, stability, and cost-effectiveness of perovskite solar modules.
In 2025, the global perovskite PV market is expected to witness its first significant commercial deployments. Oxford PV, a UK-German company, is at the forefront, having announced plans to ramp up production at its Brandenburg, Germany facility. The company is targeting the integration of perovskite-silicon tandem cells, aiming for module efficiencies above 25%. Oxford PV’s manufacturing line is designed for gigawatt-scale output, and the company has stated its intention to supply commercial modules to the market by 2025.
Similarly, Meyer Burger Technology AG, a Swiss manufacturer known for its high-efficiency PV technologies, has entered the perovskite field through partnerships and R&D investments. Meyer Burger is exploring the integration of perovskite layers into its existing heterojunction cell lines, with pilot production expected to inform commercial scaling decisions by 2026.
In Asia, TCL and its subsidiary TCL China Star Optoelectronics Technology are investing in perovskite PV research and pilot manufacturing, leveraging their expertise in thin-film deposition and large-area coating. These efforts are expected to accelerate the availability of perovskite modules for both utility-scale and building-integrated applications in the region.
Industry bodies such as Solar Energy Industries Association and SolarPower Europe have highlighted perovskite PV as a key technology for the next wave of solar growth, projecting that perovskite-based modules could capture a significant share of new installations by 2030, particularly as manufacturing costs decline and performance improves.
Looking ahead, the market outlook for 2025–2030 anticipates rapid capacity expansion, with several gigawatts of perovskite module production coming online globally. The main drivers will be continued improvements in module lifetimes, the scaling of roll-to-roll and sheet-to-sheet manufacturing processes, and the integration of perovskite layers with established silicon PV lines. As these advances materialize, perovskite thin-film technology is expected to play a pivotal role in meeting global renewable energy targets and driving down the levelized cost of solar electricity.
Emerging Applications and Integration with Existing PV
Perovskite photovoltaic thin-film manufacturing is entering a pivotal phase in 2025, with a strong focus on emerging applications and integration with established photovoltaic (PV) technologies. The unique properties of perovskite materials—such as tunable bandgaps, high absorption coefficients, and compatibility with low-temperature solution processing—are driving their adoption in both novel and hybrid PV products.
A major trend is the development of tandem solar cells, where perovskite layers are combined with conventional silicon wafers to surpass the efficiency limits of single-junction silicon cells. In 2023, several manufacturers reported certified tandem cell efficiencies exceeding 29%, and in 2025, the industry is targeting commercial modules with efficiencies above 30%. Companies like Oxford PV are at the forefront, having scaled up pilot production of perovskite-on-silicon tandem modules and announced plans for mass production. Their German facility is expected to deliver the first commercial volumes in 2025, aiming to supply modules for both rooftop and utility-scale applications.
Beyond tandem integration, perovskite thin films are enabling new form factors and applications. Flexible and lightweight perovskite modules are being developed for building-integrated photovoltaics (BIPV), portable electronics, and vehicle-integrated PV. Saule Technologies is commercializing flexible perovskite panels, targeting architectural glass and IoT devices. Their roll-to-roll manufacturing process is designed for scalability and cost-effectiveness, with pilot installations underway in Europe and Asia.
Integration with existing PV infrastructure is also advancing. Perovskite modules are being designed to retrofit or complement legacy silicon installations, either as overlays or as part of hybrid systems. This approach leverages existing balance-of-system components and accelerates market adoption. Meyer Burger Technology AG, a leading European PV equipment manufacturer, is investing in perovskite-compatible production lines and collaborating with research institutes to optimize module durability and performance.
Looking ahead, the next few years will see increased collaboration between perovskite innovators and established PV manufacturers. Industry alliances and standardization efforts are underway to address challenges such as long-term stability, encapsulation, and large-area uniformity. The outlook for 2025 and beyond is optimistic: perovskite thin-film manufacturing is expected to diversify the PV market, enabling higher efficiencies, new applications, and accelerated integration with existing solar infrastructure.
Future Outlook: Challenges, Opportunities, and R&D Directions
The future of perovskite photovoltaic (PV) thin-film manufacturing in 2025 and the coming years is marked by both significant promise and notable challenges. As the industry transitions from laboratory-scale breakthroughs to commercial-scale production, several key factors will shape its trajectory.
One of the primary challenges remains the long-term stability and durability of perovskite solar cells. While laboratory devices have achieved power conversion efficiencies exceeding 25%, maintaining this performance under real-world conditions—exposure to moisture, heat, and UV light—remains a hurdle. Leading manufacturers such as Oxford PV are actively addressing these issues by developing tandem silicon-perovskite cells and implementing advanced encapsulation techniques. Their pilot production lines in Germany are expected to ramp up in 2025, aiming to demonstrate both high efficiency and improved operational lifetimes.
Scalability and manufacturing yield are also central concerns. The transition from spin-coating and other lab-scale deposition methods to scalable techniques such as slot-die coating, blade coating, and vapor deposition is underway. Companies like Saule Technologies are pioneering roll-to-roll manufacturing for flexible perovskite modules, targeting applications in building-integrated photovoltaics (BIPV) and portable electronics. Their production facility in Poland is among the first to commercialize large-area perovskite modules, with further expansion planned through 2025.
Supply chain and material sustainability are gaining attention as perovskite PV approaches commercialization. The use of lead in most high-efficiency perovskite formulations raises environmental and regulatory concerns. Research into lead-free alternatives and recycling strategies is intensifying, with organizations such as imec collaborating with industry partners to develop eco-friendly materials and closed-loop manufacturing processes.
On the opportunity side, perovskite PV offers unique advantages: lightweight, flexible form factors, and compatibility with tandem architectures that can surpass the efficiency limits of conventional silicon. The integration of perovskite layers onto existing silicon cell lines is a major R&D direction, with Meyer Burger Technology AG—a leading European PV equipment supplier—investing in pilot projects and partnerships to accelerate tandem cell commercialization.
Looking ahead, the next few years will likely see the first commercial installations of perovskite-silicon tandem modules, broader adoption in niche markets such as BIPV, and continued R&D to address stability and sustainability. Industry collaboration, standardization, and regulatory frameworks will be crucial to ensure safe, reliable, and scalable deployment of perovskite PV technologies.
Sources & References
- Oxford PV
- Saule Technologies
- Microquanta Semiconductor
- Meyer Burger Technology AG
- TCL China Star Optoelectronics Technology
- National Renewable Energy Laboratory
- Solar Energy Industries Association
- imec