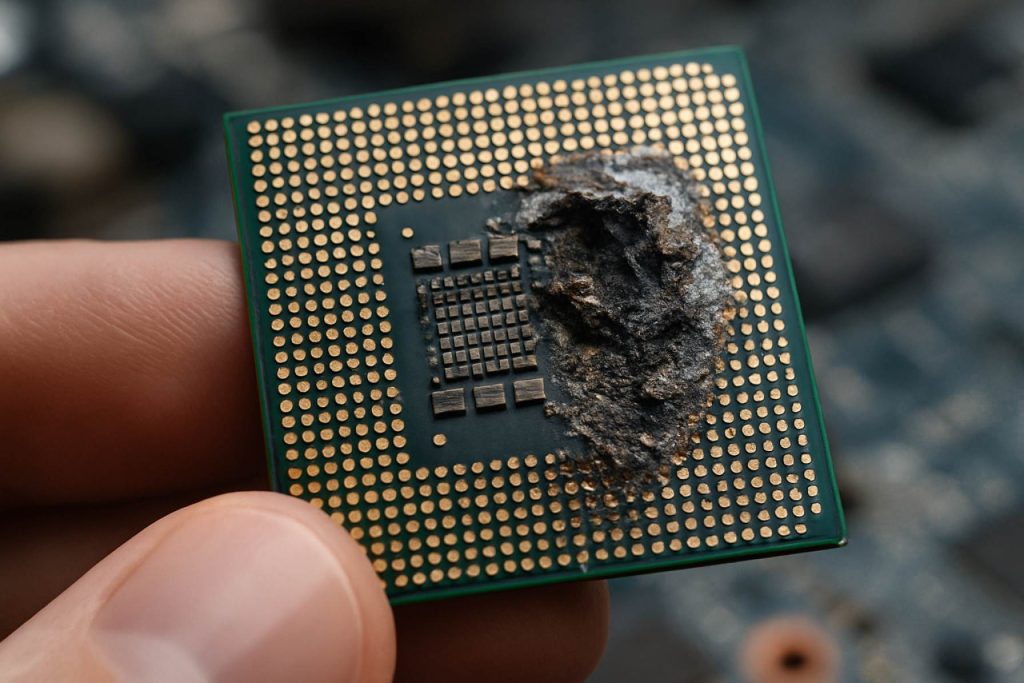
Table of Contents
- Executive Summary: Key Trends and Market Forecasts Through 2030
- What’s Causing Semiconductor Failures? A Deep Dive Into Defect Origins
- Latest Advances in Failure Analysis Technology: 2025 Landscape
- Competitive Analysis: Leading Companies and Strategic Partnerships
- Materials and Manufacturing: Where Defects Begin
- Emerging Failure Modes in Next-Gen Chips (AI, Automotive, IoT)
- Case Studies: Real-World Failures and Diagnostic Solutions
- Regulatory, Standards, and Industry Initiatives (IEEE, JEDEC, SEMI)
- Market Size, Demand Drivers, and Revenue Projections (2025–2030)
- Future Outlook: Innovations, Investments, and Industry Roadmap
- Sources & References
Executive Summary: Key Trends and Market Forecasts Through 2030
The semiconductor industry is entering a critical phase in 2025, marked by increasing complexity of integrated circuits and mounting pressures on supply chain reliability. As a result, defective semiconductor failure analysis (FA) has become a strategic priority for manufacturers and their downstream partners. In 2025, the industry continues to grapple with yield losses driven by advanced process nodes (5nm, 3nm), heterogeneous integration, and the proliferation of automotive, AI, and IoT applications that demand ultra-high reliability.
Key trends in defective semiconductor failure analysis include the rapid adoption of advanced diagnostic technologies such as machine learning-driven defect classification, high-resolution transmission electron microscopy (TEM), and non-destructive techniques like X-ray computed tomography. Major equipment vendors and foundries are investing heavily in both in-line and end-of-line FA tools to catch latent defects earlier in the process flow. Companies such as Applied Materials and Lam Research are expanding their portfolios of metrology and inspection solutions tailored for next-generation device architectures.
