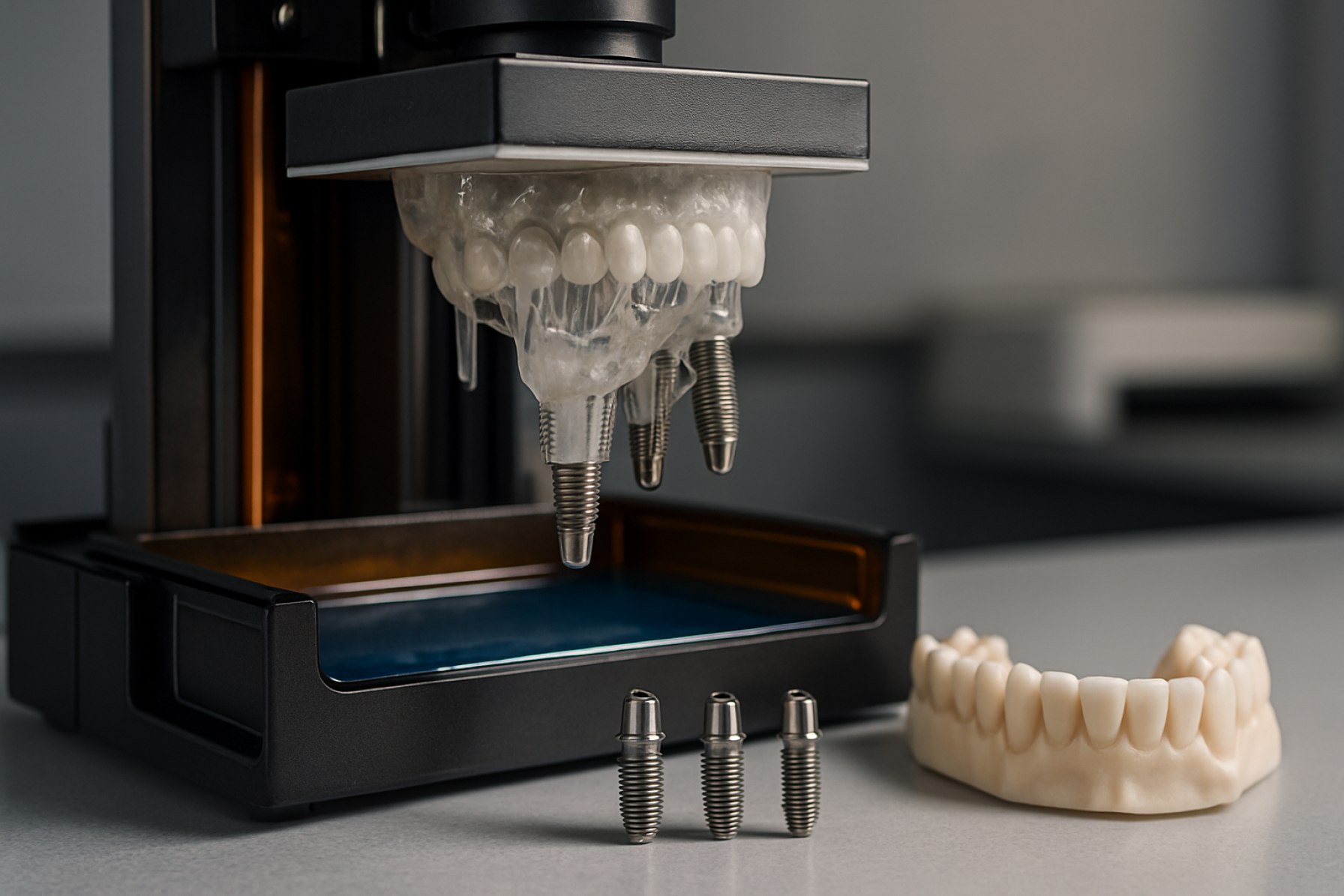
Inhaltsverzeichnis
- Zusammenfassung: Marktübersicht 2025 & Schlüsseltreiber
- Additive Lithographie erklärt: Technologieübersicht & Kernprinzipien
- Aktuelle Branchenakzeptanz: Führende Unternehmen und Innovatoren (z.B. straumann.com, 3dsystems.com, eos.info)
- Durchbrüche in der Herstellung von Zahnimplantaten: Verbesserte Genauigkeit, Anpassungsfähigkeit und Biokompatibilität
- Marktprognosen (2025–2030): Wachstumsprognosen, regionale Hotspots und Umsatzschätzungen
- Reg regulatorische Landschaft & Standards: Compliance- und Zertifizierungsherausforderungen
- Workflow-Integration: Von digitalen Scans zur Implantatproduktion am Behandlungsstuhl
- Wettbewerbsanalyse: Traditionelle Fertigung vs. additive Lithographie
- Zukünftige Perspektiven: Next-Gen Materialien, KI-Integration und Automatisierung
- Strategische Einblicke & Empfehlungen für Stakeholder in der dentalen additiven Lithographie
- Quellen & Referenzen
Zusammenfassung: Marktübersicht 2025 & Schlüsseltreiber
Die additive Lithographie, ein Teilbereich der additiven Fertigung, der Photopolymerisationsverfahren für präzise Schicht-für-Schicht-Herstellung verwendet, treibt den Sektor der Zahnimplantate bis 2025 rasch voran. Diese Technologie ermöglicht die Produktion von hochgradig angepassten, komplexen Zahnimplantaten mit verbesserter Präzision und schnelleren Durchlaufzeiten im Vergleich zu herkömmlichen subtraktiven und Gießmethoden. Der globale Markt für Zahnimplantate verzeichnet ein robustes Wachstum, angetrieben von einer älter werdenden Bevölkerung, einem steigenden Bedarf an ästhetischen und funktionalen zahnärztlichen Restaurationen und der Verbreitung digitaler Zahnmedizin-Workflows.
