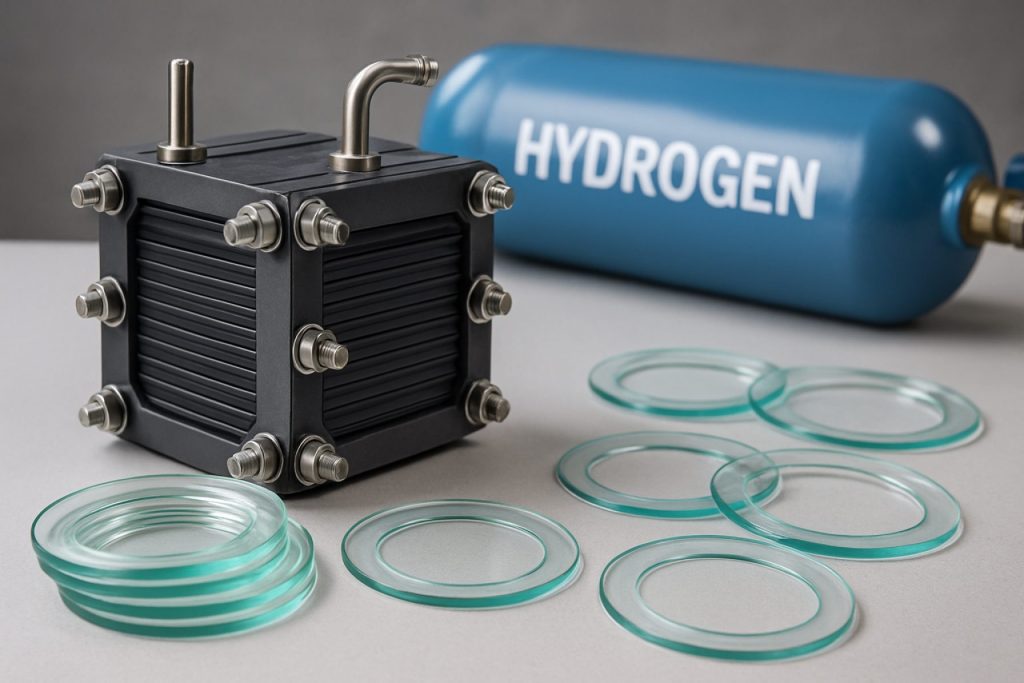
Table of Contents
- Executive Summary: Defining 2025’s Glass Sealing Gasket Landscape
- Market Size & Growth Forecasts Through 2030
- Key Drivers: Hydrogen Economy Expansion and Electrolyzer Demand
- Technology Deep Dive: Glass Sealing Gasket Innovations
- Competitive Landscape: Leading Manufacturers and Strategic Moves
- Material Science Advances and Performance Benchmarks
- Regulatory and Industry Standards Impacting Gasket Manufacturing
- Supply Chain Challenges and Opportunities
- Regional Analysis: Key Markets and Emerging Hotspots
- Future Outlook: Trends, Investments, and Next-Gen Opportunities
- Sources & References
Executive Summary: Defining 2025’s Glass Sealing Gasket Landscape
The landscape for glass sealing gasket manufacturing in hydrogen electrolyzers is poised for significant evolution in 2025, underpinned by the rapidly scaling hydrogen economy and the drive for durable, high-performance electrochemical components. Glass-to-metal seals and glass-ceramic gaskets are critical in proton exchange membrane (PEM) and solid oxide electrolyzer cell (SOEC) stacks, providing hermetic sealing, electrical insulation, and corrosion resistance under demanding operational conditions.
In 2025, leading manufacturers are expanding their production capacities and portfolio of sealing materials tailored to hydrogen electrolyzers. SCHOTT AG has highlighted the increasing demand for glass-to-metal sealing solutions, investing in material innovations such as alkali-resistant glass compositions to enhance stack longevity and safety. Likewise, Heraeus continues to refine its glass-ceramic sealants for advanced SOEC and PEM designs, focusing on minimizing hydrogen permeation and optimizing thermal expansion compatibility.
Component suppliers like Elan Technology and Pacific Ceramics are scaling up to meet OEM demand for bespoke glass sealing solutions, reporting increased inquiries and orders from electrolyzer integrators across Europe and Asia. These developments align with the surge in electrolyzer gigafactory announcements, notably by Siemens Energy and Nel Hydrogen, both of which emphasize the reliability and longevity of stack sealing technologies in their future product roadmaps.
