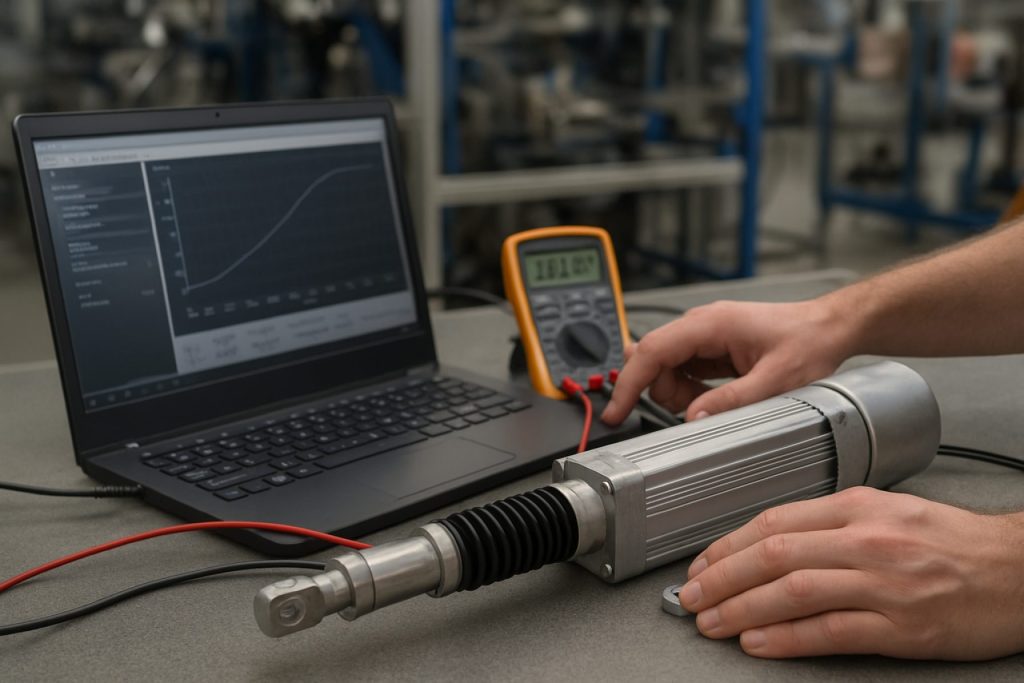
Actuator Calibration Technologies in 2025: How Precision Engineering and Smart Automation Are Shaping the Next Era. Explore the Innovations, Market Shifts, and Strategic Opportunities Transforming This Critical Industry.
- Executive Summary: Key Trends and Market Outlook (2025–2029)
- Market Size, Growth Forecasts, and Regional Hotspots
- Core Technologies: Digital, Wireless, and AI-Driven Calibration
- Leading Players and Strategic Partnerships (e.g., emerson.com, siemens.com, honeywell.com)
- Emerging Standards and Regulatory Developments (e.g., isa.org, asme.org)
- Industrial Applications: Oil & Gas, Power, Pharma, and Beyond
- Integration with IIoT and Smart Manufacturing Ecosystems
- Challenges: Cybersecurity, Interoperability, and Workforce Skills
- Innovation Pipeline: R&D, Patents, and Next-Gen Solutions
- Future Outlook: Disruptive Trends and Strategic Recommendations
- Sources & References
Executive Summary: Key Trends and Market Outlook (2025–2029)
The actuator calibration technologies sector is undergoing significant transformation as industries prioritize precision, automation, and digital integration. In 2025, the market is characterized by rapid adoption of smart calibration solutions, driven by the increasing complexity of industrial automation systems and the need for higher operational efficiency. Key trends include the integration of digital twins, cloud-based calibration management, and the use of advanced sensors for real-time feedback and self-calibration capabilities.
Major actuator manufacturers such as Festo, Siemens, and Emerson Electric are investing heavily in digital calibration platforms. These platforms enable remote diagnostics, predictive maintenance, and seamless integration with industrial IoT (IIoT) ecosystems. For example, Festo has introduced smart actuators with embedded sensors that facilitate automatic calibration and continuous performance monitoring, reducing downtime and manual intervention. Similarly, Siemens is advancing its portfolio with actuators that support digital commissioning and cloud-based calibration data storage, enhancing traceability and compliance in regulated industries.