Im Jahr 2025 integrieren führende Unternehmen der Zahntechnologie additive Lithographie in ihre Produktionspipelines sowohl für Prototypen als auch für Endanwendungen von Zahnimplantaten. Zum Beispiel hat die Straumann Group ihre digitalen Fertigungskapazitäten erweitert und nutzt additive Lithographie, um patientenspezifische Abutments und Kronen mit verbesserter Passgenauigkeit und Haltbarkeit zu produzieren. Ähnlich hat Dentsply Sirona fortschrittliche Photopolymerisationssysteme in ihren Zahnlaboren integriert, um die Herstellung von implantatgetragenen Restaurationen zu optimieren, wobei schnellerer Versand und reproduzierbare Qualität betont werden.
Zu den wichtigsten Markttreibern im Jahr 2025 zählt die fortlaufende Evolution der Integration digitaler Workflows, die einen nahtlosen Übergang vom intraoralen Scannen zum virtuellen Design und zur additiven Fertigung ermöglicht. Die Fähigkeit der additiven Lithographie, komplizierte Geometrien – wie poröse Strukturen, die die Osseointegration fördern – herzustellen, verschafft den Herstellern einen Wettbewerbsvorteil. Unternehmen wie 3D Systems entwickeln sich bei Harzformulierungen, die speziell auf Anwendungen im Bereich Zahnimplantate ausgerichtet sind, und konzentrieren sich auf Biokompatibilität und mechanische Festigkeit zur Erfüllung strenger regulatorischer Standards.
Die Akzeptanz wird auch durch eine zunehmende regulatorische Klarheit gefördert. Die U.S. Food and Drug Administration (FDA) hat Richtlinien für 3D-gedruckte zahnärztliche Geräte erstellt, was zu beschleunigten Genehmigungen und breiterer klinischer Akzeptanz führt (U.S. Food & Drug Administration). Diese regulatorische Unterstützung hat Investitionen in Geräte und Schulungen zur additiven Lithographie durch Zahnärztliche Dienstleister und Laboratorien gefördert.
In den kommenden Jahren wird erwartet, dass die Produktionskosten weiter sinken und die Materialleistung verbessert wird, angetrieben durch fortlaufende F&E-Initiativen der Branchenführer. Die Konvergenz von KI-gesteuerter Designoptimierung mit additiver Lithographie steht kurz davor, Zahnimplantate weiter zu personalisieren, während die dezentralisierte Herstellung in Kliniken immer verbreiteter wird, da die Systemkosten sinken und sich die Benutzeroberflächen verbessern. Daher ist die additive Lithographie nicht nur als technologischer Treiber positioniert, sondern auch als grundlegender Ermöglicher der digitalen Transformation des Marktes für Zahnimplantate bis 2025 und darüber hinaus.
Additive Lithographie erklärt: Technologieübersicht & Kernprinzipien
Die additive Lithographie, auch bekannt als additive Fertigung (AM) Lithographie, stellt einen transformativen Ansatz in der Herstellung von Zahnimplantaten dar, indem sie den präzisen schichtweisen Bau komplexer Geometrien ermöglicht. Im Gegensatz zu herkömmlichen subtraktiven Techniken, bei denen Material von einem Massesubstrat entfernt wird, nutzt die additive Lithographie digitale Entwurfsdateien, um Photopolymerisation oder Sintern zu steuern, was zu hochgradig angepassten und patientenspezifischen zahnmedizinischen Komponenten führt. Diese Methode umfasst eine Reihe von Technologien, einschließlich Stereolithographie (SLA), digitale Lichtverarbeitung (DLP) und Zwei-Photonen-Polymerisation, die alle fokussierte Lichtquellen nutzen, um Material selektiv zu härten oder zu verbinden.
Im Kontext der Zahnimplantologie ermöglicht die additive Lithographie die Herstellung von Kronen, Brücken, Abutments und sogar gesamten implantatgetragenen Prothesen mit beispielloser Genauigkeit. Der Kernworkflow beginnt mit intraoralen oder extraoralen Scans, um die Anatomie des Patienten zu erfassen, gefolgt von einem computerunterstützten Design (CAD) des Implantats oder der Restauration. Die digitale Datei wird dann an ein System zur additiven Lithographie übertragen, das die Struktur schrittweise mit biokompatiblen Harzen oder zunehmend mit keramischen und Metallpulvern aufbaut. Dies ermöglicht die Herstellung von Implantaten mit komplexen inneren Kanälen, mikroskopischen Oberflächenstrukturen zur Osseointegration und maßgeschneiderter Passform – alles entscheidend für langfristigen klinischen Erfolg.
