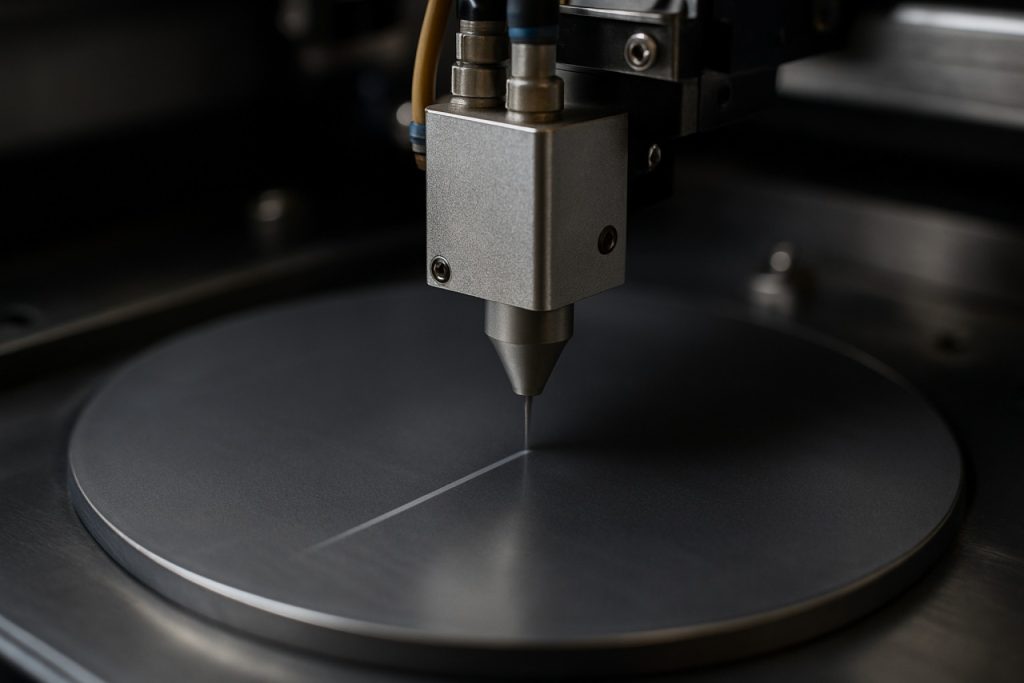
Nanoparticle Jet Printing Technologies in 2025: Transforming Advanced Manufacturing with Unmatched Precision and Speed. Explore Market Growth, Breakthroughs, and the Road Ahead.
- Executive Summary: Key Trends and 2025 Market Outlook
- Technology Overview: Principles of Nanoparticle Jet Printing
- Major Players and Industry Ecosystem (e.g., nanopjet.com, xjet3d.com, optomec.com)
- Current Applications: Electronics, Biomedicine, and Beyond
- Market Size and Growth Forecast (2025–2030): CAGR Analysis
- Recent Innovations and R&D Pipelines
- Competitive Landscape and Strategic Partnerships
- Regulatory Environment and Industry Standards (e.g., ieee.org, asme.org)
- Challenges: Technical, Economic, and Supply Chain Factors
- Future Outlook: Disruptive Potential and Emerging Opportunities
- Sources & References
Executive Summary: Key Trends and 2025 Market Outlook
Nanoparticle jet printing technologies are rapidly transforming the landscape of advanced manufacturing, offering unprecedented precision and scalability for the deposition of functional materials at the micro- and nanoscale. As of 2025, the sector is witnessing robust growth, driven by surging demand in electronics, flexible displays, biomedical devices, and energy applications. The technology’s ability to print conductive, dielectric, and semiconducting nanoparticle inks onto diverse substrates is enabling new product architectures and accelerating the shift toward additive manufacturing in high-value sectors.
