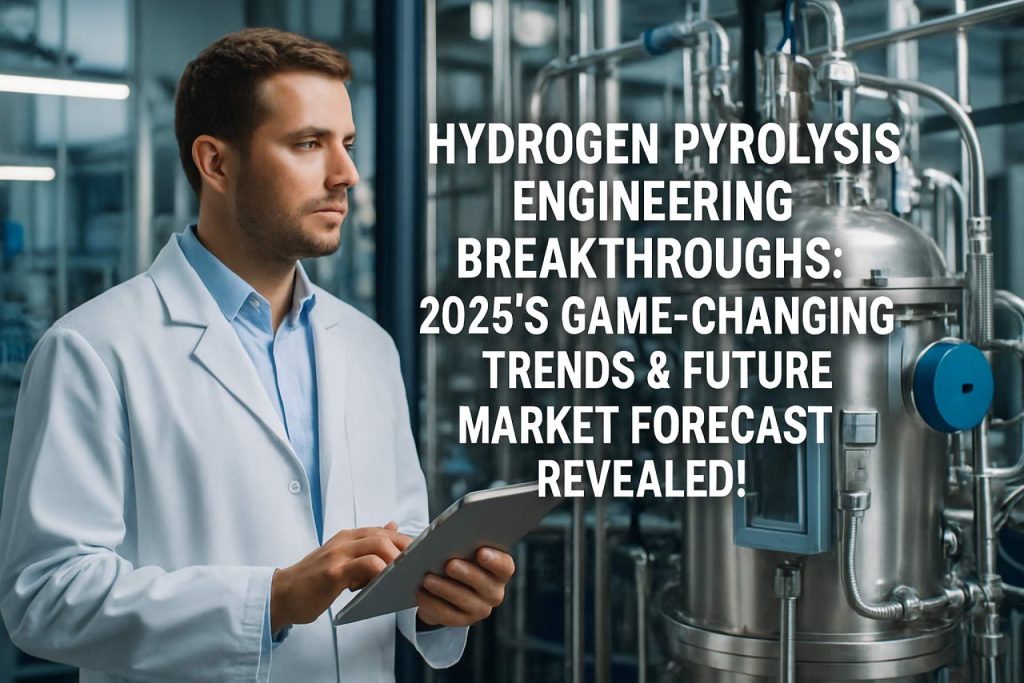
Table of Contents
- Executive Summary: Key Findings & 2025 Outlook
- Market Size & Growth Forecast: 2025–2030
- Core Technologies in Hydrogen Pyrolysis Systems
- Competitive Landscape: Leading Innovators & Manufacturers
- Major Projects & Pilot Installations (2024–2025)
- Cost Analysis: CAPEX, OPEX & LCOH Comparisons
- Policy Drivers, Incentives & Regulatory Shifts
- Supply Chain & Feedstock Dynamics
- Investment Trends & Funding Landscape
- Future Outlook: Disruptive Innovations & Roadmap to 2030
- Sources & References
Executive Summary: Key Findings & 2025 Outlook
Hydrogen pyrolysis, a process that splits methane into hydrogen and solid carbon without direct CO2 emissions, is gaining traction as an innovative pathway for low-carbon hydrogen production. In 2025, the sector is transitioning from pilot to early commercial deployment, with multiple technology providers advancing scalable systems tailored for industrial decarbonization.
- Commercial Demonstrations: Companies such as BASF and Tydac Technologies are operating demonstration units in Europe, with BASF’s methane pyrolysis unit in Ludwigshafen targeting hydrogen output with a carbon intensity significantly lower than traditional steam methane reforming. BASF’s facility, supported by German federal funding, is expected to inform scale-up strategies through 2025 and beyond.
- Technology Innovation: Monolith in the United States is scaling its proprietary plasma-based pyrolysis reactors, aiming for commercial hydrogen production alongside carbon black as a valuable co-product. Their Olive Creek facility is scheduled to reach full operational capacity in 2025, projecting annual hydrogen outputs exceeding 14,000 tonnes while reducing lifecycle emissions.
- Strategic Partnerships: Wood has entered partnerships to integrate its hydrogen pyrolysis (hydrogen from natural gas without CO2 emissions) technology into existing energy infrastructure, paving the way for distributed hydrogen hubs. These collaborations are expected to accelerate technology transfer and deployment over the next three years.