Bis Anfang 2025 haben führende Hersteller von zahnmedizinischen Geräten fortschrittliche Plattformen der additiven Lithographie kommerzialisiert, die in der Lage sind, Präzision im Mikrometerbereich zu erreichen. Beispielsweise bietet Formlabs Desktop-SLA- und DLP-Drucker an, die in Zahnlaboren weit verbreitet sind, um schnelle Prototypen und direkte Produktionen von chirurgischen Führungen und temporären Kronen zu ermöglichen. Ebenso haben Stratasys und 3D Systems professionelle Systeme eingeführt, die permanente zahnmedizinische Komponenten drucken und validierte Materialien verwenden, die den regulatorischen Standards entsprechen.
Das zugrunde liegende Kernprinzip – die kontrollierte lichtinduzierte Polymerisation – ermöglicht den Bau von dichten, glatten und mechanisch robusten Restaurationen. Fortschrittliche Softwarealgorithmen optimieren zudem die Druckausrichtung und die Unterstützungsstruktur, minimieren die Anforderungen an die Nachbearbeitung und den Materialabfall. Darüber hinaus erleichtert die additive Lithographie die Integration digitaler Workflows in zahnmedizinischen Praxen und beschleunigt die Durchlaufzeiten vom Abdruck bis zur endgültigen Implantatplatzierung.
In den nächsten Jahren erwarten Stakeholder der Branche weiterhin Verbesserungen in Druckgeschwindigkeit, Materialvielfalt (einschließlich bioaktiver und antimikrobieller Harze) und der direkten Druckfähigkeit von finalen Implantatkomponenten. Mit fortlaufender Forschung und Validierung durch Organisationen wie Dentsply Sirona und EnvisionTEC (jetzt Teil von Desktop Metal) steht die additive Lithographie kurz davor, die Zahnimplantologie weiter zu revolutionieren – mit verbesserten Patientenergebnissen durch größere Personalisierung und effiziente, bedarfsgerechte Fertigung.
Aktuelle Branchenakzeptanz: Führende Unternehmen und Innovatoren (z.B. straumann.com, 3dsystems.com, eos.info)
Die additive Lithographie, ein Teilbereich der additiven Fertigungstechnologien, gewinnt schnell an Bedeutung in der Zahnimplantatindustrie, angetrieben durch den Bedarf an größerer Anpassung, verbesserter Biokompatibilität und verkürzten Durchlaufzeiten. Im Jahr 2025 führen mehrere führende Unternehmen der Zahnmedizin und 3D-Druckunternehmen die Akzeptanz dieser fortschrittlichen Fertigungsmethoden an und setzen neue Maßstäbe für Präzision und Effizienz in der Zahnimplantologie.
Zu den vordersten Innovatoren zählt die Straumann Group, die erheblich in die Integration additive Fertigung in ihre Produktionsabläufe für Zahnimplantate investiert hat. Die Partnerschaften von Straumann mit Anbietern von 3D-Drucktechnologie haben die Entwicklung patientenspezifischer Implantate und Prothesen ermöglicht, wobei lithographie-basierte keramische Fertigung (LCM) und selektives Laserschmelzen (SLM) sowohl für Metall- als auch Keramikelemente genutzt werden. Die neuen Produktlinien des Unternehmens betonen hochpräzise, maßgefertigte Implantate, die durch die Flexibilität und Auflösung der additiven Lithographie-Techniken möglich werden.
Ebenso bleibt 3D Systems ein zentraler Akteur und bietet zahnspezifische additive Fertigungslösungen wie die NextDent 5100- und Figure 4-Plattformen an. Diese Systeme nutzen digitale Lichtverarbeitung (DLP) und Stereolithographie (SLA), die essentielle Formen der additiven Lithographie sind, um chirurgische Führungen, Kronen, Brücken und implantatgetragene Prothesen zu fertigen. 3D Systems arbeitet weltweit mit Zahnlaboren und Kliniken zusammen, um die Workflows zu optimieren und das Sortiment an zugelassenen biokompatiblen Materialien zu erweitern, was ein kritischer Faktor im Markt für medizinische Geräte ist.
Auf der Seite der Materialien und Geräte hat EOS den Einsatz der additiven Lithographie für metallische Zahnimplantate durch ihre Plattformen für direktes Metalllasersintern (DMLS) vorangetrieben. Die Systeme von EOS ermöglichen es Herstellern, Titanelemente und Kobalt-Chrom-Komponenten mit komplexen Geometrien und optimierter Porosität herzustellen, was eine bessere Osseointegration und Patientenergebnisse unterstützt. Die fortlaufende F&E des Unternehmens stellt sicher, dass seine Lösungen den sich entwickelnden regulatorischen Anforderungen und Branchenstandards entsprechen.
In Zukunft wird erwartet, dass diese Branchenführer weitere Innovationen vorantreiben, einschließlich der Integration digitaler Workflows vom intraoralen Scannen bis zur endgültigen Implantatproduktion sowie der Entwicklung neuer biokompatibler Photopolymere und Keramiken. Da sich die regulatorischen Rahmenbedingungen an diese technologischen Fortschritte anpassen und immer mehr Zahnmediziner digitale Implantologie-Workflows annehmen, steht die Anwendung von additiver Lithographie in der Herstellung von Zahnimplantaten vor einem starken Wachstum bis zum Rest des Jahrzehnts.
