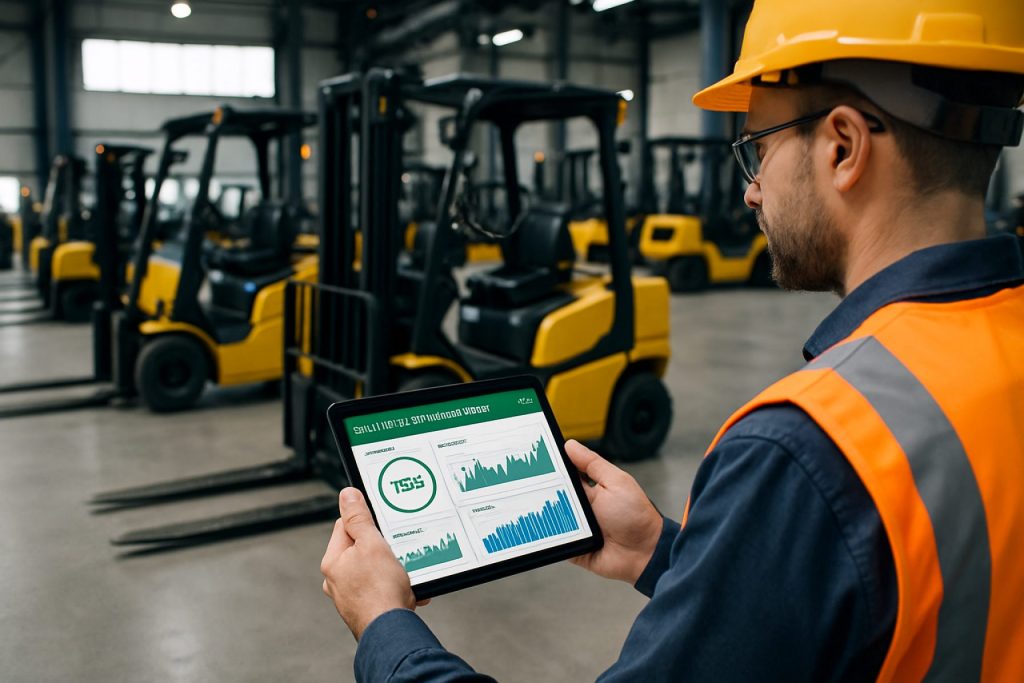
Forklift Fleet Telematics Systems in 2025: How Smart Connectivity and Real-Time Analytics Are Transforming Warehouse Operations. Discover the Next Wave of Productivity and Safety Innovations.
- Executive Summary: Key Trends and Market Outlook (2025–2030)
- Market Size, Growth Forecasts, and Regional Hotspots
- Core Technologies: IoT, Sensors, and Cloud Integration
- Leading Vendors and Industry Initiatives (e.g., Toyota, Hyster-Yale, Crown Equipment)
- Telematics Applications: Asset Tracking, Predictive Maintenance, and Safety
- Data Security, Privacy, and Compliance in Fleet Telematics
- Integration with Warehouse Management and ERP Systems
- ROI, Cost-Benefit Analysis, and Adoption Barriers
- Case Studies: Real-World Deployments and Measured Impact
- Future Outlook: AI, Automation, and the Evolving Role of Telematics (2025–2030)
- Sources & References
Executive Summary: Key Trends and Market Outlook (2025–2030)
The forklift fleet telematics systems market is entering a pivotal phase in 2025, driven by rapid digitalization across logistics, warehousing, and manufacturing sectors. Telematics solutions—integrating GPS, IoT sensors, cloud analytics, and real-time data visualization—are increasingly being adopted to optimize fleet utilization, enhance safety, and reduce operational costs. The convergence of these technologies is transforming traditional forklift operations into data-driven, connected ecosystems.
Key industry players such as Toyota Industries Corporation, Crown Equipment Corporation, and Hyster-Yale Materials Handling are expanding their telematics offerings, embedding advanced connectivity and analytics into their forklift fleets. For example, Toyota’s T-Matics and Crown’s InfoLink platforms provide real-time monitoring of vehicle status, operator behavior, and maintenance needs, enabling predictive maintenance and compliance with safety standards. These systems are increasingly being integrated with warehouse management systems (WMS) and enterprise resource planning (ERP) platforms, reflecting a broader trend toward end-to-end supply chain visibility.