Key industry players are expanding their portfolios and production capacities to meet this demand. Xerox, through its Palo Alto Research Center (PARC), continues to advance its direct-to-object printing platforms, focusing on high-resolution nanoparticle jetting for printed electronics and smart packaging. Optomec is scaling up its Aerosol Jet technology, which is widely adopted for printing fine-feature electronic circuits and sensors, particularly in aerospace and medical device manufacturing. Nano Dimension is leveraging its proprietary nanoparticle inkjet systems to enable rapid prototyping and low-volume production of multilayer printed circuit boards (PCBs) and other complex electronic components.
Recent years have seen significant investments in R&D and manufacturing infrastructure. Fujifilm is expanding its inkjet printhead and nanoparticle ink offerings, targeting applications in flexible displays and organic electronics. HP Inc. is also active in the field, developing scalable nanoparticle-based printing solutions for industrial and commercial markets. These companies are collaborating with material suppliers and end-users to optimize ink formulations and printing processes, ensuring compatibility with emerging substrates and device architectures.
The outlook for 2025 and the following years is marked by several key trends:
- Continued miniaturization and integration of printed components, enabling smarter and more compact devices.
- Expansion into new markets such as wearable electronics, IoT sensors, and point-of-care diagnostics, where nanoparticle jet printing offers unique advantages in customization and rapid iteration.
- Advancements in multi-material and multi-layer printing, supporting the fabrication of complex, multifunctional devices in a single process step.
- Growing emphasis on sustainability, with companies developing eco-friendly nanoparticle inks and energy-efficient printing platforms.
As the technology matures, industry leaders such as Xerox, Optomec, Nano Dimension, Fujifilm, and HP Inc. are expected to drive further innovation, standardization, and market adoption. The next few years will likely see nanoparticle jet printing technologies become integral to the digital manufacturing ecosystem, supporting the creation of next-generation electronic, biomedical, and energy devices.
Technology Overview: Principles of Nanoparticle Jet Printing
Nanoparticle jet printing technologies represent a rapidly advancing segment of additive manufacturing, enabling the precise deposition of functional materials at the micro- and nanoscale. The core principle involves the controlled ejection of nanoparticle-laden inks through fine nozzles, allowing for the direct patterning of conductive, dielectric, or semiconducting features onto a variety of substrates. This approach is particularly significant for applications in printed electronics, flexible displays, sensors, and biomedical devices.
The most prevalent methods in 2025 include inkjet, aerosol jet, and electrohydrodynamic (EHD) jet printing. Inkjet printing, pioneered by companies such as HP Inc. and Seiko Epson Corporation, utilizes piezoelectric or thermal actuation to eject droplets of nanoparticle ink. This method is valued for its scalability and compatibility with a wide range of materials, including silver, copper, and graphene-based inks. However, the minimum feature size is typically limited to around 20–50 microns due to droplet coalescence and substrate wetting effects.
Aerosol jet printing, commercialized by Optomec, employs a focused gas stream to deliver aerosolized nanoparticles onto the substrate, achieving finer features—down to 10 microns or less. This technique is gaining traction for its ability to print on non-planar and 3D surfaces, making it suitable for advanced packaging and conformal electronics. Optomec reports ongoing improvements in throughput and multi-material integration, with recent systems supporting simultaneous deposition of conductors and dielectrics.
Electrohydrodynamic jet (EHD) printing, advanced by firms such as Scrona, leverages high electric fields to draw ultra-fine jets from nanoparticle suspensions, enabling sub-micron resolution. In 2024–2025, Scrona demonstrated multi-nozzle EHD printheads capable of parallelized, high-throughput patterning, addressing previous limitations in scalability. This technology is being closely watched for its potential in micro-optics, photonics, and next-generation semiconductor packaging.
Material formulation remains a critical enabler, with companies like NovaCentrix and Sun Chemical supplying nanoparticle inks tailored for specific jetting technologies. These inks are engineered for stability, viscosity, and post-print sintering compatibility, supporting the transition from R&D to industrial-scale production.