Durchbrüche in der Herstellung von Zahnimplantaten: Verbesserte Genauigkeit, Anpassungsfähigkeit und Biokompatibilität
In den letzten Jahren wurde die additive Lithographie – ein Teilbereich der 3D-Drucktechnologien, die lichtbasierte Polymerisation nutzen – zunehmend für die Herstellung von Zahnimplantaten übernommen, was eine beispiellose Präzision, Anpassungsfähigkeit und Materialleistung verspricht. Ab 2025 wechseln Zahnlaboratorien und Implantathersteller von herkömmlichen subtraktiven Fräs- und Gießverfahren zu fortschrittlichen additiven lithografischen Prozessen, wie z.B. Digital Light Processing (DLP) und Stereolithographie (SLA), um der wachsenden Nachfrage nach patientenspezifischen Lösungen gerecht zu werden.
Ein bemerkenswerter Fortschritt ergibt sich aus der Integration von DLP-basierten Systemen in die zahnärztlichen Workflows. Diese Systeme können hochdetaillierte Implantatführer, vorläufige Restaurationen und sogar permanente implantat-getragene Prothesen mit Mikrometerpräzision herstellen. Beispielsweise hat Stratasys sein DLP-Druckportfolio erweitert, um speziell zahnmedizinische Anwendungen zu adressieren, und bietet validierte Workflows für maßgefertigte Abutments und chirurgische Führungen an, die die Produktion am Behandlungsstuhl und im Labor optimieren.
Die Anpassungsfähigkeiten werden zusätzlich durch die Einführung fortschrittlicher biokompatibler Photopolymerharze verbessert. 3D Systems hat nächste Generation von zahnmedizinischen Harzen vorgestellt, die unter ISO 10993 zertifiziert und von der FDA für den langfristigen intraoralen Einsatz zugelassen sind, was die direkte Herstellung von finalen Implantatprothesen mit komplexen Geometrien ermöglicht, die auf die individuelle Anatomie abgestimmt sind. Dies reduziert die Durchlaufzeiten von Wochen auf nur wenige Tage und verbessert dabei den Komfort und die Ästhetik für die Patienten.
Über polymerbasierte Implantate und Führungen hinaus setzen Forscher und Hersteller die Grenzen der additiven Lithographie mit hybriden und keramischen Materialien neu. Dentsply Sirona hat neue photopolymer-keramische Composites getestet, die für DLP optimiert sind und eine verbesserte Verschleißfestigkeit und Biokompatibilität im Vergleich zu herkömmlichen PMMA- oder harzbasierten Kronen bieten. Die laufenden Kooperationen des Unternehmens mit Zahnlaboren sollen diese Innovationen bis 2026 in die routinemäßige klinische Anwendung bringen.
In der Zukunft wird erwartet, dass die Konvergenz von additiver Lithographie mit digitalem Scannen und KI-gesteuertem Design die Präzision und Vorhersagbarkeit von Implantatbehandlungen weiter verbessern wird. Formlabs hat fortschrittliche Softwarepakete veröffentlicht, die KI-basierte Designfunktionen für patientenspezifische Implantat-Abutments integrieren, die, in Kombination mit ihren SLA-Druckern und biokompatiblen Harzen, einen vollständig digitalen, End-to-End-Workflow ermöglichen. Diese digitale Transformation wird voraussichtlich die weit verbreitete Akzeptanz von additiver Lithographie für Zahnimplantate vorantreiben, Materialabfälle reduzieren und bedarfsgerechte, lokale Fertigung ermöglichen – entscheidende Vorteile, da der zahnmedizinische Sektor weiterhin Effizienz und personalisierte Pflege in den kommenden Jahren priorisiert.
Marktprognosen (2025–2030): Wachstumsprognosen, regionale Hotspots und Umsatzschätzungen
Der Markt für additive Lithographie in Zahnimplantaten ist zwischen 2025 und 2030 auf robustes Wachstum eingestellt, angetrieben durch die steigende Nachfrage nach patientenspezifischen Lösungen, kürzeren Vorlaufzeiten und fortlaufenden Fortschritten in der digitalen Zahnmedizin. Branchenführer und Technologietreiber investieren weiterhin in die Skalierung von additiven Lithographie-Techniken, wie z. B. der Zwei-Photonen-Polymerisation und der projektiven Mikrostereolithographie, um die Präzisions- und Biokompatibilitätsstandards zu erfüllen, die für implantierbare zahnmedizinische Geräte erforderlich sind.
Laut 3D Systems, einem der größten Anbieter von zahnmedizinischen 3D-Drucklösungen, beschleunigt die Akzeptanz fortschrittlicher additiver Fertigung in zahnmedizinischen Anwendungen – einschließlich lithographischer Techniken – aufgrund der Fähigkeit, maßgeschneiderte Geräte zu liefern und Workflows für Kliniken und Zahnlaboratorien zu optimieren. In ihrem Jahresbericht 2024 hob 3D Systems ein rasches Wachstum im zahnmedizinischen Umsatz hervor und umreißte Pläne zur weiteren Entwicklung lithographiebasierter Lösungen, die auf Multi-Material- und biokompatible Zahnimplantate abzielen.
