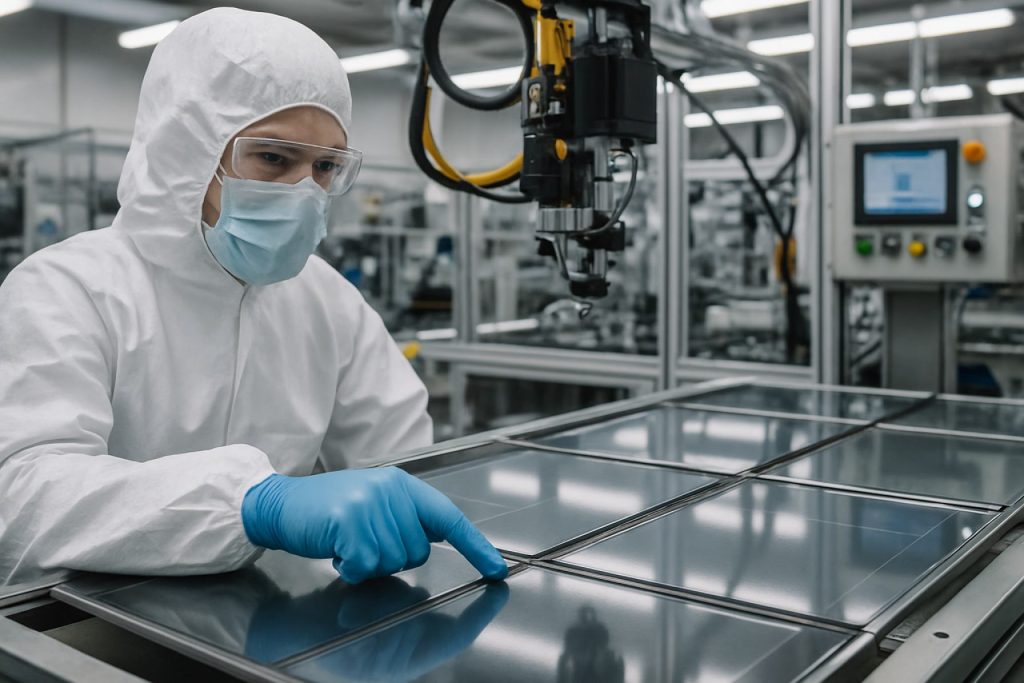
Capacitive Touch Panel Manufacturing in 2025: Navigating Explosive Growth, Technological Breakthroughs, and the Evolving Global Supply Chain. Discover how innovation and market forces are reshaping the industry’s future.
- Executive Summary: Key Trends and 2025 Outlook
- Market Size, Segmentation, and 8% CAGR Forecast (2025–2030)
- Technological Innovations: Materials, Design, and Performance
- Major Players and Competitive Landscape (e.g., tpk.com, synaptics.com, 3m.com)
- Supply Chain Dynamics and Regional Manufacturing Hubs
- Application Expansion: Automotive, Consumer Electronics, and Industrial Uses
- Sustainability Initiatives and Environmental Impact
- Challenges: Raw Material Sourcing, Cost Pressures, and IP Issues
- Emerging Opportunities: Flexible, Transparent, and Haptic Panels
- Future Outlook: Strategic Recommendations and Industry Roadmap
- Sources & References
Executive Summary: Key Trends and 2025 Outlook
The capacitive touch panel manufacturing sector is entering 2025 with robust momentum, driven by sustained demand across consumer electronics, automotive, industrial, and emerging IoT applications. The proliferation of smart devices, coupled with the integration of touch interfaces in new product categories, continues to expand the addressable market for capacitive touch technology. Leading manufacturers such as TPK Holding, Wintek Corporation, and Hon Hai Precision Industry (Foxconn) are scaling up production capacities and investing in advanced manufacturing processes to meet evolving customer requirements.
Key trends shaping the industry in 2025 include the adoption of thinner, flexible, and larger-format touch panels, as well as the integration of multi-touch and gesture recognition capabilities. The automotive sector, in particular, is accelerating demand for high-reliability, curved, and in-cell touch solutions for infotainment and control systems. Companies such as Kyocera Corporation and Nissha Co., Ltd. are at the forefront of supplying advanced touch panels for automotive and industrial applications, leveraging proprietary sensor and lamination technologies.