Looking ahead, the next few years are expected to see further convergence of jet printing modalities, with hybrid systems combining the strengths of inkjet, aerosol, and EHD approaches. Integration with in-line metrology and AI-driven process control is anticipated to enhance yield and reliability. As the ecosystem matures, collaborations between equipment manufacturers, ink suppliers, and end-users are likely to accelerate the adoption of nanoparticle jet printing in high-value sectors such as medical diagnostics, IoT, and advanced displays.
Major Players and Industry Ecosystem (e.g., nanopjet.com, xjet3d.com, optomec.com)
The landscape of nanoparticle jet printing technologies in 2025 is shaped by a dynamic ecosystem of specialized manufacturers, technology developers, and materials suppliers. This sector is characterized by rapid innovation, with companies focusing on high-precision additive manufacturing for electronics, biomedical devices, and advanced materials. The major players are distinguished by their proprietary jetting technologies, materials expertise, and integration capabilities with industrial automation.
A prominent innovator in this space is Optomec, a U.S.-based company recognized for its Aerosol Jet printing systems. Optomec’s technology enables the direct printing of electronic circuits and functional materials onto 3D surfaces, supporting applications in semiconductor packaging, antenna fabrication, and medical device manufacturing. In 2024 and 2025, Optomec has expanded its partnerships with electronics manufacturers and automotive suppliers, leveraging its scalable systems for both prototyping and high-volume production. The company’s focus on digital manufacturing aligns with the broader industry trend toward flexible, on-demand electronics fabrication.
Another key player is XJet, headquartered in Israel, which specializes in NanoParticle Jetting™ (NPJ) technology. XJet’s systems are unique in their ability to print ultra-fine ceramic and metal parts with high resolution and complex geometries. The company’s Carmel line of 3D printers has gained traction in the dental, medical, and aerospace sectors, where precision and material purity are critical. In 2025, XJet continues to invest in expanding its material portfolio and enhancing throughput, responding to growing demand for advanced ceramics and metals in additive manufacturing.
Emerging companies such as Nanopjet are also contributing to the ecosystem by developing next-generation nanoparticle jetting platforms. Nanopjet focuses on scalable, high-speed deposition of functional inks for printed electronics, sensors, and display technologies. Their approach emphasizes compatibility with a wide range of substrates and integration with roll-to-roll manufacturing, positioning them as a potential disruptor in large-area electronics production.
The industry ecosystem is further supported by materials suppliers and equipment integrators who provide specialized nanoparticle inks, printheads, and process control systems. Collaborations between printer manufacturers and materials companies are intensifying, as end-users demand tailored solutions for specific applications. Industry bodies and consortia are also playing a role in standardizing processes and promoting interoperability across platforms.
Looking ahead, the outlook for nanoparticle jet printing technologies is robust. The convergence of digital manufacturing, miniaturization, and advanced materials is expected to drive adoption across sectors such as flexible electronics, medical implants, and micro-optics. Major players are investing in R&D to improve print resolution, speed, and material diversity, while new entrants are pushing the boundaries of scalability and cost-effectiveness. As the ecosystem matures, partnerships and open innovation will be key to unlocking the full potential of nanoparticle jet printing in the coming years.
Current Applications: Electronics, Biomedicine, and Beyond
Nanoparticle jet printing technologies have rapidly advanced in recent years, enabling precise deposition of functional materials at the micro- and nanoscale. As of 2025, these technologies are being increasingly adopted across a range of sectors, with notable momentum in electronics, biomedicine, and emerging interdisciplinary applications.
In the electronics industry, nanoparticle jet printing is revolutionizing the fabrication of flexible and printed electronics. The technology allows for the direct writing of conductive traces, antennas, and sensors onto flexible substrates, supporting the development of next-generation wearables, RFID tags, and IoT devices. Companies such as Xerox—through its Palo Alto Research Center (PARC)—have been instrumental in commercializing inkjet-based nanoparticle printing for printed electronics, offering solutions that enable high-resolution patterning of silver and copper inks. Similarly, HP Inc. has leveraged its expertise in inkjet technology to develop platforms capable of printing conductive nanoparticle inks for circuit prototyping and low-volume manufacturing.
