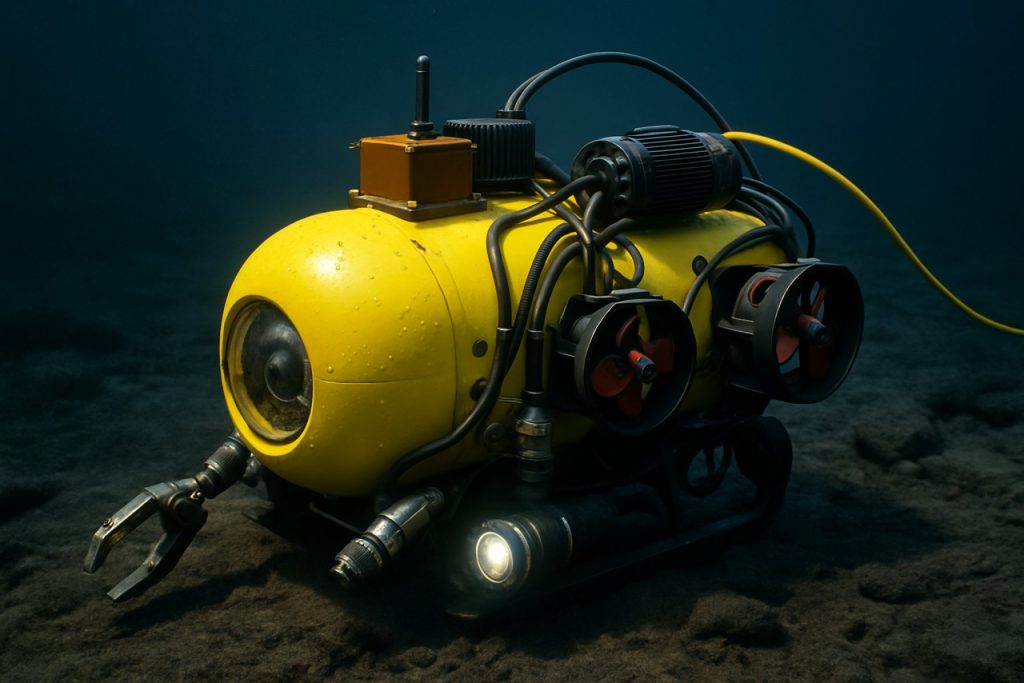
Table of Contents
- Executive Summary: Key Drivers and 2025 Snapshot
- Technology Overview: Principles of Brushless Vector Drives
- Market Size & Growth Forecast (2025–2030)
- Emerging Applications in Subsea Robotics
- Competitive Landscape: Leading Manufacturers and Innovators
- Technological Advancements & R&D Focus Areas
- Regulatory Standards and Industry Initiatives (e.g., ieee.org, asme.org)
- Challenges: Reliability, Integration, and Harsh Environment Performance
- Investment Trends & Strategic Partnerships
- Future Outlook: Disruptive Trends and Long-Term Opportunities
- Sources & References
Executive Summary: Key Drivers and 2025 Snapshot
The market for variable frequency brushless vector drives in subsea robotics is entering a period of robust innovation and adoption as of 2025, underpinned by the need for greater reliability, energy efficiency, and precision control in demanding marine environments. These advanced drives—critical for remotely operated vehicles (ROVs), autonomous underwater vehicles (AUVs), and subsea manipulation systems—address unique challenges such as pressure resilience, thermal management, and real-time adaptive control demanded by offshore energy, defense, and scientific operations.
Key drivers in 2025 include the expansion of offshore wind and oil & gas infrastructure, increasing deployment of deepwater robotics for maintenance and inspection, and the integration of AI-powered navigation requiring ultra-precise motor control. Major energy operators are prioritizing subsea asset uptime and operational safety, driving demand for robust drive systems capable of withstanding extended missions and variable load conditions. The ongoing electrification of subsea systems, replacing hydraulic actuation with electric alternatives, further accelerates adoption of high-efficiency variable frequency drives.
Leading solution providers such as Siemens and ABB are investing in subsea-qualified variable speed drive platforms capable of delivering compactness, modularity, and high fault tolerance. Their recent product offerings focus on enhanced ingress protection, advanced vector control algorithms, and digital integration for predictive maintenance—features increasingly demanded by operators in the North Sea, Gulf of Mexico, and Asia-Pacific projects. For instance, Bosch Rexroth and Parker Hannifin are expanding their portfolios with tailored brushless drive solutions for underwater thrusters and robotic arms, emphasizing real-time feedback and adaptive torque control.