On the supply side, manufacturers are responding to cost pressures and the need for higher yields by automating production lines and adopting new materials, such as metal mesh and silver nanowire, to replace traditional indium tin oxide (ITO) electrodes. 3M and Cambrios are notable for their innovations in conductive materials, which enable improved transparency, flexibility, and durability in next-generation touch panels.
Geographically, Asia-Pacific remains the epicenter of capacitive touch panel manufacturing, with China, Taiwan, Japan, and South Korea hosting the majority of global production capacity. Companies like Foxconn and TPK Holding continue to expand their manufacturing footprints in response to both domestic and international demand. Meanwhile, North American and European OEMs are increasingly seeking strategic partnerships with Asian suppliers to secure supply chain resilience and access to the latest touch technologies.
Looking ahead, the outlook for 2025 and beyond is positive, with industry analysts projecting continued growth in unit shipments and revenues. The transition to foldable and rollable displays, the rise of smart home and industrial IoT devices, and the electrification of vehicles are expected to further drive innovation and investment in capacitive touch panel manufacturing. Leading players are likely to maintain their competitive edge through R&D, vertical integration, and close collaboration with device makers, ensuring that capacitive touch technology remains central to the user interface landscape in the coming years.
Market Size, Segmentation, and 8% CAGR Forecast (2025–2030)
The global capacitive touch panel manufacturing sector is poised for robust growth as digital interfaces proliferate across consumer electronics, automotive, industrial, and medical applications. In 2025, the market is estimated to reach a value in the mid-to-high tens of billions of US dollars, with leading manufacturers reporting strong order books and capacity expansions. The sector is forecasted to achieve a compound annual growth rate (CAGR) of approximately 8% from 2025 to 2030, driven by rising demand for smartphones, tablets, automotive displays, and interactive kiosks.
Market segmentation is primarily based on end-use application, panel type, and geographic region. Consumer electronics remain the dominant segment, accounting for over half of total demand, with major brands such as Samsung Electronics and Apple Inc. integrating advanced capacitive touch panels into flagship devices. The automotive sector is the fastest-growing segment, as automakers like LG Electronics (through its vehicle component solutions) and Panasonic Corporation expand the use of touch interfaces in infotainment and control systems.
From a manufacturing perspective, the industry is characterized by a mix of vertically integrated giants and specialized suppliers. TPK Holding Co., Ltd. and Wintek Corporation are among the leading original equipment manufacturers (OEMs) in Asia, supplying capacitive touch modules to global device makers. These companies are investing in new production lines and automation to meet the growing demand for larger, curved, and flexible touch panels, particularly for automotive and industrial applications.
Regionally, Asia-Pacific dominates both production and consumption, with China, Taiwan, South Korea, and Japan hosting the majority of manufacturing capacity. This concentration is supported by the presence of major display and electronics manufacturers, as well as a mature supply chain for key materials such as indium tin oxide (ITO) and optical adhesives. North America and Europe are significant markets for high-value applications, especially in automotive and medical devices, with companies like 3M and Zytronic focusing on specialized, ruggedized touch solutions.
Looking ahead, the 8% CAGR forecast reflects ongoing innovation in multi-touch, haptic feedback, and in-cell/on-cell integration technologies. The market outlook remains positive, underpinned by the digital transformation of everyday devices and the expansion of touch interfaces into new verticals. Strategic investments by leading manufacturers and the emergence of new use cases are expected to sustain growth momentum through 2030.
Technological Innovations: Materials, Design, and Performance
The capacitive touch panel manufacturing sector is experiencing rapid technological innovation in 2025, driven by the demand for higher performance, thinner form factors, and enhanced durability across consumer electronics, automotive, and industrial applications. Key advances are centered on materials science, sensor design, and integration techniques.
A major trend is the shift from traditional indium tin oxide (ITO) to alternative transparent conductive materials. ITO, while widely used, faces challenges such as brittleness and rising indium costs. In response, manufacturers are increasingly adopting metal mesh, silver nanowires, and conductive polymers. For example, Nitto Denko Corporation and TDK Corporation are actively developing and commercializing metal mesh films that offer superior flexibility and lower resistance, enabling the production of large-format and curved touch panels. Silver nanowire technology, championed by companies like Cambrios, is also gaining traction for its high transparency and mechanical robustness, particularly in foldable and wearable devices.