Data from industry leaders indicates a growing demand for FA services that address both process-induced and field-returned failures. For example, Intel and TSMC have both publicly highlighted ongoing investments in failure analysis laboratories and the integration of AI-driven analytics to accelerate root cause identification. Additionally, the automotive sector’s push for functional safety (ISO 26262) is elevating requirements for traceability and defect screening, as evidenced by initiatives from Infineon Technologies and NXP Semiconductors.
Looking toward 2030, forecasts suggest that the defective semiconductor failure analysis market will expand steadily, driven by three factors: the continual reduction of process geometries, broader adoption of chiplets and 3D packaging, and tightening quality regulations across automotive, aerospace, and medical segments. Industry stakeholders anticipate double-digit growth rates in advanced FA equipment spending, with new capabilities for atomic-level defect localization and big-data-enabled predictive maintenance. These developments will be essential in supporting the robust growth of the semiconductor market as projected by organizations such as Semiconductor Industry Association.
In summary, as the semiconductor landscape evolves rapidly through 2030, defective semiconductor failure analysis will play a pivotal role in safeguarding quality, reducing time-to-market, and underpinning the reliability expectations of next-generation electronic systems.
What’s Causing Semiconductor Failures? A Deep Dive Into Defect Origins
As semiconductor technology advances towards smaller nodes, higher complexity, and greater integration, the origins of defects leading to device failure have become an increasingly critical focus area for the industry in 2025 and beyond. The main causes of semiconductor failures can be traced to three broad categories: material defects, process-induced flaws, and operational stress.
Material defects remain a key challenge, especially as fabs transition to advanced nodes such as 3nm and 2nm. Microscopic contaminants, crystal dislocations, and doping inconsistencies can result in latent device failures that may not surface until post-manufacture testing or even field operation. For example, companies like TSMC and Samsung Electronics have highlighted the difficulties of controlling particle contamination and maintaining uniformity in epitaxial layers as process geometries shrink further. Even a single atomic-scale particle can cause significant performance degradation or catastrophic failure at these scales.
Process-induced flaws are also a growing concern. As the number of process steps increases with advanced device architectures—such as gate-all-around (GAA) FETs and 3D stacking—there are more opportunities for misalignments, improper etching, and layer delamination. Intel and Micron Technology have reported that yield losses from process-induced defects such as via voids and metal migration are rising, even as automated inspection and metrology tools become more sophisticated.
Operational stress, especially in high-performance and automotive applications, is causing new failure modes to emerge. Electromigration, time-dependent dielectric breakdown (TDDB), and thermal cycling are increasingly relevant as chips are pushed to higher frequencies and power densities. NXP Semiconductors and Infineon Technologies have emphasized the importance of reliability testing under harsh conditions to uncover these latent defects before deployment.
Looking ahead, the industry is responding with enhanced defect detection and failure analysis approaches. Electron microscopy, machine learning-based pattern recognition, and real-time inline monitoring are being rapidly adopted to catch potential issues earlier and with greater accuracy. Furthermore, collaboration between foundries, equipment makers, and end-users is intensifying to share data and best practices for root cause analysis, as seen in initiatives led by organizations like Semiconductor Industry Association.
As semiconductor devices become ever more integral to critical infrastructure and safety applications, the imperative to understand, detect, and eliminate defect origins is expected to drive both technological innovation and cross-industry collaboration throughout 2025 and the coming years.
Latest Advances in Failure Analysis Technology: 2025 Landscape
The landscape of defective semiconductor failure analysis is experiencing significant transformation in 2025, driven by the escalating complexity of integrated circuits and the ever-shrinking geometries of advanced nodes. As devices approach the sub-3nm scale and incorporate heterogeneous integration, advanced failure analysis (FA) technologies have become critical to ensure product reliability and yield.
One of the most notable advances is the wider adoption of AI-assisted defect classification and root cause analysis. Major semiconductor manufacturers are leveraging machine learning algorithms to automate defect detection using high-resolution imaging data, substantially reducing analysis time and improving accuracy. For example, Taiwan Semiconductor Manufacturing Company (TSMC) has integrated AI-driven analytics into its manufacturing lines, enabling real-time feedback and adaptive process control. This integration is essential for identifying subtle failure modes in advanced logic and memory devices.