Technical challenges persist in balancing manufacturability, leak-tightness, and thermal cycling resistance. Industry standards are evolving, with organizations such as the Fuel Cell & Hydrogen Energy Association calling for harmonized testing protocols to qualify glass sealing gaskets under realistic hydrogen service conditions. In response, manufacturers are investing in advanced simulation and accelerated aging tests to validate new glass formulations and assembly processes.
Looking forward, 2025 will see intensified collaboration between electrolyzer OEMs, material science innovators, and component suppliers, aiming to deliver scalable, cost-effective, and robust glass sealing gaskets. The sector’s outlook is strengthened by public and private investments in hydrogen infrastructure, ensuring that glass sealing technology remains a cornerstone of next-generation electrolyzer reliability and safety.
Market Size & Growth Forecasts Through 2030
The market for glass sealing gasket manufacturing in hydrogen electrolyzers is experiencing significant momentum as the global push for clean hydrogen accelerates. Glass-to-metal and glass-to-ceramic seals are critical in proton exchange membrane (PEM) and solid oxide electrolyzer cells (SOEC), where they ensure hermeticity, chemical resistance, and operational durability under harsh conditions. Glass sealing gaskets are favored for their ability to withstand high temperatures, corrosive environments, and pressure differentials typical in electrolyzer stacks.
As of 2025, demand is being driven by large-scale electrolyzer projects in Europe, Asia, and North America, supported by government incentives and green hydrogen mandates. Major electrolyzer OEMs are scaling up capacity, with several gigawatt-scale plants announced or under construction. For example, Siemens Energy and Nel ASA are expanding their manufacturing footprints, both relying on robust component supply chains, including glass sealing gaskets, to support projected multi-gigawatt deployment.
Specialty materials manufacturers, such as SCHOTT and Heraeus, report growing order volumes for glass sealing technologies tailored to hydrogen applications. SCHOTT, for instance, is developing glass-to-metal seals optimized for the unique challenges of PEM and SOEC electrolyzers, emphasizing gas tightness and resistance to aggressive electrolytes. Heraeus is similarly innovating in glass-ceramic compositions to meet the reliability and operational life requirements of next-generation electrolyzer stacks.
Looking toward 2030, the outlook for this niche market is strongly positive. Industry roadmaps anticipate installed electrolyzer capacity may exceed 100 GW globally by the end of the decade, with Europe and Asia-Pacific regions leading growth (Siemens Energy). As electrolyzer stack production scales, demand for high-performance glass sealing gaskets is expected to grow at a compound annual growth rate (CAGR) in the double digits. Recent investments in advanced materials R&D and automation of gasket manufacturing processes, as seen at SCHOTT, underscore the sector’s readiness to meet rising quality and volume requirements.
- 2025: Market growth underpinned by gigawatt-scale electrolyzer projects and strategic supplier partnerships.
- 2026–2030: Rapid expansion as new manufacturing lines come online, with increasing adoption in both PEM and SOEC technologies.
- By 2030: Anticipated multi-fold increase in gasket volumes, driven by global decarbonization targets and hydrogen economy maturation.
Key Drivers: Hydrogen Economy Expansion and Electrolyzer Demand
The rapid expansion of the hydrogen economy is a pivotal driver for the glass sealing gasket manufacturing sector, particularly in relation to hydrogen electrolyzers. As nations and industries intensify decarbonization efforts, electrolyzer deployment is accelerating, fueling a corresponding surge in demand for high-performance sealing solutions. Glass sealing gaskets, essential for ensuring gas-tight integrity and chemical resistance in electrolyzer stacks, are increasingly recognized as critical components for system efficiency and safety.
In 2025, the landscape is shaped by substantial public and private investments into green hydrogen infrastructure. The European Union’s Clean Hydrogen Partnership has set ambitious targets for electrolyzer capacity, aiming for at least 100 GW installed by 2030, with significant capacity to be realized by 2025 (Clean Hydrogen Partnership). This is mirrored by large-scale manufacturing expansions from leading electrolyzer OEMs such as Siemens Energy and Nel Hydrogen, both of which rely on robust supply chains for critical stack components, including glass-to-metal and glass-ceramic gaskets.