In biomedicine, nanoparticle jet printing is facilitating the creation of biosensors, microarrays, and drug delivery systems with unprecedented precision. The ability to deposit biomolecules and nanoparticles in controlled patterns is critical for the fabrication of diagnostic devices and lab-on-a-chip platforms. Fujifilm has developed inkjet systems tailored for life sciences, enabling the printing of proteins, DNA, and living cells for research and clinical applications. Additionally, Nanoscribe is advancing multiphoton 3D printing technologies that utilize nanoparticle-laden resins for fabricating micro- and nanoscale biomedical devices.
Beyond electronics and biomedicine, nanoparticle jet printing is finding applications in energy, optics, and advanced manufacturing. For instance, the technology is being used to print perovskite and quantum dot layers for next-generation solar cells and displays. NovaCentrix is a key player in this space, providing photonic curing systems that complement nanoparticle printing by rapidly sintering printed metallic inks, thus enhancing conductivity and device performance.
Looking ahead, the outlook for nanoparticle jet printing technologies is robust. Ongoing improvements in printhead design, ink formulation, and process integration are expected to drive higher throughput, finer resolution, and broader material compatibility. As more industries seek additive, digital, and sustainable manufacturing solutions, nanoparticle jet printing is poised to play a pivotal role in the commercialization of advanced devices and systems over the next several years.
Market Size and Growth Forecast (2025–2030): CAGR Analysis
The global market for nanoparticle jet printing technologies is poised for robust growth between 2025 and 2030, driven by increasing demand for high-resolution, additive manufacturing solutions in electronics, biomedical devices, and advanced materials. Nanoparticle jet printing, which enables precise deposition of functional inks containing metallic, ceramic, or polymer nanoparticles, is gaining traction as industries seek scalable, cost-effective alternatives to traditional lithography and screen printing.
As of 2025, the market is characterized by a surge in adoption across sectors such as flexible electronics, printed sensors, and microelectromechanical systems (MEMS). Key players like Xerox—through its Palo Alto Research Center (PARC)—have pioneered scalable nanoparticle inkjet platforms, while Optomec has commercialized Aerosol Jet technology, enabling the direct printing of fine features down to 10 microns for applications in semiconductor packaging and antenna fabrication. Nano Dimension is another notable company, focusing on additive manufacturing systems for electronics, including multi-material and multi-layer printing with conductive nanoparticle inks.
Industry data from these manufacturers and their public statements indicate a compound annual growth rate (CAGR) for nanoparticle jet printing technologies in the range of 18% to 24% through 2030. This growth is underpinned by expanding use cases in Internet of Things (IoT) devices, wearable electronics, and medical diagnostics, where miniaturization and rapid prototyping are critical. For example, Optomec reports increasing demand from automotive and aerospace sectors for printed sensors and conformal electronics, while Nano Dimension highlights the acceleration of rapid prototyping and low-volume production in the electronics industry.
Geographically, North America and Asia-Pacific are expected to lead market expansion, with significant investments in R&D and manufacturing infrastructure. The presence of major electronics manufacturers and research institutions in these regions is fostering innovation and early adoption. European companies are also advancing, particularly in the development of nanoparticle inks and integration with roll-to-roll manufacturing processes.
Looking ahead, the market outlook for 2025–2030 is optimistic, with continued advancements in printhead technology, ink formulation, and process automation expected to further reduce costs and improve throughput. Strategic collaborations between equipment manufacturers, ink suppliers, and end-users are anticipated to accelerate commercialization and unlock new applications, solidifying nanoparticle jet printing as a cornerstone technology in next-generation additive manufacturing.
