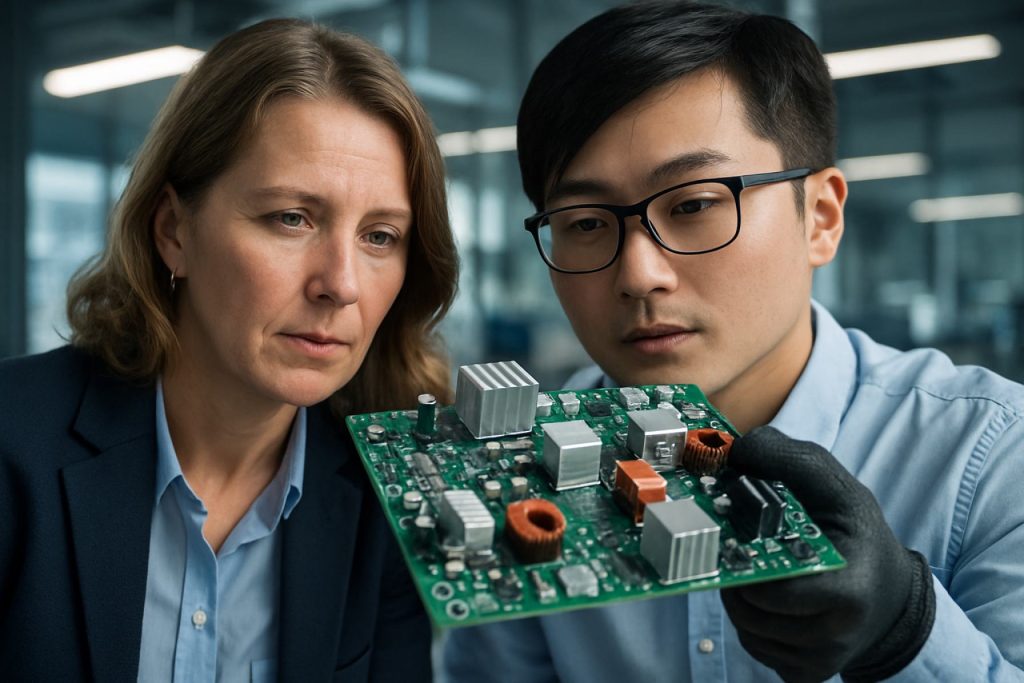
- Fraunhofer IISB and AIXTRON are accelerating innovation in Silicon Carbide (SiC) epitaxy technology for next-generation power electronics.
- The advanced AIXTRON G5WW Vapor Phase Epitaxy system enables simultaneous processing of eight 150 mm SiC wafers, improving scale and precision.
- Moving from 100 mm to 150 mm wafers significantly reduces manufacturing costs and defects, increasing device yields for solar inverters, data centers, and transportation.
- State-of-the-art techniques like photoluminescence imaging and defect etching ensure SiC crystals meet strict quality requirements for applications in critical infrastructure.
- This collaboration supports the mass production of affordable, high-performance SiC devices, paving the way for greater energy efficiency and sustainability in power electronics.
Bright overhead lights reveal a swirling dance of engineers and researchers within the cleanroom corridors of Erlangen, Germany—home to the Fraunhofer IISB, a world-class center for semiconductor innovation. In a move that signals a shift in the power electronics landscape, Fraunhofer IISB and AIXTRON have joined forces to unlock new dimensions for Silicon Carbide (SiC) epitaxy technology.
Silicon Carbide isn’t new to the scene; this resilient material powers essential components inside computer servers, medical equipment, solar inverters, and the trains that carry commuters home. What’s changing, and changing fast, is the way we build these tiny, powerful devices.
AIXTRON’s cutting-edge G5WW Vapor Phase Epitaxy system, capable of simultaneously processing eight 150 mm SiC wafers, is at the heart of this leap. The system—destined for Fraunhofer IISB’s state-of-the-art laboratories—promises a scale and precision previously out of reach. Here, world-renowned scientists, armed with years of SiC research and advanced defect-detection tools, push the boundaries of what’s possible.
The advantage in size is more than academic. By moving from 100 mm to 150 mm wafers, manufacturers could slash both costs and defects. Larger wafers translate to more devices produced per run—a vital step toward bringing affordable, high-performance power electronics to everyday life.
Researchers have fine-tuned every stage. At Fraunhofer, they deploy specialized techniques, from room-temperature photoluminescence imaging to selective defect etching, ensuring the SiC layers exhibit ultra-low densities of crystalline flaws. This focus on perfection is crucial. Even a single imperfection in a power device, such as a Metal-Oxide-Semiconductor Field-Effect Transistor (MOSFET) or Schottky diode, can mean the difference between failure and flawless function in critical infrastructure.
The collaboration aims not just at prototype demonstration but at real, high-volume manufacturing. Think solar grids humming more efficiently, data centers consuming less energy, and electric trains running smoother—all thanks to the foundational work happening within these laboratory walls.
This partnership sets the course for the next generation of SiC devices, which experts believe will dominate power electronics markets by the end of this decade. The domino effect for consumers will be palpable: sharper declines in energy usage, faster adoption of green-energy tech, and a quieter environmental footprint, all propelled by the silent, steady progress of wafer technology.
As the world races toward higher efficiency and sustainability, collaboration between industry leaders like AIXTRON and research giants such as Fraunhofer IISB demonstrates not just technical prowess, but a shared vision. These titans are forging the building blocks of an electrified future—one silicon carbide layer at a time.
For more on leading innovations and the companies powering global change, visit AIXTRON and Fraunhofer.