Electrolyzer manufacturers are increasingly specifying advanced glass sealing gaskets for both proton exchange membrane (PEM) and alkaline electrolyzer stacks, as these gaskets provide essential hermeticity under high pressures and corrosive environments. Companies such as Schott and Heraeus are actively innovating in this space, developing glass-to-metal sealing technologies that address demanding hydrogen electrolyzer operating conditions. For instance, Schott has recently announced advancements in glass seal materials tailored for next-generation hydrogen applications, focusing on durability, thermal cycling, and long-term reliability.
The outlook for 2025 and the subsequent years points to further intensification of demand, as more nations incorporate clean hydrogen targets into their energy transitions. The U.S. Department of Energy’s Hydrogen Shot initiative, for example, is catalyzing domestic electrolyzer manufacturing and supply chain development (U.S. Department of Energy). This macroeconomic momentum is compelling gasket manufacturers to scale production, enhance quality control, and collaborate closely with OEMs for customized solutions.
Overall, the expansion of the hydrogen economy is tightly interlinked with advances and growth in glass sealing gasket manufacturing. The industry’s trajectory in 2025 and beyond is characterized by increased capacity, technological innovation, and strategic partnerships to meet the stringent demands of next-generation hydrogen electrolyzer deployment.
Technology Deep Dive: Glass Sealing Gasket Innovations
Glass sealing gaskets are a crucial component in the assembly of hydrogen electrolyzers, particularly in solid oxide and proton exchange membrane (PEM) systems, where chemical resistance, hermeticity, and thermal stability are paramount. As the global hydrogen sector accelerates into 2025, manufacturers are directing significant R&D efforts toward advanced glass sealing technologies to improve reliability and efficiency in electrolyzer stacks.
One major area of innovation is the development of glass-ceramic composite gaskets, which combine the low leakage rates and chemical inertness of glass with enhanced mechanical compliance. Companies like SCHOTT AG are actively producing tailored glass-ceramic solutions for hydrogen electrolyzers, emphasizing high ionic resistance and long-term durability even under cyclic thermal and pressure loads. SCHOTT’s recent advancements focus on minimizing interfacial reactions and improving wettability to metallic and ceramic interconnects, which are essential for scaling up electrolyzer stacks beyond the 5MW threshold.
Precision in manufacturing is also advancing, with companies such as Heraeus adopting automated laser-cutting and screen-printing processes for glass powder deposition, ensuring consistent thickness and dimensional tolerances across high-volume production lines. These techniques are critical for meeting the evolving requirements of next-generation electrolyzers, which demand gasket thicknesses below 100 microns for minimized electrical resistance and stack height.
Material composition is another focus. Nippon Electric Glass has introduced borosilicate and aluminosilicate glass formulations specifically engineered for compatibility with nickel and stainless-steel-based electrolyzer components, targeting improved sealing performance during rapid thermal cycling and resistance to humidified hydrogen atmospheres. Their ongoing pilot-scale production, slated for commercial deployment in 2025, is positioned to serve both the Asian and European electrolyzer markets.
Looking forward, the outlook for glass sealing gasket technology in hydrogen electrolyzers is defined by greater stack sizes, higher operational pressures, and more aggressive durability standards. Major suppliers are expected to expand collaborations with electrolyzer OEMs for co-innovation and rapid prototyping, while process digitalization (e.g., in-line quality control and predictive defect analysis) will gain adoption to ensure reliability and traceability. These advances will be critical in supporting the scaling of green hydrogen infrastructure globally over the next several years.
Competitive Landscape: Leading Manufacturers and Strategic Moves
The competitive landscape for glass sealing gasket manufacturing in hydrogen electrolyzers is rapidly evolving as the global push for green hydrogen accelerates. In 2025, several established industrial material specialists and emerging innovators are positioning themselves as key suppliers to electrolyzer OEMs, focusing on advanced glass-to-metal and glass-ceramic sealing technologies that ensure durability, chemical resistance, and hydrogen tightness.
Among the leaders, SCHOTT AG continues to leverage its decades-long expertise in glass-to-metal sealing, offering hermetic feedthroughs and custom glass components tailored for electrochemical cells. SCHOTT’s high-performance gaskets are specifically engineered for proton exchange membrane (PEM) and solid oxide electrolyzers, with recent investments in production capacity to meet surging demand from European and Asian electrolyzer manufacturers.
Similarly, Heraeus has expanded its portfolio of glass sealing materials, including specialized glasses and glasses for metal-ceramic joining, aimed at the hydrogen sector. The company’s glass-to-metal seals are designed for robust performance under high-pressure hydrogen conditions, and Heraeus is actively collaborating with electrolyzer system integrators for joint development projects.
