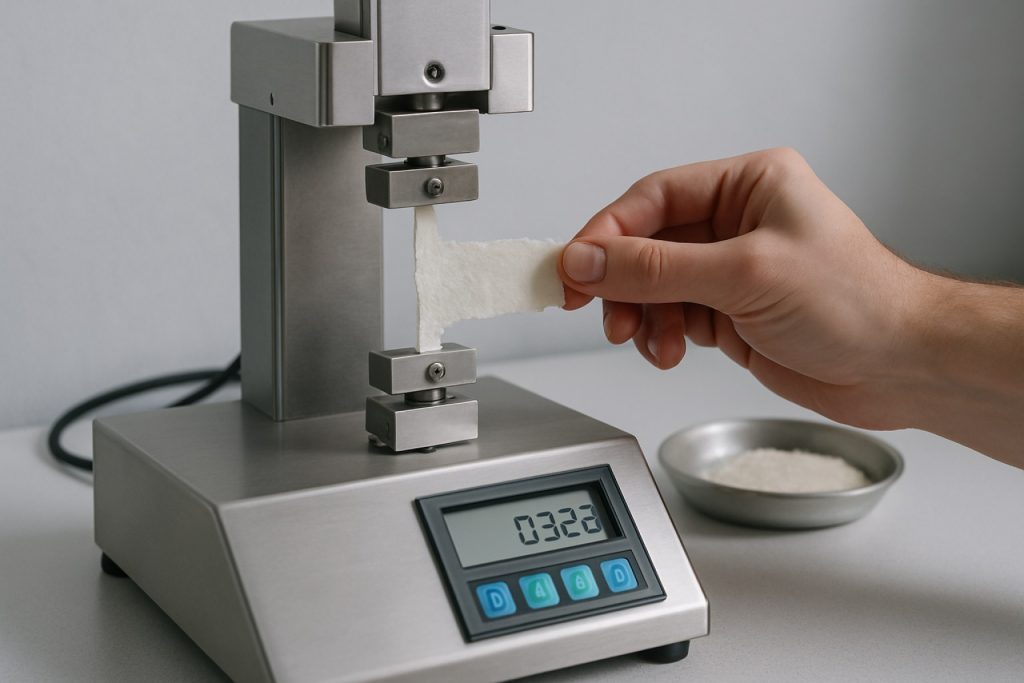
Wet-Tensile Pulp Testing Instrumentation in 2025: The Surprising Tech Shifts and Market Leaders Shaping Paper Quality for the Next 5 Years
- Executive Summary: The State of Wet-Tensile Pulp Testing in 2025
- Market Size & Growth Forecast to 2030
- Key Players: Manufacturers & Innovators (e.g., lorentzen-wettre.com, emcopapertesting.com, messmerbuchel.com)
- Emerging Technologies & Automation Trends
- Regulatory Standards & Compliance: ISO, TAPPI, and Global Bodies
- Adoption Drivers: Sustainability, Digitalization, and Industry 4.0
- Regional Analysis: Hotspots of Demand and Investment
- Competitive Landscape: Pricing, Differentiation, and Strategic Moves
- Customer Perspectives: Priorities of Pulp & Paper Producers
- Future Outlook: Disruptive Innovations, Challenges, and Opportunities
- Sources & References
Executive Summary: The State of Wet-Tensile Pulp Testing in 2025
Wet-tensile pulp testing instrumentation, a core component in the quality assurance processes of the global pulp and paper industry, is experiencing a period of incremental advancement as of 2025. The sector, historically driven by regulatory standards and the need for consistent product performance, is witnessing enhancements in automation, precision, and data integration. Key industry players are responding to the dual demands for higher testing throughput and more robust data management, reflecting broader digitalization trends across manufacturing.
Instrument manufacturers such as Metrohm, Mecmesin, and ZwickRoell continue to dominate the wet-tensile testing market, offering a variety of automated and semi-automated systems tailored for pulp and paper laboratories. Their devices are engineered to comply with international standards, such as ISO 3781 and TAPPI T456, ensuring results are globally comparable. Recent product generations have focused on improving the repeatability and reliability of measurements, with features such as closed-loop force control, high-precision load cells, and intuitive touchscreen interfaces.
One trend accelerating in 2025 is the integration of laboratory testing equipment into digital laboratory information management systems (LIMS). Companies like Mecmesin and ZwickRoell are actively enhancing software connectivity, enabling real-time data transfer and analysis, which supports both internal quality control and external compliance reporting. This digital shift not only reduces human error but also facilitates faster, data-driven decision-making across production lines.