Recent Innovations and R&D Pipelines
Nanoparticle jet printing technologies have experienced significant advancements in recent years, with 2025 marking a period of accelerated innovation and commercialization. These technologies, which enable the precise deposition of functional nanoparticle inks onto a variety of substrates, are increasingly central to the fabrication of next-generation electronics, sensors, and biomedical devices.
A key trend in 2025 is the refinement of printhead architectures and ink formulations to achieve higher resolution and throughput. Companies such as Xerox and HP Inc. have continued to invest in nanoparticle inkjet platforms, leveraging their expertise in digital printing to push the boundaries of feature size and material compatibility. Xerox has reported progress in multi-material jetting, enabling the integration of conductive, dielectric, and semiconducting nanoparticles within a single print process, which is crucial for printed electronics and flexible circuits.
In parallel, Nano Dimension has expanded its R&D pipeline to include advanced nanoparticle jetting systems for additive manufacturing of high-performance electronic components. Their proprietary AgCite™ nanoparticle silver inks are being optimized for finer line widths and improved adhesion, targeting applications in radio frequency (RF) devices and high-density interconnects. The company’s DragonFly IV platform, launched in late 2023, is now being adapted for broader industrial use, with ongoing collaborations with aerospace and defense partners.
Another notable player, Optomec, has advanced its Aerosol Jet technology, which utilizes aerodynamic focusing to deposit nanoparticle inks with feature sizes down to 10 microns. In 2025, Optomec is piloting new systems capable of printing on complex 3D surfaces, addressing the growing demand for conformal electronics in automotive and medical device sectors. Their open materials platform is also fostering partnerships with ink suppliers to accelerate the development of novel nanoparticle formulations.
On the materials front, Sun Chemical and DuPont are actively developing nanoparticle-based inks with enhanced conductivity, environmental stability, and compatibility with flexible substrates. These efforts are supported by collaborations with equipment manufacturers to ensure seamless integration into high-speed jet printing systems.
Looking ahead, the outlook for nanoparticle jet printing technologies is robust. Industry analysts anticipate that ongoing R&D will yield further improvements in print resolution, process reliability, and multi-material integration. The convergence of advanced printhead design, smart ink chemistries, and AI-driven process control is expected to unlock new applications in wearables, IoT devices, and bioelectronics over the next few years. As leading companies continue to scale up their manufacturing capabilities and expand their patent portfolios, the sector is poised for sustained growth and broader adoption across multiple high-value industries.
Competitive Landscape and Strategic Partnerships
The competitive landscape for nanoparticle jet printing technologies in 2025 is characterized by rapid innovation, strategic collaborations, and a growing number of industry entrants. This sector, which enables high-resolution, additive manufacturing of functional materials at the nanoscale, is being shaped by both established players and agile startups, each leveraging unique technological approaches and market strategies.
Key industry leaders such as Xerox and HP Inc. continue to invest in advanced inkjet and nanoparticle deposition systems, building on their decades-long expertise in digital printing. Xerox has expanded its portfolio to include nanoparticle-based conductive inks and precision jetting platforms, targeting applications in flexible electronics and printed sensors. HP Inc. is similarly advancing its proprietary thermal inkjet technology to accommodate nanoparticle suspensions, with a focus on printed electronics and biomedical devices.
Emerging companies are also making significant strides. Nano Dimension, an Israeli-American firm, has established itself as a leader in additive manufacturing for electronics, offering direct jetting of nanoparticle inks for multilayer printed circuit boards (PCBs) and microelectronic devices. Their DragonFly system, for example, is being adopted by aerospace and defense sectors for rapid prototyping and low-volume production. Meanwhile, Optomec specializes in Aerosol Jet technology, which enables the printing of fine features using nanoparticle inks on 3D surfaces, serving industries from medical devices to automotive electronics.
Strategic partnerships are a defining feature of the sector’s evolution. In 2024 and 2025, collaborations between technology providers and material suppliers have intensified. For instance, Xerox has partnered with specialty chemical companies to co-develop nanoparticle ink formulations optimized for their printheads. Nano Dimension has entered into joint development agreements with leading electronics manufacturers to integrate their jet printing platforms into existing production lines, accelerating the adoption of additive manufacturing in high-reliability sectors.
