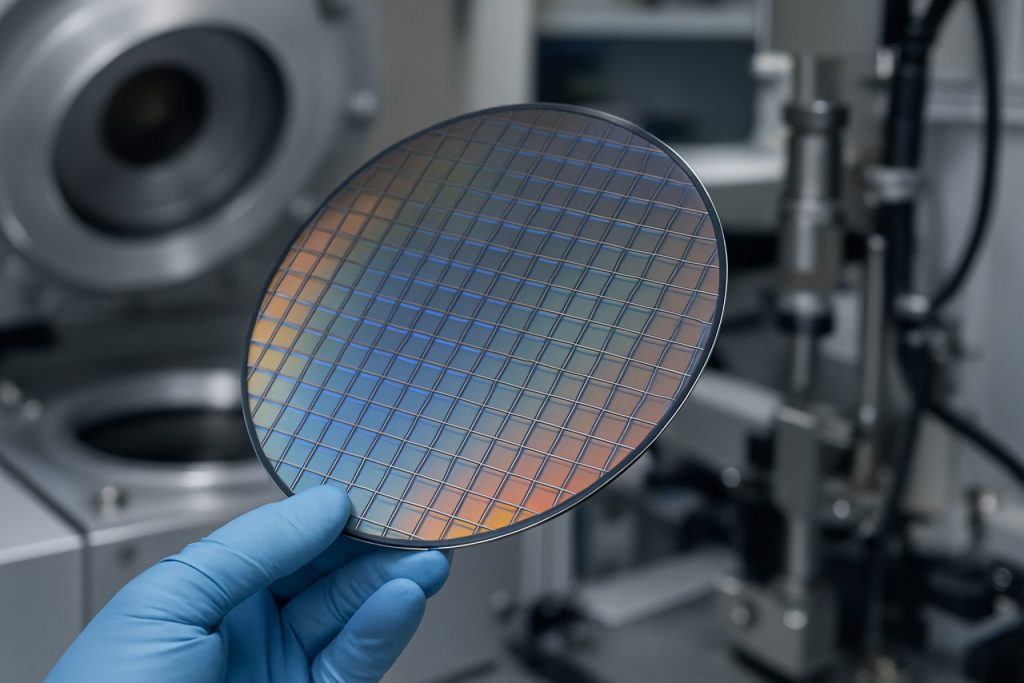
Nitride Semiconductor Wafer Fabrication in 2025: Unleashing Next-Gen Power and Optoelectronics. Explore How Advanced Materials and Global Demand Are Shaping the Industry’s Future.
- Executive Summary: Key Trends and 2025 Outlook
- Market Size and Growth Forecast (2025–2030): CAGR and Revenue Projections
- Technology Landscape: GaN, AlN, and InN Wafer Innovations
- Major Players and Strategic Initiatives (e.g., Cree/Wolfspeed, Sumitomo Electric, Nichia)
- Manufacturing Process Advances: MOCVD, HVPE, and Substrate Developments
- Application Segments: Power Electronics, RF Devices, LEDs, and Emerging Uses
- Regional Analysis: Asia-Pacific Leadership and Global Expansion
- Supply Chain and Raw Material Dynamics
- Challenges: Yield, Cost, and Scalability Barriers
- Future Outlook: Disruptive Technologies and Long-Term Market Opportunities
- Sources & References
Executive Summary: Key Trends and 2025 Outlook
Nitride semiconductor wafer fabrication is entering a pivotal phase in 2025, driven by surging demand for high-performance electronics, energy-efficient lighting, and next-generation power devices. Gallium nitride (GaN) and aluminum gallium nitride (AlGaN) wafers are at the forefront, enabling advances in 5G infrastructure, electric vehicles (EVs), and advanced optoelectronics. The industry is witnessing rapid capacity expansions, technology scaling, and strategic collaborations among leading manufacturers.