Regional differences remain notable. In North America and Europe, demand is driven by strict regulatory compliance and the push for sustainability, encouraging investment in high-end, automated instruments. Meanwhile, Asia-Pacific manufacturers continue to expand their presence, offering competitively priced, robust solutions aimed at the growing number of pulp and paper mills in China, India, and Southeast Asia. Companies such as Labthink Instruments are notable in this space, providing a wide range of physical testing equipment, including wet-tensile testers, for both domestic and export markets.
Looking ahead, the outlook for wet-tensile pulp testing instrumentation is one of steady, technology-driven evolution. While no disruptive breakthroughs are anticipated in core measurement principles over the next few years, incremental advances in automation, connectivity, and user experience are expected. Environmental considerations—such as reduced water and energy usage during testing—may also shape future instrumentation design as sustainability becomes an even greater industry focus. Overall, the sector is set to remain a vital, if understated, enabler of quality and innovation in pulp and paper manufacturing through 2025 and beyond.
Market Size & Growth Forecast to 2030
The market for wet-tensile pulp testing instrumentation is experiencing steady expansion in 2025, supported by continued global demand for quality assurance and process optimization in pulp and paper production. Wet-tensile testing—which measures the strength of pulp and paper products when saturated—remains a critical parameter for manufacturers of packaging, tissue, and specialty papers. As sustainability standards and performance expectations rise, the need for precise, reliable testing equipment is intensifying across major markets in the Americas, Europe, and Asia-Pacific.
In 2025, the market size for wet-tensile pulp testing instrumentation is estimated to be in the high tens of millions USD globally, with mid-single-digit annual growth rates projected through 2030. This reflects not only organic growth in the pulp and paper sector but also increasing adoption of automated, digitalized testing systems. Key market drivers include the modernization of legacy mills, the emergence of bio-based packaging solutions, and stricter regulatory frameworks regarding product safety and recyclability.
Prominent manufacturers such as Koehler Instrument Company, Lorentzen & Wettre (now part of ABB), and I.M.A Srl are intensifying their R&D investments to deliver instruments with enhanced automation, user-friendly interfaces, and advanced analytics. Koehler Instrument Company remains recognized for its robust wet-tensile testers, catering to both research laboratories and industrial settings. Lorentzen & Wettre, under the umbrella of ABB, leverages data integration capabilities to offer end-to-end pulp testing solutions, integrating wet-tensile measurement with broader quality control systems. I.M.A Srl continues to serve European and global customers with specialized testing instruments for pulp and paper analysis.
Geographically, Asia-Pacific leads in both installed base and incremental demand for wet-tensile testing equipment, reflecting rapid infrastructure development and rising paper consumption in China, India, and Southeast Asia. Europe and North America maintain strong replacement and upgrade cycles, driven by sustainability targets and the transition to greener packaging alternatives.
Looking ahead to 2030, digital transformation and Industry 4.0 trends are expected to reshape the market. The integration of wet-tensile testing devices with plant-wide digital ecosystems and cloud-based quality management platforms is anticipated to unlock new value streams for mills seeking real-time process optimization. As a result, the global market is anticipated to sustain or slightly accelerate its growth trajectory, with leading instrumentation providers poised to capture demand through innovation and service expansion.
Key Players: Manufacturers & Innovators (e.g., lorentzen-wettre.com, emcopapertesting.com, messmerbuchel.com)
The landscape of wet-tensile pulp testing instrumentation in 2025 is characterized by the consolidation of established manufacturers, new product developments, and the integration of automation and digitalization. Wet-tensile testing remains a critical quality parameter for pulp and paper producers, influencing end-use performance, process optimization, and compliance with global standards. The sector is led by a handful of specialized manufacturers with global reach, each contributing to innovation and reliability in laboratory and production settings.
One of the most prominent players is Lorentzen & Wettre, part of the ABB Group. With a legacy spanning over a century, the company is recognized for its robust, automated testing solutions. Their wet-tensile testers are widely adopted in both R&D and quality control labs, valued for standardized measurements and compatibility with evolving digital laboratory management systems. Recent product generations emphasize automated sample handling and data integration, aligning with the industry’s push toward Industry 4.0.