2025 also sees growing collaboration between drive manufacturers and subsea OEMs, fostering rapid customization and rigorous qualification processes. The push towards standardization, interoperability, and digital twin integration is shaping procurement decisions among major offshore contractors. Moreover, safety standards and environmental regulations around subsea emissions and noise pollution are incentivizing the migration to electric drives with lower acoustic signatures and higher operational efficiency.
Looking ahead, the outlook for variable frequency brushless vector drives in subsea robotics remains strongly positive. With the offshore robotics fleet expected to expand, and digitalization trends mandating smarter, data-enabled actuation, suppliers positioned with robust, high-efficiency, and easily integrated drive solutions are set to capture significant market share. Continued innovation by industry leaders such as Siemens, ABB, and Bosch Rexroth will be pivotal in shaping the sector’s technological trajectory through 2025 and beyond.
Technology Overview: Principles of Brushless Vector Drives
Variable frequency brushless vector drives have emerged as a cornerstone technology in advanced subsea robotics, enabling precise, high-efficiency electric motor control under extreme underwater conditions. These drives operate by modulating the frequency and amplitude of the voltage supplied to brushless motors—typically permanent magnet synchronous motors (PMSMs) or brushless DC motors (BLDCs)—to achieve variable speed and torque control. The “vector” aspect refers to field-oriented control (FOC), a sophisticated algorithm that manipulates the stator current components to optimize motor torque and efficiency, which is crucial for the demanding maneuvers and endurance required in subsea operations.
In 2025, the fundamental architecture of these drives remains focused on digital signal processing, real-time feedback from encoders or resolvers, and robust power electronics engineered for high reliability. Integrated sensors provide continuous data on rotor position and speed, allowing for real-time adjustments and fault detection—vital for unmanned underwater vehicles (UUVs), remotely operated vehicles (ROVs), and subsea manipulators where maintenance access is limited. Leading sector participants including ABB, Siemens, and Parker Hannifin have advanced drive technology with high ingress protection (IP) ratings, corrosion-resistant enclosures, and advanced thermal management systems to extend operational life in high-pressure saltwater environments.
Recent technological progress has centered on improving drive efficiency and reducing electromagnetic interference, both critical in the crowded electronic environments of subsea vehicles. For example, in 2024–2025, drive manufacturers have begun integrating wide-bandgap semiconductors—such as silicon carbide (SiC) and gallium nitride (GaN)—into inverter circuitry, dramatically increasing switching speeds and reducing energy losses. These advances support higher power density and smaller form factors, which are particularly advantageous in space-constrained subsea robotics (Schneider Electric).
Additionally, embedded communication protocols such as CANopen and EtherCAT have become standard, facilitating real-time coordination between drive systems, vehicle controllers, and mission payloads. With growing requirements for autonomy and remote diagnostics, the emphasis on cybersecure firmware and remote firmware update capabilities is increasing.
Looking ahead, the outlook for 2025 and the next few years indicates continued focus on reliability, miniaturization, and integration with AI-based control platforms for autonomous robotics. As subsea missions demand greater endurance and dexterity, the role of variable frequency brushless vector drives in enabling high-precision, energy-efficient actuation is set to expand, with ongoing R&D investments from OEMs and suppliers directly shaping the capabilities of next-generation subsea robotic platforms.
Market Size & Growth Forecast (2025–2030)
The market for variable frequency brushless vector drives in subsea robotics is positioned for robust growth from 2025 through 2030, driven by rising investments in offshore energy, undersea infrastructure maintenance, and advanced oceanographic exploration. As the subsea robotics sector expands—encompassing remotely operated vehicles (ROVs), autonomous underwater vehicles (AUVs), and subsea manipulators—demand for high-performance motion control solutions such as brushless vector drives is accelerating.
Key players, including Siemens, ABB, and Schneider Electric, are actively developing and supplying variable frequency drive (VFD) technologies tailored for harsh subsea environments. These drives offer closed-loop vector control for brushless motors, enabling precise torque and speed regulation—critical for the efficiency, reliability, and safety of subsea robotic operations.