- Market Drivers & Challenges: Momentum is bolstered by public funding, regulatory support for low-carbon hydrogen, and the dual value streams of hydrogen and solid carbon (e.g., carbon black and graphite). However, challenges remain in scaling reactor engineering, cost reduction, and integration with existing gas grids. The cost-competitiveness of pyrolytic hydrogen remains sensitive to methane feedstock prices and demand for carbon co-products.
- 2025–2027 Outlook: The sector is poised for rapid growth as pilot plants validate performance and commercial offtake agreements emerge. Industry players are targeting lower levelized costs of hydrogen and improved reactor lifespans. Continued public and private investment is anticipated, with the goal of enabling multi-megawatt facilities and supporting the broader hydrogen economy transition.
In summary, hydrogen pyrolysis systems engineering is at a pivotal stage in 2025, balancing technical advances with market integration. The next few years will be critical for establishing performance benchmarks, cost trajectories, and commercial viability in the low-carbon hydrogen landscape.
Market Size & Growth Forecast: 2025–2030
The global market for hydrogen pyrolysis systems engineering is poised for significant growth between 2025 and 2030, driven by increasing demand for low-carbon hydrogen and advances in methane pyrolysis technology. As industries seek alternatives to steam methane reforming (SMR) and electrolysis for hydrogen production, pyrolysis—which generates solid carbon instead of CO2 emissions—has emerged as a compelling solution for decarbonizing hydrogen-intensive sectors.
In 2025, commercial-scale hydrogen pyrolysis projects are transitioning from demonstration to deployment, with Europe and North America leading market activity. Companies such as BASF and thyssenkrupp are actively developing and piloting methane pyrolysis reactors, leveraging their expertise in chemical engineering and industrial plant construction. For instance, BASF has initiated demonstration plants with projected capacities reaching up to several thousand tonnes of hydrogen per year by 2026, aiming to scale up as demand grows.
The market size for hydrogen pyrolysis systems in 2025 is estimated to be in the low hundreds of millions (USD), primarily driven by pilot facilities and early commercial deployments. Growth is expected to accelerate rapidly post-2025, with a strong pipeline of projects targeting industrial decarbonization in sectors such as steel, chemicals, and transportation. Hydrogenious LOHC Technologies and Hyzon Motors are among those integrating pyrolysis hydrogen into their supply chain and mobility solutions, signaling expanding end-use applications.
- Technology outlook: Continued refinement of reactor designs, including fluidized bed and plasma-based systems, is anticipated to boost system efficiency and lower capital costs. Monolith, for example, has reported progress towards commercial-scale plasma pyrolysis, targeting both hydrogen and carbon black co-production by the late 2020s.
- Regional trends: The European Union’s “Hydrogen Strategy” and the U.S. Department of Energy’s “Hydrogen Shot” initiatives are accelerating project funding and regulatory support for low-emission hydrogen, fostering a favorable environment for pyrolysis system engineering firms (European Commission).
- Growth forecast: By 2030, the market for hydrogen pyrolysis systems is projected to surpass USD 2 billion, with annual capacity additions expected to reach several hundred thousand tonnes of hydrogen globally, as industrial-scale deployments mature and end-user adoption broadens.
Overall, the next five years will be pivotal for the hydrogen pyrolysis sector, with engineering innovation, strategic partnerships, and supportive policy frameworks driving market expansion and technology adoption.
Core Technologies in Hydrogen Pyrolysis Systems
Hydrogen pyrolysis, also known as methane pyrolysis or turquoise hydrogen production, represents a promising pathway for low-carbon hydrogen generation. At its core, hydrogen pyrolysis systems engineering centers on splitting methane into hydrogen and solid carbon without direct CO2 emissions. This is typically achieved through high-temperature reactors employing thermal, catalytic, or plasma processes. As of 2025, technological advancements and pilot deployments are rapidly shaping the sector’s engineering landscape.
The dominant reactor designs include fluidized-bed reactors, molten metal reactors, and plasma-based systems. BASF has been developing a molten metal pyrolysis process, utilizing a liquid metal catalyst to decompose methane at temperatures above 800°C. Their pilot plant in Ludwigshafen is demonstrating continuous operation since 2023, with ongoing system optimizations targeting scalable hydrogen outputs and cost-effective carbon recovery.
Another key player, Monolith, operates commercial-scale plasma pyrolysis reactors in Nebraska. Their technology leverages high-temperature plasma arcs (above 1,500°C) to split methane, yielding hydrogen and carbon black. By 2025, Monolith’s facilities have ramped up production, emphasizing modular system design for ease of scaling and integration with existing natural gas infrastructure. The company’s engineering advances focus on reactor longevity, energy efficiency, and maximizing the economic value of both hydrogen and carbon products.