Another significant contributor is EMCO Elektronische Mess- und Steuerungstechnik GmbH. EMCO focuses on high-precision, user-friendly laboratory equipment dedicated specifically to paper and pulp testing. Their wet-tensile testers are noted for precise force measurement, repeatability, and compliance with international test standards such as ISO 3781. EMCO’s emphasis on modularity enables tailored solutions for diverse customer requirements, and the company is actively expanding its digital interface offerings for real-time data analysis.
Messmer Büchel, a division of Industrial Physics, is a key innovator in this space. The company is renowned for its comprehensive line of pulp and paper testing instruments, including advanced wet-tensile testers that integrate intuitive touchscreen controls and automated water-immersion mechanisms. Messmer Büchel’s focus on user experience and testing throughput has positioned it as a preferred supplier for both high-volume mills and research institutions.
Emerging trends among these manufacturers include increased automation of the sample soaking and loading processes, direct cloud connectivity for test data, and the use of AI-based analytics for predictive maintenance and process optimization. The next few years are expected to see further integration of these systems into broader mill digital ecosystems, as well as a focus on sustainability—such as reducing water and energy consumption during testing.
Other relevant suppliers, such as PTI Paper Testing Instruments, are also enhancing their portfolios with digital upgrades and modular solutions, reflecting the broader industry’s commitment to adaptability and future-proofing. As global demand for higher quality and sustainability in paper products rises, these key players are set to drive the evolution of wet-tensile pulp testing instrumentation well into the next decade.
Emerging Technologies & Automation Trends
The landscape of wet-tensile pulp testing instrumentation is undergoing significant transformation in 2025, as paper and pulp manufacturers prioritize automation, digital integration, and data-driven quality control. Historically, wet-tensile testing—the measurement of paper and pulp strength when wet—relied on semi-automatic machines and manual sample preparation. As demand rises for higher operational efficiency and more reproducible results, leading instrumentation companies are investing in next-generation solutions that emphasize connectivity, automation, and user-centric design.
A notable trend is the adoption of fully automated wet-tensile testers by major equipment manufacturers. Companies like Lorentzen & Wettre (a division of ABB), ABB, and Papiertechnische Stiftung (PTS) are integrating robotic sample handling, auto-alignment, and real-time digital feedback into their systems. For instance, Lorentzen & Wettre’s latest wet-tensile testers feature automated sample clamping and programmable test sequences, reducing human error and increasing throughput. Such innovations are especially relevant as mills aim for higher sampling frequencies to enable faster process adjustments and minimize waste.
Another major development involves connectivity and digitalization. Modern instruments now offer seamless integration with mill-wide quality management and Manufacturing Execution Systems (MES). This allows live streaming of test data, remote diagnostics, and predictive maintenance scheduling. ABB has been at the forefront, providing solutions where wet-tensile data are instantly available for process control, supporting closed-loop optimization. These systems not only streamline compliance with international standards (such as ISO 3781 and TAPPI T456) but also enable better traceability and data analytics for continuous improvement.
Sensor and actuator improvements are also reshaping the field. Enhanced load cell sensitivity and faster feedback loops allow for more precise measurement and better repeatability, even in challenging high-humidity environments. Companies like Mecmesin and AMETEK (through their Materials Testing division) have introduced modular systems that can be updated with the latest sensors and software, future-proofing capital investments for pulp and paper companies.
Looking ahead, the next few years are expected to bring even greater integration of artificial intelligence and machine learning for anomaly detection and process optimization. As mills invest in Industry 4.0 and digital transformation, wet-tensile testers will increasingly function as nodes in interconnected quality networks, supporting both sustainability targets and competitive efficiency. The sector’s outlook is one of rapid technological adoption, with global suppliers and innovative niche firms alike shaping the pace of modernization in wet-tensile pulp testing instrumentation.
Regulatory Standards & Compliance: ISO, TAPPI, and Global Bodies
The landscape of wet-tensile pulp testing instrumentation is deeply influenced by evolving regulatory standards and compliance mandates set by international organizations such as the International Organization for Standardization (ISO) and the Technical Association of the Pulp and Paper Industry (TAPPI). In 2025 and the coming years, these standards are central to ensuring quality, safety, and market access for pulp, paper, and related products.
ISO standard 1924, which specifies test methods for the determination of tensile properties of paper and board, remains a cornerstone in wet-tensile testing protocols. The standard requires precise instrumentation capable of delivering consistent tension, accurate force measurement, and reliable data capture under controlled moisture conditions. Companies manufacturing instrumentation must ensure their devices are validated against the most current revision of this ISO standard to maintain global market eligibility.
