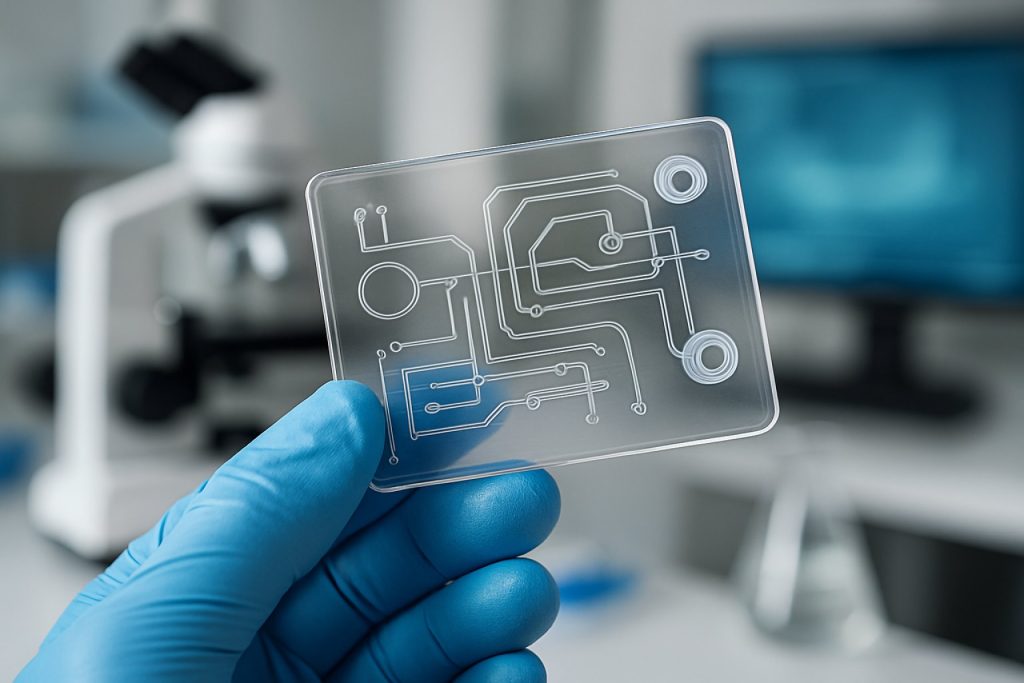
Microfluidic Platform Fabrication in 2025: Unleashing Next-Gen Manufacturing, Market Growth, and Disruptive Technologies. Explore How Advanced Fabrication is Shaping the Future of Diagnostics, Life Sciences, and Beyond.
- Executive Summary: Key Trends and Market Drivers in 2025
- Global Market Forecasts and Growth Projections (2025–2029)
- Emerging Fabrication Technologies: 3D Printing, Soft Lithography, and Beyond
- Material Innovations: Polymers, Glass, Silicon, and Hybrid Approaches
- Leading Players and Strategic Partnerships (e.g., dolomite-microfluidics.com, microfluidicsbio.com)
- Application Spotlight: Diagnostics, Drug Discovery, and Point-of-Care Devices
- Regulatory Landscape and Standardization Initiatives (e.g., microfluidics-association.org)
- Manufacturing Scale-Up: Automation, Cost Reduction, and Quality Control
- Regional Analysis: North America, Europe, Asia-Pacific, and Emerging Markets
- Future Outlook: Disruptive Trends, Investment Hotspots, and Technology Roadmap
- Sources & References
Executive Summary: Key Trends and Market Drivers in 2025
The microfluidic platform fabrication sector is poised for significant growth and transformation in 2025, driven by advances in materials science, automation, and the expanding application landscape in diagnostics, drug discovery, and personalized medicine. The convergence of these factors is accelerating the adoption of microfluidic technologies across both research and commercial domains.