The growth trajectory is underpinned by several factors:
- Offshore Energy Expansion: The global push for deepwater oil and gas extraction and the installation of offshore wind farms are driving the deployment of advanced subsea robotics, which rely on rugged, high-efficiency drive systems.
- Technological Advancements: Innovations in drive miniaturization, digital control, and integration with real-time monitoring systems are making vector drives increasingly viable for compact, battery-powered robotic platforms.
- Operational Demands: Growing requirements for longer missions, greater maneuverability, and reduced maintenance intervals are accelerating the adoption of brushless vector drive solutions.
Although precise market sizing figures are proprietary or fragmented across company disclosures, industry leaders like Siemens and ABB report increased orders for subsea-rated VFDs in their energy and marine business units. The volume of subsea robotics deployments is anticipated to rise, with a corresponding increase in demand for motion control systems. The period 2025–2030 is expected to see compounded annual growth rates in the high single to low double digits, as manufacturers and integrators upgrade both new and legacy subsea platforms.
Looking ahead, market expansion is likely to be most pronounced in regions with strong offshore development activity, such as the North Sea, Gulf of Mexico, and Asia-Pacific. Partnerships between drive manufacturers, subsea robotics OEMs, and offshore operators will further accelerate technology adoption and drive incremental gains in performance and reliability.
Emerging Applications in Subsea Robotics
Variable frequency brushless vector drives (VFBVDs) are rapidly becoming a crucial enabling technology for next-generation subsea robotics as operators demand greater efficiency, precision, and reliability in increasingly challenging marine environments. In 2025, the deployment of these drives is accelerating, driven by advancements in power electronics, real-time control algorithms, and materials that withstand harsh subsea conditions. VFBVDs offer precise torque and speed control for brushless motors, which is particularly advantageous for remotely operated vehicles (ROVs), autonomous underwater vehicles (AUVs), and resident subsea intervention systems.
A key trend in 2025 is the integration of sensorless vector control within compact, pressure-tolerant drive modules. This approach reduces the need for external sensors, improving reliability and reducing maintenance—a priority for subsea operations where intervention is costly. Major subsea solutions providers such as Schneider Electric and ABB are refining subsea drive platforms to deliver higher power density and modularity, allowing operators to tailor propulsion and manipulation systems to mission requirements. These drives are increasingly paired with high-efficiency permanent magnet synchronous motors (PMSMs), providing optimized performance for variable load and speed profiles encountered during exploration, inspection, and intervention tasks.
Recent deployments emphasize the role of VFBVDs in resident subsea robotics—systems designed for long-term deployment at the seabed, often powered via subsea umbilicals or through local subsea power distribution grids. The reliability and energy efficiency of VFBVDs are critical for these applications, directly impacting operational costs and enabling new forms of persistent, autonomous operations. Companies like Baker Hughes have demonstrated subsea control and actuation systems leveraging advanced vector drive technologies for applications such as valve manipulation, hydraulic power units, and electric thrusters.
Industry outlook for the next few years points to continued adoption of VFBVDs as robotic payloads diversify and missions extend to deeper and more remote waters. There is a focus on digital integration, with leading players incorporating advanced diagnostics, remote monitoring, and predictive maintenance features via embedded connectivity. Siemens and TechnipFMC are among those exploring the use of digital twins for subsea drive systems, enhancing reliability and lifecycle management.
Overall, as the subsea robotics sector expands to address offshore energy, aquaculture, and infrastructure inspection, the performance gains offered by variable frequency brushless vector drives will be pivotal in achieving greater autonomy, safety, and efficiency. The near-term roadmap includes higher voltage designs, improved redundancy, and further miniaturization—ensuring VFBVDs remain central to subsea robotic innovation through the rest of the decade.
Competitive Landscape: Leading Manufacturers and Innovators
The competitive landscape for variable frequency brushless vector drives in subsea robotics is marked by a convergence of established industrial drive manufacturers and specialized subsea technology innovators. As of 2025, the sector is characterized by a blend of large multinational corporations leveraging their expertise in drives and automation, and niche players focused on the unique demands of the subsea environment—namely, high reliability, compactness, and robust sealing for deepwater operations.