Key takeaway: The leap from 100 mm to 150 mm SiC wafers, powered by pioneering partnerships and relentless research, holds the promise of radically more efficient, reliable, and cost-effective power electronics—ready to redefine how energy moves through our world.
This Semiconductor Breakthrough Could Supercharge the Future of Green Tech (And Slash Your Energy Bills)
Unlocking the Full Power of Silicon Carbide: What the Fraunhofer IISB–AIXTRON Partnership Means for You
Silicon Carbide (SiC) technology is setting the stage for a revolution in power electronics, unlocking greater efficiency, sustainability, and device reliability. While the collaboration between Fraunhofer IISB and AIXTRON to scale up SiC epitaxy to 150 mm wafers is making headlines, there’s much more beneath the surface. Here are crucial, expert-backed facts and actionable insights that were not fully detailed in the source material, shedding light on how this leap could affect everything from your car charger to the global energy market.
—
What Sets 150 mm SiC Wafers Apart? Features & Specs
– Higher Yield: 150 mm wafers offer up to twice the yield per run compared to 100 mm wafers, multiplying device throughput and driving down unit costs.
– Enhanced Current Handling: SiC’s high breakdown electric field lets it handle higher voltages and temperatures than traditional silicon—a game-changer for electric vehicles (EVs) and renewable energy inverters.
– Low Defect Density: Advanced defect-detection (like photoluminescence imaging and selective etching) ensures industry-leading wafer quality, crucial for mission-critical systems.
– Precision Manufacturing: The G5WW system from AIXTRON delivers unmatched gas and temperature uniformity—key to consistent performance and high yields.
—
Controversies & Limitations
– Production Cost: SiC wafers, while more efficient, remain pricier to manufacture than silicon, at least in the short term.
– Supply Chain: The transition to larger SiC wafers requires capital investment in new equipment and facilities, potentially creating bottlenecks.
– Material Fragility: SiC, though robust in use, is brittle during processing, increasing the risk of wafer breakage if not managed by advanced systems.
—
Real-World Use Cases
1. Electric Vehicles (EVs)
– Faster charging, lighter and more efficient powertrains, and extended battery range are all possible due to SiC-based MOSFETs and diodes. Tesla, for example, famously adopted SiC inverters in its Model 3 to gain a competitive edge.
2. Renewable Energy
– More efficient solar inverters and wind power converters mean that more of the sun’s and wind’s energy makes it into the grid. SiC enables smaller, lighter, and more reliable installations.
3. Data Centers
– Servers and cooling systems consume enormous energy; SiC allows for more compact and cooler-running power delivery, potentially slashing operational costs.
—
Industry Trends & Market Forecasts
– Mass Adoption Imminent: Yole Développement forecasts the SiC device market will exceed $6 billion by 2027, growing at a CAGR of over 30%.
– Automotive Lead: The EV sector dominates SiC demand, with the market share for SiC MOSFETs in EVs expected to double by 2026.
– Expansion Beyond Automotive: Telecom, aerospace, and medical industries are increasingly embracing SiC for its reliability and efficiency (source: Fraunhofer).
—
Security & Sustainability Insights
– Lower CO2 Footprint: By enabling higher efficiency and lower losses, SiC devices help cut emissions across their installation base.
– Supply Security: Partnerships like Fraunhofer IISB–AIXTRON are strategically important to decrease reliance on non-European suppliers, bolstering regional supply chains.
– Device Longevity: SiC’s exceptional hardness and thermal stability ensure devices last longer, reducing electronic waste.
—
Pressing Reader Questions Answered
How does SiC compare to traditional silicon?
SiC can operate at higher voltages, higher temperatures, and with better efficiency than standard silicon devices—key advantages for next-gen electronics.
Will this make electronics cheaper?
As wafer sizes grow and manufacturing scales up, expect a significant reduction in SiC device costs—potentially halving them by the decade’s end, according to various market analyses.
What about recycling or end-of-life?
SiC devices are more environmentally friendly due to extended lifespans, but recycling processes are still being optimized to meet mass adoption.
—
Quick Tutorial: How to Identify SiC-Enabled Devices
1. Check Product Specs: Look for mentions of “SiC MOSFET”, “SiC Schottky diode”, or “wide bandgap semiconductor”.
2. Manufacturer Insights: Visit device manufacturer websites (e.g., AIXTRON) for whitepapers or technical details on power devices.
3. Efficiency Benchmarks: SiC devices typically enable smaller, lighter, and more efficient power stages in high-performance equipment.
—
Pros & Cons Overview
Pros
– Dramatically higher efficiency
– Endures extreme temperatures and voltages
– Longer device lifespans
– Enables higher power density for compact products
Cons
– Higher initial manufacturing cost
– Requires updated production lines
– Supply chain currently in transition
—
Actionable Recommendations & Tips
– If you’re in tech procurement: Start prioritizing SiC-based devices for new power electronics investments to future-proof operations and enhance energy performance.
– For manufacturers: Proactively assess equipment compatibility with 150 mm SiC wafers, and partner with market leaders for access to cutting-edge epitaxy technology.
– Consumers: Seek out energy-efficient products that highlight SiC use for lower bills and reduced environmental impact.
—
Final Words
The transition to 150 mm SiC wafers, driven by the synergy between Fraunhofer IISB and AIXTRON, is poised to deliver a powerful market shift. By adopting larger, purer, and more reliable SiC devices, industries and consumers alike stand to gain—from plummeting energy costs to sustainable innovation across smart grids, e-mobility, and more. For the latest breakthroughs, visit AIXTRON and Fraunhofer.
Key takeaway: Today’s advancements in SiC wafer technology don’t just promise better electronics—they lay the groundwork for a greener, more economical, and resilient energy future for everyone.