A key trend in 2025 is the shift toward scalable, high-throughput manufacturing methods. Traditional soft lithography, while still prevalent, is increasingly complemented by injection molding, hot embossing, and advanced 3D printing techniques. These methods enable mass production of microfluidic devices with improved reproducibility and lower per-unit costs, addressing the needs of both research and clinical markets. Leading industry players such as Dolomite Microfluidics and Fluidigm Corporation are at the forefront, offering integrated solutions that span from prototyping to large-scale manufacturing.
Material innovation is another major driver. The adoption of thermoplastics, such as cyclic olefin copolymer (COC) and polymethyl methacrylate (PMMA), is rising due to their biocompatibility, optical clarity, and suitability for mass production. Companies like ZEONEX (a brand of Zeon Corporation) are supplying advanced polymers tailored for microfluidic applications, supporting the trend toward disposable, single-use devices in clinical diagnostics and point-of-care testing.
Automation and digitalization are reshaping fabrication workflows. The integration of robotics, machine vision, and AI-driven quality control is reducing human error and increasing throughput. This is particularly evident in the offerings of AIM Biotech and Micronit Microtechnologies, which provide automated microfluidic device production and assembly services for both custom and standardized platforms.
Sustainability is emerging as a critical consideration, with manufacturers exploring recyclable materials and greener fabrication processes. The push for environmentally friendly solutions is expected to intensify over the next few years, as regulatory pressures and customer preferences evolve.
Looking ahead, the microfluidic platform fabrication market is set to benefit from continued investment in R&D, strategic partnerships, and the expansion of application areas such as organ-on-chip, cell therapy manufacturing, and environmental monitoring. The sector’s outlook remains robust, with established players and innovative startups alike driving technological progress and market adoption.
Global Market Forecasts and Growth Projections (2025–2029)
The global market for microfluidic platform fabrication is poised for robust growth between 2025 and 2029, driven by expanding applications in diagnostics, drug discovery, and point-of-care testing. The increasing demand for rapid, cost-effective, and miniaturized analytical devices is catalyzing investments in advanced fabrication technologies, including soft lithography, injection molding, and 3D printing. Key industry players are scaling up production capacities and innovating materials to meet the evolving requirements of healthcare, biotechnology, and industrial sectors.
In 2025, the market is expected to witness significant expansion, particularly in North America, Europe, and Asia-Pacific, where government initiatives and private investments are accelerating the adoption of microfluidic solutions. The United States remains a leader, with companies such as Dolomite Microfluidics and Fluidigm Corporation (now Standard BioTools) advancing both prototyping and mass-manufacturing capabilities. These firms are focusing on scalable fabrication methods and integration of novel polymers and glass substrates to enhance device performance and reproducibility.
In Europe, Microfluidic ChipShop is expanding its manufacturing footprint, leveraging injection molding and hot embossing to deliver high-volume, cost-efficient microfluidic chips for diagnostics and life sciences. The company’s collaborations with academic and industrial partners are expected to drive further innovation in device design and fabrication processes through 2029.
Asia-Pacific is emerging as a dynamic growth region, with countries like China, Japan, and South Korea investing heavily in microfluidics R&D and manufacturing infrastructure. Companies such as Micralyne (now part of Teledyne MEMS) are strengthening their presence in the region, offering MEMS-based microfluidic fabrication services that cater to both local and global markets. The proliferation of contract manufacturing organizations (CMOs) specializing in microfluidics is anticipated to lower entry barriers for startups and accelerate commercialization timelines.
Looking ahead, the market outlook for 2025–2029 is characterized by increasing standardization, automation, and digitalization of fabrication workflows. The integration of artificial intelligence and machine learning for process optimization is expected to further enhance yield and quality. As regulatory frameworks evolve to support rapid device approval, the microfluidic platform fabrication sector is set to play a pivotal role in the next generation of healthcare and industrial solutions.