In 2025, regulatory pressures and corporate sustainability goals are accelerating the adoption of telematics. Enhanced safety features—such as automated alerts for unsafe driving, collision detection, and geofencing—are becoming standard, in line with evolving workplace safety regulations in North America, Europe, and Asia-Pacific. Additionally, telematics data is being leveraged to support electrification strategies, as companies transition to electric forklifts and seek to optimize battery usage and charging cycles.
Data security and interoperability are emerging as critical concerns. Leading manufacturers are investing in secure cloud infrastructure and open APIs to ensure seamless integration with third-party software and hardware. Jungheinrich AG and KION Group are notable for their focus on scalable, modular telematics platforms that can be tailored to diverse fleet sizes and operational requirements.
Looking ahead to 2030, the forklift telematics market is expected to see continued double-digit growth, fueled by the expansion of e-commerce, automation, and the Industrial Internet of Things (IIoT). The proliferation of 5G connectivity and AI-driven analytics will further enhance the capabilities of telematics systems, enabling real-time decision-making and autonomous fleet management. As digital transformation accelerates, telematics will become a foundational technology for efficient, safe, and sustainable material handling operations worldwide.
Market Size, Growth Forecasts, and Regional Hotspots
The global market for forklift fleet telematics systems is experiencing robust growth in 2025, driven by the accelerating adoption of digital fleet management solutions across logistics, manufacturing, and warehousing sectors. Telematics systems, which integrate GPS tracking, real-time diagnostics, operator behavior monitoring, and predictive maintenance, are increasingly seen as essential for optimizing fleet efficiency, safety, and regulatory compliance.
Major forklift manufacturers and technology providers are expanding their telematics offerings. Toyota Industries Corporation, a global leader in material handling equipment, continues to enhance its I_Site telematics platform, which is widely deployed in Europe and Asia. KION Group, through its brands such as Linde and STILL, is also investing in digital fleet management solutions, targeting both large-scale logistics providers and smaller operators. Crown Equipment Corporation and Hyster-Yale Materials Handling are similarly expanding their connected fleet offerings, with a focus on North America and Europe.
In terms of market size, industry sources and company statements indicate that the forklift telematics sector is expected to maintain double-digit annual growth rates through the next several years. The proliferation of e-commerce, the need for real-time asset visibility, and stricter safety regulations are key demand drivers. North America and Western Europe remain the largest regional markets, with high telematics penetration rates among large fleet operators. However, Asia-Pacific—particularly China, Japan, and Southeast Asia—is emerging as a hotspot for rapid adoption, fueled by expanding logistics infrastructure and government initiatives supporting digital transformation in manufacturing and warehousing.
Recent years have also seen increased collaboration between forklift OEMs and telematics technology specialists. For example, Jungheinrich AG has integrated advanced telematics and fleet management features into its vehicles, while also offering retrofit solutions for mixed-brand fleets. Meanwhile, companies like Mitsubishi Logisnext are leveraging telematics to support predictive maintenance and remote diagnostics, reducing downtime and total cost of ownership for customers.
Looking ahead, the outlook for forklift fleet telematics systems remains highly positive. The convergence of telematics with IoT, AI-driven analytics, and cloud-based platforms is expected to further accelerate adoption, especially as end-users seek to maximize operational efficiency and sustainability. Regional hotspots such as China, India, and Southeast Asia are projected to see the fastest growth, while established markets in Europe and North America will continue to drive innovation and set industry standards.
Core Technologies: IoT, Sensors, and Cloud Integration
Forklift fleet telematics systems are rapidly evolving in 2025, driven by advances in core technologies such as the Internet of Things (IoT), sensor integration, and cloud-based data management. These systems are transforming how warehouse and logistics operators monitor, manage, and optimize their forklift fleets, with a strong focus on safety, efficiency, and predictive maintenance.
At the heart of modern telematics solutions are IoT-enabled devices that collect real-time data from forklifts, including location, speed, load weight, battery status, and operator behavior. This data is gathered through a network of embedded sensors—such as accelerometers, gyroscopes, proximity sensors, and load cells—installed on each vehicle. The information is then transmitted wirelessly to centralized cloud platforms, where it is aggregated, analyzed, and visualized for fleet managers.
