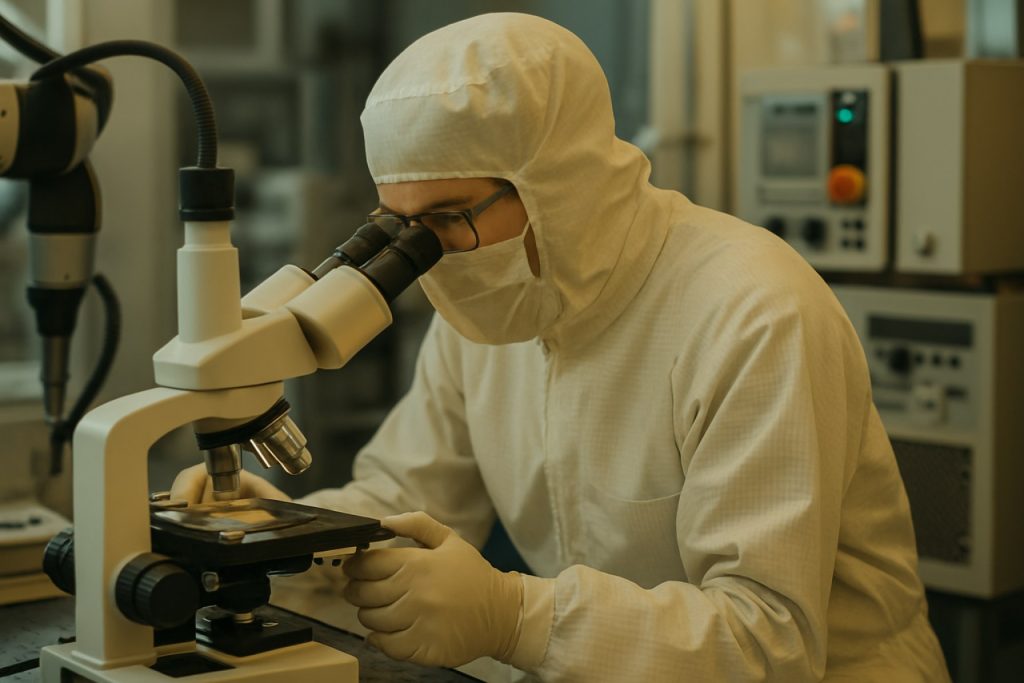
Table of Contents
- Executive Summary: The 2025 Microfabrication Engineering Inflection Point
- Breakthrough Technologies Revolutionizing Framework Microfabrication
- Market Size, Segmentation, and 5-Year Forecasts (2025–2029)
- Key Industry Players & Strategic Alliances
- Supply Chain Innovations and Bottlenecks
- Emerging Applications: From Quantum Devices to Wearables
- Regulatory Landscape and Global Standards (citing ieee.org, asme.org)
- Competitive Landscape: Startups vs. Established Leaders
- Investment Trends and Funding Hotspots
- Future Outlook: Opportunities, Challenges, and Expert Predictions (2025–2029)
- Sources & References
Executive Summary: The 2025 Microfabrication Engineering Inflection Point
The year 2025 marks a pivotal inflection point for framework microfabrication engineering, driven by the convergence of advanced lithography, novel materials, and demand for highly integrated, energy-efficient devices. As the electronics and photonics industries shift toward sub-5 nm nodes and heterogeneous integration, the microfabrication sector is undergoing rapid technological evolution. Companies at the forefront, including ASML, Applied Materials, and Lam Research, are accelerating the commercialization of extreme ultraviolet (EUV) lithography and atomic layer deposition (ALD), enabling feature sizes and pattern fidelity previously unattainable in mass production.
The adoption of EUV lithography has been particularly transformative. In 2025, leading semiconductor manufacturers are ramping high-volume production using EUV, with sub-3 nm logic chips entering mainstream fabrication. TSMC and Samsung Electronics have both announced plans to extend their EUV capabilities, targeting enhanced performance and yield for next-generation processors and system-on-chip (SoC) devices. This leap in resolution is accompanied by a parallel push for advanced patterning and etching tools from suppliers such as Lam Research and Applied Materials, supporting the increasing complexity of device architectures.
Framework microfabrication is also experiencing a surge in hybrid bonding and 3D integration, essential for chiplet-based designs and advanced packaging. Intel’s adoption of hybrid bonding for its Foveros Direct technology, and Amkor Technology’s expansion of advanced packaging services, underscore the industry’s shift toward high-density interconnects and heterogeneous integration. These technologies are pivotal for applications in AI, high-performance computing, and edge devices, where bandwidth and power efficiency are critical performance metrics.