Among the global leaders, Siemens AG maintains a significant footprint, leveraging its SINAMICS range of variable frequency drives (VFDs) that are often adapted for marine and subsea applications. Siemens, through ongoing advancements in vector control algorithms and modular drive system architectures, continues to address the specific requirements of remotely operated vehicles (ROVs) and autonomous underwater vehicles (AUVs), focusing on energy efficiency and precise torque control. Similarly, ABB Ltd is recognized for its ACS drives, which have seen integration into subsea robotics for mission-critical propulsion and manipulator functions. ABB’s emphasis on digitalization and remote diagnostics provides advantages in maintenance and lifecycle management.
Specialized subsea automation companies are also prominent in the competitive arena. Bosch Rexroth AG is investing in compact, pressure-tolerant electric drive solutions for deepwater tasks, a trend expected to intensify through 2025 as the industry seeks to replace hydraulic actuation with electric alternatives for improved efficiency and environmental safety. Saab Seaeye Ltd, a leading developer of electric ROVs, has been at the forefront of integrating brushless vector drives designed to withstand subsea pressures while delivering high dynamic response and fine motion control. Their adoption of advanced motor control electronics is shaping standards for next-generation underwater vehicles.
Another key player, Schneider Electric SE, is extending its Altivar line with models tailored for harsh marine environments, emphasizing modularity and remote configurability—critical for subsea deployments. The market is also witnessing increased collaboration between drive manufacturers and subsea system integrators, aiming to optimize the interface between power electronics, motors, and vehicle control systems.
Looking ahead, the competitive landscape is expected to be shaped by advancements in power density, reliability, and embedded intelligence within vector drives. Strategic investments in R&D, particularly in pressure-tolerant electronics and predictive maintenance features, are likely to differentiate the leading manufacturers through 2025 and beyond. As subsea robotics missions become more complex, the demand for customizable, high-performance drive solutions will remain a decisive factor in market leadership.
Technological Advancements & R&D Focus Areas
In 2025, technological advancements in variable frequency brushless vector drives (VFDs) are rapidly shaping the capabilities and reliability of subsea robotics. These drives, which precisely control the speed and torque of brushless motors, are critical for underwater vehicles and robotic manipulators operating in complex, high-pressure environments. Recent developments focus on several key areas: enhanced power density, improved reliability, integration with digital control systems, and expanded compatibility with wide-voltage subsea power networks.
Leading subsea robotics and drive manufacturers have prioritized the miniaturization and ruggedization of VFDs. Newer models boast increased power-to-size ratios, enabling more compact robotic designs without sacrificing performance. For example, firms such as Siemens and Schneider Electric are investing in robust encapsulation techniques and advanced thermal management solutions, allowing drives to withstand the corrosive and high-pressure subsea environment for extended periods.
Another major focus is digitalization and remote diagnostics. R&D teams are integrating advanced sensor arrays and real-time health monitoring into VFDs, leveraging edge computing and machine learning to predict component failures before they occur. This approach is championed by players like ABB, who are embedding condition monitoring and predictive maintenance features directly into their drive systems, supporting unmanned or remotely operated subsea missions with enhanced uptime and reduced operational risk.
Energy efficiency remains a crucial driver for innovation. R&D is targeting lower switching losses and more efficient power conversion, using silicon carbide (SiC) and gallium nitride (GaN) semiconductors in drive inverters. These technologies are being trialed by companies such as Hitachi and Yaskawa Electric Corporation, aiming to reduce total energy consumption and extend mission duration for battery-powered underwater vehicles.
The next few years are expected to see more open-architecture VFD platforms, facilitating seamless integration with emerging subsea communication protocols and autonomous control systems. Collaborative R&D projects between drive manufacturers and subsea robotics specialists are increasing, particularly in Europe and Asia-Pacific, to accelerate the adaptation of VFDs for deepwater and harsh-environment applications.
Overall, the outlook for 2025 and beyond points to more intelligent, resilient, and interoperable VFD solutions, directly supporting the expanding scope of subsea robotics in exploration, inspection, construction, and environmental monitoring.
Regulatory Standards and Industry Initiatives (e.g., ieee.org, asme.org)
The regulatory landscape and industry initiatives surrounding variable frequency brushless vector drives (VFBVDs) for subsea robotics are evolving rapidly as these components become integral to underwater vehicles and intervention systems. As of 2025, the focus remains on harmonizing safety, reliability, and interoperability standards to support increasingly complex subsea operations in energy, defense, and research sectors.