Leading manufacturers and technology providers are investing heavily in these core technologies. Toyota Industries Corporation, a global leader in material handling equipment, has integrated advanced telematics and IoT modules into its forklifts, enabling remote diagnostics, usage tracking, and automated maintenance alerts. Similarly, Crown Equipment Corporation offers its InfoLink system, which leverages cloud connectivity and sensor data to provide actionable insights on fleet utilization, operator performance, and safety compliance.
Another major player, Jungheinrich AG, has developed its own telematics platform, which combines IoT sensors and cloud analytics to support predictive maintenance and energy management. These systems are designed to reduce unplanned downtime and extend the operational life of forklift fleets. Hyster-Yale Materials Handling, Inc. also continues to expand its telematics offerings, focusing on real-time monitoring and integration with warehouse management systems.
The integration of cloud computing is a key enabler, allowing for scalable data storage, advanced analytics, and remote access to fleet information. This is particularly important as fleets grow in size and complexity, and as operators seek to centralize management across multiple sites. Cloud-based platforms also facilitate over-the-air software updates and the deployment of new features without the need for on-site intervention.
Looking ahead, the outlook for forklift fleet telematics systems is marked by increasing adoption of AI-driven analytics, enhanced sensor fusion, and deeper integration with enterprise resource planning (ERP) and warehouse management systems (WMS). As regulatory and customer demands for safety and sustainability intensify, these core technologies will play a pivotal role in shaping the next generation of intelligent, connected forklift fleets.
Leading Vendors and Industry Initiatives (e.g., Toyota, Hyster-Yale, Crown Equipment)
The forklift fleet telematics sector is experiencing rapid evolution in 2025, driven by the integration of advanced IoT, data analytics, and cloud-based management platforms. Leading manufacturers are embedding telematics as a core component of their value proposition, aiming to enhance safety, productivity, and cost efficiency for warehouse and logistics operators.
Toyota Industries Corporation remains a dominant force, leveraging its global reach and technological investments. Its telematics platform, Toyota T-Matics, is designed to provide real-time fleet monitoring, operator management, and predictive maintenance. Toyota’s ongoing initiatives focus on expanding connectivity and interoperability with warehouse management systems, supporting both internal combustion and electric forklifts. The company’s commitment to digital transformation is evident in its continuous updates to telematics features, including enhanced data visualization and automated reporting (Toyota Industries Corporation).
Hyster-Yale Materials Handling, Inc. is another key player, offering the Hyster Tracker and Yale Vision telematics solutions. These systems deliver comprehensive insights into equipment utilization, operator behavior, and maintenance needs. In 2025, Hyster-Yale is emphasizing integration with broader enterprise systems and the use of telematics data to support sustainability goals, such as energy consumption tracking and emissions reduction. The company is also investing in remote diagnostics and over-the-air software updates to minimize downtime and improve fleet responsiveness (Hyster-Yale Materials Handling, Inc.).
Crown Equipment Corporation continues to innovate with its InfoLink fleet management system, which provides cloud-based access to real-time operational data. Crown’s telematics initiatives in 2025 are centered on user-friendly dashboards, mobile accessibility, and advanced analytics for safety compliance and cost control. The company is also expanding its telematics offerings to support mixed-brand fleets, reflecting the industry’s shift toward open, interoperable solutions (Crown Equipment Corporation).
Other notable industry participants include Jungheinrich AG and KION Group, both of which are scaling their telematics platforms to address the growing demand for automation and data-driven decision-making in material handling. These companies are investing in AI-powered analytics, enhanced cybersecurity, and seamless integration with autonomous vehicles and robotics.
Looking ahead, the outlook for forklift fleet telematics is marked by increasing standardization, greater emphasis on cybersecurity, and the proliferation of AI-driven insights. As regulatory and customer demands for safety, sustainability, and efficiency intensify, leading vendors are expected to further expand their telematics ecosystems, fostering deeper collaboration with logistics technology providers and end users.
Telematics Applications: Asset Tracking, Predictive Maintenance, and Safety
Forklift fleet telematics systems are rapidly transforming material handling operations by integrating advanced digital technologies for asset tracking, predictive maintenance, and safety management. As of 2025, the adoption of telematics in forklift fleets is accelerating, driven by the need for greater operational efficiency, regulatory compliance, and cost reduction across logistics, warehousing, and manufacturing sectors.