Catalytic pyrolysis is under active development by firms such as hte GmbH, which is piloting fixed-bed catalytic reactors with novel catalyst formulations. In these systems, process engineering challenges include catalyst stability, carbon removal, and maintaining high methane conversion rates. Efforts are underway to automate carbon extraction and regeneration cycles to ensure continuous operation and minimize downtime.
Systems integration remains a critical focus area. Hydrogen pyrolysis plants in 2025 are increasingly engineered for modularity, digital monitoring, and compatibility with renewable energy sources. Companies are embedding advanced process controls and predictive maintenance using digital twins and AI-based monitoring, as seen in the engineering roadmaps of Baker Hughes and other technology partners.
Looking ahead, the next few years are expected to bring further scale-up of pyrolysis installations, improvements in energy efficiency (targeting electrical consumption below 7 kWh/kg H2), and enhanced carbon valorization strategies. With several demonstration and early commercial plants operating or in construction, the sector is poised for accelerated deployment, contingent upon continued advancements in reactor engineering, process integration, and market development for solid carbon co-products.
Competitive Landscape: Leading Innovators & Manufacturers
The competitive landscape for hydrogen pyrolysis systems engineering in 2025 is characterized by a dynamic mix of established industrial giants, specialized technology startups, and collaborative public-private partnerships. The sector’s momentum is driven by global decarbonization targets and the growing demand for low-emission hydrogen, especially as hydrogen produced via methane pyrolysis can yield a solid carbon co-product and dramatically reduce CO2 emissions compared to conventional steam methane reforming.
One of the most prominent players is BASF SE, which has advanced its methane pyrolysis demonstration plant in Ludwigshafen, Germany. BASF’s process uses a molten metal reactor to split methane into hydrogen and solid carbon, with the company targeting industrial-scale hydrogen production for its own chemical manufacturing operations and aiming for commercialization within the decade.
In North America, Monolith stands out as a pioneer, having developed and scaled up its proprietary plasma-based pyrolysis reactors in Nebraska, USA. Monolith’s Olive Creek facility is expected to ramp up hydrogen and carbon black output through 2025, supported by strategic partnerships with industry leaders for both product off-take and technology deployment. The company has received investment and commitments from firms including Tokai Carbon Co., Ltd. and energy majors, further solidifying its competitive position.
In Asia, Toshiba Energy Systems & Solutions Corporation is actively developing methane pyrolysis systems as part of Japan’s national hydrogen roadmap, integrating its capabilities in advanced materials and industrial engineering. Toshiba’s hydrogen solutions are being tested in pilot projects in collaboration with government and private sector partners, with a focus on modular, scalable systems.
Australia is also emerging as a hub for innovation, with Hazer Group Limited commissioning its Commercial Demonstration Plant in Western Australia. The Hazer Process utilizes an iron ore catalyst for methane pyrolysis and is supported by governmental funding and offtake agreements for both hydrogen and graphite by-products.
Looking ahead, the competitive environment will likely intensify as these and other innovators scale up production, optimize process energy efficiency, and secure supply chain integration for both hydrogen and valuable co-products. Strategic collaborations, intellectual property development, and the ability to demonstrate cost-effective, low-carbon hydrogen at commercial scale will define leadership in this rapidly evolving sector over the next several years.
Major Projects & Pilot Installations (2024–2025)
Hydrogen pyrolysis—often referred to as methane pyrolysis or turquoise hydrogen—has seen significant momentum in pilot projects and demonstration-scale installations since 2024, as industries seek scalable, low-carbon hydrogen production methods. Major engineering developments are focused on scaling reactor technology, optimizing heat integration, and managing solid carbon by-products. In 2024 and 2025, several notable projects are advancing the commercial readiness of hydrogen pyrolysis.