Japan’s Nippon Electric Glass Co., Ltd. (NEG) is also intensifying its focus on the hydrogen market, with proprietary glass compositions for sealing gaskets that offer enhanced reliability at elevated temperatures—critical for solid oxide electrolyzer applications. NEG is investing in R&D and pilot-scale manufacturing lines to support the next generation of electrolyzer stacks.
On the supplier side, Elan Technology in the US provides custom glass-to-metal sealing solutions and technical glass gaskets, with a growing base of clients in the hydrogen value chain. The company is scaling up production and developing rapid prototyping services to shorten development cycles for electrolyzer OEMs.
Looking ahead, the competitive landscape is expected to intensify further as demand from gigawatt-scale electrolyzer projects increases. Strategic moves include capacity expansions, localized manufacturing to serve regional markets, and partnerships with stack developers to co-engineer solutions. Leading manufacturers are also investing in automation and digital quality control to ensure consistent gasket performance at scale. As hydrogen infrastructure expands, the ability to deliver reliable, high-volume, and application-specific glass sealing gaskets will be a critical differentiator in this market.
Material Science Advances and Performance Benchmarks
In 2025, the field of glass sealing gasket manufacturing for hydrogen electrolyzers is witnessing notable material science advances, driven by the need for higher-efficiency, longer-lifetime, and cost-effective electrolyzer stacks. Glass sealing gaskets are critical components that ensure the gas-tight separation of hydrogen and oxygen, while providing electrical insulation and chemical stability under harsh electrochemical environments. Recent innovations center on optimizing glass compositions and manufacturing protocols to meet the stringent demands of next-generation proton exchange membrane (PEM) and solid oxide electrolyzers.
Key manufacturers and suppliers such as SCHOTT AG and Heraeus are actively developing advanced glass-to-metal sealing technologies. These companies focus on low-alkali, borosilicate, and aluminosilicate glass systems, which deliver improved resistance to alkali vapor and minimize ion migration that can compromise long-term performance. Material scientists are also working on glass-ceramic composites, offering tailored coefficients of thermal expansion (CTE) to precisely match metallic interconnects—a critical factor for durability during thermal cycling.
Performance benchmarks in 2025 are increasingly defined by durability targets exceeding 80,000 operating hours, hydrogen purity above 99.999%, and resistance to temperatures above 800°C for solid oxide electrolyzers. Glass seals must also withstand repeated start-stop cycles without microcracking or delamination. Saint-Gobain and ElringKlinger AG are publishing technical data on their glass-sealing materials, showing mechanical strength retention and gas impermeability after thousands of thermal cycles and continuous operation in aggressive environments.
Looking ahead, the next few years will see accelerated collaboration between electrolyzer OEMs and glass seal specialists to commercialize new formulations aimed at reducing stack costs and boosting efficiency. Advances in automated glass gasket manufacturing—such as precision slurry casting and laser-assisted sealing—are expected to further enhance consistency and scalability. As hydrogen production ramps up in response to global decarbonization goals, the role of high-performance glass sealing gaskets will become even more pivotal, with ongoing material science breakthroughs setting new industry standards.
Regulatory and Industry Standards Impacting Gasket Manufacturing
The regulatory and industry standards landscape is evolving rapidly for glass sealing gasket manufacturing in hydrogen electrolyzers, particularly as global decarbonization targets accelerate the adoption of green hydrogen technologies. By 2025 and in the following years, manufacturers are facing increasingly stringent requirements around material performance, safety, and environmental impact to ensure reliable and efficient electrolyzer operation.
At the core, glass sealing gaskets in proton exchange membrane (PEM) and solid oxide electrolyzers must comply with international standards governing hydrogen systems. The International Organization for Standardization (ISO) and the International Electrotechnical Commission (IEC) both maintain key frameworks, such as ISO 22734 for hydrogen generators using water electrolysis and IEC 62282-3 for fuel cell technologies, which specify test methods and safety criteria for components including gaskets. Recent updates to these standards have emphasized chemical durability, hydrogen impermeability, and high-temperature stability—qualities that glass sealing gaskets must demonstrably meet through rigorous type testing and certification.