The adoption of wireless calibration tools is also accelerating, particularly in sectors such as oil & gas, water treatment, and pharmaceuticals, where minimizing human exposure and ensuring process safety are paramount. Companies like Emerson Electric and SMC Corporation are developing portable, wireless calibration devices that streamline field operations and support real-time data synchronization with central control systems.
Data from industry bodies such as the FieldComm Group and PI (PROFIBUS & PROFINET International) indicate a growing emphasis on standardized communication protocols for actuator calibration. This standardization is expected to facilitate interoperability between devices from different manufacturers, further accelerating the adoption of smart calibration solutions.
Looking ahead to 2029, the outlook for actuator calibration technologies is robust. The convergence of artificial intelligence, machine learning, and edge computing is anticipated to enable fully autonomous calibration systems capable of self-optimization and adaptive control. As regulatory requirements tighten and industries demand higher levels of traceability, the market will likely see increased collaboration between actuator manufacturers, automation software providers, and standards organizations to deliver secure, scalable, and future-proof calibration solutions.
Market Size, Growth Forecasts, and Regional Hotspots
The global market for actuator calibration technologies is experiencing robust growth in 2025, driven by the increasing adoption of automation across industries such as automotive, aerospace, energy, and manufacturing. Actuator calibration—critical for ensuring precision and reliability in automated systems—has become a focal point as industries pursue higher efficiency, safety, and regulatory compliance.
Current estimates place the actuator calibration technology market in the multi-billion dollar range, with annual growth rates projected between 6% and 9% through the late 2020s. This expansion is fueled by the proliferation of smart factories and the Industrial Internet of Things (IIoT), where precise actuator performance is essential for process optimization and predictive maintenance. The demand is particularly strong in sectors where safety and accuracy are paramount, such as oil & gas, pharmaceuticals, and power generation.
Regionally, Asia-Pacific stands out as the fastest-growing hotspot, led by China, Japan, and South Korea. These countries are investing heavily in advanced manufacturing and automation infrastructure, with government initiatives supporting digital transformation in industry. Europe remains a significant market, with Germany, France, and the UK at the forefront due to their established industrial bases and stringent quality standards. North America, particularly the United States, continues to see steady demand, driven by ongoing modernization of legacy systems and the integration of smart technologies in both manufacturing and energy sectors.
Key players in actuator calibration technologies include Emerson Electric Co., which offers a range of calibration solutions for valve and process automation, and Siemens AG, known for its digital calibration tools integrated into industrial automation platforms. Honeywell International Inc. provides advanced calibration services and software, particularly for process industries. Festo AG & Co. KG and SMC Corporation are also prominent, supplying pneumatic and electric actuator calibration systems globally.
Looking ahead, the market is expected to benefit from advancements in AI-driven calibration, cloud-based monitoring, and remote diagnostics. These innovations are anticipated to further reduce downtime, enhance accuracy, and support the shift toward predictive maintenance. As regulatory requirements tighten and the complexity of automated systems increases, actuator calibration technologies will remain a critical enabler of industrial productivity and safety worldwide.
Core Technologies: Digital, Wireless, and AI-Driven Calibration
Actuator calibration technologies are undergoing rapid transformation in 2025, driven by the convergence of digitalization, wireless connectivity, and artificial intelligence (AI). These advancements are reshaping how industries such as manufacturing, process automation, and automotive ensure the precision and reliability of actuators—critical components responsible for controlling movement and positioning in machinery and systems.
Digital calibration platforms are now widely adopted, replacing manual and analog methods with software-driven solutions that enable remote configuration, diagnostics, and data logging. Leading actuator manufacturers such as Siemens and Emerson Electric have integrated digital calibration tools into their actuator product lines, allowing for real-time monitoring and adjustment via centralized control systems. These platforms often leverage standardized communication protocols (e.g., HART, Profibus, Foundation Fieldbus) to ensure interoperability across diverse industrial environments.
Wireless calibration is another significant trend, reducing the need for physical access to actuators installed in hazardous or hard-to-reach locations. Companies like Schneider Electric and Honeywell International have introduced wireless-enabled actuator solutions that support over-the-air firmware updates and calibration routines. This not only enhances safety and efficiency but also minimizes downtime during maintenance cycles. The adoption of industrial wireless standards such as WirelessHART and ISA100.11a is expected to accelerate through 2025 and beyond, further enabling remote calibration capabilities.