Materials innovation remains a core driver of microfabrication progress. The deployment of new high-k and low-k dielectrics, advanced photoresists, and novel substrate materials is being accelerated by collaborations between chemical suppliers such as DuPont and device manufacturers. These material advancements are essential for mitigating parasitic effects, improving device reliability, and enabling further scaling.
Looking ahead to the next several years, the outlook for framework microfabrication engineering is robust. With sustained investment in process equipment, materials R&D, and factory automation, the sector is poised for continued growth and innovation. Strategic partnerships and standardization efforts led by organizations such as SEMI will further facilitate ecosystem-wide progress, ensuring that microfabrication engineering remains at the core of the global semiconductor value chain as it navigates the post-Moore era.
Breakthrough Technologies Revolutionizing Framework Microfabrication
Framework microfabrication engineering is undergoing a transformative phase in 2025, propelled by several breakthrough technologies that are redefining precision, scalability, and application domains. Central to this evolution is the rapid adoption of advanced additive manufacturing techniques, such as two-photon polymerization and high-resolution micro-stereolithography. These methods enable the creation of complex 3D microstructures with feature sizes well below one micron, supporting innovations in micro-optics, MEMS, and biomedical scaffolds. Companies like Nanoscribe GmbH & Co. KG are at the forefront, providing commercial two-photon lithography systems that achieve unprecedented accuracy and throughput, already being integrated into R&D and prototyping lines worldwide.
In parallel, the semiconductor industry’s push towards sub-5 nm fabrication nodes is influencing framework microfabrication. Extreme ultraviolet (EUV) lithography, championed by firms such as ASML Holding N.V., is now enabling the creation of intricate framework patterns at wafer-scale, with alignment precision critical for advanced logic and memory devices. The continued optimization of EUV source power and mask technology is expected to drive further miniaturization and efficiency through 2025 and beyond.
Material science breakthroughs are also pivotal. The development of novel photoresists, such as hybrid organic-inorganic materials, is enhancing both resolution and mechanical stability of microfabricated frameworks. Leading suppliers like MicroChem Corp. are introducing advanced resist formulations compatible with next-generation lithographic and etching processes, supporting the shift to heterogeneous integration in microelectromechanical systems (MEMS) and sensors.
Another revolutionizing technology is the rise of micro-transfer printing and wafer bonding, which facilitate the heterogeneous integration of dissimilar materials and devices onto a single substrate. This is enabling flexible and stretchable framework architectures for applications in wearable electronics and implantable devices. Industrial players such as ams-OSRAM AG are actively deploying micro-transfer printing to integrate optoelectronic components at the wafer level, opening up new possibilities for miniaturized, multifunctional systems.
Looking ahead, the convergence of artificial intelligence-driven process control and real-time metrology is expected to further enhance the yield and reliability of framework microfabrication. Industry initiatives focus on automating defect detection and adaptive process tuning, leveraging machine learning algorithms to optimize every step from design to fabrication. With these technologies maturing rapidly, the next few years are set to witness even greater leaps in complexity, throughput, and customization of microfabricated frameworks, underpinning advances in computing, healthcare, and photonic applications.
Market Size, Segmentation, and 5-Year Forecasts (2025–2029)
Framework microfabrication engineering, a core enabler for advanced electronics, MEMS, photonics, and biomedical devices, is positioned for continued robust growth from 2025 through 2029. The market encompasses a diverse array of technologies—including lithography, etching, deposition, and packaging—driven by demand for miniaturization, high performance, and integration across industries. Key segments include semiconductor manufacturing, micro-optics, lab-on-chip devices, and microfluidics. Industry leaders are investing in next-generation fabrication tools and process innovation to address emerging requirements in AI hardware, 5G/6G communications, automotive sensors, and medical diagnostics.
In 2025, the global framework microfabrication engineering sector is estimated to be valued in the tens of billions of US dollars, with the semiconductor segment representing the largest share due to sustained investments in advanced logic and memory devices. For instance, the expansion of EUV (extreme ultraviolet) lithography and advanced packaging technologies is accelerating, supported by major suppliers such as ASML Holding N.V. and Taiwan Semiconductor Manufacturing Company Limited. MEMS devices—ranging from inertial sensors to micro-mirrors—are also expanding rapidly, with leading contributions from manufacturers like STMicroelectronics and Robert Bosch GmbH.