Asset Tracking is a core application of telematics, enabling real-time visibility of forklift locations, usage patterns, and operational status. Leading manufacturers such as Toyota Material Handling and Crown Equipment Corporation have integrated telematics modules into their fleets, allowing managers to monitor equipment across multiple sites. These systems utilize GPS, RFID, and IoT sensors to provide granular data on asset movement, utilization rates, and unauthorized use, supporting better fleet allocation and reducing idle time.
Predictive Maintenance is another significant benefit, as telematics platforms collect and analyze data from forklift sensors to anticipate component wear and potential failures. Companies like Hyster-Yale Group and Jungheinrich AG offer telematics-enabled maintenance solutions that track engine hours, battery health, and error codes. This data-driven approach enables proactive scheduling of service, minimizing unplanned downtime and extending equipment lifespan. In 2025, the integration of AI and machine learning algorithms is expected to further enhance predictive capabilities, with more manufacturers embedding these features into their telematics offerings.
Safety Management is increasingly prioritized, with telematics systems providing tools for monitoring operator behavior, enforcing safety protocols, and incident reporting. For example, Linde Material Handling and Mitsubishi Logisnext have developed solutions that track speed, impact events, and seatbelt usage, generating alerts and reports for fleet managers. These insights support targeted training, reduce accident rates, and help organizations comply with evolving safety regulations.
Looking ahead, the outlook for forklift fleet telematics is robust. The next few years are expected to see deeper integration with warehouse management systems, increased use of cloud-based analytics, and broader adoption of 5G connectivity for real-time data transmission. As sustainability becomes a key focus, telematics will also play a role in optimizing energy consumption and supporting the transition to electric forklift fleets. Major OEMs and technology providers are investing heavily in R&D to deliver more intelligent, interoperable, and user-friendly telematics platforms, positioning the sector for continued growth and innovation through 2025 and beyond.
Data Security, Privacy, and Compliance in Fleet Telematics
The rapid adoption of forklift fleet telematics systems is transforming material handling operations, but it also brings heightened focus on data security, privacy, and regulatory compliance. As of 2025, telematics platforms—integrated by leading manufacturers and technology providers—collect and transmit vast amounts of operational data, including vehicle location, operator behavior, maintenance status, and even real-time video feeds. This data is critical for optimizing fleet performance, but its sensitivity requires robust safeguards.
Major forklift OEMs such as Toyota Industries Corporation, KION Group (parent of Linde and STILL), and Crown Equipment Corporation have embedded advanced telematics modules in their latest models. These systems often leverage cloud-based platforms, enabling remote diagnostics and analytics. However, the shift to cloud and IoT connectivity increases exposure to cyber threats, including unauthorized access, data breaches, and ransomware attacks.
In response, manufacturers and telematics providers are investing in end-to-end encryption, secure authentication protocols, and regular software updates. For example, Toyota Industries Corporation emphasizes multi-layered security architecture in its T-Matics system, while KION Group integrates compliance features to support GDPR and other regional data protection laws. Crown Equipment Corporation highlights secure data storage and role-based access controls in its InfoLink platform, ensuring only authorized personnel can access sensitive fleet information.
Privacy concerns are also at the forefront, especially as telematics data can include operator identification and behavioral metrics. Companies must balance operational transparency with employee privacy rights, particularly in regions with stringent regulations such as the EU. Compliance with frameworks like the General Data Protection Regulation (GDPR) and, increasingly, the California Consumer Privacy Act (CCPA) in the US, is now a standard requirement for telematics deployments. This includes clear data retention policies, user consent mechanisms, and the ability to anonymize or delete personal data upon request.
Looking ahead, the outlook for 2025 and beyond suggests that data security and compliance will remain central to telematics innovation. Industry bodies such as the MHI are expected to issue updated best practices, while OEMs and technology partners will likely expand cybersecurity partnerships and invest in AI-driven threat detection. As telematics systems become more interconnected with warehouse management and enterprise IT, the sector will need to continuously adapt to evolving cyber risks and regulatory landscapes.