AI-driven calibration is emerging as a transformative force, with machine learning algorithms analyzing actuator performance data to optimize calibration parameters automatically. ABB and Festo are at the forefront of integrating AI into their actuator management systems, enabling predictive maintenance and self-calibrating actuators that adapt to changing operational conditions. These intelligent systems can detect drift, wear, or anomalies in actuator behavior, triggering recalibration or alerting operators before failures occur.
Looking ahead, the outlook for actuator calibration technologies is marked by increasing automation, connectivity, and intelligence. The integration of digital twins—virtual replicas of physical actuators—by companies such as Siemens is expected to further enhance calibration accuracy and lifecycle management. As industrial sectors continue to prioritize operational efficiency, safety, and sustainability, the demand for advanced calibration technologies will remain strong, with ongoing innovation anticipated from both established players and emerging technology providers.
Leading Players and Strategic Partnerships (e.g., emerson.com, siemens.com, honeywell.com)
The actuator calibration technologies market in 2025 is characterized by the active involvement of several global industrial automation leaders, who are leveraging strategic partnerships and technological innovation to address the increasing demand for precision, reliability, and digital integration in process industries. Key players such as Emerson Electric Co., Siemens AG, and Honeywell International Inc. are at the forefront, each bringing decades of expertise in automation, control systems, and field instrumentation.
Emerson, through its Automation Solutions division, continues to expand its portfolio of smart actuator calibration tools, integrating advanced diagnostics and digital communication protocols. Their focus on interoperability and predictive maintenance is evident in recent product launches and collaborations with process industry clients, aiming to reduce downtime and improve asset performance. Emerson’s Plantweb digital ecosystem, for example, incorporates actuator calibration as a core component of its IIoT-enabled asset management strategy, supporting both legacy and next-generation field devices.
Siemens, another major player, is advancing actuator calibration through its Digital Industries division. The company’s SIMATIC and SIPART product lines offer automated calibration routines and seamless integration with distributed control systems (DCS), enabling remote diagnostics and real-time performance monitoring. Siemens’ strategic partnerships with industrial software providers and end-users are driving the adoption of digital twins and cloud-based calibration management, which are expected to become standard practice in the next few years as industries accelerate digital transformation.
Honeywell, with its Process Solutions business, is also investing heavily in actuator calibration technologies. The company’s SmartLine transmitters and control systems feature embedded calibration and self-diagnostic capabilities, supporting both on-site and remote calibration workflows. Honeywell’s alliances with oil & gas, chemical, and power generation companies are fostering the development of calibration solutions tailored to harsh and safety-critical environments, with a strong emphasis on cybersecurity and regulatory compliance.
Looking ahead, the next few years are likely to see increased collaboration between these leading players and specialized actuator manufacturers, such as Festo and SMC Corporation, to develop plug-and-play calibration modules and open communication standards. Industry consortia and standards bodies, including FieldComm Group, are expected to play a pivotal role in harmonizing protocols and ensuring interoperability across multi-vendor environments. As digitalization deepens, strategic partnerships will be essential for delivering scalable, secure, and future-proof actuator calibration solutions.
Emerging Standards and Regulatory Developments (e.g., isa.org, asme.org)
The landscape of actuator calibration technologies is undergoing significant transformation in 2025, driven by the emergence of new standards and regulatory frameworks. As industrial automation and robotics become increasingly sophisticated, the need for precise, reliable, and standardized calibration methods for actuators—ranging from pneumatic and hydraulic to electric and smart actuators—has never been more critical. Regulatory bodies and standards organizations are responding with updated guidelines and collaborative initiatives to ensure interoperability, safety, and performance across diverse sectors.
A key player in this evolution is the International Society of Automation (ISA), which continues to refine its ISA-75 and ISA-20 series standards. These standards address the calibration, testing, and performance verification of control valves and actuators, emphasizing digital communication protocols and cybersecurity considerations. In 2025, ISA is actively working with industry partners to expand guidelines for smart actuators, integrating requirements for self-diagnostics and remote calibration capabilities, reflecting the growing adoption of Industrial Internet of Things (IIoT) technologies.
Similarly, the American Society of Mechanical Engineers (ASME) is advancing its standards for actuator calibration, particularly within the ASME B16 and B40 series. These standards are being updated to include best practices for calibration traceability, uncertainty quantification, and compatibility with automated calibration systems. ASME’s efforts are closely aligned with the push for digital transformation in manufacturing, supporting the integration of actuators into smart factory environments.