- BASF: The German chemical giant is continuing its large-scale methane pyrolysis demonstration at Ludwigshafen, Germany. The project leverages a molten metal reactor to split methane into hydrogen and solid carbon, with the aim of drastically reducing CO2 emissions associated with traditional hydrogen production. The plant, which began operation in late 2023, is now providing critical engineering data on reactor performance, carbon handling, and integration with existing chemical infrastructure. BASF’s project is co-funded by the German Federal Ministry of Education and Research and is expected to inform decisions on commercial deployment by 2026. (BASF)
- Monolith: In the United States, Monolith is scaling up its commercial pyrolysis plant in Hallam, Nebraska. Their proprietary process uses renewable electricity to drive plasma-based methane splitting, generating hydrogen and carbon black. In 2024–2025, Monolith is expanding production capacity and collaborating with major partners in fertilizer and tire manufacturing to offtake both hydrogen and solid carbon. The company has received support from the U.S. Department of Energy and private investors, aiming to demonstrate both technical viability and product market integration at scale. (Monolith)
- Hazer Group: In Australia, Hazer Group’s Commercial Demonstration Plant (CDP) at Woodman Point is nearing completion, targeting continuous operation in 2025. Hazer’s catalytic pyrolysis process converts biogas into hydrogen and high-purity graphite, with the demonstration facility designed for 100 tonnes/year hydrogen output. The CDP is a key milestone in validating Hazer’s engineering approach for modular deployment and integration with wastewater treatment infrastructure. (Hazer Group)
- Ember: In Germany, Ember’s pilot plant is employing a novel allothermal pyrolysis reactor, aiming to showcase high efficiency and process scalability. The plant is engineered for flexible feedstocks and rapid load changes, providing data critical for grid integration and distributed hydrogen production schemes. Results from 2024–2025 will guide Ember’s plans for larger installations. (Ember)
These projects collectively represent significant progress in hydrogen pyrolysis systems engineering, with real-world operational data expected to de-risk technology, inform standards, and accelerate the commercial rollout of turquoise hydrogen within the next few years.
Cost Analysis: CAPEX, OPEX & LCOH Comparisons
A comprehensive cost analysis of hydrogen pyrolysis systems engineering in 2025 must address capital expenditure (CAPEX), operational expenditure (OPEX), and the levelized cost of hydrogen (LCOH), as industry players scale up from pilot to commercial deployments. Hydrogen pyrolysis, particularly methane pyrolysis, enables hydrogen production with solid carbon byproducts rather than CO2 emissions, offering economic and environmental advantages over conventional steam methane reforming (SMR) if process integration and scale are achieved.
Recent installations, such as those by BASF and Monolith, indicate that first-of-a-kind (FOAK) commercial units face relatively high CAPEX, ranging from $1,000 to over $2,000 per kg H2/year of capacity, depending on reactor design, feedstock handling, and carbon valorization infrastructure. For example, Monolith’s Olive Creek project in Nebraska, which aims for 94,000 tonnes per year hydrogen output, reflects a CAPEX in the $1 billion range, hinting at capital intensity comparable to blue hydrogen facilities in early phases.
OPEX in pyrolysis plants is heavily influenced by methane (natural gas or biogas) pricing, electricity costs (especially for plasma or electrically heated reactors), and the potential revenue from carbon co-products. Baker Hughes and LyondellBasell have announced strategic collaborations to optimize reactor energy efficiency and solid carbon handling, aiming to reduce OPEX below $1.50/kg H2 as plants scale and operational experience grows. The sale of carbon black or graphite can offset OPEX if market demand remains robust, but volatility in these commodity markets introduces uncertainty.
Looking ahead, the LCOH for hydrogen pyrolysis is projected to be $1.5–2.5/kg at 100,000 tpa scale, assuming natural gas prices under $5/MMBtu and solid carbon selling at or above $500/tonne, according to public techno-economic analyses and company disclosures (BASF). Several industry roadmaps foresee LCOH falling toward $1/kg by 2030 as modular reactor designs mature and carbon markets stabilize. Government incentives for low-carbon hydrogen and utilization of biogas/renewable methane could further enhance cost-competitiveness relative to blue and green hydrogen pathways.
- In 2025, CAPEX remains elevated but is expected to decrease as supply chains mature and standardization occurs.
- OPEX could decrease with energy integration and increasing carbon byproduct value.
- LCOH for pyrolysis hydrogen is already competitive in regions with low-cost methane and strong carbon markets, and may soon rival leading low-carbon alternatives.
Policy Drivers, Incentives & Regulatory Shifts
Policy and regulatory frameworks are exerting a significant influence on the deployment and engineering of hydrogen pyrolysis systems as the sector enters 2025. Governments and supranational bodies are increasingly differentiating between “green,” “blue,” and “turquoise” hydrogen, with pyrolysis—a process that decomposes methane into hydrogen and solid carbon without direct CO₂ emissions—emerging as a preferred pathway for low-carbon hydrogen, particularly where renewable electricity is constrained.