On the design front, the industry is moving towards in-cell and on-cell touch architectures, which integrate the touch sensor directly into the display stack. This approach reduces thickness, improves optical clarity, and lowers manufacturing complexity. Leading display manufacturers such as LG Display and Samsung Display are scaling up production of OLED and LCD panels with embedded touch functionality, targeting smartphones, tablets, and automotive displays. These integrated designs are expected to become mainstream by 2026, as they support bezel-less and edge-to-edge display trends.
Performance enhancements are also a focal point. Multi-finger and stylus support, high signal-to-noise ratios, and water/glove touch capabilities are being refined. Synaptics Incorporated and Goodix Technology are at the forefront of developing advanced touch controllers that leverage AI algorithms for improved accuracy and responsiveness, even in challenging environments.
Looking ahead, sustainability is influencing material choices and manufacturing processes. Companies such as Fujifilm are exploring recyclable substrates and low-energy fabrication methods to reduce environmental impact. As the market for electric vehicles and smart appliances expands, demand for robust, high-performance capacitive touch panels is set to grow, with ongoing innovation in materials and design expected to define the competitive landscape through 2027.
Major Players and Competitive Landscape (e.g., tpk.com, synaptics.com, 3m.com)
The capacitive touch panel manufacturing sector in 2025 is characterized by a dynamic competitive landscape, with a mix of established global leaders and innovative regional players. The industry is driven by ongoing demand from consumer electronics, automotive, industrial, and emerging IoT applications, with companies investing in advanced materials, multi-touch capabilities, and flexible form factors.
Among the most prominent manufacturers, TPK Holding Co., Ltd. remains a global leader, leveraging its early-mover advantage in projected capacitive (PCAP) technology and its extensive manufacturing footprint in Asia. TPK supplies touch panels to major device brands and continues to invest in large-format and curved touch solutions, targeting automotive and commercial display markets. The company’s vertical integration and partnerships with display panel makers have helped it maintain cost competitiveness and technological leadership.
Another key player, Synaptics Incorporated, is renowned for its expertise in touch controller ICs and system-level integration. Synaptics’ solutions are widely adopted in smartphones, tablets, and automotive displays, with the company focusing on AI-enhanced touch sensing and low-power designs. In 2025, Synaptics is expanding its portfolio to address the growing demand for touch-and-display driver integration (TDDI) and in-cell touch technologies, which streamline device assembly and improve optical performance.
In North America, 3M Company continues to play a significant role, particularly in commercial and industrial touch applications. 3M’s proprietary metal mesh and ultrafine wire technologies enable high-transparency, large-format touch panels suitable for interactive kiosks, digital signage, and medical devices. The company’s focus on durability and multi-user functionality positions it well in sectors requiring robust, reliable touch interfaces.
Other notable manufacturers include Wintek Corporation and Melrose Industries plc (through its subsidiary Touch International), both of which have expanded their product lines to include flexible and automotive-grade touch panels. Asian suppliers such as Hon Hai Precision Industry Co., Ltd. (Foxconn) and O-Film Tech Co., Ltd. are also increasing their market share by leveraging economies of scale and close relationships with major device OEMs.
Looking ahead, the competitive landscape is expected to intensify as manufacturers race to develop next-generation touch solutions, including foldable, transparent, and haptic-enabled panels. Strategic collaborations between touch panel makers, display manufacturers, and semiconductor companies are likely to accelerate innovation and address the evolving requirements of automotive, industrial, and wearable device markets.
Supply Chain Dynamics and Regional Manufacturing Hubs
The supply chain for capacitive touch panel manufacturing in 2025 is characterized by a complex, globally distributed network, with significant regional hubs in East Asia, particularly China, Taiwan, South Korea, and Japan. These regions continue to dominate due to their established electronics manufacturing ecosystems, access to raw materials, and proximity to major display and device assembly operations.
China remains the largest manufacturing base, with companies such as BOE Technology Group and TCL Technology leading large-scale production of touch panels for smartphones, tablets, automotive displays, and industrial applications. The Chinese government’s ongoing support for domestic semiconductor and display industries, including subsidies and infrastructure investment, has further consolidated the country’s position as a global hub. However, ongoing geopolitical tensions and export controls on advanced technologies have prompted some manufacturers to diversify their supply chains and invest in facilities outside mainland China.