Emerging Fabrication Technologies: 3D Printing, Soft Lithography, and Beyond
The landscape of microfluidic platform fabrication is undergoing rapid transformation in 2025, driven by the convergence of advanced manufacturing techniques and the growing demand for scalable, customizable, and cost-effective solutions. Among the most significant developments are the adoption of 3D printing (additive manufacturing), innovations in soft lithography, and the emergence of hybrid and novel fabrication methods that promise to redefine the capabilities and accessibility of microfluidic devices.
3D printing has moved from a prototyping tool to a viable method for producing functional microfluidic devices with complex geometries and integrated features. Leading manufacturers such as Formlabs and Stratasys have expanded their portfolios to include high-resolution printers and biocompatible resins specifically tailored for microfluidic applications. These advances enable rapid iteration and on-demand production, reducing the time from design to deployment. In 2025, the introduction of new photopolymer materials and multi-material printing capabilities is allowing for the integration of valves, sensors, and even flexible membranes directly into microfluidic chips, a leap forward for lab-on-a-chip and organ-on-chip technologies.
Soft lithography, traditionally the backbone of microfluidic fabrication, continues to evolve. Companies like ibidi GmbH and Microfluidic ChipShop are refining polydimethylsiloxane (PDMS) molding processes to improve reproducibility, scalability, and compatibility with automation. Recent years have seen the development of alternative elastomers and hybrid materials that address PDMS’s limitations, such as absorption of small molecules and limited chemical resistance. These innovations are making soft lithography more suitable for industrial-scale production and for applications in pharmaceuticals and diagnostics where material performance is critical.
Beyond these established methods, 2025 is witnessing the rise of hybrid fabrication approaches that combine the strengths of multiple techniques. For example, companies are integrating laser micromachining, injection molding, and hot embossing with 3D printing and soft lithography to achieve higher throughput and finer feature resolution. Dolomite Microfluidics is notable for offering modular systems that support a range of fabrication methods, enabling rapid prototyping and scale-up within the same platform.
Looking ahead, the outlook for microfluidic platform fabrication is marked by increasing automation, digital design integration, and the democratization of device manufacturing. As open-source hardware and cloud-based design tools proliferate, the barriers to entry for custom microfluidic device development are expected to fall, fostering innovation across biomedical research, diagnostics, and industrial applications.
Material Innovations: Polymers, Glass, Silicon, and Hybrid Approaches
The landscape of microfluidic platform fabrication is undergoing rapid transformation in 2025, driven by material innovations that address scalability, biocompatibility, and integration challenges. Traditionally, microfluidic devices were fabricated using silicon and glass due to their excellent chemical resistance and optical properties. However, the high cost and complex processing requirements of these materials have spurred the adoption of polymers and hybrid approaches, especially as the field moves toward mass production and point-of-care applications.
Polydimethylsiloxane (PDMS) remains a staple in academic research for its ease of prototyping and optical clarity. Yet, its limitations—such as absorption of small molecules and incompatibility with certain solvents—have led to increased interest in thermoplastics like cyclic olefin copolymer (COC), polymethyl methacrylate (PMMA), and polycarbonate. These materials are now being widely adopted by commercial manufacturers for their suitability in injection molding and hot embossing, enabling high-throughput, cost-effective production. Companies such as Dolomite Microfluidics and Microfluidic ChipShop are at the forefront, offering a range of polymer-based microfluidic chips tailored for diagnostics, drug discovery, and cell analysis.
Glass continues to play a critical role in applications requiring superior chemical resistance and minimal autofluorescence, such as high-sensitivity analytical assays. Advances in laser micromachining and bonding techniques have improved the manufacturability of glass microfluidic devices, with companies like SCHOTT AG leveraging their expertise in specialty glass to supply custom solutions for both research and industrial clients.
Silicon, the original material for microfluidics, is experiencing a resurgence in niche applications, particularly where integration with electronic components is essential. The compatibility of silicon with established semiconductor processes allows for the development of highly integrated lab-on-chip systems, a trend supported by organizations such as IMTEK – University of Freiburg, which collaborates with industry to push the boundaries of silicon-based microfluidics.