Similarly, TAPPI standards such as T456 and T494 provide detailed protocols for wet and dry tensile testing, widely adopted by pulp and paper producers, especially in North America and Asia-Pacific. TAPPI’s regular updates to these methods, in response to technological advances and industry feedback, drive continuous innovation in instrumentation. Compliance with these standards is often a prerequisite for suppliers to engage with major manufacturers and converters in the sector.
Instrumentation suppliers such as Koehler Instrument Company and Lorentzen & Wettre (a brand of ABB) are prominent in aligning their wet-tensile testers with these international standards. These companies invest in regular calibration, software updates, and participation in round-robin testing organized by standards bodies to ensure their systems deliver traceable and reproducible results.
In the near term, regulatory bodies are expected to place greater emphasis on digital traceability, data integrity, and automated compliance documentation. This will encourage further integration of smart sensors and cloud connectivity in wet-tensile testing platforms. The move aligns with broader trends in Industry 4.0 and the push for sustainability, as regulatory frameworks increasingly require transparent reporting of test results for certification and environmental labeling.
Global harmonization of test standards remains a strategic focus for organizations like ISO and TAPPI, aiming to reduce technical barriers to trade and facilitate acceptance of test results across jurisdictions. This presents both a challenge and an opportunity for manufacturers of wet-tensile testing equipment, who must stay agile to adapt to evolving compliance landscapes while leveraging unified standards to expand into new markets.
Adoption Drivers: Sustainability, Digitalization, and Industry 4.0
The adoption of wet-tensile pulp testing instrumentation is accelerating in 2025, driven by a convergence of sustainability imperatives, digital transformation, and Industry 4.0 strategies across the pulp and paper industry. These instruments, which assess the mechanical strength of wet pulp and paper materials, are central to both quality assurance and process optimization.
Sustainability is a major impetus. Pulp and paper producers are under increasing regulatory and consumer pressure to reduce waste, minimize raw material usage, and certify the recyclability and durability of their products. Wet-tensile testing provides critical data for optimizing fiber blends and refining processes to achieve stronger products with fewer resources. Companies such as Lorentzen & Wettre (part of ABB), known for their advanced wet-tensile and fiber testing systems, are seeing increased demand as mills seek to document product performance for sustainability certifications and life-cycle assessments.
Digitalization is also reshaping the landscape. Modern wet-tensile testers now integrate with laboratory information management systems (LIMS) and production control software, enabling real-time data collection, automated reporting, and faster feedback loops for process adjustments. Key manufacturers such as Innventia (now part of RISE Research Institutes of Sweden) and Papiertechnische Stiftung (PTS) offer digital-enabled solutions that interface seamlessly with broader mill IT infrastructure. This connectivity supports traceability, remote monitoring, and predictive analytics, which are increasingly demanded by mill operators.
Industry 4.0 strategies—encompassing automation, IoT, and smart manufacturing—are further propelling the uptake of advanced wet-tensile testing instrumentation. Sensors embedded in new-generation testers allow for automated sample handling, calibration, and even self-diagnosis, minimizing downtime and labor costs. Global suppliers such as Metso (which includes Valmet as a major division) have expanded their digital service portfolios to include online and at-line wet-tensile measurement, facilitating continuous quality control directly on production lines.
Looking ahead, the outlook for wet-tensile pulp testing instrumentation is robust. The next few years are likely to see further integration of artificial intelligence for anomaly detection and process optimization, as well as the development of more compact, energy-efficient devices. As the industry continues to prioritize sustainable practices and digital transformation, companies capable of delivering smart, connected, and environmentally friendly testing solutions are expected to lead the market.
Regional Analysis: Hotspots of Demand and Investment
Wet-tensile pulp testing instrumentation is a specialized segment within the broader pulp and paper testing equipment market, playing a critical role in quality control for tissue, specialty, and packaging paper grades. As of 2025, demand for such instrumentation is characterized by strong regional variation, driven by industrial modernization, regulatory compliance, and the geographic distribution of pulp and paper production.
Asia-Pacific remains the undisputed hotspot for demand and investment, underpinned by the region’s dominant share in global pulp and paper manufacturing. China, India, and Southeast Asian nations are intensifying investments in automated and precise testing equipment to support rising exports and to meet both domestic and international quality standards. Key local manufacturers and global suppliers are expanding their footprints and distribution channels to cater to this demand surge. For instance, TMI Group and Lorentzen & Wettre (a division of ABB) have increased their engagement with Asian mills, offering advanced wet-tensile testers compatible with Industry 4.0 integration.
