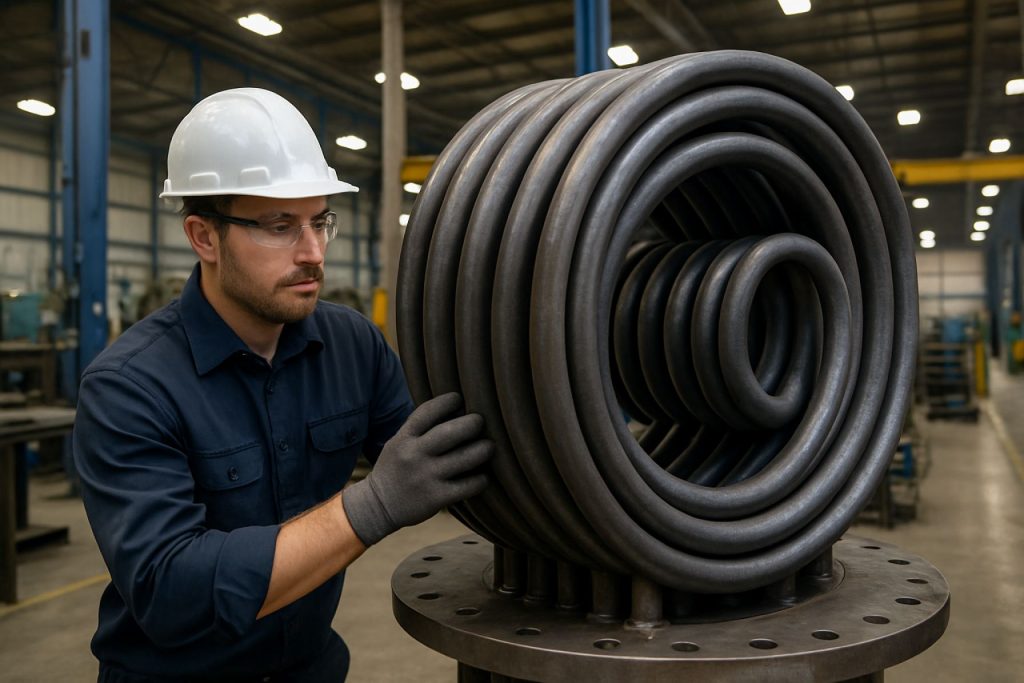
Geothermal Heat Exchanger Manufacturing in 2025: Innovations, Market Expansion, and the Path to Sustainable Energy Solutions. Explore the Key Drivers and Future Trends Shaping This High-Growth Sector.
- Executive Summary: 2025 Market Highlights and Key Takeaways
- Industry Overview: Geothermal Heat Exchanger Manufacturing Landscape
- Market Size and Forecast (2025–2030): Growth Rates and Projections
- Key Manufacturers and Competitive Dynamics
- Technological Innovations and R&D Trends
- Supply Chain, Materials, and Production Advances
- Regulatory Environment and Industry Standards
- Regional Analysis: Leading Markets and Emerging Opportunities
- Sustainability, Decarbonization, and Environmental Impact
- Future Outlook: Strategic Opportunities and Challenges Ahead
- Sources & References
Executive Summary: 2025 Market Highlights and Key Takeaways
The geothermal heat exchanger manufacturing sector is poised for significant growth in 2025, driven by global decarbonization efforts, rising energy costs, and increasing adoption of renewable heating and cooling solutions. Geothermal heat exchangers—critical components in ground source heat pump (GSHP) systems—are experiencing heightened demand across residential, commercial, and industrial markets. This surge is underpinned by supportive policy frameworks in North America, Europe, and parts of Asia, as well as technological advancements that are improving system efficiency and reducing installation costs.
Key industry players such as Bosch Thermotechnology, Viessmann, and Trane Technologies are expanding their geothermal product portfolios and manufacturing capacities to meet this demand. Bosch Thermotechnology continues to invest in R&D for more efficient and durable heat exchanger designs, while Viessmann is focusing on modular systems that simplify installation and maintenance. Trane Technologies is leveraging its global supply chain to scale up production and address supply bottlenecks, particularly in North America and Europe.