Hybrid approaches are gaining momentum, combining the strengths of multiple materials to overcome individual limitations. For example, glass-polymer and silicon-polymer hybrids enable the integration of optical detection with flexible fluidic architectures. Companies like ZEON Corporation are developing advanced cyclo olefin polymers and copolymers that can be bonded to glass or silicon, expanding the design space for next-generation devices.
Looking ahead, the next few years are expected to see further convergence of material science and microfabrication, with a focus on sustainable materials, improved surface functionalization, and seamless integration with electronics and sensors. The ongoing collaboration between material suppliers, device manufacturers, and end-users will be pivotal in shaping the future of microfluidic platform fabrication.
Leading Players and Strategic Partnerships (e.g., dolomite-microfluidics.com, microfluidicsbio.com)
The microfluidic platform fabrication sector in 2025 is characterized by a dynamic landscape of established leaders, innovative startups, and a growing web of strategic partnerships. These collaborations are accelerating the commercialization of advanced microfluidic devices for applications in diagnostics, drug discovery, and industrial processing.
Among the most prominent players is Dolomite Microfluidics, a subsidiary of the Blacktrace group. Dolomite is recognized for its modular microfluidic systems and custom chip fabrication services, supporting both research and industrial-scale production. The company has expanded its global reach through partnerships with academic institutions and biotechnology firms, focusing on rapid prototyping and scalable manufacturing of polymer and glass microfluidic chips.
Another key player is Microfluidics International Corporation, a part of the IDEX Corporation. Microfluidics International specializes in high-shear fluid processors and microfluidic platform solutions, with a strong emphasis on pharmaceutical and bioprocessing applications. Their collaborations with pharmaceutical manufacturers have led to the development of robust, GMP-compliant microfluidic systems for nanoparticle synthesis and drug formulation.
In the Asia-Pacific region, Fluidigm Corporation (now Standard BioTools) continues to be a significant force, particularly in single-cell analysis and genomics. The company’s partnerships with leading research hospitals and diagnostic companies are driving the integration of microfluidic platforms into clinical workflows, with a focus on personalized medicine and high-throughput screening.
Emerging companies such as Elveflow are gaining traction by offering high-precision flow control instruments and customizable microfluidic chips. Elveflow’s collaborations with academic research centers and industrial partners are enabling the development of next-generation organ-on-chip and lab-on-chip devices, with a focus on rapid prototyping and flexible manufacturing.
Strategic partnerships are also shaping the sector’s future. For example, alliances between microfluidic chip manufacturers and materials suppliers are fostering the adoption of novel polymers and hybrid materials, improving device performance and scalability. Collaborations with automation and robotics companies are streamlining the integration of microfluidic platforms into automated laboratory environments, enhancing throughput and reproducibility.
Looking ahead, the next few years are expected to see further consolidation among leading players, increased cross-sector partnerships, and the emergence of new entrants leveraging advances in 3D printing and digital microfabrication. These trends are poised to accelerate the deployment of microfluidic technologies across healthcare, environmental monitoring, and industrial bioprocessing.
Application Spotlight: Diagnostics, Drug Discovery, and Point-of-Care Devices
Microfluidic platform fabrication is at the heart of recent advances in diagnostics, drug discovery, and point-of-care (POC) devices, with 2025 marking a period of rapid technological maturation and commercialization. The field is witnessing a shift from traditional soft lithography and PDMS-based methods toward scalable, industrial-grade manufacturing techniques such as injection molding, hot embossing, and 3D printing. These methods are enabling the production of robust, reproducible, and cost-effective microfluidic devices suitable for high-throughput applications and regulatory compliance.
Key industry players are driving this evolution. Dolomite Microfluidics, a subsidiary of Blacktrace Holdings, continues to expand its portfolio of modular microfluidic systems and custom chip fabrication services, supporting both research and commercial-scale production. Their expertise in glass, polymer, and hybrid chip manufacturing is particularly relevant for diagnostics and drug screening applications, where material compatibility and optical clarity are critical.