Within Europe, the CEN-CENELEC harmonization initiatives are driving alignment of national standards with EU directives, such as the Pressure Equipment Directive (PED) 2014/68/EU, impacting the design and material selection for electrolyzer gaskets. Manufacturers like SCHOTT and Heraeus have publicly acknowledged ongoing investments in compliance with REACH and RoHS regulations, ensuring glass compositions for sealing gaskets eliminate hazardous substances while maintaining high-performance sealing characteristics.
- Material Traceability and Quality Assurance: Regulatory bodies increasingly mandate traceability of raw materials and in-process controls. For example, SCHOTT has implemented digital tracking systems for glass-to-metal seal production to meet customer and regulatory audit requirements.
- Hydrogen Permeation Testing: As electrolyzer pressures rise, standards such as ISO 14687 now require quantitative hydrogen leak testing, driving innovation in gasket glass formulations and manufacturing process control. Companies are adapting their quality management systems accordingly.
- Global Certification: Gasket suppliers must navigate parallel certification pathways for North American, European, and Asian markets. Heraeus and Nippon Electric Glass report ongoing coordination with notified bodies and testing labs to streamline product approvals for electrolyzer OEMs.
Looking ahead, as governments and industry alliances—such as those coordinated by the Hydrogen Europe—prioritize safety and lifecycle sustainability, glass sealing gasket manufacturers are likely to see further tightening of regulations and standards. This will foster greater transparency, higher reliability, and accelerated innovation in gasket materials and manufacturing processes through 2025 and beyond.
Supply Chain Challenges and Opportunities
The supply chain for glass sealing gasket manufacturing, a critical component in hydrogen electrolyzers, is currently undergoing significant evolution as the hydrogen economy accelerates in 2025 and beyond. Glass-to-metal seals are essential for ensuring the chemical stability, gas-tightness, and longevity of electrolyzer stacks, particularly in proton exchange membrane (PEM) and solid oxide electrolyzers. As demand for green hydrogen rises, so does the need for reliable and scalable supply chains for these specialized gaskets.
A key challenge in 2025 is the limited number of suppliers capable of producing glass sealing gaskets that meet the stringent purity and durability requirements for hydrogen applications. Manufacturers such as SCHOTT AG and Heraeus are among the few global players with the technical expertise and established production lines for glass-to-metal sealing technology suitable for electrolyzers. However, the ramp-up in electrolyzer gigafactory projects, particularly in Europe and Asia, is placing pressure on these specialized upstream suppliers to expand capacity and diversify their material sourcing.
Raw material sourcing is another bottleneck, especially for high-purity glass and compatible metals such as nickel, stainless steel, and specialty alloys. Fluctuations in raw material prices and logistical disruptions—exacerbated by global geopolitical tensions—pose a risk to the stability and predictability of gasket supply. Companies are increasingly looking to secure long-term contracts and localize parts of their supply chain to mitigate these risks. For instance, SCHOTT AG has announced investments in expanding its manufacturing facilities in Germany and the US to address anticipated increases in demand and shorten lead times.
Despite these challenges, opportunities are emerging. Collaborative efforts between electrolyzer OEMs and gasket manufacturers are fostering innovations in material science, process automation, and quality control, aiming to improve yield and reduce costs. Industry initiatives to standardize gasket designs and specifications—led by bodies such as Fuel Cells and Hydrogen Joint Undertaking (FCH JU)—are also helping to streamline procurement and qualification processes, making it easier for new entrants to contribute to the supply base.
Looking ahead, the supply chain for glass sealing gaskets is expected to become more resilient through vertical integration, regional diversification, and digitalization. As electrolyzer deployment scales up through 2025 and into the latter part of the decade, continued investment in capacity, skills, and cross-sector collaboration will be essential to meet the growing and increasingly sophisticated needs of the hydrogen sector.
Regional Analysis: Key Markets and Emerging Hotspots
The global landscape for glass sealing gasket manufacturing for hydrogen electrolyzers is rapidly evolving, with key regional markets demonstrating significant momentum through 2025 and beyond. The critical role of high-integrity glass-to-metal seals in proton exchange membrane (PEM) and alkaline electrolyzers—essential for safe and efficient hydrogen production—has catalyzed investment and capacity expansion in established and emerging regions.
- Europe: Europe remains at the forefront of both hydrogen electrolyzer deployment and the associated supply chains, including specialized sealing technologies. Germany, in particular, is a hub for advanced materials and component manufacturing, with companies like SCHOTT AG producing glass-to-metal seals tailored for the demanding conditions of electrolyzers. The region benefits from ambitious EU targets—such as the “Fit for 55” package and REPowerEU plan—which are accelerating electrolyzer adoption and thus driving demand for reliable glass sealing gaskets.