In 2025, the market is characterized by a shift toward advanced materials such as high-density polyethylene (HDPE) and stainless steel, which enhance the longevity and thermal performance of heat exchangers. Manufacturers are also adopting automated fabrication processes to improve quality control and reduce lead times. The integration of digital monitoring and control systems is becoming standard, enabling predictive maintenance and optimizing system performance.
Government incentives and regulatory mandates are accelerating adoption. For example, the European Union’s Fit for 55 package and the U.S. Inflation Reduction Act are providing substantial financial support for geothermal installations, directly benefiting heat exchanger manufacturers. In Asia, countries like China and Japan are increasing investments in geothermal infrastructure, further expanding the addressable market for manufacturers.
Looking ahead, the outlook for geothermal heat exchanger manufacturing remains robust. Industry analysts anticipate double-digit annual growth rates through the late 2020s, with the sector’s expansion supported by ongoing urbanization, electrification of heating, and the need for resilient, low-carbon energy solutions. Companies with strong R&D capabilities, scalable manufacturing, and global distribution networks—such as Bosch Thermotechnology, Viessmann, and Trane Technologies—are well positioned to capitalize on these trends and shape the future of geothermal heat exchanger technology.
Industry Overview: Geothermal Heat Exchanger Manufacturing Landscape
The geothermal heat exchanger manufacturing sector is experiencing a period of dynamic growth and technological advancement as the global push for decarbonization intensifies. In 2025, the industry is characterized by a diverse array of manufacturers specializing in both closed-loop and open-loop systems, with a particular emphasis on ground source heat pump (GSHP) applications for residential, commercial, and industrial markets. The demand for efficient, durable, and cost-effective heat exchangers is being driven by government incentives, stricter building codes, and the increasing adoption of renewable heating and cooling solutions.
Key players in the sector include established multinational corporations and specialized engineering firms. Bosch is a prominent example, leveraging its global manufacturing footprint and R&D capabilities to produce advanced geothermal heat pump systems and associated heat exchangers. Trane Technologies is another major manufacturer, offering a range of geothermal solutions tailored for both commercial and residential applications. Daikin, recognized for its innovation in HVAC technologies, has expanded its geothermal product lines, integrating high-efficiency heat exchangers into its systems.
Specialized companies such as Viessmann and ClimateMaster focus on the design and manufacture of ground heat exchangers, often collaborating with drilling and installation partners to deliver turnkey solutions. Viessmann in particular has invested in modular, scalable heat exchanger designs to address the needs of both small-scale and district energy projects. Meanwhile, ClimateMaster continues to innovate in the U.S. market, emphasizing energy efficiency and system longevity.
Material innovation is a notable trend, with manufacturers increasingly adopting high-density polyethylene (HDPE) and corrosion-resistant alloys to enhance the lifespan and performance of heat exchangers. Automation and digitalization are also reshaping production processes, enabling greater customization and quality control. The integration of smart monitoring systems is becoming standard, allowing for predictive maintenance and optimization of geothermal systems.
Looking ahead, the geothermal heat exchanger manufacturing landscape is expected to expand further as more countries implement policies supporting renewable heating and cooling. The sector is poised for continued investment in R&D, with a focus on reducing installation costs, improving thermal conductivity, and scaling up for large infrastructure projects. As the industry matures, collaboration between manufacturers, utilities, and policymakers will be crucial in meeting the growing demand for sustainable energy solutions.
Market Size and Forecast (2025–2030): Growth Rates and Projections
The geothermal heat exchanger manufacturing sector is poised for robust growth between 2025 and 2030, driven by increasing global emphasis on renewable energy, decarbonization targets, and the electrification of heating and cooling systems. As governments and industries intensify efforts to reduce greenhouse gas emissions, demand for efficient geothermal systems—particularly ground source heat pumps (GSHPs) and their associated heat exchangers—is expected to accelerate.
Key players in the sector, such as Bosch Thermotechnology, Viessmann, and Trane Technologies, are expanding their geothermal product lines and manufacturing capacities to meet this anticipated surge. These companies are investing in advanced materials and automated production processes to improve the efficiency and durability of heat exchangers, which are critical components in geothermal systems.