Europe is another significant region, with Scandinavia—especially Sweden and Finland—acting as a technological nucleus. The emphasis here is on automation, sustainability, and compliance with strict EU environmental and product standards. Nordic companies are both large buyers and innovators: Metsä Group and UPM-Kymmene Corporation are known for investing in cutting-edge laboratory and process testing systems, often collaborating with instrument suppliers to develop customized solutions for wet-tensile strength analysis.
North America, led by the United States and Canada, is a mature but steadily evolving market. The focus in 2025 is on upgrading legacy mills with modern, digitally connected instrumentation to boost efficiency, enhance reporting, and maintain competitiveness. Suppliers such as International Paper and FPInnovations (a major Canadian R&D institute) work closely with manufacturers to pilot and validate next-generation wet-tensile testing technologies.
Other emerging hotspots include Brazil (within Latin America), where large integrated pulp producers such as Suzano are investing in advanced quality control laboratories as part of facility expansions. Similarly, Turkey and Russia are witnessing investment in testing instrumentation, driven by export ambitions and modernization of domestic mills.
Looking ahead, regional demand and investment in wet-tensile pulp testing instrumentation will increasingly mirror broader trends in pulp and paper production modernization, with Asia-Pacific maintaining its lead, Europe pushing the envelope on automation and sustainability, and North America focusing on digital upgrades and compliance.
Competitive Landscape: Pricing, Differentiation, and Strategic Moves
The competitive landscape for wet-tensile pulp testing instrumentation in 2025 is characterized by a handful of established global manufacturers, ongoing product differentiation, and shifting pricing strategies aligned with technological and market developments. This segment of materials testing equipment is vital for the pulp and paper industry, as wet-tensile strength is a key performance indicator for paper quality and process optimization.
Leading suppliers include Instron, Thwing-Albert Instrument Company, Toni Technik, and Koehler Instrument Company. These companies supply a range of automated and semi-automated wet-tensile testers, designed for laboratory and quality control environments.
Pricing remains a critical factor in the competitive landscape. Entry-level, bench-top wet-tensile testers generally start at several thousand USD, while high-throughput, fully automated systems can range up to tens of thousands of dollars, depending on features such as load cell precision, automation, data integration, and software analytics. Manufacturers are increasingly offering modular systems, enabling customers to add functionality as needed and thus optimizing price/performance ratios.
Differentiation strategies focus on several axes:
- Automation and Throughput: Companies like Instron and Thwing-Albert Instrument Company are emphasizing automated sample handling, integrated wetting stations, and batch processing to reduce errors and boost productivity.
- Data Integration: Enhanced connectivity with laboratory information management systems (LIMS) and digital analytics platforms is a growing feature, supporting traceability and statistical process control—important for customers optimizing manufacturing lines or complying with tighter regulatory requirements.
- Precision and Compliance: Adherence to international standards (ISO, TAPPI) is a baseline, with some vendors offering precision improvements (e.g., higher load cell resolutions, real-time environmental compensation) to differentiate in quality-sensitive markets.
- Customization: Modular accessories and software options, such as variable sample holders and test protocols, are being promoted to address niche applications (e.g., specialty papers, nonwovens, or bio-based pulps).
Strategic moves in the sector include partnerships with pulp and paper producers to co-develop application-specific solutions, as well as investments in digitalization (IoT-enabled instruments, cloud-based data management). Notably, companies like Instron have signaled ongoing R&D aimed at smarter, more autonomous testing platforms.
Looking forward, pricing pressure is anticipated as new entrants—particularly from Asia—target cost-sensitive segments with basic models, while established players double down on advanced features and service bundles. The overall outlook is for continued innovation and segmentation, with competitive dynamics shaped by both technological advances and shifting end-user demands.
Customer Perspectives: Priorities of Pulp & Paper Producers
In 2025, customer perspectives in the pulp and paper sector are increasingly shaped by the growing demand for precision, automation, and data connectivity in wet-tensile pulp testing instrumentation. Wet-tensile strength remains a critical quality parameter, directly influencing end-product performance in applications such as packaging, specialty papers, and hygiene products. As global producers seek to enhance product consistency, reduce waste, and maintain compliance with international standards, their priorities are reflected in the latest procurement and operational strategies for wet-tensile testing equipment.