Industry consortia and research alliances are also playing a pivotal role. Organizations such as the SEMI industry association are facilitating pre-competitive research and standardization efforts, aiming to address challenges related to ink stability, printhead reliability, and process scalability. These collaborations are expected to yield new standards and best practices by 2026, further lowering barriers to commercialization.
Looking ahead, the competitive landscape is likely to see increased consolidation as larger players acquire innovative startups to expand their technological capabilities. The next few years will also witness deeper integration of nanoparticle jet printing with digital manufacturing ecosystems, driven by ongoing partnerships and the maturation of supply chains. As a result, the sector is poised for robust growth, with strategic alliances and cross-industry collaborations serving as key enablers of market expansion and technological advancement.
Regulatory Environment and Industry Standards (e.g., ieee.org, asme.org)
The regulatory environment and industry standards for nanoparticle jet printing technologies are rapidly evolving as the sector matures and applications proliferate across electronics, biomedical devices, and advanced manufacturing. In 2025, the focus is on harmonizing safety, quality, and interoperability requirements to support commercialization and cross-border collaboration.
Key industry bodies such as the IEEE and the ASME are actively engaged in developing and updating standards relevant to nanoparticle jet printing. The IEEE, through its Nanotechnology Council, is working on standardizing terminology, measurement protocols, and performance benchmarks for printed nanomaterials and devices. These efforts aim to ensure consistency in reporting and facilitate the comparison of results across different platforms and manufacturers. The ASME, meanwhile, is addressing mechanical and safety standards for equipment and processes, with particular attention to the unique challenges posed by handling and jetting nanoparticles, such as containment, filtration, and operator safety.
In parallel, regulatory agencies in major markets are updating their frameworks to address the specific risks and opportunities associated with nanoparticle jet printing. The U.S. Food and Drug Administration (FDA) has issued guidance for manufacturers of medical devices incorporating printed nanomaterials, emphasizing biocompatibility, sterility, and traceability. The European Union, through its REACH regulation and the European Chemicals Agency, is focusing on the safe use of nanomaterials, requiring detailed documentation and risk assessments for nanoparticle inks and printed products.
Industry consortia and alliances are also playing a pivotal role. The SEMI association, representing the global electronics manufacturing supply chain, is facilitating the development of best practices for nanoparticle ink formulation, jetting reliability, and post-processing. These guidelines are increasingly referenced by manufacturers and suppliers to demonstrate compliance and build customer trust.
Looking ahead, the next few years are expected to see the introduction of more comprehensive standards covering the entire lifecycle of nanoparticle jet printing—from material synthesis and ink formulation to device integration and end-of-life management. There is also a growing emphasis on environmental, health, and safety (EHS) standards, particularly as production scales up and new applications emerge in sensitive sectors such as healthcare and aerospace. Collaboration between industry, academia, and regulators will be crucial to ensure that standards keep pace with technological advances and market needs.
Challenges: Technical, Economic, and Supply Chain Factors
Nanoparticle jet printing technologies, which enable the precise deposition of functional inks containing metallic, ceramic, or polymeric nanoparticles, are at the forefront of advanced manufacturing for electronics, sensors, and biomedical devices. However, as the sector matures in 2025, several technical, economic, and supply chain challenges persist, shaping the pace and direction of adoption.
Technical Challenges remain significant. Achieving consistent jetting of nanoparticle inks requires stringent control over ink rheology, particle size distribution, and surface chemistry. Nozzle clogging, a persistent issue, is exacerbated by agglomeration or sedimentation of nanoparticles, especially at higher concentrations needed for functional performance. Companies such as Xerox and HP Inc., both with established inkjet technology portfolios, have invested in proprietary ink formulations and printhead designs to mitigate these issues, but universal solutions remain elusive. Furthermore, the sintering or curing of printed nanoparticle patterns—essential for achieving desired electrical or mechanical properties—often requires high temperatures incompatible with flexible or temperature-sensitive substrates. This limits the range of printable materials and applications, despite ongoing research into low-temperature sintering techniques by firms like NovaCentrix.