Meanwhile, Standard BioTools (formerly Fluidigm) leverages its proprietary integrated fluidic circuit (IFC) technology to deliver high-throughput genomics and proteomics platforms. Their microfluidic chips, manufactured using advanced photolithography and precision molding, are widely adopted in clinical diagnostics and pharmaceutical research, enabling multiplexed assays and single-cell analysis.
The adoption of thermoplastics such as cyclic olefin copolymer (COC) and polymethyl methacrylate (PMMA) is accelerating, driven by their biocompatibility, low autofluorescence, and suitability for mass production. Companies like Microfluidic ChipShop are at the forefront, offering standardized and custom microfluidic devices fabricated via injection molding, which is essential for scaling up POC diagnostic devices and ensuring batch-to-batch consistency.
3D printing is also gaining traction for rapid prototyping and low-volume production, with firms such as Protolabs providing on-demand manufacturing of complex microfluidic geometries in a range of materials. This flexibility is particularly valuable for early-stage drug discovery and personalized medicine, where device customization and fast iteration cycles are required.
Looking ahead, the next few years are expected to see further integration of microfluidic fabrication with automation, quality control, and digital design tools. This will streamline the transition from prototype to product, reduce time-to-market, and support the growing demand for decentralized diagnostics and personalized therapeutics. As regulatory requirements tighten, especially for clinical and POC applications, manufacturers are investing in cleanroom facilities and ISO-certified processes to ensure device reliability and safety.
Overall, the convergence of advanced fabrication technologies, material innovation, and industry collaboration is poised to accelerate the deployment of microfluidic platforms across diagnostics, drug discovery, and POC devices, shaping the landscape of healthcare and life sciences through 2025 and beyond.
Regulatory Landscape and Standardization Initiatives (e.g., microfluidics-association.org)
The regulatory landscape and standardization initiatives for microfluidic platform fabrication are rapidly evolving as the technology matures and its applications expand across diagnostics, drug development, and industrial processes. In 2025, the sector is witnessing increased collaboration between industry stakeholders, regulatory agencies, and standardization bodies to address the unique challenges posed by microfluidic devices, which often combine materials science, fluid dynamics, and integrated electronics.
A key development is the ongoing work by the Microfluidics Association, a global industry consortium dedicated to advancing the commercialization and standardization of microfluidic technologies. The association is actively engaging with manufacturers, end-users, and regulators to develop consensus-based standards for device fabrication, quality control, and interoperability. Their initiatives include working groups focused on defining terminology, establishing test protocols, and harmonizing material specifications, which are critical for ensuring reproducibility and safety in both research and commercial settings.
On the regulatory front, agencies such as the U.S. Food and Drug Administration (FDA) and the European Medicines Agency (EMA) are increasingly recognizing the distinct regulatory needs of microfluidic-based products, particularly in the context of in vitro diagnostics and point-of-care devices. In 2024 and 2025, the FDA has expanded its engagement with microfluidics manufacturers through its Emerging Technology Program, providing a pathway for early dialogue and feedback on novel fabrication methods and device designs. This proactive approach is expected to continue, with further guidance documents anticipated in the next few years to clarify requirements for device validation, biocompatibility, and manufacturing controls.
Industry leaders such as Dolomite Microfluidics and Fluidigm Corporation are actively participating in these standardization efforts, leveraging their expertise in microfluidic chip design and mass production. These companies are also investing in scalable, automated fabrication processes that align with emerging standards, aiming to streamline regulatory approval and facilitate broader adoption in clinical and industrial markets.