Regional gesehen repräsentieren Nordamerika und Westeuropa weiterhin die größten Märkte für digitale Zahnherstellung, bedingt durch hohe Pro-Kopf-Ausgaben im zahnmedizinischen Bereich und frühe Annahme neuer Technologien. Allerdings wird erwartet, dass der asiatisch-pazifische Raum bis 2030 das schnellste Wachstum verzeichnen wird, da aufstrebende Volkswirtschaften in digitale zahnmedizinische Infrastrukturen investieren und lokale Hersteller die Produktion implantierbarer Geräte mit additiver Lithographie hochfahren. Stratasys, ein weiterer wichtiger Akteur im zahnmedizinischen 3D-Druck, hat sein Händlernetzwerk und den technischen Support in China, Indien und Südostasien erweitert und verweist auf eine starke regionale Nachfrage nach digitalen Implantologielösungen.
Aus Sicht des Umsatzes erwarten Branchenquellen, dass der globale Markt für additive Zahnmedizin – von dem die lithographiebasierten Zahnimplantate ein schnell wachsendes Segment darstellen – bis 2030 die Marke von 5 Milliarden US-Dollar überschreiten wird, mit einer jährlichen Wachstumsrate (CAGR) von über 20 % ab 2025. Dentsply Sirona, ein führender Anbieter von Zahntechnologie, hat ein zweistelliges Wachstum in digitalen Produktlinien berichtet, einschließlich derjenigen, die Photopolymerisation und lithographische Techniken zur Herstellung von Kronen, Brücken und Implantat-Abutments nutzen.
In Zukunft wird erwartet, dass die Verbreitung von Software-Ökosystemen und validierten Materialbibliotheken von Unternehmen wie Formlabs die klinische Akzeptanz beschleunigt. Mit dem Reifeprozess regulatorischer Rahmenbedingungen und der zunehmenden Annahme digitaler Workflows durch mehr Zahnmediziner scheint die additive Lithographie zwischen 2025 und 2030 zu einer Standardmethode für nächste Generation von Zahnimplantaten zu werden.
Reg regulatorische Landschaft & Standards: Compliance- und Zertifizierungsherausforderungen
Die regulatorische Landschaft für additive Lithographie in Zahnimplantaten entwickelt sich schnell, da die Technologie reift und die Akzeptanz in klinischen Umgebungen zunimmt. Im Jahr 2025 passen Regulierungsbehörden wie die U.S. Food and Drug Administration (FDA), die Europäische Arzneimittel-Agentur (EMA) und ihre internationalen Pendants bestehende Rahmenbedingungen an, um die einzigartigen Herausforderungen der additiven Fertigung (AM) und insbesondere lithographischer Techniken zu adressieren.
Eine zentrale Herausforderung besteht in der Qualifizierung und Validierung von Prozessen der additiven Lithographie, um eine konsistente Produktion sicherer, biokompatibler und mechanisch robuster Zahnimplantate zu gewährleisten. Die FDA hat Leitfäden veröffentlicht, die sich auf technische Überlegungen für additive gefertigte medizinische Geräte konzentrieren und Anforderungen an die Prozessvalidierung, Materialkontrollen und Nachbearbeitungsverifizierung betonen (FDA). Im Jahr 2024 hat die FDA die Erwartungen für Ausnahmen bei maßgeschneiderten Geräten weiter präzisiert, eine wesentliche Bestimmung für patientenspezifische Zahnimplantate, die mit additiver Lithographie hergestellt werden.
Internationale Standardisierungsbemühungen haben zugenommen, wobei die Internationale Organisation für Normung (ISO) und ASTM International ihr gemeinsames Komiteepotpourri für AM-Standards um lithographiebasierte keramische und polymerverarbeitende Technologien für zahnmedizinische Anwendungen erweitern (ISO). Standards wie ISO/ASTM 52900 und ISO/ASTM 52921 legen Terminologie und Entwurfsrichtlinien fest, während neue Initiativen die Materialcharakterisierung, Rückverfolgbarkeit und Prozessüberwachung adressieren – kritische Bereiche für die regulatorische Akzeptanz von Zahnimplantaten, die durch fortgeschrittene Lithographie hergestellt werden.
Hersteller wie Stratasys und Dentsply Sirona engagieren sich zunehmend bei Regulierungsbehörden und liefern Daten von Pilotproduktionslinien und klinischen Studien, um die Zertifizierung zu erleichtern. Beispielsweise arbeitet Dentsply Sirona mit benannten Stellen in der EU zusammen, um die Konformitätsbewertung von zahnmedizinischen Geräten unter der Medizinprodukteverordnung (MDR) zu optimieren, die striktere Anforderungen an technische Dokumentationen, klinische Bewertungen und Marktüberwachung vorschreibt.
Trotz Fortschritten bleiben Herausforderungen bestehen. Die Zertifizierungsprozesse für AM-Zahnimplantate sind oft länger und komplexer als für konventionell hergestellte Geräte, insbesondere wenn neue Materialien oder höchst patientenspezifische Geometrien involviert sind. Das Fehlen harmonisierter Standards für lithographiebasierte AM, insbesondere in keramischen und hybriden Materialien, schafft Unsicherheit für Hersteller, die eine mehrjurisdiktionale Genehmigung anstreben. Um dem entgegenzuwirken, arbeiten Branchenvereinigungen wie die Additive Manufacturing Users Group (AMUG) daran, bewährte Praktiken abzustimmen und den Dialog zwischen Regulierungsbehörden und der Industrie zu fördern.