Segmentation of the market reflects its technological breadth:
- By Application: semiconductors, MEMS & sensors, microfluidics/biomedical, photonics/optoelectronics, and advanced packaging.
- By Material: silicon, gallium arsenide, polymers, glass, and advanced ceramics.
- By Process: lithography (UV, EUV, nanoimprint), etching (dry, wet, deep reactive ion), thin-film deposition (CVD, PVD, ALD), and bonding/packaging.
- By Region: Asia-Pacific (driven by manufacturing in Taiwan, South Korea, China, and Japan), North America (notably US innovation hubs), and Europe (with strong R&D and niche fabrication capabilities).
From 2025 to 2029, the sector is projected to grow at a compound annual growth rate (CAGR) in the high single to low double digits, propelled by the scaling of heterogeneous integration, adoption of chiplet architectures, and increased demand for compact, high-efficiency systems. Strategic investments by companies such as Intel Corporation, Samsung Electronics Co., Ltd., and Applied Materials, Inc. are set to further expand market capacity and technological capabilities.
Looking ahead, the convergence of AI, quantum computing, and advanced communications will necessitate even more sophisticated microfabrication platforms. As such, the framework microfabrication engineering market is expected to remain a critical and rapidly evolving pillar of the global high-tech landscape through 2029 and beyond.
Key Industry Players & Strategic Alliances
Framework microfabrication engineering, a cornerstone for advanced semiconductor devices, MEMS, and photonic systems, is currently shaped by a select group of global industry leaders and collaborative alliances. As of 2025, these entities are defining the technological and commercial landscape through innovation in process equipment, materials, and foundry services.
Among the most prominent players, ASML Holding stands out for its leadership in photolithography systems, essential for patterning nanometer-scale features in semiconductor frameworks. ASML’s extreme ultraviolet (EUV) lithography machines remain critical to progressing Moore’s Law, enabling finer microfabrication in both logic and memory devices. In parallel, Lam Research and Applied Materials continue to supply advanced etching, deposition, and metrology solutions, supporting rapid scaling and the integration of novel material stacks for next-generation applications.
On the foundry and manufacturing side, TSMC and Samsung Electronics are pushing the boundaries of framework microfabrication at volume. TSMC’s 2nm and gate-all-around (GAA) transistor technologies, slated for high-volume manufacturing in 2025, depend on advances in microfabrication engineering to deliver higher performance and energy efficiency. Similarly, Samsung continues to invest in new process platforms and collaborative R&D through its foundry ecosystem.
For MEMS, sensors, and photonics, STMicroelectronics and ROHM Semiconductor are integrating microfabrication engineering into high-volume production of advanced sensors and optical components. Their efforts are enhanced through strategic partnerships with equipment vendors and research consortia, aiming for rapid prototyping and commercialization.
Strategic alliances and consortia are crucial accelerators. The SEMI industry association plays a central role in standards, roadmaps, and fostering collaborations between toolmakers, fabs, and material suppliers. Additionally, joint development agreements—such as those between leading foundries and equipment suppliers—are addressing challenges in scaling, yield improvement, and the introduction of new materials like 2D semiconductors and advanced dielectrics.
Looking forward, the next few years will likely see increased cross-border collaborations, as well as public-private partnerships, to address supply chain resilience and talent shortages in microfabrication engineering. The continued convergence of electronics, photonics, and MEMS will drive further strategic partnerships, especially as industry players seek to integrate artificial intelligence and quantum technologies at the microfabrication level.
Supply Chain Innovations and Bottlenecks
The landscape of framework microfabrication engineering in 2025 is shaped by rapid innovation and persistent supply chain challenges, as the sector responds to surging global demand for semiconductors, MEMS, and advanced microsystems. As device architectures become more complex and the push for heterogeneous integration accelerates, the supply networks that support microfabrication are undergoing significant transformation.
On the innovation front, leading wafer foundries and equipment manufacturers have intensified efforts to secure and diversify their supply chains. For instance, Taiwan Semiconductor Manufacturing Company (TSMC) and Samsung Electronics are investing in geographically distributed facilities and advanced logistics solutions. This trend is mirrored by suppliers of specialty materials and photolithography systems, such as ASML, which are increasing production capacity and localizing critical components to mitigate regional risks.