Integration with Warehouse Management and ERP Systems
The integration of forklift fleet telematics systems with Warehouse Management Systems (WMS) and Enterprise Resource Planning (ERP) platforms is accelerating in 2025, driven by the need for real-time data, operational efficiency, and seamless supply chain visibility. Telematics solutions, which collect and transmit data from forklifts—including location, usage, maintenance status, and operator behavior—are increasingly being designed with open APIs and standardized protocols to facilitate interoperability with broader warehouse and enterprise software ecosystems.
Major forklift manufacturers and telematics providers are prioritizing integration capabilities. For example, Toyota Material Handling offers its T-Matics telematics platform, which can be connected to WMS and ERP systems to automate data flows such as asset utilization, maintenance scheduling, and safety compliance. Similarly, Crown Equipment Corporation provides the InfoLink system, enabling real-time forklift data to be shared with warehouse and business management software, supporting data-driven decision-making and process automation.
In 2025, the trend is toward cloud-based telematics platforms, which simplify integration with leading WMS and ERP vendors. Hyster-Yale Group and Jungheinrich AG are both expanding their telematics offerings to support cloud connectivity, allowing for scalable, secure data exchange between forklift fleets and enterprise systems. This enables features such as automated inventory updates, dynamic task allocation, and predictive maintenance alerts to be synchronized across operational platforms.
The adoption of open standards, such as MQTT and RESTful APIs, is further reducing integration complexity. Forklift telematics data can now be ingested directly into WMS and ERP dashboards, providing warehouse managers with unified visibility over assets, workflows, and inventory. This is particularly valuable for large-scale logistics operations and third-party logistics (3PL) providers, who require seamless coordination between material handling equipment and digital supply chain platforms.
Looking ahead, the outlook for 2025 and beyond points to deeper, more automated integration. Forklift telematics systems are expected to play a central role in the evolution of smart warehouses, supporting AI-driven optimization, autonomous vehicle coordination, and real-time compliance monitoring. As more manufacturers and software vendors embrace open integration frameworks, the barriers to connecting forklift fleets with WMS and ERP systems will continue to diminish, enabling higher productivity, safety, and cost efficiency across the logistics sector.
ROI, Cost-Benefit Analysis, and Adoption Barriers
Forklift fleet telematics systems are increasingly recognized as a strategic investment for warehouse and logistics operators, with the potential to deliver measurable returns on investment (ROI) through enhanced safety, productivity, and asset utilization. In 2025, the cost-benefit analysis of these systems is shaped by both technological advancements and evolving operational demands.
The primary ROI drivers for telematics adoption include reduced equipment downtime, lower maintenance costs, improved operator accountability, and compliance with safety regulations. By providing real-time data on vehicle usage, location, and operator behavior, telematics platforms enable predictive maintenance scheduling, which can significantly decrease unplanned repairs and extend equipment lifespan. For example, Toyota Industries Corporation—a global leader in material handling—offers telematics solutions that integrate with their forklifts to monitor performance metrics and maintenance needs, helping customers optimize fleet operations and reduce total cost of ownership.
Another key benefit is the reduction in workplace accidents and associated costs. Telematics systems from companies like Crown Equipment Corporation and Hyster-Yale Materials Handling provide detailed incident reporting and operator access control, which can lead to fewer safety violations and lower insurance premiums. These systems also support compliance with increasingly stringent occupational safety standards, a factor that is expected to drive further adoption through 2025 and beyond.
Despite these advantages, several barriers to widespread adoption remain. Initial capital expenditure for hardware and software, integration with legacy systems, and concerns over data privacy are frequently cited by fleet operators. Smaller businesses, in particular, may struggle to justify upfront costs, even as leading suppliers such as Jungheinrich AG and Linde Material Handling are working to offer scalable, modular telematics solutions tailored to different fleet sizes and budgets.
Looking ahead, the outlook for forklift telematics adoption is positive, with ongoing digitalization in logistics and supply chain sectors acting as a catalyst. As cloud-based analytics and IoT connectivity become more affordable and user-friendly, the cost-benefit equation is expected to tilt further in favor of telematics investment. Industry leaders are also focusing on interoperability and open data standards, which should help lower integration barriers and accelerate ROI realization for a broader range of operators through 2025 and the following years.
Case Studies: Real-World Deployments and Measured Impact
Forklift fleet telematics systems have seen significant real-world adoption across logistics, manufacturing, and retail sectors, with measurable impacts on safety, efficiency, and cost control. As of 2025, several leading companies have publicized case studies and deployment outcomes, highlighting the transformative role of telematics in material handling operations.