On the international front, organizations such as the International Electrotechnical Commission (IEC) and the International Organization for Standardization (ISO) are harmonizing actuator calibration standards to facilitate global trade and regulatory compliance. The IEC 61508 and ISO 13849 standards, which address functional safety for electrical and electronic systems, are being revised to include more explicit requirements for actuator calibration and validation, especially in safety-critical applications like process industries and autonomous vehicles.
Looking ahead, the next few years are expected to see increased collaboration between standards bodies, manufacturers, and end-users. Major actuator manufacturers such as Emerson, Siemens, and Festo are actively participating in standards development, contributing field data and technical expertise to ensure that new guidelines are both practical and forward-looking. These companies are also investing in digital calibration platforms and cloud-based calibration management, anticipating regulatory shifts toward continuous compliance and real-time performance monitoring.
In summary, 2025 marks a pivotal year for actuator calibration technologies, with emerging standards and regulatory developments setting the stage for safer, smarter, and more interoperable automation systems worldwide.
Industrial Applications: Oil & Gas, Power, Pharma, and Beyond
Actuator calibration technologies are critical in ensuring the precision, safety, and efficiency of automated systems across industrial sectors such as oil & gas, power generation, and pharmaceuticals. As of 2025, the demand for advanced calibration solutions is intensifying, driven by stricter regulatory requirements, the proliferation of digitalization, and the need for predictive maintenance in mission-critical environments.
In the oil & gas sector, actuator calibration is essential for maintaining the integrity of flow control systems, safety shut-off valves, and pressure regulators. Companies like Emerson Electric Co. and Siemens AG have developed smart actuator platforms that integrate self-diagnostic and auto-calibration features. These systems leverage embedded sensors and digital communication protocols (such as HART and Foundation Fieldbus) to enable real-time calibration, reducing manual intervention and minimizing downtime. For example, Emerson’s Fisher FIELDVUE digital valve controllers are widely adopted for their ability to perform in-situ calibration and provide continuous health monitoring, which is particularly valuable in remote or hazardous oilfield environments.
In power generation, actuator calibration technologies are evolving to support the transition to renewable energy and the integration of distributed energy resources. Schneider Electric and ABB Ltd. are notable for their actuator solutions that incorporate advanced calibration algorithms and cloud connectivity. These features facilitate remote diagnostics and predictive maintenance, which are increasingly important as power plants seek to maximize uptime and comply with evolving grid standards. ABB’s digital actuators, for instance, can be calibrated and monitored via secure cloud platforms, enabling operators to optimize performance and preemptively address potential failures.
The pharmaceutical industry, with its stringent regulatory landscape, places a premium on traceable and repeatable actuator calibration. Companies such as Festo AG & Co. KG and SMC Corporation provide actuator systems with integrated calibration routines and electronic record-keeping, supporting compliance with Good Manufacturing Practice (GMP) and FDA requirements. These technologies ensure that critical processes—such as dosing, mixing, and packaging—are executed with high precision and documented for auditability.
Looking ahead, the next few years are expected to see further convergence of actuator calibration with Industrial Internet of Things (IIoT) platforms, artificial intelligence, and edge computing. This will enable even more autonomous calibration, adaptive control, and real-time analytics, further reducing operational risks and costs across industries. As digital transformation accelerates, leading manufacturers are likely to expand their offerings with enhanced cybersecurity and interoperability features, ensuring that actuator calibration technologies remain at the forefront of industrial automation.
Integration with IIoT and Smart Manufacturing Ecosystems
The integration of actuator calibration technologies with Industrial Internet of Things (IIoT) and smart manufacturing ecosystems is accelerating rapidly in 2025, driven by the need for higher precision, predictive maintenance, and seamless data exchange across industrial environments. Actuators—critical components in process automation, robotics, and motion control—require regular calibration to maintain accuracy and reliability. Traditionally, calibration was a manual, time-consuming process, but the advent of IIoT-enabled solutions is transforming this landscape.
Leading actuator manufacturers are embedding smart sensors and connectivity modules directly into their devices, enabling real-time monitoring and remote calibration. For example, Festo has developed intelligent actuators with built-in diagnostics and cloud connectivity, allowing for continuous performance tracking and automated calibration alerts. Similarly, Siemens integrates its actuators with the MindSphere IIoT platform, facilitating centralized data collection and analytics for predictive calibration scheduling.