Key players such as Kyocera Corporation, Sumitomo Chemical, and Ferrotec Holdings Corporation are scaling up production of GaN and related nitride wafers, leveraging proprietary crystal growth and wafering technologies. Kyocera Corporation continues to invest in expanding its nitride substrate lines, targeting both power electronics and RF device markets. Sumitomo Chemical is advancing hydride vapor phase epitaxy (HVPE) and metal-organic chemical vapor deposition (MOCVD) processes to improve wafer quality and yield, while Ferrotec Holdings Corporation is focusing on high-purity nitride substrates for optoelectronic and microelectronic applications.
In 2025, the transition to larger wafer diameters—moving from 2-inch and 4-inch to 6-inch and even 8-inch GaN wafers—is accelerating, driven by the need for higher throughput and cost efficiency. This shift is supported by investments in advanced crystal growth furnaces and automated wafer processing lines. Companies such as Kyocera Corporation and Sumitomo Chemical are at the forefront of this transition, with pilot production of 6-inch and 8-inch wafers underway.
Strategic partnerships and supply agreements are shaping the competitive landscape. Device manufacturers are securing long-term wafer supply from established substrate producers to mitigate risks associated with material shortages and quality variability. For example, Ferrotec Holdings Corporation has announced collaborations with device makers to co-develop application-specific nitride wafers, particularly for automotive and telecom sectors.
Looking ahead, the outlook for nitride semiconductor wafer fabrication remains robust. The sector is expected to benefit from continued electrification trends, expansion of 5G and 6G networks, and the proliferation of high-efficiency LEDs and laser diodes. Ongoing R&D into defect reduction, wafer scaling, and new nitride compositions will further enhance device performance and manufacturing yields, positioning the industry for sustained growth through 2025 and beyond.
Market Size and Growth Forecast (2025–2030): CAGR and Revenue Projections
The nitride semiconductor wafer fabrication market is poised for robust growth between 2025 and 2030, driven by surging demand for high-performance optoelectronic and power electronic devices. Gallium nitride (GaN) and aluminum gallium nitride (AlGaN) wafers are at the forefront, enabling advancements in 5G infrastructure, electric vehicles (EVs), and energy-efficient lighting. Industry leaders such as Wolfspeed, Inc. (formerly Cree), Kyocera Corporation, Sumitomo Chemical, and Coherent Corp. (formerly II-VI Incorporated) are expanding their production capacities to meet this rising demand.
In 2025, the global nitride semiconductor wafer fabrication market is estimated to surpass several billion USD in annual revenue, with projections indicating a compound annual growth rate (CAGR) between 10% and 15% through 2030. This growth is underpinned by the rapid adoption of GaN-based power devices in automotive and industrial applications, as well as the proliferation of GaN and AlGaN wafers in micro-LED displays and high-frequency RF components. For instance, Wolfspeed, Inc. has recently inaugurated the world’s largest 200mm GaN-on-SiC wafer fabrication facility, signaling a significant scale-up in production capabilities and a commitment to long-term market expansion.
Japanese manufacturers such as Sumitomo Chemical and Kyocera Corporation continue to invest in advanced crystal growth and wafering technologies, targeting both the power electronics and optoelectronics sectors. Meanwhile, Coherent Corp. is leveraging its expertise in compound semiconductor materials to supply high-quality GaN and AlGaN substrates for next-generation device fabrication. These strategic investments are expected to accelerate the market’s revenue trajectory and support a steady CAGR through the forecast period.
- By 2030, the market is anticipated to reach a value in the high single-digit to low double-digit billion USD range, reflecting the increasing penetration of nitride semiconductors in automotive, consumer electronics, and telecom sectors.
- Ongoing R&D and capacity expansions by leading wafer suppliers are likely to further reduce production costs and improve wafer quality, enhancing the competitiveness of nitride-based devices.
- Regional growth is expected to be strongest in Asia-Pacific, led by investments from Japanese, South Korean, and Chinese manufacturers, while North America and Europe will continue to see steady demand from automotive and industrial segments.
Overall, the nitride semiconductor wafer fabrication market is set for sustained double-digit growth, with major industry players scaling up to capture opportunities in emerging high-power and high-frequency device applications.
Technology Landscape: GaN, AlN, and InN Wafer Innovations
The technology landscape for nitride semiconductor wafer fabrication is rapidly evolving in 2025, driven by the surging demand for high-performance electronics, power devices, and optoelectronics. Gallium nitride (GaN), aluminum nitride (AlN), and indium nitride (InN) wafers are at the forefront of this innovation, each offering unique material properties that enable next-generation applications.