In 2025, the global market for geothermal heat exchangers is estimated to be valued in the low single-digit billions (USD), with Europe and North America representing the largest regional markets due to supportive policy frameworks and established installation bases. The European Union’s Fit for 55 package and the U.S. Inflation Reduction Act are expected to further stimulate adoption of geothermal technologies, including heat exchangers, through incentives and regulatory support.
Growth rates for the geothermal heat exchanger manufacturing market are projected to range from 7% to 10% annually through 2030, with the highest expansion anticipated in regions with aggressive climate targets and rising energy costs. Manufacturers such as NIBE Industrier and Stiebel Eltron are actively scaling up production and innovating with new heat exchanger designs to capture this growth. Additionally, companies like Danfoss are focusing on integrating digital monitoring and control technologies into their heat exchanger offerings, enhancing system performance and lifecycle management.
Looking ahead, the market outlook remains positive, with continued investment in R&D and manufacturing capacity expected from both established players and emerging entrants. The sector’s growth will be underpinned by ongoing urbanization, electrification of heating, and the need for sustainable building solutions. As a result, geothermal heat exchanger manufacturing is set to play a pivotal role in the global transition to low-carbon energy systems through 2030 and beyond.
Key Manufacturers and Competitive Dynamics
The geothermal heat exchanger manufacturing sector in 2025 is characterized by a blend of established industrial giants and specialized engineering firms, each vying for technological leadership and market share as global demand for sustainable heating and cooling solutions accelerates. The competitive landscape is shaped by ongoing innovation in materials, design efficiency, and installation methods, with a strong emphasis on reducing environmental impact and lifecycle costs.
Among the most prominent players, Bosch continues to leverage its extensive experience in heating and cooling technologies, offering a range of ground source heat pump systems and associated heat exchangers. The company’s manufacturing operations emphasize high-efficiency, corrosion-resistant materials and modular designs, catering to both residential and commercial applications. Similarly, Viessmann maintains a significant presence in Europe and North America, focusing on integrated geothermal solutions and digital monitoring capabilities to optimize system performance.
In North America, Trane Technologies and Carrier are key competitors, each with dedicated product lines for geothermal heat exchangers. These companies invest heavily in R&D to improve heat transfer efficiency and reduce installation complexity, responding to growing policy incentives and building codes favoring renewable HVAC systems. Trane Technologies in particular has expanded its manufacturing footprint and partnerships to address rising demand in both new construction and retrofit markets.
Specialized manufacturers such as ClimateMaster and WaterFurnace International (a subsidiary of NIBE Group) are recognized for their focus on ground loop heat exchanger technology, including vertical, horizontal, and pond/lake loop systems. These companies emphasize product customization and support for large-scale commercial and institutional projects, often collaborating with drilling and installation contractors to deliver turnkey solutions.
On the materials and component side, REHAU is a leading supplier of polymer-based piping systems for geothermal applications, providing pre-insulated and corrosion-resistant pipework that enhances system durability and thermal performance. The company’s global manufacturing and logistics network supports rapid deployment in diverse geographies, reflecting the sector’s increasing internationalization.
Looking ahead, the competitive dynamics are expected to intensify as new entrants—particularly from Asia—seek to capitalize on expanding markets in Europe and North America. Strategic alliances, vertical integration, and digitalization of manufacturing processes are likely to define the next phase of competition, with established players such as Bosch, Viessmann, and Trane Technologies investing in smart manufacturing and lifecycle service offerings to maintain their leadership positions.
Technological Innovations and R&D Trends
The landscape of geothermal heat exchanger manufacturing in 2025 is characterized by a surge in technological innovation and focused research and development (R&D) efforts. As global decarbonization targets intensify, manufacturers are accelerating the adoption of advanced materials, automation, and digitalization to enhance the efficiency, durability, and scalability of geothermal heat exchangers.
A key trend is the integration of novel materials such as advanced polymers, stainless steels, and composite alloys, which offer improved thermal conductivity and corrosion resistance. Companies like Bosch Thermotechnology and Viessmann are investing in R&D to optimize the performance of ground heat exchangers, focusing on reducing installation costs and extending operational lifespans. These efforts are supported by the development of modular and prefabricated systems, which streamline on-site assembly and minimize labor requirements.