Leading international organizations, such as the IEEE and the ASME, are at the forefront of standards development relevant to VFBVDs. The IEEE’s ongoing work on standards like IEEE 1566, which outlines performance requirements for adjustable speed drives, is expected to see further adaptation for harsh subsea environments, reflecting the sector’s push for higher efficiency and robust fault tolerance. Additionally, efforts within the IEEE Petroleum and Chemical Industry Committee address the unique electrical and safety requirements of subsea robotics, including electromagnetic compatibility and insulation integrity under high pressure.
The ASME has increased its focus on subsea robotics through the development of mechanical and mechatronic standards applicable to pressure vessels, seals, and drive integration. Their initiatives, such as updates to codes for remote-operated and autonomous systems, emphasize the importance of integrating VFBVDs with safety-critical electronics and mechanical assemblies, aiming to mitigate risks of failure in deepwater missions.
In parallel, industry consortia and classification societies are pushing for interoperability and reliability benchmarks for drive technologies. The DNV (Det Norske Veritas) is actively collaborating with manufacturers to refine standards for electric motor drives and controls used in subsea robotics, reflecting the growing adoption of all-electric systems over hydraulic counterparts. DNV’s guidelines for qualification of new technology are influencing procurement and deployment decisions among leading offshore operators and OEMs.
Key industry players, including electric drive manufacturers and subsea system integrators, are contributing to joint industry projects (JIPs) aimed at validating VFBVD performance under realistic subsea conditions, with results feeding into future regulatory frameworks. There is a notable trend toward digitalization—standards under discussion now address cybersecurity for drive controllers, remote diagnostics, and predictive maintenance.
Looking ahead, regulatory harmonization is expected to accelerate, with cross-industry collaboration ensuring that standards keep pace with technological advances. The emphasis will remain on lifecycle reliability, energy efficiency, and safe integration of VFBVDs, with industry feedback loops fostering continuous improvement in both standards and compliance practices.
Challenges: Reliability, Integration, and Harsh Environment Performance
Variable frequency brushless vector drives are increasingly vital in subsea robotics, offering precise motor control and efficiency essential for operations at ocean depths. However, their deployment in such environments presents distinct challenges, particularly concerning reliability, integration, and performance under harsh conditions—issues which remain at the forefront for 2025 and the coming years.
Reliability is paramount, as subsea robotics are often deployed for extended missions where maintenance and retrieval are both costly and logistically complex. The primary challenge arises from the need to ensure continuous, fault-free operation of drives exposed to high pressure, corrosive saltwater, and extreme temperature gradients. Current industry leaders such as Siemens and Schneider Electric are investing heavily in ruggedization, with encapsulation techniques, advanced sealing, and pressure-compensated enclosures to mitigate water ingress and corrosion. Still, field reports from 2024 and early 2025 indicate that even with these measures, electrical failures due to micro-leakage and connector degradation remain significant concerns.
Integration of variable frequency brushless vector drives with the complex electromechanical architectures of modern subsea vehicles is another challenge. Robotics manufacturers such as Saab and TechnipFMC are pushing for modular drive units that can be easily interfaced with existing power and communication systems. Despite progress, issues persist regarding electromagnetic compatibility (EMC) and the need for robust communication protocols that can withstand subsea signal attenuation and interference. The trend for 2025 is toward fully integrated drive systems with embedded diagnostics, enabling predictive maintenance and reducing unscheduled downtime.
- Reliability remains threatened by saltwater corrosion and pressure-induced stress, especially at depths beyond 3000 meters.
- Connector technology and cable sealing are focus areas for innovation, as failures here are a leading cause of downtime.
- Drive manufacturers are partnering with subsea cable and connector specialists to co-develop solutions, as indicated by collaborations reported by ABB.
Looking ahead, the harsh environmental performance of these systems will depend on continued advancements in materials science and embedded system resilience. The increasing automation and autonomy of subsea vehicles by 2025 will further stress the need for self-monitoring drives capable of local fault mitigation. With the energy transition driving more offshore activity, there is a clear industry outlook for reinforced reliability standards, deeper integration, and smarter diagnostics that can collectively address the persistent challenges of subsea deployment.
Investment Trends & Strategic Partnerships
The landscape for investment and strategic partnerships in variable frequency brushless vector drives (VFDs) for subsea robotics is experiencing significant momentum as the offshore energy, defense, and marine research sectors intensify their focus on electrification, autonomy, and efficiency. In 2025, capital is increasingly directed toward enhancing the performance and reliability of VFD technologies tailored for harsh subsea conditions. Several leading marine automation and robotics firms are forming alliances with drive manufacturers to accelerate development cycles and address rising demand for advanced subsea robotic solutions.