In Zukunft werden in den nächsten Jahren voraussichtlich robustere, prozessspezifische Standards und klarere regulatorische Wege für additive Lithographie in Zahnimplantaten eingeführt. Wenn Pilotprogramme und Daten aus der Praxis ansteigen, wird erwartet, dass die Regulierungsbehörden risikobasierte Ansätze verfeinern, was möglicherweise die Markteinführungszeiten für konforme Produkte beschleunigt, während die Patientensicherheit und die Wirksamkeit der Geräte gewahrt bleibt.
Workflow-Integration: Von digitalen Scans zur Implantatproduktion am Behandlungsstuhl
Die Integration der additiven Lithographie in die Arbeitsabläufe für Zahnimplantate transformiert den Prozess vom Scannen des Patienten bis hin zur Implantatproduktion am Behandlungsstuhl. Ab 2025 machen Fortschritte in der digitalen Zahnmedizin es möglich, intraorale Scans direkt in maßgeschneiderte Implantatkomponenten umzuwandeln, die vor Ort hergestellt werden, wodurch die Durchlaufzeiten drastisch verkürzt und die Patientenergebnisse verbessert werden.
Der Workflow beginnt mit hochauflösenden digitalen Scans, die mit intraoralen Scannern erfasst werden und die zahnmedizinische Anatomie des Patienten präzise festhalten. Diese Scans werden in fortschrittliche CAD-Software importiert, in der Zahnärzte und Zahntechniker patientenspezifische Implantate und chirurgische Führungen entwerfen. Der digitale Entwurf wird anschließend an ein System zur additiven Lithographie übertragen – üblicherweise unter Verwendung von Technologien wie Digital Light Processing (DLP) oder Stereolithographie (SLA) – um die Implantatkomponenten schichtweise mit Mikrometerpräzision herzustellen.
Führende Hersteller von Zahntechnologie sind an der Spitze dieser Transformation. Formlabs bietet den Form 3B+ Drucker an, der speziell für zahnmedizinische Anwendungen ausgelegt ist, und ermöglicht die Herstellung von biokompatiblen, präzisen chirurgischen Führungen und temporären Kronen am Behandlungsstuhl. Ebenso integriert Dentsply Sirona additive Fertigungssysteme in ihre digitalen Workflow-Lösungen, wodurch Kliniken nahtlos vom Scannen über das Design bis hin zur Produktion in einem einheitlichen Ökosystem wechseln können.
Im Jahr 2025 liegt der Fokus auf der Optimierung der Produktion am Behandlungsstuhl. Stratasys hat Drucker eingeführt, die ihre proprietäre PolyJet-Technologie nutzen, welche das Mehrmaterial-Drucken und hohe Präzision unterstützt, geeignet für die Herstellung von Implantatmodellen und chirurgischen Führungen direkt in Zahnarztpraxen. 3D Systems erweitert weiterhin seine NextDent-Linie und bietet zertifizierte Materialien und validierte Workflows für zahnmedizinische Fachkräfte an, die die Produktion in-house bringen möchten.
Regulatorische Compliance und Rückverfolgbarkeit werden immer wichtiger, insbesondere da die Herstellung am Behandlungsstuhl näher daran rückt, definitive Implantatkomponenten anstelle von nur Führungen oder vorläufigen Restaurationen zu produzieren. Führende Branchenverbände wie die American Dental Association (ADA) entwickeln neue Richtlinien für die sichere Integration von additiven Fertigungstechnologien in die klinische Praxis.
In den kommenden Jahren wird erwartet, dass weitere Verfeinerungen in automatisierten Workflows, verbesserte Materialien mit erhöhter Biokompatibilität und eine breitere Annahme vollständig integrierter Systeme am Behandlungsstuhl stattfinden. Mit dem Reifeprozess der Technologie wird die Fähigkeit, patientenspezifische Implantate innerhalb von Stunden – anstatt von Wochen – zu liefern, zu einer Standardpraxis in der digitalen Zahnmedizin werden, unterstützt durch fortwährende Innovationen und Kooperationen zwischen Technologieanbietern und Zahnarztpraxen.
Wettbewerbsanalyse: Traditionelle Fertigung vs. additive Lithographie
Die Wettbewerbslandschaft für die Herstellung von Zahnimplantaten unterliegt einem erheblichen Wandel, während Technologien der additiven Lithographie gegen traditionelle subtraktive Methoden wie CNC-Fräsen und Gießen gewähren. Im Jahr 2025 bleibt der globale Markt für Zahnimplantate von etablierten Herstellern dominiert, die hochpräzises CNC-Bearbeiten von Titan und Zirkonia nutzen. Allerdings nimmt die additive Lithographie – insbesondere die photopolymerbasierte 3D-Druck- und lithographiebasierte keramische Fertigung (LCM) – rasch zu, angetrieben durch ihre einzigartigen Vorteile in Bezug auf Designflexibilität, Geschwindigkeit und Anpassungsfähigkeit.
Traditionelle Fertigungsmethoden bieten zwar zuverlässige Festigkeit und Biokompatibilität, gehen jedoch häufig mit Materialverschwendung, langen Vorlaufzeiten und Einschränkungen in der Komplexität der erreichbaren Geometrien einher. Im Gegensatz dazu ermöglicht die additive Lithographie die direkte Herstellung komplexer Implantatgeometrien, wie z.B. poröse Oberflächen und Gitterstrukturen, die die Osseointegration und das Patientenresultat verbessern können. Beispielsweise haben Unternehmen wie Straumann und Dentsply Sirona in additive Technologien investiert, um maßgeschneiderte Abutments und chirurgische Führungen herzustellen, während die meisten endossose Implantate bis 2025 weiterhin traditionell hergestellt werden.