Another technological leap is witnessed in the area of non-destructive testing. 3D X-ray microscopy and advanced electron microscopy (such as TEM and STEM) are now routinely used for sub-nanometer resolution imaging. Intel Corporation and Samsung Electronics have both reported the deployment of such tools, which allow for detailed visualization of buried defects and interconnect failures without damaging the specimen. Techniques like atom probe tomography are also gaining traction for their ability to provide atomic-scale chemical analysis, essential for advanced material systems.
Defective semiconductor analysis is further enhanced by the increasing deployment of in-line failure analysis tools. Semiconductor equipment suppliers such as Lam Research are developing integrated metrology and inspection systems that enable early-stage defect detection. These tools are pivotal in high-volume manufacturing environments, where rapid feedback loops are necessary to maintain yield at leading-edge nodes.
Looking ahead, the industry is poised to adopt even more sophisticated techniques, such as quantum-based sensing and advanced AI models trained on massive multimodal datasets, to tackle the challenges posed by 3D-ICs, chiplets, and novel materials. The outlook for the next several years suggests a convergence of data-driven analysis, high-resolution imaging, and in-situ diagnostics, underpinning the reliable scaling of semiconductor technologies. Ongoing collaborations between device manufacturers and equipment suppliers will be crucial for translating these innovations into robust solutions, ensuring the continued progress of the semiconductor sector.
Competitive Analysis: Leading Companies and Strategic Partnerships
The competitive landscape for defective semiconductor failure analysis is evolving rapidly as major players in semiconductor manufacturing and testing intensify their investments in advanced analytical tools, automation, and collaborative partnerships. In 2025, industry leaders such as Intel Corporation, Taiwan Semiconductor Manufacturing Company (TSMC), and Samsung Electronics continue to spearhead innovations in failure analysis methodologies, leveraging their extensive in-house R&D capabilities and global supply chains.
These companies are integrating artificial intelligence (AI) and machine learning (ML) algorithms into their analytical workflows to enhance detection accuracy and reduce turnaround times. For instance, Intel Corporation has publicly highlighted the use of AI-driven defect detection to expedite root cause analysis and improve wafer yield, which is crucial given the increasing complexity of sub-5nm process nodes. Similarly, TSMC is investing in proprietary inspection systems and predictive analytics to proactively identify potential failure points throughout the semiconductor lifecycle.
Equipment suppliers such as KLA Corporation and ASML Holding are also key contributors, offering advanced inspection and metrology solutions that enable more granular failure localization. KLA Corporation has introduced next-generation electron microscopy and defect review platforms, which have become indispensable in root cause analysis for leading fabs. Meanwhile, ASML Holding’s deep ultraviolet (DUV) and extreme ultraviolet (EUV) lithography systems are complemented by their defect inspection modules, supporting early detection and process optimization.
Strategic partnerships between foundries, equipment manufacturers, and design houses are becoming increasingly prominent. An example is the collaboration between TSMC and Synopsys to develop design-for-test (DFT) solutions that streamline failure analysis during integrated circuit (IC) development. Joint ventures and knowledge-sharing alliances are expected to accelerate in the coming years as companies address challenges posed by heterogeneous integration, advanced packaging, and increasing device reliability demands.
Looking ahead, the global shift toward automotive, AI, and IoT applications will drive further sophistication in failure analysis tools and methodologies. The leading companies are expected to deepen their investments in automation, cross-company data sharing, and ecosystem partnerships to maintain competitive advantage and support the delivery of ever-more reliable semiconductor products.
Materials and Manufacturing: Where Defects Begin
The process of semiconductor manufacturing is highly intricate, involving hundreds of steps from raw material purification to wafer fabrication and packaging. In 2025, as device geometries continue to shrink below 5nm, the industry faces increased susceptibility to defects that can cause catastrophic or latent failures in chips. Defective semiconductor failure analysis starts with understanding the genesis of these defects at the materials and manufacturing stages.
Key contributors to semiconductor defects include contamination, crystalline imperfections, and process-induced damage. The transition to extreme ultraviolet (EUV) lithography has reduced some patterning-related defects, but introduced new sources of particle contamination and photoresist-related issues. Materials quality, particularly in silicon and compound semiconductors such as SiC and GaN, is a persistent concern. Leading wafer suppliers like SUMCO and Shin-Etsu Chemical have invested in ultra-pure crystal growth and advanced inspection systems, yet even at defect densities of less than 0.1/cm², critical failures can occur in advanced nodes.