One prominent example is the deployment of the Toyota Material Handling T-Matics system at large distribution centers. Toyota’s telematics platform enables real-time monitoring of forklift usage, operator behavior, and maintenance needs. In documented deployments, customers have reported up to 30% reductions in equipment downtime and significant improvements in operator accountability, leading to fewer safety incidents and lower repair costs. The system’s integration with warehouse management software has also enabled data-driven optimization of fleet size and utilization.
Similarly, Crown Equipment Corporation has showcased the impact of its InfoLink telematics solution in multi-site logistics operations. Crown’s case studies detail how InfoLink provides actionable insights into operator performance, battery management, and asset utilization. For example, a major retail client reported a 15% increase in productivity and a 20% reduction in energy consumption after implementing InfoLink across its forklift fleet. The system’s ability to track impacts and enforce pre-shift safety checks has also contributed to a measurable decline in workplace accidents.
Another notable deployment involves Hyster-Yale Group, whose Hyster Tracker and Yale Vision telematics platforms have been adopted by manufacturing and warehousing clients seeking to standardize safety protocols and reduce total cost of ownership. Hyster-Yale’s published results indicate that clients have achieved up to 25% reductions in maintenance expenses and extended equipment lifespans by leveraging predictive maintenance alerts and automated service scheduling.
Looking ahead, the outlook for forklift fleet telematics is robust. Industry leaders are investing in advanced analytics, AI-driven predictive maintenance, and seamless integration with broader supply chain management systems. The next few years are expected to see wider adoption of cloud-based telematics, real-time location tracking, and enhanced operator training modules, further amplifying the measurable benefits already demonstrated in these case studies. As regulatory and customer demands for safety and sustainability intensify, telematics systems are poised to become standard across fleets worldwide.
Future Outlook: AI, Automation, and the Evolving Role of Telematics (2025–2030)
The period from 2025 through 2030 is poised to be transformative for forklift fleet telematics systems, as artificial intelligence (AI), automation, and advanced connectivity reshape the landscape of material handling. Telematics—already a critical tool for monitoring forklift usage, safety, and maintenance—will increasingly serve as the backbone for more autonomous and data-driven warehouse operations.
Leading manufacturers such as Toyota Industries Corporation, Crown Equipment Corporation, and Hyster-Yale Materials Handling are investing heavily in telematics platforms that integrate AI-powered analytics. These systems are expected to move beyond basic tracking and reporting, enabling predictive maintenance, real-time safety interventions, and dynamic optimization of fleet deployment. For example, AI algorithms can analyze sensor data to predict component failures before they occur, reducing unplanned downtime and extending equipment life.
Automation is also accelerating, with telematics systems acting as the digital nervous system for fleets that include both human-operated and autonomous forklifts. Companies like Jungheinrich AG and KION Group are developing solutions where telematics platforms coordinate mixed fleets, optimize traffic flow, and ensure safety compliance in real time. The integration of telematics with warehouse management systems (WMS) and enterprise resource planning (ERP) platforms is expected to become standard, enabling seamless data exchange and holistic operational oversight.
The role of telematics in safety management is also evolving. Advanced driver assistance features, such as collision avoidance and geofencing, are being enhanced by AI to provide context-aware alerts and automated interventions. Toyota Industries Corporation and Crown Equipment Corporation are both piloting systems that use machine learning to identify risky behaviors and recommend targeted training, further reducing accident rates and insurance costs.
Looking ahead, the proliferation of 5G and edge computing will enable even richer data streams and faster decision-making at the fleet level. As regulatory bodies and industry standards evolve, telematics data will play a growing role in compliance reporting and sustainability initiatives, such as tracking energy consumption and carbon emissions. By 2030, forklift fleet telematics systems are expected to be deeply embedded in the digital fabric of supply chains, driving efficiency, safety, and adaptability in increasingly automated environments.
Sources & References
- Toyota Industries Corporation
- Crown Equipment Corporation
- Hyster-Yale Materials Handling
- KION Group
- Toyota Material Handling
- Hyster-Yale Group
- Linde Material Handling
- MHI
- Toyota Material Handling
- Crown Equipment Corporation
- Hyster-Yale Group