Supply chain bottlenecks, however, remain a significant concern. The global shortage of high-purity gases, advanced photoresists, and silicon wafers—exacerbated by geopolitical tensions and export controls—continues to impact microfabrication throughput and lead times. Sumitomo Chemical and Entegris, prominent materials suppliers, report ongoing efforts to ramp up production and develop alternative sourcing strategies. In parallel, equipment lead times for advanced lithography and etching systems, particularly from single-source vendors like ASML and Lam Research, are extending beyond 12-18 months, prompting fabs to revise expansion timelines.
To address these challenges, collaborative initiatives are emerging across the ecosystem. Industry consortia and partnerships between manufacturers and suppliers are facilitating shared forecasting, just-in-time inventory models, and transparent supply-demand mapping. For example, SEMI, the global industry association, is actively promoting standardization and digitalization of supply chain processes to enhance resilience and traceability. Furthermore, growing adoption of smart manufacturing platforms and AI-driven analytics is enabling real-time monitoring of critical inventories and predictive maintenance of fabrication equipment.
Looking ahead into the next few years, the outlook for supply chain robustness in framework microfabrication engineering is cautiously optimistic. While near-term constraints—especially for EUV lithography tools and specialty chemicals—are likely to persist, sustained investment in capacity expansion, regional diversification, and digital supply chain solutions is expected to incrementally alleviate bottlenecks. The sector’s ability to synchronize innovation with risk-aware supply management will be crucial in supporting the next generation of microfabricated devices.
Emerging Applications: From Quantum Devices to Wearables
Framework microfabrication engineering is entering a transformative phase in 2025, driven by accelerating demand for precisely tailored microstructures in sectors such as quantum technologies, advanced sensors, and next-generation wearables. The convergence of nanofabrication, additive manufacturing, and heterogeneous integration methods is enabling the creation of miniaturized frameworks with high functional density and design flexibility.
In quantum device development, microfabrication frameworks are critical for producing superconducting qubits, ion traps, and photonic circuits with the requisite precision and reproducibility. Manufacturers such as IBM and Intel are actively scaling up microfabrication processes to support the transition from laboratory-scale quantum prototypes to manufacturable quantum processors. These efforts include the integration of advanced lithography, atomic-layer deposition, and deep-reactive ion etching to meet the stringent requirements for coherence and control in quantum systems.
The wearables sector is also experiencing significant innovation due to microfabrication advances. Companies like Apple and Samsung Electronics are leveraging wafer-level packaging and flexible substrate patterning to embed more sensors and communication modules within ever-smaller and lighter devices. Recent announcements highlight the use of microfabricated frameworks in biosensing, where miniaturized transducers and microfluidic channels are integrated into textile fibers or skin patches, enabling continuous health monitoring with high sensitivity and reliability.
The field of micro-electro-mechanical systems (MEMS) is benefiting from these engineering approaches, expanding into new applications such as environmental monitoring, autonomous mobility, and industrial automation. STMicroelectronics and Bosch are pushing the boundaries of MEMS fabrication, producing highly integrated sensor arrays and actuators with improved performance at reduced cost and power consumption.
Looking forward, the outlook for framework microfabrication engineering is marked by rapid scaling and diversification. Hybrid approaches that combine traditional silicon processing with emerging materials (including III-V semiconductors and 2D materials) are expected to unlock new device classes, particularly in optoelectronics and quantum photonics. Industry roadmaps suggest that, over the next few years, the adoption of scalable, automated microfabrication platforms will be essential to meet the growing demands of both quantum and wearable technologies, driving further collaboration between device manufacturers and equipment suppliers.
Regulatory Landscape and Global Standards (citing ieee.org, asme.org)
In 2025, the regulatory landscape and global standards governing framework microfabrication engineering are experiencing significant evolution, reflecting the sector’s rapid technological advancements and its expanding influence across diverse industries. Regulatory bodies and standardization organizations are responding to the increased demand for high-precision, reliable, and safe microfabricated components used in sectors such as semiconductors, medical devices, and microelectromechanical systems (MEMS).
A central player in this ecosystem is the IEEE (Institute of Electrical and Electronics Engineers), which continues to develop and update standards critical to microfabrication processes and device interoperability. The IEEE’s standards, such as those addressing wafer-level packaging, microelectronic device reliability, and interface protocols, are being adopted globally to ensure consistency and quality across manufacturing lines. In 2025, ongoing efforts focus on harmonizing these standards internationally to accommodate emerging technologies like flexible electronics and nanostructured materials, which present new fabrication challenges and opportunities.