Automation and digital manufacturing are also reshaping the sector. Leading manufacturers such as Tranter and Alfa Laval are deploying robotics and advanced quality control systems to ensure precision in the fabrication of heat exchanger components. This not only increases production throughput but also enhances product reliability, a critical factor for geothermal applications where maintenance access is limited.
R&D is increasingly focused on optimizing heat exchanger designs for low-enthalpy geothermal resources, which are more widely available but require highly efficient heat transfer solutions. For example, Danfoss is developing compact plate heat exchangers tailored for shallow geothermal systems, aiming to maximize energy extraction even in less favorable geological conditions. Additionally, the use of digital twins and simulation software is becoming standard practice, enabling manufacturers to model thermal performance and predict long-term behavior under varying operational scenarios.
Collaborative initiatives between industry and research institutions are accelerating innovation. Organizations such as the International Geothermal Association are facilitating knowledge exchange and joint R&D projects, particularly in the areas of sustainable manufacturing and lifecycle analysis. These partnerships are expected to yield breakthroughs in both product design and manufacturing processes over the next few years.
Looking ahead, the outlook for geothermal heat exchanger manufacturing is robust. With policy support and growing demand for renewable heating and cooling, manufacturers are poised to deliver increasingly efficient, cost-effective, and environmentally friendly solutions. The next few years will likely see the commercialization of new materials, further automation, and the widespread adoption of digital tools, positioning the sector at the forefront of the clean energy transition.
Supply Chain, Materials, and Production Advances
The manufacturing landscape for geothermal heat exchangers in 2025 is characterized by a dynamic interplay of supply chain optimization, material innovation, and production technology advances. As global demand for sustainable heating and cooling solutions accelerates, manufacturers are scaling up operations and refining processes to meet both residential and commercial market needs.
A key trend is the diversification and localization of supply chains. In response to recent global disruptions, leading manufacturers such as Bosch Thermotechnology and Viessmann have invested in regional production hubs and supplier partnerships to ensure resilience and reduce lead times. This shift is particularly evident in Europe and North America, where policy incentives and decarbonization targets are driving rapid market growth.
Material selection remains central to performance and cost. Stainless steel and high-density polyethylene (HDPE) continue to dominate due to their corrosion resistance and thermal conductivity. However, 2025 sees increased adoption of advanced polymer composites and hybrid materials, which offer improved durability and lower environmental impact. Companies like REHAU are at the forefront, developing proprietary polymer formulations for ground loop systems that enhance heat transfer efficiency and extend service life.
Production advances are equally significant. Automation and digitalization are streamlining manufacturing lines, with robotic welding, precision extrusion, and real-time quality monitoring becoming standard. NIBE Industrier, a major European player, has integrated Industry 4.0 technologies to boost throughput and maintain stringent quality standards across its heat exchanger product lines. Additive manufacturing (3D printing) is also emerging for prototyping and small-batch production of complex exchanger geometries, reducing material waste and enabling rapid customization.
Sustainability is a growing focus throughout the supply chain. Manufacturers are increasingly sourcing recycled metals and biobased polymers, and implementing closed-loop water and energy systems in their plants. Danfoss has publicly committed to carbon-neutral operations by 2030, with geothermal product lines playing a central role in its strategy.
Looking ahead, the outlook for geothermal heat exchanger manufacturing is robust. Ongoing R&D into nanomaterial coatings and phase-change materials promises further efficiency gains. As governments and utilities expand support for geothermal deployment, the sector is poised for continued investment in both capacity and innovation, ensuring that supply chains and production technologies keep pace with rising global demand.
Regulatory Environment and Industry Standards
The regulatory environment and industry standards for geothermal heat exchanger manufacturing are evolving rapidly as the sector expands in response to global decarbonization goals. In 2025, manufacturers are navigating a landscape shaped by both national and international frameworks, with a strong emphasis on safety, environmental protection, and performance efficiency.
In the United States, geothermal heat exchanger systems are regulated under a combination of federal and state-level codes. The U.S. Department of Energy (DOE) provides technical guidelines and supports the development of voluntary consensus standards, while the U.S. Environmental Protection Agency (EPA) oversees environmental compliance, particularly regarding ground loop installations and fluid management. The International Ground Source Heat Pump Association (IGSHPA) continues to play a pivotal role in setting installation and material standards, with its 2024 update to the “Standards for Ground Source Heat Pump Systems” now widely adopted by manufacturers and installers.