The adoption of open communication protocols such as OPC UA and MQTT is further enhancing interoperability between actuators, calibration tools, and manufacturing execution systems (MES). Companies like Emerson and Schneider Electric are actively promoting these standards, enabling their actuator solutions to seamlessly interface with broader smart factory architectures. This integration supports closed-loop calibration workflows, where sensor data is automatically analyzed and calibration routines are triggered without human intervention.
Data security and integrity are also key concerns as calibration data becomes part of the larger IIoT ecosystem. Industry leaders are implementing robust cybersecurity measures and blockchain-based traceability to ensure that calibration records are tamper-proof and compliant with regulatory standards. Honeywell, for instance, is investing in secure edge computing solutions that process calibration data locally before transmitting it to the cloud, reducing latency and exposure to cyber threats.
Looking ahead, the next few years are expected to see further convergence of actuator calibration technologies with artificial intelligence (AI) and machine learning (ML) algorithms. These advancements will enable self-calibrating actuators capable of adapting to changing operational conditions and predicting calibration needs based on historical performance data. As digital twins become more prevalent in smart manufacturing, virtual calibration and simulation tools will also gain traction, reducing downtime and optimizing maintenance schedules.
In summary, the integration of actuator calibration technologies with IIoT and smart manufacturing ecosystems in 2025 is fostering greater automation, reliability, and efficiency. Major industry players are driving this evolution by embedding intelligence, connectivity, and security into their actuator solutions, setting the stage for a new era of autonomous, data-driven calibration processes.
Challenges: Cybersecurity, Interoperability, and Workforce Skills
The rapid evolution of actuator calibration technologies in 2025 is accompanied by a set of pressing challenges, particularly in the domains of cybersecurity, interoperability, and workforce skills. As actuators become increasingly integrated into industrial automation, robotics, and smart infrastructure, the complexity and criticality of their calibration processes have grown, exposing new vulnerabilities and operational hurdles.
Cybersecurity is a mounting concern as actuator calibration systems are now frequently connected to broader industrial networks and cloud-based platforms. The risk of unauthorized access or manipulation of calibration parameters can have severe consequences, including equipment malfunction or safety hazards. Leading actuator manufacturers such as Siemens and ABB have responded by embedding advanced encryption and authentication protocols into their calibration tools and software suites. However, the proliferation of legacy devices and the diversity of communication standards continue to present significant security gaps. Industry bodies like the ODVA are actively developing guidelines to secure device-level communications, but widespread adoption remains a work in progress.
Interoperability is another critical challenge, as actuator calibration technologies must function seamlessly across a heterogeneous landscape of devices, protocols, and platforms. The lack of universal standards often leads to integration bottlenecks, especially in facilities that operate equipment from multiple vendors. Organizations such as the FieldComm Group and PI (PROFIBUS & PROFINET International) are promoting open standards like HART, FOUNDATION Fieldbus, and PROFINET to facilitate cross-vendor compatibility. Despite these efforts, full interoperability is still elusive, and many end-users are compelled to rely on proprietary calibration solutions, which can limit flexibility and increase long-term costs.
Workforce skills represent a third major challenge. The sophistication of modern actuator calibration—often involving digital twins, AI-driven diagnostics, and remote calibration capabilities—demands a workforce with advanced technical expertise. Companies such as Emerson and Schneider Electric have launched training initiatives and certification programs to upskill technicians and engineers. Nevertheless, the pace of technological change is outstripping the availability of qualified personnel, leading to a skills gap that could hinder the effective deployment and maintenance of next-generation calibration systems.
Looking ahead, addressing these challenges will require coordinated action among manufacturers, standards organizations, and educational institutions. The next few years are likely to see increased investment in secure, interoperable, and user-friendly calibration technologies, as well as expanded efforts to cultivate a digitally skilled workforce capable of supporting the future of actuator calibration.
Innovation Pipeline: R&D, Patents, and Next-Gen Solutions
The landscape of actuator calibration technologies is undergoing rapid transformation as industries demand higher precision, reliability, and automation in motion control systems. In 2025, the innovation pipeline is characterized by a convergence of advanced sensor integration, AI-driven calibration algorithms, and digital twin methodologies, all aimed at reducing downtime and enhancing system performance.