Recent years have seen key players such as Siemens, ABB, and Schneider Electric increase investments in R&D and forge collaborations with subsea system integrators. For example, partnerships between drive manufacturers and remotely operated vehicle (ROV) suppliers are focusing on integrating compact, high-reliability VFDs with brushless vector control to enable precise maneuvering and energy savings in deepwater operations. The trend is particularly strong in regions with large offshore infrastructure, such as the North Sea and Gulf of Mexico, where investment in digitalization and electrification of subsea assets is a strategic priority.
Emerging subsea robotics companies are also attracting venture funding and forming joint ventures with established subsea equipment providers. In 2025, investments are being channeled into the miniaturization of VFDs, improved thermal management, and enhanced software control architectures—key factors for next-generation autonomous underwater vehicles (AUVs) and ROVs. Strategic collaborations are further reinforced by the push for all-electric subsea production systems, where variable frequency drive technology plays a pivotal role in reducing hydraulic components and maintenance costs.
Industry organizations, such as the Society of Petroleum Engineers and ROV Committee of the Marine Technology Society, have highlighted an uptick in cooperative R&D projects and pilot deployments involving VFD-based robotic platforms. These partnerships extend to academic institutions, leveraging public-private funding to address technical challenges such as high-reliability connectors and long-term system survivability.
Looking forward, the outlook for investment and partnership formation in this sector remains robust through the next few years. The ongoing energy transition, increased offshore wind activity, and the expansion of deep-sea mining are expected to further catalyze funding and collaborative innovation in variable frequency brushless vector drives for subsea robotics. As the drive toward autonomous and remotely operated subsea systems continues, strong synergies between VFD technology developers, robotics OEMs, and end-users are anticipated to intensify, shaping the future trajectory of the subsea robotics market.
Future Outlook: Disruptive Trends and Long-Term Opportunities
The future landscape for variable frequency brushless vector drives (VFDs) in subsea robotics is marked by rapid technological advancement and growing market demand, particularly as offshore energy, scientific exploration, and defense sectors continue to prioritize underwater autonomy and reliability. In 2025 and beyond, several disruptive trends are shaping the adoption and evolution of these drives.
One of the most significant trends is the integration of advanced power electronics and digital control algorithms, enabling higher efficiency and precision in subsea electric propulsion and actuation. Key manufacturers are implementing silicon carbide (SiC) and gallium nitride (GaN) semiconductors, which offer superior performance in harsh environments due to their higher voltage tolerance, thermal stability, and compact form factors. For example, Siemens and Schneider Electric are enhancing their industrial drive portfolios with these technologies, aiming to reduce system size and weight—crucial advantages for remotely operated vehicles (ROVs) and autonomous underwater vehicles (AUVs).
Another disruptive trend is the increased adoption of integrated vector control and predictive maintenance features. Using embedded sensors and digital twins, VFDs are now capable of real-time diagnostics and adaptive control, significantly reducing unplanned downtime and optimizing performance throughout the mission life cycle. Companies such as ABB are focusing on smart drive solutions tailored for the subsea sector, leveraging condition monitoring and cloud connectivity to support remote operations and maintenance.
Electrification of subsea systems is accelerating, driven by the push for decarbonization and the expansion of deepwater renewable energy projects. The demand for all-electric subsea processing and intervention systems is resulting in new opportunities for compact, high-reliability brushless vector drives. Major subsea technology suppliers, including Baker Hughes and TechnipFMC, are actively developing next-generation electric actuation and propulsion platforms that rely on VFDs for precise torque and speed control in dynamic underwater conditions.
Looking ahead, the convergence of artificial intelligence with VFDs is expected to further revolutionize subsea robotics. AI-driven control strategies promise to improve energy efficiency, fault tolerance, and autonomous decision-making, enabling complex missions in deeper and more challenging environments. The ongoing collaboration between drive manufacturers, subsea integrators, and research institutions will be pivotal in realizing these advancements.
Overall, the next few years are set to witness accelerated adoption of variable frequency brushless vector drives in subsea robotics, underpinned by innovations in materials, digitalization, and system integration. These developments will unlock new operational capabilities and long-term opportunities across offshore energy, marine research, and defense sectors.