In Europe, the regulatory framework is shaped by the European Union’s Renewable Energy Directive and the Ecodesign Directive, which set minimum energy performance and environmental criteria for heat exchangers and related components. The Euroheat & Power association and the European Heat Pump Association (EHPA) are instrumental in harmonizing standards across member states, promoting certification schemes such as the EHPA Quality Label for geothermal products. Manufacturers like Viessmann and Bosch Thermotechnology are actively engaged in compliance and standardization efforts, ensuring their products meet or exceed these evolving requirements.
Globally, the International Organization for Standardization (ISO) has established key standards such as ISO 11855 for the design and installation of ground source heat pump systems, which are increasingly referenced in national codes. Leading manufacturers, including NIBE Group and Daikin Industries, participate in ISO technical committees to shape future standards and ensure alignment with best practices.
Looking ahead, the regulatory outlook for 2025 and beyond points to stricter requirements for lifecycle environmental impact, refrigerant management, and system efficiency. Digitalization and data reporting are also becoming integral, with regulators requiring more transparent documentation of system performance and environmental compliance. As governments and industry bodies continue to refine standards, manufacturers are investing in advanced materials, automated quality control, and third-party certification to maintain market access and competitiveness.
Regional Analysis: Leading Markets and Emerging Opportunities
In 2025, the global landscape for geothermal heat exchanger manufacturing is characterized by strong regional leadership in established markets and dynamic growth in emerging economies. The sector is closely tied to the expansion of geothermal energy projects, government incentives for renewable heating and cooling, and advances in drilling and materials technology.
Europe remains a leading market, driven by ambitious decarbonization targets and supportive policy frameworks. Countries such as Germany, France, and the Netherlands are investing heavily in district heating networks and ground source heat pump (GSHP) installations, fueling demand for high-efficiency heat exchangers. Major European manufacturers, including Viessmann and Bosch Thermotechnology, are expanding their geothermal product lines and production capacities to meet this demand. The European Heat Pump Association reports that the region’s GSHP market is expected to grow steadily through 2025, with heat exchanger manufacturing closely following this trend.
In North America, the United States leads in both installed geothermal capacity and manufacturing expertise. The U.S. Department of Energy’s continued support for geothermal innovation, including the Enhanced Geothermal Systems (EGS) initiative, is spurring new projects and partnerships. Companies such as Tranter and Modine Manufacturing Company are recognized for their advanced heat exchanger technologies, supplying both utility-scale and residential geothermal systems. Canada is also seeing increased activity, particularly in provinces with supportive energy policies and cold climates that benefit from GSHP adoption.
Asia-Pacific is emerging as a significant growth region, with China, Japan, and South Korea investing in geothermal heating as part of broader clean energy strategies. Chinese manufacturers, including Haier and Gree Electric Appliances, are scaling up production of geothermal heat exchangers for both domestic and export markets. Japan’s focus on energy resilience and decarbonization post-Fukushima has led to increased deployment of geothermal systems, with local firms innovating in compact and corrosion-resistant exchanger designs.
Looking ahead, emerging markets in Eastern Europe, Turkey, and parts of Latin America are expected to offer new opportunities for geothermal heat exchanger manufacturing. These regions are benefiting from international financing, technology transfer, and growing awareness of geothermal’s role in sustainable heating and cooling. As manufacturing capacity expands and supply chains globalize, the sector is poised for robust growth, with regional leaders and agile newcomers shaping the competitive landscape through 2025 and beyond.
Sustainability, Decarbonization, and Environmental Impact
Geothermal heat exchanger manufacturing is increasingly positioned at the intersection of sustainability and decarbonization, as global efforts to reduce greenhouse gas emissions intensify in 2025 and beyond. The sector’s environmental impact is shaped by both the materials and processes used in manufacturing, as well as the operational benefits of geothermal systems over their lifecycle.
A key sustainability advantage of geothermal heat exchangers lies in their ability to enable low-carbon heating and cooling. When deployed, these systems can reduce building emissions by up to 70% compared to conventional fossil-fuel-based HVAC systems, according to industry data. The manufacturing sector is responding to this demand by prioritizing eco-friendly materials, such as high-density polyethylene (HDPE) and stainless steel, which offer durability and recyclability. Leading manufacturers like GEA Group and Danfoss are investing in closed-loop production systems and energy-efficient fabrication processes to further minimize their carbon footprint.