Ein entscheidendes Unterscheidungsmerkmal der additiven Lithographie ist ihre Fähigkeit zur Integration digitaler Workflows. Mit intraoralem Scannen und CAD/CAM-Design können Zahnimplantate an die Anatomie des einzelnen Patienten angepasst, bedarfsgerecht hergestellt und innerhalb von Tagen geliefert werden. Lithoz hat die LCM-basierte Produktion von Zirkonia-Implantaten mit hoher Dichte und mechanischer Festigkeit demonstriert, die mit konventionell gesinterten Komponenten vergleichbar ist, und dabei mikrostrukturierte Oberflächen ermöglicht, die zuvor nicht möglich waren. 3D Systems hat die Arbeitsabläufe am Behandlungsstuhl weiter beschleunigt, indem die Photopolymerharze für zahnmedizinische Anwendungen optimiert und die Integration mit digitalen Zahnmedizin-Plattformen unterstützt werden.
- Kosten und Durchsatz: Während die anfänglichen Investitionen in Systeme der additiven Lithographie hoch sind, verringern laufende Fortschritte in Druckgeschwindigkeit und Automatisierung die Lücke zu traditionellen Verfahren. Stratasys und Formlabs haben zahnmedizinische 3D-Drucker eingeführt, die eine Batch-Produktion ermöglichen, wodurch die Kosten pro Einheit reduziert und kleine Chargen ermöglicht werden können.
- Regulatorische Wege: Additiv hergestellte Zahnimplantate erhalten zunehmend regulatorische Genehmigungen, da Organisationen wie die U.S. FDA und die Europäische Arzneimittel-Agentur beginnen, Richtlinien für 3D-gedruckte medizinische Geräte zu etablieren, was den Weg für eine breitere Akzeptanz ebnet.
- Materialfortschritte: Laufende Forschungen von Unternehmen wie Envista konzentrieren sich auf die Optimierung biokompatibler Photopolymere und Keramiken für den langfristigen klinischen Einsatz, um Bedenken hinsichtlich der mechanischen Eigenschaften und der Osseointegration zu adressieren.
In Zukunft sieht die Prognose für die additive Lithographie in Zahnimplantaten positiv aus, wobei Vorhersagen auf einen wachsenden Anteil von maßgeschneiderten Abutments und möglicherweise endossose Implantaten hinweisen, die in den nächsten Jahren mit lithografischen Methoden hergestellt werden. Da die Zuverlässigkeit von Systemen, Materialien und regulatorische Standards reifen, ist die additive Lithographie bereit, die traditionelle Fertigung herauszufordern, insbesondere in hochwertigen, patientenspezifischen Anwendungen.
Zukünftige Perspektiven: Next-Gen Materialien, KI-Integration und Automatisierung
Die Landschaft der Zahnimplantatfertigung unterliegt einem bedeutenden Wandel, wobei die additive Lithographie als wichtiger Ermöglicher nächster Generation Lösungen auftritt. Ab 2025 prägen die Konvergenz von fortschrittlichen Materialien, künstlicher Intelligenz (KI) und Automatisierung die zukünftige Richtung des Sektors. Die additive Lithographie – die sich von herkömmlichem 3D-Druck unterscheidet, indem sie lichtbasierte Musterung auf Mikro- und Nanoskalen nutzt – bietet beispiellose Präzision und Materialvielfalt und entwickelt sich schnell von experimentellen Phasen in die kommerzielle Zahnmedizin.
Wichtige zahnmedizinische Hersteller investieren stark in die Entwicklung und Validierung neuer Photopolymerharze und keramischer Materialien, die für additive Lithographie optimiert sind. Beispielsweise hat Dentsply Sirona laufende Kooperationen angekündigt, um keramische lithographische Prozesse voranzutreiben, mit dem Ziel, die Osseointegration und mechanische Stabilität in Zahnimplantaten zu verbessern. Ebenso berichtet die Straumann Group von aktiven Erkundungen hybrider Harz-Keramikformulierungen, um schnellere Produktionszeiträume und Anpassungen im großen Stil zu erzielen.
Die Integration von KI fördert das Design und die Workflow-Optimierung in der additiven Lithographie. KI-gesteuerte Algorithmen werden innerhalb von Dental-CAD/CAM-Plattformen eingebettet, um die Planung von Implantaten zu automatisieren, die Materialleistung vorherzusagen und manuelle Eingriffe zu reduzieren. exocad, ein prominenter Anbieter von Zahntechnologie-Software, hat kürzlich KI-unterstützte Funktionen präsentiert, die automatisch patientenspezifische Implantatgeometrien erstellen, die für die lithographische Fertigung geeignet sind. Diese Fortschritte sollen die Wartezeiten am Behandlungsstuhl verkürzen und die klinischen Ergebnisse verbessern.
Automatisierung ist ein weiterer definierender Trend, bei dem End-to-End-Digital-Workflows alles vom Abdruckscannen bis zur Nachbearbeitung optimieren. 3D Systems hat automatisierte Produktionslinien auf Basis von Lithographie für Zahnlaboratorien eingeführt, die robotergestützte Handhabung und Echtzeitprozessüberwachung integrieren. Dies erhöht nicht nur die Durchsatzleistung, sondern stellt auch eine gleichbleibende Qualität sicher – ein entscheidender Faktor, da die regulatorischen Erwartungen an zahnmedizinische Geräte weltweit strenger werden.