Economic Factors also influence the sector’s trajectory. The cost of high-purity, monodisperse nanoparticles remains elevated due to complex synthesis and purification processes. While scale-up efforts by suppliers such as Chemours and Umicore are underway, price volatility and supply constraints persist, especially for precious metals like silver and platinum. Equipment costs for industrial-scale nanoparticle jet printers, offered by companies like Fujifilm and Seiko Instruments, remain high, limiting accessibility for small and medium-sized enterprises. Additionally, the lack of standardized testing and qualification protocols for printed electronics complicates the integration of these technologies into established manufacturing lines.
- Supply Chain Factors are increasingly critical in 2025. Geopolitical tensions and export controls on critical raw materials, such as rare earths and specialty metals, have led to disruptions and price spikes. Companies with vertically integrated supply chains, such as Umicore, are better positioned to weather these shocks, but most industry players remain vulnerable to upstream volatility.
- The sector also faces logistical challenges in transporting and storing nanoparticle inks, which are sensitive to temperature, light, and contamination. This necessitates robust quality assurance and cold-chain logistics, adding to operational costs.
Looking ahead, the outlook for nanoparticle jet printing technologies will depend on continued innovation in ink formulation, printhead engineering, and supply chain resilience. Industry collaboration and standardization efforts, led by organizations such as the SEMI industry association, are expected to play a pivotal role in overcoming these barriers and enabling broader commercialization in the coming years.
Future Outlook: Disruptive Potential and Emerging Opportunities
Nanoparticle jet printing technologies are poised to play a transformative role in advanced manufacturing sectors over the next several years, with 2025 marking a pivotal period for both commercialization and technological maturation. These additive manufacturing techniques, which enable the precise deposition of functional nanoparticles onto a variety of substrates, are increasingly being adopted for applications in electronics, energy devices, and biomedical engineering.
A key driver of this disruptive potential is the ability of nanoparticle jet printing to fabricate high-resolution, multi-material structures at room temperature, which is particularly advantageous for flexible electronics and next-generation sensors. Companies such as Xerox—through its Palo Alto Research Center (PARC)—have been at the forefront, developing scalable inkjet and aerosol jet systems capable of printing conductive, dielectric, and semiconducting nanoparticle inks. These systems are already being integrated into pilot production lines for printed circuit boards and flexible displays.
Another major player, Optomec, has commercialized Aerosol Jet technology, which is being adopted by leading electronics manufacturers for the direct printing of antennas, sensors, and interconnects on 3D surfaces. The company’s collaborations with global OEMs in automotive and aerospace sectors underscore the growing industrial confidence in nanoparticle jet printing for high-value, low-volume production runs.
In the energy sector, nanoparticle jet printing is enabling the fabrication of advanced battery electrodes and fuel cell components with tailored microstructures, improving both performance and manufacturability. Solaris Print and other emerging firms are leveraging these techniques to develop next-generation photovoltaic devices and printed energy storage solutions, aiming for commercial deployment within the next few years.
Looking ahead, the convergence of nanoparticle jet printing with artificial intelligence and real-time process monitoring is expected to further enhance print quality, yield, and scalability. Industry consortia and standards bodies, such as SEMI, are actively working to establish interoperability and quality benchmarks, which will be critical for broader adoption in regulated industries like medical devices and aerospace.
By 2025 and beyond, the disruptive potential of nanoparticle jet printing will be realized through its integration into digital manufacturing ecosystems, enabling rapid prototyping, mass customization, and on-demand production. As material portfolios expand and system costs decrease, the technology is set to unlock new opportunities in areas ranging from wearable electronics to smart packaging, positioning it as a cornerstone of the next industrial revolution.