Similarly, the ASME (American Society of Mechanical Engineers) plays a pivotal role in establishing mechanical and process standards for microfabrication. ASME standards are particularly influential in defining tolerances, materials specifications, and testing methods for microscale components, which are increasingly integrated into critical infrastructure and devices. Recent initiatives include updating standards for the mechanical reliability of MEMS devices, and refining guidelines for additive micro-manufacturing, a growing area as 3D printing technologies scale down to the micro and nano domains.
Both organizations work closely with international partners to foster cross-border alignment, essential for the global supply chains that characterize microfabrication. The push towards harmonization is also driven by regulatory requirements in major markets, including the European Union, United States, and Asia-Pacific, which are tightening controls around quality assurance and device traceability. These trends are highlighted by the continued adoption of ISO/IEC standards, frequently developed in tandem with IEEE and ASME input, to further unify best practices across the industry.
Looking ahead, industry analysts anticipate an acceleration in standard-setting activity as new applications in quantum computing, wearable health devices, and advanced sensors become mainstream. Regulatory frameworks are expected to further emphasize environmental sustainability and lifecycle management in microfabrication, requiring companies to adapt their engineering practices to comply with evolving norms. As such, the interplay between standardization, innovation, and regulation will remain a defining feature of the microfabrication landscape through the remainder of the decade.
Competitive Landscape: Startups vs. Established Leaders
The competitive landscape of framework microfabrication engineering in 2025 is characterized by dynamic interplay between established industry leaders and a rapidly growing cohort of innovative startups. This sector—which encompasses the design and manufacture of highly precise micro-scale structures crucial for semiconductors, MEMS, photonics, and biomedical applications—has seen intensified activity as demand for miniaturized, high-performance components accelerates.
Established leaders such as Taiwan Semiconductor Manufacturing Company (TSMC), Intel Corporation, and ASML Holding maintain dominant positions through their vast capital investments, global foundry ecosystems, and continued advancements in extreme ultraviolet (EUV) lithography and advanced packaging technologies. For instance, TSMC and Intel are investing heavily in sub-3nm process nodes, which require unprecedented precision in microfabrication and the integration of new materials and architectures. ASML remains the primary supplier of EUV lithography tools, which are essential for the next generation of microfabricated frameworks.
In parallel, startups and scale-ups are increasingly carving out niches by focusing on specialized techniques such as two-photon polymerization, additive micro-manufacturing, and novel lithography approaches. Companies like Heidelberg Instruments and Nanoscribe (a BICO Company) are pushing the boundaries of 3D micro- and nano-printing, enabling the fabrication of complex frameworks for applications in micro-optics, medical devices, and integrated photonics. Their agility allows for rapid prototyping and customization, which larger firms often cannot match due to scale and process rigidity.
Collaborative dynamics are also emerging, with established players acquiring or partnering with startups to accelerate innovation and expand technical capabilities. Recent years have seen an uptick in such strategic moves, as leaders seek to integrate disruptive microfabrication methods into their existing platforms. This synergy is vital as supply chain resilience and technology diversification become priorities in response to geopolitical and market pressures.
Looking forward to the next few years, competition is expected to intensify, driven by the proliferation of AI, IoT, and advanced sensing technologies—all of which demand more sophisticated microfabricated frameworks. The continued convergence of materials science, process automation, and digital design toolchains will likely lower entry barriers for startups while challenging incumbents to remain agile. As a result, the sector is poised for robust growth, with both established giants and innovative newcomers playing pivotal roles in shaping its technological trajectory.
Investment Trends and Funding Hotspots
Investment in framework microfabrication engineering is intensifying in 2025, driven by surging demand for miniaturized devices across sectors such as semiconductors, photonics, and advanced medical technologies. Recent funding patterns highlight both robust private equity flows and significant public initiatives aimed at accelerating innovation in micro- and nano-scale fabrication capabilities. Key geographies leading in funding include the United States, Japan, South Korea, and select European nations, each fostering ecosystem synergies between research institutions, foundries, and end-use industries.