In den nächsten Jahren erwarten Branchenanalysten und Hersteller weitere Durchbrüche bei biokompatiblen Materialien, wie z.B. bioaktiven Gläsern und funktionalisierten Keramiken. Diese Innovationen sollen die Herstellung von Implantaten mit verbesserten antibakteriellen Eigenschaften und langfristiger Haltbarkeit unterstützen. Darüber hinaus wird die Integration von KI mit Echtzeitprozesskontrollen voraussichtlich adaptive Fertigung ermöglichen, bei der die Implantatparameter während der Herstellung dynamisch angepasst werden, um optimale Passform und Funktion zu gewährleisten.
Zusammenfassend lässt sich sagen, dass die additive Lithographie für Zahnimplantate kurz vor einer breiten Akzeptanz steht, angetrieben durch Materialien der nächsten Generation, KI-gestütztem Design und End-to-End-Automatisierung. Die Zusammenarbeit zwischen zahnmedizinischen Herstellern, Softwareunternehmen und Materialwissenschaftlern wird entscheidend sein, um diese Fortschritte zu beschleunigen und sicherzustellen, dass klinische Vorteile für Praxen und Patienten gleichermaßen realisiert werden.
Strategische Einblicke & Empfehlungen für Stakeholder in der dentalen additiven Lithographie
Die additive Lithographie, insbesondere im Kontext von Zahnimplantaten, wandelt sich von einem neuartigen Prototyping-Werkzeug zu einem Eckpfeiler der klinischen Produktion. Ab 2025 stehen Stakeholder – einschließlich Hersteller, Zahnlaboratorien, Kliniker und Materiallieferanten – vor einem Umfeld, das von rascher technologischer Entwicklung, regulatorischer Anpassung und sich ändernden Patientenerwartungen geprägt ist.
Strategische Einblicke für Stakeholder konzentrieren sich auf drei zentrale Säulen: Technologische Integration, kollaborative Partnerschaften und regulatorische Agilität.
- End-to-End-Digitale Workflows priorisieren: Anbieter und Labore von Zahnimplantaten sollten in vollständig integrierte digitale Workflows investieren, vom intraoralen Scannen über additive Lithographie bis zur Nachbearbeitung. Unternehmen wie Stratasys und 3D Systems haben ihre Lösungen für zahnmedizinische Lithographie erweitert und bieten validierte Material-Drucker-Kombinationen an, die die Produktion rationalisieren und die Reproduzierbarkeit von Implantatkomponenten verbessern.
- Materialinnovation annehmen: In den nächsten Jahren wird eine beschleunigte Entwicklung biokompatibler, hochfester Photopolymere und Keramiken zu erwarten sein, die für tragfähige Zahnimplantate geeignet sind. Die frühe Anwendung neuer Materialien von Lieferanten wie Dentsply Sirona und Formlabs, die aktiv ihre Zahnharzportfolios erweitern, ermöglicht es Stakeholdern, langlebigere und anpassungsfähigere Implantatlösungen anzubieten.
- Strategische Partnerschaften bilden: Die Zusammenarbeit zwischen Zahnarztpraxen, Laboren und Herstellern von additiven Verfahren ist entscheidend für den Wissensaustausch und die Workflow-Optimierung. Beispielsweise arbeitet EnvoDent direkte mit Zahnmedizinern zusammen, um patientenspezifische Lösungen zu entwickeln und additive Lithographie für personalisierte Implantologie zu nutzen.
- Regulatorische Entwicklungen überwachen: Die regulatorischen Rahmenbedingungen für additive Fertigung in Zahnimplantaten ändern sich. Stakeholder müssen die Aktualisierungen von anerkannten Stellen wie der U.S. Food and Drug Administration (FDA) und der International Organization for Standardization (ISO) genau verfolgen, die Standards für die Validierung von Geräten, Rückverfolgbarkeit und Patientensicherheit bei 3D-gedruckten zahnmedizinischen Geräten weiter verfeinern.
- In Schulung und Ausbildung investieren: Die Weiterbildung von Zahnmedizinern und Technikern ist entscheidend, um die klinischen Vorteile der additiven Lithographie zu maximieren. Unternehmen wie exocad bieten spezialisierte Schulungsmodule und Software an, die auf das Design von Zahnimplantaten und 3D-Druck zugeschnitten sind und die effektive Technologieanwendung unterstützen.
In der Zukunft werden Stakeholder, die proaktiv fortschrittliche lithografische Technologien integrieren, strategische Allianzen fördern und sich über regulatorische und materialtechnische Neuerungen informieren, am besten positioniert sein, um vom wachsenden Markt für Zahnimplantate zu profitieren. Kontinuierliche Investitionen in Bildung, validierte Workflows und patientenspezifische Lösungen werden entscheidend sein, um klinische Exzellenz und Wettbewerbsunterscheidung bis 2025 und darüber hinaus aufrechtzuerhalten.
Quellen & Referenzen
- Straumann Group
- Dentsply Sirona
- 3D Systems
- Formlabs
- Stratasys
- EOS
- Formlabs
- ISO
- Dentsply Sirona
- American Dental Association (ADA)
- Lithoz
- Envista
- exocad