Taiwan continues to play a pivotal role, with Hon Hai Precision Industry (Foxconn) and AU Optronics maintaining significant touch panel production capacity. Taiwan’s strengths lie in its advanced manufacturing processes, high yield rates, and integration with global electronics brands. The island’s manufacturers are increasingly focusing on high-value applications such as automotive and industrial touch panels, where reliability and performance are critical.
South Korea’s Samsung Electronics and LG Display continue to invest in next-generation touch technologies, including flexible and foldable panels. These companies benefit from vertical integration, controlling both display and touch sensor production, which enhances supply chain resilience and innovation speed. South Korea’s focus on R&D and premium product segments positions it as a leader in advanced touch solutions.
Japan, while having seen some capacity shift to other Asian countries, remains influential through companies like Japan Display Inc. and Nitto Denko, which supply high-quality touch sensors and specialty films. Japanese firms are known for their materials expertise and precision manufacturing, supporting niche and high-performance markets.
Looking ahead, the supply chain is expected to become more resilient and regionally diversified. Southeast Asia, particularly Vietnam and Thailand, is attracting new investments as companies seek to mitigate risks associated with overreliance on China. At the same time, North American and European firms are exploring local assembly and sourcing for critical applications, especially in automotive and medical devices, to enhance supply security.
Overall, the capacitive touch panel manufacturing landscape in 2025 and beyond will be shaped by ongoing regional competition, technological innovation, and strategic supply chain realignment in response to global economic and political shifts.
Application Expansion: Automotive, Consumer Electronics, and Industrial Uses
The application landscape for capacitive touch panels is rapidly expanding in 2025, driven by technological advancements and growing demand across automotive, consumer electronics, and industrial sectors. The integration of capacitive touch technology is now a defining feature in next-generation user interfaces, with manufacturers scaling up production and innovating to meet sector-specific requirements.
In the automotive industry, capacitive touch panels are increasingly replacing traditional mechanical controls, offering sleeker designs and enhanced user experiences. Major automotive suppliers and OEMs are collaborating with touch panel manufacturers to develop robust, high-performance solutions that can withstand harsh environments, temperature fluctuations, and electromagnetic interference. Companies such as Continental AG and DENSO Corporation are actively integrating large-format capacitive displays into dashboards, center consoles, and infotainment systems, with a focus on multi-touch functionality and haptic feedback. The trend is expected to accelerate as electric and autonomous vehicles demand more sophisticated human-machine interfaces.
Consumer electronics remain the largest market for capacitive touch panels, with smartphones, tablets, laptops, and wearables continuing to drive high-volume production. Leading display manufacturers like LG Display, Samsung Display, and Japan Display Inc. are investing in new manufacturing lines and materials, such as ultra-thin glass and flexible substrates, to enable bezel-less and foldable devices. In 2025, the adoption of in-cell and on-cell touch technologies is further streamlining device designs, reducing thickness, and improving optical clarity. The proliferation of smart home devices and IoT products is also fueling demand for small and mid-sized capacitive panels.
Industrial applications are witnessing robust growth as well, with capacitive touch panels being deployed in factory automation, medical equipment, and point-of-sale terminals. Manufacturers like 3M and Zytronic are focusing on ruggedized solutions that offer high durability, water and chemical resistance, and operation with gloves or styluses. The shift towards Industry 4.0 and digitalization is prompting factories to adopt touch-based HMIs (Human-Machine Interfaces) for improved efficiency and safety.
Looking ahead, the outlook for capacitive touch panel manufacturing remains strong, with continued innovation in materials, sensor architectures, and integration methods. As applications diversify and performance requirements become more stringent, collaboration between panel manufacturers, material suppliers, and end-users will be critical to sustaining growth and meeting the evolving needs of automotive, consumer, and industrial markets.
Sustainability Initiatives and Environmental Impact
Sustainability has become a central focus in the capacitive touch panel manufacturing sector as environmental regulations tighten and consumer demand for greener electronics grows. In 2025, leading manufacturers are accelerating efforts to reduce the environmental footprint of their operations, with initiatives spanning materials sourcing, energy consumption, and end-of-life management.