In 2025, the adoption of lifecycle assessment (LCA) methodologies is becoming standard practice among major producers. This approach evaluates the environmental impact of heat exchangers from raw material extraction through manufacturing, installation, operation, and end-of-life recycling. Companies such as Tranter and Alfa Laval are publishing environmental product declarations (EPDs) to provide transparency and support green building certifications, reflecting a broader industry shift toward measurable sustainability metrics.
Material innovation is also a focus area. For example, Viessmann is exploring the use of advanced polymers and corrosion-resistant alloys to extend product lifespan and reduce maintenance, thereby lowering the overall environmental impact. Additionally, manufacturers are increasingly sourcing raw materials from certified sustainable suppliers and implementing waste reduction programs in their facilities.
Looking ahead, the geothermal heat exchanger manufacturing sector is expected to benefit from tightening regulatory frameworks in the EU, North America, and Asia-Pacific, which are mandating lower embodied carbon in building materials and incentivizing renewable heating technologies. The sector’s outlook is further bolstered by the integration of digital manufacturing and quality control systems, which optimize resource use and reduce scrap rates.
Overall, the industry’s commitment to sustainability and decarbonization is not only reducing the environmental impact of geothermal heat exchangers themselves but also supporting the broader transition to net-zero energy systems in the built environment.
Future Outlook: Strategic Opportunities and Challenges Ahead
The future of geothermal heat exchanger manufacturing in 2025 and the coming years is shaped by a convergence of technological innovation, policy support, and evolving market demands. As global decarbonization efforts intensify, geothermal energy is increasingly recognized for its reliability and low emissions, positioning heat exchanger manufacturers at the forefront of the energy transition.
A key strategic opportunity lies in the scaling of advanced heat exchanger designs, such as coaxial and multi-loop systems, which improve efficiency and reduce installation footprints. Leading manufacturers like Bosch Thermotechnology and Viessmann are investing in R&D to enhance the thermal conductivity and corrosion resistance of exchanger materials, including the use of stainless steel alloys and advanced polymers. These innovations are expected to lower lifecycle costs and expand the applicability of geothermal systems in both residential and commercial sectors.
Another significant trend is the integration of digital monitoring and predictive maintenance technologies. Companies such as Tranter are developing smart heat exchangers equipped with sensors and IoT connectivity, enabling real-time performance tracking and early fault detection. This digitalization not only improves system reliability but also provides valuable data for optimizing energy use and maintenance schedules.
On the policy front, governments in North America, Europe, and parts of Asia are introducing incentives and regulatory frameworks to accelerate geothermal adoption. For example, the European Union’s Green Deal and the U.S. Inflation Reduction Act include provisions that support the deployment of ground-source heat pumps and associated infrastructure, directly benefiting heat exchanger manufacturers. Organizations such as the International Geothermal Association are also advocating for harmonized standards, which could streamline manufacturing and certification processes globally.
However, the sector faces challenges. Supply chain disruptions, particularly for specialty metals and polymers, may impact production timelines and costs. Additionally, the need for skilled labor in both manufacturing and installation remains a bottleneck, prompting companies to invest in workforce development and automation. Environmental considerations, such as the recyclability of exchanger materials and the minimization of drilling impacts, are also coming under greater scrutiny.
Looking ahead, the geothermal heat exchanger manufacturing industry is poised for robust growth, driven by technological advancements, supportive policy environments, and rising demand for sustainable heating and cooling solutions. Strategic collaboration between manufacturers, utilities, and policymakers will be essential to overcome challenges and fully realize the sector’s potential in the global energy landscape.
Sources & References
- Viessmann
- Trane Technologies
- Bosch
- Daikin
- ClimateMaster
- NIBE Industrier
- Stiebel Eltron
- Danfoss
- Carrier
- Tranter
- Alfa Laval
- NIBE Industrier
- IGSHPA
- Euroheat & Power
- European Heat Pump Association
- Viessmann
- ISO
- NIBE Group
- Haier
- Gree Electric Appliances
- GEA Group