- Asia-Pacific: China, Japan, and South Korea are experiencing rapid growth in both electrolyzer manufacturing and the supporting ecosystem. China’s domestic focus on green hydrogen has spurred local firms to invest in high-precision glass gasket capabilities. Japanese companies, such as NGK Insulators, Ltd., are leveraging ceramics and glass expertise to supply components for leading electrolyzer OEMs. South Korea is similarly scaling up, with government-backed initiatives supporting local supply chains.
- North America: The United States and Canada are emerging as key players, propelled by policy incentives under frameworks like the U.S. Inflation Reduction Act and Canada’s Clean Hydrogen Strategy. U.S.-based manufacturers such as Specialty Seal Group are scaling up production and focusing on custom glass-to-metal sealing solutions for electrolyzer stacks and balance-of-plant applications. The North American market is expected to expand further as new gigawatt-scale hydrogen projects come online through 2025 and 2026.
- Emerging Hotspots: India and the Middle East are building domestic hydrogen sectors, with early investments in electrolyzer assembly and component production. These regions are actively courting technology transfers and joint ventures to develop local glass sealing gasket capabilities, aiming to reduce reliance on imports as demand accelerates.
Outlook for 2025 and beyond suggests growing localization of critical electrolyzer components, including glass sealing gaskets, as governments and OEMs seek resilient, regionally sourced supply chains. The sector is expected to see increasing collaboration between materials specialists and electrolyzer manufacturers to meet the stringent performance and durability requirements of next-generation hydrogen infrastructure.
Future Outlook: Trends, Investments, and Next-Gen Opportunities
As the hydrogen economy accelerates towards 2025 and beyond, the glass sealing gasket manufacturing segment for hydrogen electrolyzers is poised for pivotal advancements and investment. Glass sealing gaskets play a vital role in ensuring the durability, chemical resistance, and gas tightness of proton exchange membrane (PEM) and solid oxide electrolyzers, which are central to green hydrogen production.
A key trend is the shift towards advanced glass-ceramic composites that combine the chemical inertness of glass with the mechanical stability of ceramics. Leading electrolyzer manufacturers such as Siemens Energy and Nel Hydrogen have highlighted the criticality of robust sealing technologies, emphasizing investments into high-purity glass materials and automated gasket fabrication. The ongoing expansion of gigawatt-scale electrolyzer factories in Europe and Asia is expected to drive demand for both traditional and next-generation sealing solutions.
With the European Union and countries like Japan and South Korea outlining ambitious hydrogen roadmaps for 2030, suppliers such as SCHOTT AG are scaling up R&D efforts in hermetic glass-to-metal seals specifically engineered for harsh electrolyzer environments. SCHOTT has reported prototype developments for gaskets with enhanced leak-tightness under high-pressure, high-temperature conditions, supporting the industry’s move towards higher efficiency and longer system lifespans.
Strategic investments are also flowing toward process automation and quality control. Companies like ElringKlinger AG are implementing advanced inspection technologies and digital manufacturing platforms to ensure consistency and traceability in gasket production—key to meeting the stringent safety requirements of hydrogen systems.
Looking ahead, the next few years are expected to witness collaborations between material science leaders and electrolyzer OEMs to co-develop custom sealing materials optimized for novel stack designs and variable operating conditions. Industry consortia, such as those coordinated by VDE Association for Electrical, Electronic & Information Technologies, are actively working on standards for gasket performance, aiming to harmonize testing and certification across regions.
Overall, 2025 marks an inflection point for glass sealing gasket manufacturing in hydrogen electrolyzers, with rapid scaling, innovation in material science, and digitalized quality assurance emerging as defining features of the sector’s future trajectory.
Sources & References
- SCHOTT AG
- Heraeus
- Siemens Energy
- Nel Hydrogen
- Fuel Cell & Hydrogen Energy Association
- Clean Hydrogen Partnership
- Nippon Electric Glass Co., Ltd.
- ElringKlinger AG
- International Organization for Standardization (ISO)
- CEN-CENELEC
- Hydrogen Europe
- NGK Insulators, Ltd.
- Specialty Seal Group
- VDE Association for Electrical, Electronic & Information Technologies