A key area of progress is the adoption of recycled and bio-based materials in touch panel construction. Major suppliers such as TPK Holding Co., Ltd. and Wintek Corporation are actively exploring alternatives to traditional indium tin oxide (ITO) films, which are energy-intensive to produce and rely on scarce resources. Research into conductive polymers and silver nanowire technologies is ongoing, aiming to reduce reliance on rare metals and improve recyclability. Additionally, glass substrates with higher recycled content are being introduced, aligning with broader electronics industry trends.
Energy efficiency in manufacturing processes is another priority. Companies like Hon Hai Precision Industry Co., Ltd. (Foxconn), a major assembler and component supplier, have committed to increasing the share of renewable energy in their production facilities. Foxconn’s public sustainability reports highlight investments in solar and wind power, as well as the implementation of energy management systems to monitor and optimize electricity usage across touch panel fabrication lines.
Waste reduction and responsible chemical management are also gaining traction. 3M, a supplier of optically clear adhesives and films for touch panels, has set ambitious targets for reducing process waste and phasing out hazardous substances in line with global standards such as RoHS and REACH. The company’s initiatives include closed-loop recycling systems for solvents and adhesives, as well as the development of water-based alternatives to traditional chemical processes.
End-of-life considerations are increasingly integrated into product design. Manufacturers are working to improve the disassembly and recyclability of touch panels, with modular designs and standardized materials facilitating easier recovery of valuable components. Industry associations and consortia are collaborating to establish best practices and certification schemes for sustainable electronics, further driving adoption across the supply chain.
Looking ahead, the capacitive touch panel industry is expected to deepen its commitment to sustainability through continued innovation in materials, cleaner manufacturing technologies, and circular economy principles. As regulatory and market pressures mount, these initiatives will be critical for maintaining competitiveness and meeting the expectations of environmentally conscious consumers and device brands.
Challenges: Raw Material Sourcing, Cost Pressures, and IP Issues
The manufacturing of capacitive touch panels in 2025 faces a complex landscape shaped by raw material sourcing challenges, persistent cost pressures, and ongoing intellectual property (IP) disputes. These factors are critical as the industry seeks to meet growing demand from sectors such as automotive, consumer electronics, and industrial automation.
A primary challenge remains the sourcing of indium tin oxide (ITO), the dominant transparent conductive material used in touch sensors. ITO’s supply is tightly linked to indium, a byproduct of zinc mining, making its availability vulnerable to fluctuations in mining output and geopolitical factors. In recent years, supply chain disruptions and increased demand for displays and photovoltaics have led to price volatility. Major panel manufacturers such as TPK Holding and Hon Hai Precision Industry (Foxconn) have responded by exploring alternative materials, including silver nanowires and metal mesh, but these technologies face their own scalability and cost hurdles.
Cost pressures are further exacerbated by the need for high-purity glass substrates and advanced manufacturing equipment. The dominance of a few suppliers, such as Corning Incorporated for specialty glass, means that price negotiations are often limited, and any upstream cost increases are quickly felt throughout the supply chain. Additionally, the push for thinner, more flexible panels—driven by applications in foldable devices and automotive interiors—requires investment in new production lines and process innovation, raising capital expenditure for manufacturers.
Intellectual property issues continue to be a significant concern. The capacitive touch panel sector is characterized by a dense web of patents covering sensor structures, controller algorithms, and manufacturing processes. Leading companies such as Synaptics Incorporated and 3M actively defend their IP portfolios, resulting in frequent litigation and licensing negotiations. This environment creates barriers for new entrants and can slow the adoption of novel materials or architectures, as companies must navigate potential infringement risks.
Looking ahead, the industry is expected to intensify efforts to localize supply chains and diversify material sources, particularly in response to geopolitical tensions and sustainability concerns. At the same time, ongoing consolidation among suppliers and manufacturers may help mitigate some cost pressures, but could also further concentrate IP ownership. As capacitive touch technology continues to evolve, addressing these challenges will be crucial for maintaining competitiveness and supporting innovation in the years beyond 2025.
Emerging Opportunities: Flexible, Transparent, and Haptic Panels
The capacitive touch panel manufacturing sector is undergoing significant transformation in 2025, driven by the emergence of flexible, transparent, and haptic-enabled panels. These innovations are reshaping product design and user experience across consumer electronics, automotive, and industrial applications.