Looking ahead, the next few years are expected to bring greater harmonization of standards at the international level, with organizations such as the International Organization for Standardization (ISO) and the International Electrotechnical Commission (IEC) likely to formalize guidelines specific to microfluidic platform fabrication. This will not only reduce barriers to global market entry but also foster innovation by providing clear frameworks for quality and safety. As the regulatory landscape matures, stakeholders anticipate a more predictable pathway for product development and commercialization, accelerating the integration of microfluidic technologies into mainstream applications.
Manufacturing Scale-Up: Automation, Cost Reduction, and Quality Control
The microfluidic platform fabrication sector is undergoing significant transformation in 2025, driven by the need for scalable manufacturing, cost efficiency, and stringent quality control. As microfluidic devices transition from research prototypes to commercial products in diagnostics, drug discovery, and environmental monitoring, manufacturers are investing heavily in automation and advanced process control.
Automation is at the forefront of manufacturing scale-up. Leading companies such as Dolomite Microfluidics and Fluidigm Corporation have integrated robotic handling, automated alignment, and in-line inspection systems into their production lines. These systems enable high-throughput fabrication of microfluidic chips with consistent quality, reducing human error and labor costs. For example, Dolomite Microfluidics offers modular automated platforms that can be rapidly reconfigured for different device designs, supporting both prototyping and mass production.
Material selection and process innovation are also contributing to cost reduction. The adoption of thermoplastics, such as cyclic olefin copolymer (COC) and polymethyl methacrylate (PMMA), is replacing traditional glass and silicon substrates in many applications. These polymers are compatible with injection molding and hot embossing, allowing for rapid, low-cost replication of microfluidic structures. Companies like Microfluidic ChipShop have established large-scale injection molding facilities, enabling the production of millions of chips annually at a fraction of the cost of conventional methods.
Quality control remains a critical focus as production volumes increase. Advanced metrology tools, such as optical profilometry and automated leak testing, are now standard in leading manufacturing facilities. Fluidigm Corporation and Dolomite Microfluidics employ real-time monitoring and data analytics to ensure dimensional accuracy and functional reliability of each device. Traceability systems, including unique device identifiers and digital batch records, are being implemented to meet regulatory requirements and facilitate root-cause analysis in case of defects.
Looking ahead, the next few years are expected to see further integration of artificial intelligence and machine learning for predictive maintenance and process optimization. Industry leaders are also exploring sustainable manufacturing practices, such as recyclable materials and energy-efficient processes, to address environmental concerns. As demand for point-of-care diagnostics and lab-on-a-chip solutions continues to rise, the microfluidic platform fabrication industry is poised for robust growth, with automation, cost reduction, and quality assurance as its cornerstones.
Regional Analysis: North America, Europe, Asia-Pacific, and Emerging Markets
The global landscape for microfluidic platform fabrication in 2025 is marked by dynamic regional developments, with North America, Europe, Asia-Pacific, and emerging markets each contributing distinct strengths and trajectories to the sector.
North America remains a leader in microfluidic innovation, driven by robust R&D ecosystems, established semiconductor and life sciences industries, and strong government support. The United States, in particular, is home to pioneering companies such as Dolomite Microfluidics and Fluidigm Corporation, both of which are advancing fabrication techniques including soft lithography, injection molding, and 3D printing. The region’s focus on high-throughput, scalable manufacturing is further supported by collaborations between academic institutions and industry, as well as the presence of major contract manufacturers. In 2025, North American firms are increasingly integrating automation and digital design tools to accelerate prototyping and reduce time-to-market for microfluidic devices.
Europe is characterized by a strong emphasis on precision engineering and regulatory compliance, with countries like Germany, the Netherlands, and Switzerland at the forefront. Companies such as Micronit and Carl Zeiss AG are notable for their expertise in glass and polymer microfabrication, leveraging advanced photolithography and etching processes. The European Union’s investment in microfluidics for healthcare and environmental monitoring is fostering cross-border collaborations and standardization efforts. In 2025, European manufacturers are expected to expand their capabilities in sustainable materials and green fabrication processes, aligning with the region’s broader environmental goals.