In the United States, the CHIPS and Science Act continues to play a pivotal role, channeling upwards of $50 billion in federal incentives into domestic microfabrication infrastructure and R&D through 2025 and beyond. This initiative has sparked a wave of private investment and joint ventures, with companies like Intel Corporation committing tens of billions in new fabrication facilities and research hubs focused on next-generation process nodes and advanced packaging technologies. Similarly, Taiwan Semiconductor Manufacturing Company (TSMC) has expanded its U.S. footprint, aligning investment with emerging demand for advanced microfabrication frameworks.
Asia remains a global powerhouse in microfabrication engineering investment, with Japanese firms such as Tokyo Ohka Kogyo Co., Ltd. and South Korea’s Samsung Electronics scaling R&D budgets and capital projects dedicated to new lithography techniques, EUV (extreme ultraviolet) processes, and 3D integration frameworks. These companies are also increasingly collaborating with local and international startups to foster innovation in microelectromechanical systems (MEMS), microfluidics, and quantum device fabrication.
Europe’s funding landscape is characterized by a mix of public-private partnerships and targeted regional initiatives. For example, the European Union’s “Chips Act” and national investments in countries like Germany and the Netherlands are supporting the expansion of microfabrication foundries and the commercialization of cutting-edge frameworks. Industry leaders such as ASML Holding and Infineon Technologies AG are at the forefront, leveraging both direct investment and collaborative frameworks with universities and applied research centers.
Looking forward, investment trajectories suggest continued acceleration in 2025 and the following years, with a strategic focus on bridging the gap between prototype development and scalable manufacturing. Funding hotspots are expected to concentrate further in regions with robust supply chains, talent pools, and government backing, as stakeholders seek to address both technical complexity and geopolitical supply chain risks in framework microfabrication engineering.
Future Outlook: Opportunities, Challenges, and Expert Predictions (2025–2029)
Framework microfabrication engineering is positioned for substantial evolution between 2025 and 2029, catalyzed by advancements in materials science, process automation, and the continuous miniaturization imperative across multiple industries. As semiconductor nodes approach the sub-2nm regime, the demand for precision microfabrication frameworks—incorporating novel lithography, etching, and deposition techniques—will intensify, particularly in fields such as advanced packaging, MEMS, and quantum computing hardware.
Key players like ASML are investing in next-generation extreme ultraviolet (EUV) and high-NA lithography systems, facilitating unprecedented feature resolution and process throughput. These advances are expected to enable more complex device architectures and tighter integration, supporting the rapid growth of AI, high-performance computing, and edge devices. Similarly, Lam Research and Applied Materials are expanding their microfabrication tool portfolios to address challenges in atomic layer etching and selective deposition, which are critical for fabricating 3D structures and heterogeneous integration frameworks.
In the biomedical sector, companies such as Dolomite Microfluidics and Standard BioTools are advancing microfluidic fabrication, enabling more sophisticated lab-on-chip systems and organ-on-chip models for drug discovery and diagnostics. The convergence of microfabrication with biocompatible materials and additive manufacturing is expected to accelerate device personalization and throughput in clinical and research settings.
Despite these opportunities, the sector faces challenges such as the escalating complexity of process control, the need for defect-free manufacturing at atomic scales, and supply chain vulnerabilities for specialty materials and precision equipment. Environmental sustainability is emerging as a critical concern, prompting initiatives from firms like Intel to reduce energy and chemical usage in fabrication facilities. Furthermore, the workforce gap in precision engineering and process automation must be addressed through targeted training and collaboration between industry and academia.
Industry experts anticipate that by 2029, the integration of AI-driven process monitoring, digital twins, and closed-loop feedback systems will be standard in advanced fabs, drastically improving yield and reliability. Collaborative efforts among leading equipment manufacturers, material suppliers, and end-user industries are forecasted to accelerate the commercialization of microfabricated frameworks for next-generation electronics, photonics, and biomedical devices. The trajectory for framework microfabrication engineering thus points to an era defined by ultra-high precision, sustainability, and cross-disciplinary innovation.
Sources & References
- ASML
- Amkor Technology
- DuPont
- Nanoscribe GmbH & Co. KG
- ASML Holding N.V.
- ams-OSRAM AG
- STMicroelectronics
- Robert Bosch GmbH
- ROHM Semiconductor
- Sumitomo Chemical
- Entegris
- IBM
- Apple
- IEEE (Institute of Electrical and Electronics Engineers)
- ASME (American Society of Mechanical Engineers)
- Heidelberg Instruments
- Nanoscribe
- Tokyo Ohka Kogyo Co., Ltd.
- Infineon Technologies AG
- Dolomite Microfluidics