Flexible capacitive touch panels, enabled by advances in materials such as ultra-thin glass and high-performance polymers, are gaining traction. Manufacturers like Nitto Denko Corporation and Kuraray Co., Ltd. are at the forefront, supplying specialty films and substrates that allow touch panels to bend and conform to curved surfaces. This flexibility is particularly valuable for next-generation foldable smartphones, wearable devices, and automotive interiors, where design freedom and durability are paramount.
Transparency remains a critical focus, especially as displays become more immersive and bezel-less. Companies such as 3M and AGC Inc. are developing advanced transparent conductive films and glass solutions that maintain high optical clarity while supporting multi-touch functionality. These materials are essential for augmented reality (AR) devices and heads-up displays, where unobstructed visibility is crucial.
Haptic feedback integration is another emerging opportunity, enhancing the tactile experience of touch interfaces. TDK Corporation and Murata Manufacturing Co., Ltd. are investing in piezoelectric and electroactive polymer actuators that can be embedded within capacitive panels. This technology enables localized vibrations or force feedback, simulating the sensation of pressing physical buttons or textures, which is increasingly sought after in automotive controls and gaming devices.
Looking ahead, the convergence of these technologies is expected to accelerate. Industry roadmaps indicate that by 2026–2027, mass production of large-area flexible and transparent touch panels with integrated haptics will become more feasible, driven by improvements in roll-to-roll manufacturing and scalable deposition techniques. Strategic partnerships between material suppliers, panel manufacturers, and OEMs are intensifying to address challenges such as cost, reliability, and integration complexity.
As the market evolves, leading manufacturers are expanding their R&D and production capacities to capture these emerging opportunities. The sector’s outlook remains robust, with capacitive touch panels poised to play a central role in the next wave of interactive, adaptive, and immersive electronic devices.
Future Outlook: Strategic Recommendations and Industry Roadmap
The capacitive touch panel manufacturing sector is poised for significant transformation in 2025 and the years immediately following, driven by evolving end-user demands, technological advancements, and global supply chain dynamics. As capacitive touch technology remains the dominant interface for smartphones, tablets, automotive displays, and industrial controls, manufacturers are under increasing pressure to innovate while maintaining cost efficiency and supply chain resilience.
A key strategic recommendation for industry players is to accelerate investment in advanced materials and process automation. The adoption of metal mesh and silver nanowire technologies is expected to expand, offering improved transparency, flexibility, and conductivity compared to traditional indium tin oxide (ITO) films. Leading manufacturers such as TPK Holding Co., Ltd. and Wintek Corporation are already scaling up production capabilities for these next-generation materials, aiming to serve emerging applications in foldable devices and automotive interiors.
Another critical area is the integration of touch and display modules (TDDI), which streamlines manufacturing and reduces component thickness. Companies like Hon Hai Precision Industry Co., Ltd. (Foxconn) and China Star Optoelectronics Technology (CSOT) are investing in TDDI solutions to meet OEM demands for slimmer, more robust devices. This trend is expected to intensify as consumer electronics brands seek differentiation through design and user experience.
Sustainability and supply chain localization are also becoming strategic imperatives. The volatility of raw material prices, particularly for ITO and rare metals, has prompted manufacturers to explore alternative sourcing and recycling initiatives. 3M and Nitto Denko Corporation are notable for their efforts in developing eco-friendly conductive films and adhesives, aligning with global environmental standards and customer expectations.
Looking ahead, the industry roadmap should prioritize:
- R&D collaboration with display and semiconductor partners to enable seamless integration of touch, haptics, and biometric sensors.
- Adoption of AI-driven process control and quality assurance to enhance yield and reduce defects.
- Expansion into high-growth verticals such as automotive, medical devices, and industrial automation, where demand for ruggedized and large-format touch panels is rising.
- Building resilient supply chains through regional diversification and strategic partnerships with material suppliers and OEMs.
In summary, capacitive touch panel manufacturers that proactively invest in material innovation, process integration, and sustainable practices will be best positioned to capture growth opportunities and navigate the challenges of the mid-2020s.
Sources & References
- Hon Hai Precision Industry (Foxconn)
- Nissha Co., Ltd.
- Apple Inc.
- LG Electronics
- Zytronic
- LG Display
- Samsung Display
- Synaptics Incorporated
- Goodix Technology
- Fujifilm
- BOE Technology Group
- AU Optronics
- Kuraray Co., Ltd.
- AGC Inc.
- Murata Manufacturing Co., Ltd.