In manufacturing, process control remains essential for defect mitigation. Advanced foundries such as TSMC and Samsung Electronics deploy in-line inspection and metrology tools at nearly every step. These tools, provided by companies like KLA Corporation and ASM International, utilize electron microscopy and spectroscopy to detect sub-micron defects and material anomalies in real time. The data-driven approach enables rapid feedback and minimizes the propagation of defective materials through the process.
Despite these advances, new challenges are emerging. Heterogeneous integration, 3D packaging, and chiplet architectures introduce new interfaces and materials, each susceptible to unique defect mechanisms such as delamination, void formation, and interfacial contamination. The rise of wide bandgap materials for power and RF devices brings additional risks of dislocations and stacking faults, impacting device reliability and yield. Manufacturers like onsemi and Infineon Technologies report ongoing investments in defect characterization and screening, especially for automotive and industrial applications where failure rates must be exceedingly low.
Looking ahead, AI-driven inspection, in-situ analytics, and digital twins are being adopted to preemptively identify and classify defects before they impact device performance. The next few years will see closer collaboration across the supply chain to address defect sources at the atomic and molecular level, ensuring that the foundation for advanced semiconductor devices is as robust and defect-free as possible.
Emerging Failure Modes in Next-Gen Chips (AI, Automotive, IoT)
The rapid evolution of next-generation semiconductor devices, particularly those powering artificial intelligence (AI), automotive, and Internet of Things (IoT) applications, is introducing a new spectrum of failure modes that challenge traditional approaches to defective semiconductor failure analysis. In 2025 and the coming years, the convergence of advanced process nodes, 3D architectures, and heterogeneous integration is raising both the complexity and criticality of identifying, characterizing, and mitigating defects.
AI accelerators and edge processors, for instance, are increasingly manufactured using sub-5nm process technologies and advanced packaging techniques such as chiplet architectures. These trends heighten susceptibility to previously rare failure mechanisms, including interconnect electromigration, time-dependent dielectric breakdown (TDDB), and early-life failures due to process variations. TSMC and Intel have reported that as die sizes shrink and transistor counts soar, even minor process anomalies or contamination events can result in systemic failures, cascading across vast arrays of logic or memory elements.
In the automotive sector, the proliferation of advanced driver-assistance systems (ADAS) and electric vehicle (EV) control modules has intensified the need for zero-defect silicon. Here, latent defects such as microcracks in through-silicon vias (TSVs), package delamination, and soft errors induced by cosmic rays are increasingly scrutinized. Automotive suppliers including Infineon Technologies and NXP Semiconductors are deploying new in-line screening and reliability monitoring strategies to preempt such failures, as the cost of in-field malfunctions is substantial both in economic and safety terms.
IoT devices, designed for ubiquitous deployment and prolonged lifetimes, face unique reliability hurdles. Miniaturized sensors and microcontrollers, often exposed to harsh and variable environments, are vulnerable to corrosion, electrostatic discharge (ESD), and early wear-out. Manufacturers such as STMicroelectronics are advancing failure analysis techniques to address these issues, including high-resolution electron microscopy and real-time environmental stress screening.
Looking forward, the defect landscape is expected to further evolve as semiconductor manufacturing incorporates new materials (e.g., gallium nitride, silicon carbide), and as chiplet-based systems become mainstream. The industry is responding with investments in AI-driven analytics for rapid defect pattern recognition and predictive failure modeling. Industry consortia, such as SEMI, are establishing standards for failure data exchange and root cause traceability, aiming to accelerate learning cycles and bolster yields in next-gen chip production.
Case Studies: Real-World Failures and Diagnostic Solutions
In the continuing evolution of semiconductor manufacturing and deployment, real-world case studies provide invaluable insights into both the nature of defects and the effectiveness of emerging diagnostic solutions. As the industry enters 2025, the pressure to maintain reliability in increasingly miniaturized and complex devices has brought attention to several high-profile failure incidents and their subsequent analysis.
A major event in recent years involved a series of field failures in automotive microcontrollers supplied for advanced driver-assistance systems. These failures, initially sporadic and difficult to reproduce, were ultimately traced to electrostatic discharge (ESD) vulnerabilities introduced during a process node transition. Engineers at Infineon Technologies AG collaborated with automotive OEMs to apply advanced failure analysis tools, such as laser voltage probing and time-resolved emission microscopy, to isolate the defective gate oxide regions. The resulting process improvements and design-for-test features have since been adopted in their next-generation automotive ICs.