Asia-Pacific is experiencing rapid growth, fueled by expanding electronics manufacturing infrastructure and increasing demand for point-of-care diagnostics. Countries such as China, Japan, and South Korea are investing heavily in microfluidic R&D and production capacity. Leading players like Samsung Electronics and Toshiba Corporation are leveraging their microfabrication expertise to develop cost-effective, high-volume production methods, including roll-to-roll processing and nanoimprint lithography. In 2025 and beyond, Asia-Pacific is poised to become a major hub for both contract manufacturing and original device development, with a focus on affordability and scalability.
Emerging markets in Latin America, the Middle East, and Africa are beginning to establish a presence in microfluidic platform fabrication, primarily through technology transfer and partnerships with established global players. While local manufacturing remains limited, initiatives to build regional expertise and infrastructure are underway, particularly in countries with growing biotech sectors. Over the next few years, these regions are expected to benefit from lower-cost fabrication technologies and increased access to global supply chains, gradually expanding their role in the microfluidics value chain.
Future Outlook: Disruptive Trends, Investment Hotspots, and Technology Roadmap
The landscape of microfluidic platform fabrication is poised for significant transformation in 2025 and the coming years, driven by disruptive trends, strategic investments, and rapid technological advancements. The sector is witnessing a convergence of materials science, advanced manufacturing, and digital integration, which is reshaping both the scale and scope of microfluidic device production.
A key disruptive trend is the shift toward scalable, high-throughput manufacturing methods. Traditional soft lithography, while foundational, is increasingly complemented or replaced by injection molding, hot embossing, and, most notably, additive manufacturing (3D printing). Companies such as Dolomite Microfluidics and Fluidigm Corporation are at the forefront, offering modular microfluidic systems and pioneering new fabrication workflows that enable rapid prototyping and mass production. The adoption of 3D printing, particularly with biocompatible and optically transparent resins, is expected to accelerate, allowing for complex geometries and integrated functionalities that were previously unattainable.
Material innovation is another focal point. The industry is moving beyond polydimethylsiloxane (PDMS) toward thermoplastics such as cyclic olefin copolymer (COC) and cyclic olefin polymer (COP), which offer superior chemical resistance, optical clarity, and compatibility with automated manufacturing. Microfluidic ChipShop and ZEON Corporation are notable for their expertise in thermoplastic microfluidic devices, with ZEON being a major supplier of COP materials. This transition is expected to lower costs and facilitate the integration of microfluidics into point-of-care diagnostics and high-volume life science applications.
Investment hotspots are emerging around integrated microfluidic platforms for diagnostics, drug discovery, and cell analysis. The COVID-19 pandemic catalyzed interest in rapid, decentralized testing, and this momentum continues to drive funding into companies developing scalable fabrication solutions. Strategic partnerships between device manufacturers and material suppliers are also intensifying, as seen in collaborations involving Abbott Laboratories and Thermo Fisher Scientific, both of which are expanding their microfluidic-enabled product lines.
Looking ahead, the technology roadmap points toward increased automation, digital design-to-device workflows, and the integration of sensors and electronics directly into microfluidic chips. The next few years will likely see the emergence of fully automated, cloud-connected microfluidic fabrication platforms, enabling rapid iteration and customization. As regulatory standards evolve and manufacturing costs decline, microfluidic platform fabrication is set to become a cornerstone technology in diagnostics, personalized medicine, and beyond.
Sources & References
- Dolomite Microfluidics
- ZEONEX
- AIM Biotech
- Micronit Microtechnologies
- Microfluidic ChipShop
- Formlabs
- Stratasys
- Microfluidic ChipShop
- Dolomite Microfluidics
- SCHOTT AG
- IMTEK – University of Freiburg
- ZEON Corporation
- Elveflow
- Protolabs
- Microfluidics Association
- Carl Zeiss AG
- Toshiba Corporation
- Thermo Fisher Scientific