One major priority is the reliability and repeatability of measurement results. Producers expect testing instruments to deliver high-precision data with minimal operator influence. This has led to widespread adoption of automated and semi-automated wet-tensile testers in modern laboratories. Companies such as ABB and Metso (Valmet), both recognized for their advanced process automation solutions, are expanding their offerings to include integrated testing systems that can seamlessly link laboratory data to mill-wide quality control platforms. Customers value these solutions for their ability to provide real-time feedback for process adjustments, helping to optimize pulp refining and improve overall product strength.
Another growing priority is digital connectivity and data management. Producers are requesting instruments equipped with advanced software interfaces, capable of supporting Industry 4.0 initiatives through cloud connectivity and remote diagnostics. For example, ABB’s focus on digital transformation in the pulp and paper industry includes secure, networked laboratory devices that allow for centralized data analysis and support predictive maintenance. This aligns with the sector’s drive toward smart manufacturing, where test data is increasingly used to guide operational decisions across the value chain.
Sustainability and efficiency are also at the forefront of customer concerns. As mills strive to reduce energy and chemical consumption, precise wet-tensile testing is essential for optimizing pulp blends and refining conditions. Instruments that offer fast test cycles and require minimal sample preparation are preferred, as they help minimize laboratory waste and resource use. Companies like Lorentzen & Wettre (part of ABB) are recognized for delivering such solutions, focusing on ease of use and environmental responsibility.
Looking ahead, the next few years are expected to see continued emphasis on automation, digital integration, and sustainability in wet-tensile testing instrumentation. Producers will likely prioritize vendors who can demonstrate robust after-sales support, regular software updates, and compatibility with evolving regulatory standards. As the industry advances, customer perspectives will continue to shape product innovations, driving suppliers to deliver ever-more reliable, connected, and sustainable testing solutions.
Future Outlook: Disruptive Innovations, Challenges, and Opportunities
The landscape for wet-tensile pulp testing instrumentation is poised for notable transformation in 2025 and the following years, driven by innovations in automation, digital integration, and sustainability demands from the pulp and paper industry. Wet-tensile testing remains a critical process for evaluating the mechanical properties and quality of pulp products under wet conditions, which directly impacts product performance in end-use applications such as tissue, specialty papers, and packaging.
One of the most significant trends is the rapid adoption of automated, digitally connected testing systems. Market leaders like Lorentzen & Wettre (a brand of ABB), Koehler Innovation & Technology, and IMA Tec have advanced wet-tensile testers with integrated data management, automated sample handling, and remote diagnostics. These platforms not only boost testing throughput and accuracy but also facilitate seamless integration with mill-wide quality control systems, aligning with the growing emphasis on Industry 4.0 and real-time process optimization.
A parallel innovation thread concerns the incorporation of advanced sensors and artificial intelligence (AI). Companies such as Metso and ABB are exploring sensor technologies that enable non-destructive, continuous wet-tensile strength monitoring directly on production lines. AI-driven analytics promise predictive maintenance and even in-line adjustment of process parameters, reducing downtime and material waste while supporting traceability and compliance with increasingly stringent quality standards.
Sustainability and circular economy pressures are also shaping the outlook. Instrument manufacturers are responding by designing more energy-efficient devices and supporting testing of new sustainable pulp compositions, including alternative fibers and recycled content. As the push for eco-friendly paper and packaging accelerates, the need for reliable wet-tensile measurements on non-traditional pulp materials will spur further adaptation and innovation in instrumentation.
Despite these advancements, challenges remain. Standardization of test protocols for novel pulp types, ensuring compatibility with legacy mill infrastructure, and the upskilling of technical personnel to operate and interpret results from advanced systems are persistent concerns. However, ongoing collaborations between equipment manufacturers, industry consortia, and standards bodies such as TAPPI are expected to address many of these barriers.
Looking forward, the wet-tensile pulp testing sector is likely to see continued convergence of automation, digital intelligence, and sustainability-driven innovation. This will create new opportunities for both established providers and agile entrants, ultimately enabling the pulp and paper industry to meet the evolving demands of global markets.
Sources & References
- Metrohm
- Mecmesin
- ZwickRoell
- Labthink Instruments
- Messmer Büchel
- AMETEK
- TAPPI
- TMI Group
- Metsä Group
- UPM-Kymmene Corporation
- International Paper
- Suzano
- Thwing-Albert Instrument Company
- IMA Tec