Another case surfaced within the consumer electronics sector, where a batch of leading-edge mobile SoCs exhibited intermittent functional failures after packaging. A joint investigation by Taiwan Semiconductor Manufacturing Company and its customer revealed that the root cause was a subtle delamination at the die-attach interface, exacerbated by thermal cycling during device operation. Using inline scanning acoustic microscopy and focused ion beam cross-sectioning, the teams were able to refine both packaging materials and process controls to prevent recurrence.
In memory manufacturing, Samsung Electronics publicly addressed a yield drop in its latest V-NAND flash products in 2024, citing the discovery of metal contamination in one of its fab lines. Through a combination of real-time in-line particle monitoring and transmission electron microscopy, their engineers identified the contamination source and implemented rigorous process containment. The case highlighted the necessity of continuous improvement in contamination control as device geometries shrink.
Looking forward, the proliferation of AI edge devices and automotive electronics is expected to amplify the importance of rapid and precise semiconductor failure analysis. The industry is adopting increasingly sophisticated diagnostic platforms, including machine learning-assisted fault localization and atomic-scale imaging. Companies such as Intel Corporation and Micron Technology are investing heavily in these technologies to support both product reliability and accelerated time-to-market. As defect modes become more elusive at advanced process nodes, collaboration across the supply chain will be vital for timely diagnosis and corrective action through 2025 and beyond.
Regulatory, Standards, and Industry Initiatives (IEEE, JEDEC, SEMI)
Defective semiconductor failure analysis is increasingly shaped by evolving regulatory frameworks, standards development, and sector-wide initiatives, particularly from organizations such as IEEE, JEDEC, and SEMI. As the global demand for advanced and reliable chips intensifies in 2025, these bodies are focusing on harmonizing methodologies and requirements to address both the technical challenges and the critical need for trustworthy electronics in applications ranging from automotive to data centers.
A significant regulatory trend is the tightening of reliability and traceability requirements for semiconductor components, particularly in safety-critical sectors. New and updated standards from JEDEC (such as JESD47 for stress-test driven qualification) are being widely referenced for both qualification and failure analysis, ensuring consistency in how defects are detected, characterized, and reported. Meanwhile, IEEE continues to advance its suite of standards for test methodologies and reliability, such as those in the 1687 series (IJTAG), which streamline access to embedded instrumentation for in-system failure diagnosis.
Industry initiatives are also addressing the increasing complexity of failure analysis at advanced process nodes (5nm and below), where defects can be minuscule and failure mechanisms more subtle. SEMI is facilitating cross-company working groups and publishing best practices to standardize analytical techniques and data sharing, notably through its SEMI Standards program. These activities are critical as the industry contends with supply chain vulnerabilities and counterfeit risks—requiring more rigorous defect detection and root cause analysis.
Recent data suggests a rise in the adoption of collaborative benchmarking programs, where companies submit devices for blind failure analysis to ensure conformance and inter-laboratory reliability. Such programs, coordinated by industry groups and standards bodies, are expected to expand over the next few years as traceability and reproducibility become central to both compliance and competitive differentiation.
Looking ahead to 2025 and beyond, regulatory and standards activities are likely to intensify. The European Union and the United States are both considering additional mandates on semiconductor quality documentation, which would further embed JEDEC, IEEE, and SEMI standards into procurement and audit processes. With geopolitical and cybersecurity concerns also influencing regulatory priorities, industry-wide initiatives will continue to drive the evolution of failure analysis protocols—emphasizing automation, AI-assisted diagnostics, and secure data handling.
Market Size, Demand Drivers, and Revenue Projections (2025–2030)
The market for defective semiconductor failure analysis is poised for robust growth between 2025 and 2030, reflecting the increasing complexity of integrated circuits and the expanding deployment of semiconductors across high-reliability sectors such as automotive, aerospace, telecommunications, and consumer electronics. As device geometries shrink and chip designs integrate more functionality, the risk and impact of latent defects—such as electromigration, dielectric breakdown, and contamination—rise, directly driving demand for advanced failure analysis services and equipment.