Leading actuator manufacturers are investing heavily in R&D to develop next-generation calibration solutions. Festo, a global leader in automation technology, has been at the forefront with its smart actuators featuring embedded self-calibration routines. These systems leverage real-time sensor feedback and edge computing to automatically adjust parameters, minimizing manual intervention and ensuring optimal performance throughout the actuator’s lifecycle. Similarly, SMC Corporation is advancing the integration of IoT-enabled calibration modules, allowing remote diagnostics and parameter tuning via secure cloud platforms.
Patent activity in this sector has intensified, with a notable increase in filings related to machine learning-based calibration and adaptive control systems. Parker Hannifin has secured intellectual property around predictive maintenance and self-learning actuators, which utilize historical operational data to anticipate calibration needs and autonomously initiate correction cycles. This approach not only extends actuator lifespan but also aligns with the broader trend toward Industry 4.0 and smart manufacturing.
Digital twin technology is emerging as a pivotal tool in actuator calibration. By creating virtual replicas of physical actuators, companies can simulate performance, predict drift, and optimize calibration schedules without interrupting production. Bosch Rexroth is actively developing digital twin frameworks that integrate with their motion control platforms, enabling continuous calibration and real-time system health monitoring.
Looking ahead, the next few years are expected to see further convergence of AI, connectivity, and miniaturized sensor technologies in actuator calibration. The adoption of standardized communication protocols and open-source calibration libraries is likely to accelerate cross-vendor compatibility and reduce integration complexity. As regulatory standards for safety and traceability tighten, automated calibration verification and digital record-keeping will become essential features in new actuator offerings.
- Self-calibrating actuators with embedded AI and edge analytics
- Remote and cloud-based calibration management
- Digital twin-driven predictive calibration and maintenance
- Increased patent filings in adaptive and autonomous calibration
- Standardization and interoperability across platforms
In summary, actuator calibration technologies in 2025 are defined by a robust innovation pipeline, with major industry players driving advancements that promise greater automation, reliability, and efficiency in industrial motion systems.
Future Outlook: Disruptive Trends and Strategic Recommendations
The landscape of actuator calibration technologies is poised for significant transformation in 2025 and the coming years, driven by advances in automation, digitalization, and the integration of artificial intelligence (AI). As industries such as automotive, aerospace, energy, and manufacturing demand higher precision and reliability, actuator calibration is evolving from manual, labor-intensive processes to highly automated, data-driven systems.
A key disruptive trend is the adoption of digital twins and model-based calibration. Digital twins—virtual replicas of physical actuators—enable real-time simulation and predictive calibration, reducing downtime and improving accuracy. Major automation and control companies, such as Siemens and ABB, are investing in digital twin platforms that integrate actuator calibration into broader asset management and predictive maintenance ecosystems. These solutions leverage sensor data and cloud connectivity to enable remote calibration, which is particularly valuable for distributed assets in sectors like oil & gas and utilities.
Another significant development is the integration of AI and machine learning algorithms into calibration workflows. By analyzing historical and real-time performance data, AI-driven systems can identify calibration drift, predict failures, and automatically adjust actuator parameters. Companies such as Emerson Electric and Honeywell are incorporating AI capabilities into their actuator and control system offerings, aiming to reduce human intervention and enhance system reliability.
Wireless and IoT-enabled calibration tools are also gaining traction. These technologies facilitate in-situ calibration, minimizing the need for physical access and manual adjustments. For example, Festo and SMC Corporation are developing smart actuators with embedded sensors and wireless communication modules, allowing for continuous monitoring and remote calibration. This trend aligns with the broader shift toward Industry 4.0, where interconnected devices and systems drive operational efficiency.
Looking ahead, the convergence of these technologies is expected to yield fully autonomous calibration systems by the late 2020s. Strategic recommendations for industry stakeholders include investing in digital infrastructure, prioritizing cybersecurity for connected calibration devices, and fostering partnerships with technology providers to accelerate innovation. As regulatory standards for safety and performance tighten, early adoption of advanced calibration technologies will be critical for maintaining competitiveness and ensuring compliance.
Sources & References
- Siemens
- Emerson Electric
- SMC Corporation
- PI (PROFIBUS & PROFINET International)
- Honeywell International Inc.
- ABB
- International Society of Automation
- American Society of Mechanical Engineers
- International Organization for Standardization
- Emerson
- Siemens
- Festo
- ODVA
- Bosch Rexroth