In the European Union, the 2021 adoption of the Fit for 55 package and the 2023 revision of the Renewable Energy Directive (RED III) have prompted member states to draft hydrogen strategies that recognize methane pyrolysis as a route to “low-carbon hydrogen” eligible for certain incentives, provided it meets strict CO₂ abatement thresholds. The European Commission’s delegated acts on hydrogen definitions are expected to further clarify the eligibility of pyrolysis-based hydrogen for contracts-for-difference, carbon contracts, and inclusion in Guarantee of Origin schemes by 2025-2026 (European Commission).
In the United States, the Inflation Reduction Act (IRA) of 2022 and the Bipartisan Infrastructure Law have triggered major investments in clean hydrogen, with Section 45V production tax credits (up to $3/kg) influencing engineering decisions at the system level. The U.S. Treasury’s guidance, anticipated in early 2025, will clarify lifecycle emission accounting and eligibility for hydrogen pyrolysis. Pilot projects like those by Monolith are closely watching regulatory definitions, which will determine their business models and system configurations. State-level incentives, particularly in California, are also expected to integrate pyrolysis-based hydrogen into low-carbon fuel standards and procurement mandates (California Energy Commission).
In Asia, Japan’s Green Growth Strategy and South Korea’s Hydrogen Economy Roadmap are shaping market signals for hydrogen pyrolysis. Both countries are supporting demonstration plants and have begun to consider solid carbon by-products (e.g., carbon black) as part of their circular economy initiatives (New Energy and Industrial Technology Development Organization (NEDO)). China is including turquoise hydrogen in its national hydrogen industry plans, though regulatory clarity is less advanced than in Western markets.
Looking to the next few years, regulatory harmonization and clear carbon accounting rules will be crucial for the scale-up of hydrogen pyrolysis systems. Engineering teams are increasingly factoring eligibility for credits and guarantees into plant design, process integration, and downstream carbon product utilization. As governments finalize rules and incentives, policy-driven demand for pyrolysis-based hydrogen and associated carbon products is expected to accelerate deployment by 2027.
Supply Chain & Feedstock Dynamics
Hydrogen pyrolysis, an emerging technological pathway for low-emission hydrogen production, is shaping new supply chain relationships and feedstock strategies in 2025. Unlike conventional steam methane reforming (SMR), pyrolysis decomposes hydrocarbons—most often methane—into hydrogen and solid carbon without direct CO₂ emissions. This approach redefines both input logistics and offtake planning for the hydrogen value chain.
A pivotal event in the sector is the commissioning of commercial-scale methane pyrolysis plants. BASF‘s pilot plant in Ludwigshafen, Germany, operational since 2024, is scaling up in 2025 and targeting integration with existing chemical infrastructure. The facility utilizes natural gas from regional suppliers, emphasizing the need for consistent, pipeline-grade methane feedstock. The plant’s design highlights the importance of close coordination between natural gas transmission operators and hydrogen producers to ensure uninterrupted, high-purity feedstock flows.
Meanwhile, Monolith in the United States is advancing its supply chain model with its Olive Creek facility, sourcing natural gas through long-term contracts with local suppliers. Their approach demonstrates a trend toward vertically integrated supply chains: securing feedstock, operating proprietary pyrolysis reactors, and managing both hydrogen and carbon black offtake. Monolith’s ongoing expansion in 2025 underscores the sector’s move toward industrial symbiosis, where solid carbon byproducts are channeled into the tire, plastics, and electronics industries.
Feedstock flexibility is an emerging consideration. While most systems currently rely on fossil-based methane, several developers are evaluating renewable biogas as a future input, aiming for negative or ultra-low carbon hydrogen. However, in 2025, the bulk of operational capacity is tied to natural gas, with biogas integration at demonstration or pilot scale.
From an engineering perspective, robust supply chains for high-purity methane, process catalysts, and reactor materials are critical. The need for specialized, corrosion-resistant alloys and reactor internals has led manufacturers to collaborate closely with suppliers, such as thyssenkrupp, to ensure material durability and equipment reliability.
Looking ahead, anticipated growth in hydrogen pyrolysis capacity will place new demands on upstream methane logistics and downstream carbon handling. The sector is expected to strengthen partnerships with gas utilities, carbon offtakers, and technology providers, laying the foundation for larger-scale, geographically diverse projects. Supply chain resilience, feedstock traceability, and optimizing carbon product markets will remain focal points for hydrogen pyrolysis systems engineering in the coming years.