In 2025, industry data indicate that the global semiconductor market is expected to surpass $600 billion in annual sales, with continued double-digit growth rates anticipated through the end of the decade. This expansion, led by advancements in artificial intelligence, automotive electrification, IoT, and 5G technologies, escalates the volume and complexity of devices requiring rigorous failure analysis to maintain yield and reliability standards (TSMC, Samsung Electronics). As a result, major semiconductor manufacturers and foundries are investing heavily in state-of-the-art analytical tools, including transmission electron microscopy (TEM), focused ion beam (FIB) systems, time-domain reflectometry, and advanced X-ray inspection platforms.
Emerging demand drivers include the proliferation of advanced packaging technologies (such as 2.5D/3D integration and chiplet architectures), which introduce new failure modes at the interconnect and substrate levels. Moreover, safety-critical applications—particularly in electric vehicles and autonomous systems—necessitate zero-defect strategies, prompting automotive OEMs and Tier 1 suppliers to tighten quality requirements and partner closely with analytical service providers (Infineon Technologies, STMicroelectronics). The migration to sub-5nm process nodes and the adoption of wide-bandgap materials like SiC and GaN further necessitate sophisticated failure analysis capabilities to detect subtle process-induced and operational defects.
Revenue projections through 2030 suggest a compound annual growth rate (CAGR) for the semiconductor failure analysis sector in the high single to low double digits, outpacing overall semiconductor equipment growth as quality assurance becomes ever more central to competitive differentiation. Leading suppliers of analytical instrumentation, such as Thermo Fisher Scientific and JEOL, are expanding their product lines to meet rising demand for higher-resolution, automated, and AI-assisted analysis platforms.
Looking ahead, the market outlook is buoyed by increasing regulatory scrutiny, the growing prevalence of counterfeit components, and the need for traceability in global supply chains. Together, these factors are anticipated to sustain elevated demand for defective semiconductor failure analysis services and solutions well into the next decade.
Future Outlook: Innovations, Investments, and Industry Roadmap
The future outlook for defective semiconductor failure analysis is shaped by rapid advances in device complexity, the adoption of new materials, and the growing importance of reliability in applications from AI computing to automotive safety. As the semiconductor industry moves toward nodes below 3nm, failure analysis (FA) methodologies must evolve to address the shrinking scale and novel failure mechanisms. In 2025 and the upcoming years, several innovations, investment trends, and industry initiatives are set to redefine the landscape of FA.
One major innovation is the increased deployment of advanced imaging and characterization tools capable of resolving features at the atomic scale. Transmission Electron Microscopy (TEM) and Atom Probe Tomography (APT) are becoming integral for identifying sub-nanometer defects and process-induced anomalies. Major equipment suppliers like Thermo Fisher Scientific are investing significantly in enhancing electron microscopy platforms with artificial intelligence-driven analytics, enabling faster and more precise defect localization. Meanwhile, Hitachi High-Tech Corporation is developing new Scanning Electron Microscope (SEM) and Focused Ion Beam (FIB) systems tailored for advanced packaging and 3D integration analysis.
Another critical trend is the integration of big data analytics and machine learning into FA workflows. By aggregating data from test, inspection, and in-line metrology, semiconductor manufacturers can identify systemic defect patterns and predict potential failure modes. TSMC and Intel Corporation have publicly discussed investments in smart factories and digital twins to accelerate root cause analysis and reduce downtime. These approaches are expected to become increasingly widespread across the industry by 2027, driven by the need for high-yield manufacturing and faster time-to-market for complex chips.
The ongoing transition to heterogeneous integration and advanced packaging, such as chiplets and 2.5D/3D ICs, presents new challenges for FA. Industry consortia like SEMI are coordinating efforts to define new reliability standards and FA methodologies suitable for these architectures. Collaborative roadmaps, such as those facilitated by the International Roadmap for Devices and Systems (IRDS), are emphasizing cross-disciplinary approaches that combine materials science, electrical engineering, and data science.
Looking ahead, investments in automated FA and remote analysis platforms are expected to rise, enabling faster turnarounds and reducing the need for physical sample transfer. The convergence of advanced instrumentation, AI-driven analytics, and collaborative industry standards will be pivotal in ensuring robust defect detection and failure prediction, keeping pace with the relentless innovation cycle of the semiconductor sector over the next few years.