Investment Trends & Funding Landscape
Investment in hydrogen pyrolysis systems engineering has accelerated markedly in 2025, driven by global decarbonization targets, rising demand for low-carbon hydrogen, and the quest for scalable, cost-competitive alternatives to conventional hydrogen production. The technology—also known as methane pyrolysis or turquoise hydrogen—splits methane into hydrogen and solid carbon without direct CO2 emissions, attracting attention from both government and private sectors.
In 2025, significant venture capital and strategic corporate funding rounds have been reported. For example, Hydrogenious LOHC Technologies and Hyzon Motors have announced multi-million dollar investments to advance their proprietary pyrolysis reactors and integrate them into pilot and early commercial-scale projects. Similarly, Monolith, a leader in methane pyrolysis, secured over $300 million in cumulative funding through a mix of private equity and public grants, notably from the U.S. Department of Energy to expand its Olive Creek facility. This site is among the first to demonstrate continuous commercial-scale hydrogen and carbon black co-production, setting a benchmark for future projects.
National and regional funding programs continue to bolster the sector. In Europe, the Clean Hydrogen Partnership has earmarked dedicated funds in 2025 for demonstration projects involving turquoise hydrogen, with a focus on industrial integration and lifecycle emissions validation. In Germany, BASF and other industrial partners have attracted public-private investment to scale up pyrolysis units aimed at decarbonizing chemical feedstocks and steel production. Such collaborations are seen as crucial for de-risking new technologies and bringing them to market.
Corporate venture arms are also active, with companies like Baker Hughes and Air Liquide participating in co-development and minority equity stakes in pyrolysis start-ups, signaling long-term commitment. The scale of investments is expected to rise further as regulatory frameworks, such as the EU’s Carbon Border Adjustment Mechanism and the U.S. Inflation Reduction Act, begin to favor low-carbon hydrogen pathways.
Looking ahead, the funding landscape for hydrogen pyrolysis systems is anticipated to remain dynamic. With growing interest from institutional investors and sovereign funds, alongside government incentives, the field is poised for a wave of commercial-scale deployments and continued innovation in system engineering, efficiency, and integration by 2027.
Future Outlook: Disruptive Innovations & Roadmap to 2030
Hydrogen pyrolysis, also known as methane pyrolysis or turquoise hydrogen production, is rapidly emerging as a disruptive technology in the hydrogen sector. This process decomposes methane at high temperatures into hydrogen gas and solid carbon, eliminating the direct emission of CO2. As the world pivots towards low-carbon hydrogen to meet climate targets, engineering innovations in hydrogen pyrolysis are poised to accelerate its commercial deployment between 2025 and 2030.
Current advancements are focused on scaling up reactor designs and improving process efficiency. In 2025, modular pilot and demonstration plants are operating, with several entering early commercial phases. For example, BASF is developing methane pyrolysis reactors targeting industrial-scale hydrogen production, aiming for significant emissions reductions compared to conventional steam methane reforming. Similarly, Hyzon Motors has announced a proprietary methane pyrolysis technology with the goal of reducing hydrogen production costs to under $3/kg, a key benchmark for market competitiveness.
An important innovation trend is integrating pyrolysis with renewable energy sources to maximize lifecycle emissions benefits. Companies like Monolith are constructing large-scale facilities in the United States, planning to supply hydrogen and solid carbon black for industrial markets. Their flagship Olive Creek facility is projected to produce tens of thousands of tons of hydrogen annually by 2025, leveraging renewable electricity to power the process.
Solid carbon management is also a focal point for system engineering. Technologies are being developed to valorize the carbon by-product, turning it into valuable materials such as carbon black, graphite, or advanced composites. This circular approach is expected to enhance the economics of pyrolysis hydrogen and drive further investment.
- By 2027, several major chemical and energy firms anticipate commercial-scale hydrogen pyrolysis units, with integrated carbon product lines, to be operational.
- Standardization of reactor designs and process control systems is underway, led by industry bodies such as Hydrogen Council, to facilitate wider adoption and interoperability.
- Policy frameworks in the EU and US are evolving to include “turquoise hydrogen” under low-carbon hydrogen definitions, paving the way for incentives and offtake agreements.
Looking towards 2030, hydrogen pyrolysis is expected to become a cornerstone of industrial decarbonization strategies. Continued systems engineering innovations—such as heat integration, advanced catalysts, and digitalized process control—will drive down costs and enhance reliability. The sector is set for rapid expansion, positioning hydrogen pyrolysis as a disruptive force in the global hydrogen economy.