GaN wafer technology continues to mature, with leading manufacturers such as Kyocera Corporation, Sumitomo Chemical, and Coherent Corp. (formerly II-VI Incorporated) scaling up production of both bulk and epitaxial GaN substrates. The industry is witnessing a shift toward larger wafer diameters—transitioning from 4-inch to 6-inch and even 8-inch formats—to improve throughput and reduce costs per device. This scaling is critical for power electronics and RF applications, where device performance and yield are closely tied to substrate quality and uniformity. Companies like Ammono and Soraa are also recognized for their advancements in ammonothermal and hydride vapor phase epitaxy (HVPE) growth techniques, which are essential for producing high-purity, low-defect GaN crystals.
AlN wafer fabrication is gaining momentum, particularly for applications in deep ultraviolet (DUV) optoelectronics and high-frequency devices. HexaTech, a subsidiary of Yole Group, and TOYOTA SOLAR are among the few companies capable of producing high-quality, single-crystal AlN substrates. The focus in 2025 is on improving crystal growth methods such as physical vapor transport (PVT) and metal-organic chemical vapor deposition (MOCVD) to achieve larger diameters and lower dislocation densities. These advances are expected to accelerate the adoption of AlN in UV-C LEDs and high-power electronic devices.
InN wafer technology, while less mature than GaN and AlN, is attracting increased research and pilot-scale production. The material’s ultra-high electron mobility and narrow bandgap make it promising for high-speed transistors and infrared optoelectronics. Companies like Nitride Solutions and research consortia in Japan and Europe are investing in scalable growth techniques, such as plasma-assisted MBE and MOVPE, to overcome challenges related to InN’s thermal instability and defect control.
Looking ahead, the nitride semiconductor wafer sector is expected to see continued investment in substrate scaling, defect reduction, and integration with silicon and other platforms. Strategic partnerships between wafer suppliers and device manufacturers are likely to accelerate commercialization, with a focus on automotive, 5G, and renewable energy markets. As fabrication technologies mature, the industry anticipates broader adoption of GaN, AlN, and InN wafers in both established and emerging applications.
Major Players and Strategic Initiatives (e.g., Cree/Wolfspeed, Sumitomo Electric, Nichia)
The nitride semiconductor wafer fabrication sector is witnessing significant activity in 2025, driven by the strategic initiatives of major industry players. These companies are investing in capacity expansion, technology innovation, and vertical integration to address surging demand for gallium nitride (GaN) and related materials in power electronics, RF devices, and optoelectronics.
Wolfspeed, Inc. (formerly Cree) remains a global leader in GaN and silicon carbide (SiC) wafer production. In 2024, Wolfspeed inaugurated its Mohawk Valley Fab in New York, the world’s largest 200mm SiC fabrication facility, and has since announced further investments to scale up GaN-on-SiC wafer output. The company’s vertically integrated model—from crystal growth to finished wafers—positions it to supply both internal device manufacturing and external customers. Wolfspeed’s strategic partnerships with automotive and industrial giants underscore its commitment to long-term supply agreements and technology co-development (Wolfspeed, Inc.).
Sumitomo Electric Industries, Ltd. is a key supplier of GaN substrates and epitaxial wafers, leveraging decades of expertise in crystal growth and wafering. The company has expanded its production lines for 4-inch and 6-inch GaN wafers, targeting high-frequency and high-power applications. Sumitomo Electric’s focus on defect reduction and uniformity improvement is critical for next-generation device yields. In 2025, the company is also advancing research into 8-inch GaN wafers, aiming to support the industry’s migration to larger diameters for cost efficiency (Sumitomo Electric Industries, Ltd.).
Nichia Corporation, renowned for its pioneering work in blue and white LEDs, continues to invest in GaN wafer and epitaxy technology. Nichia’s vertically integrated operations—from substrate fabrication to device packaging—enable tight process control and rapid innovation cycles. The company is actively developing advanced GaN-on-sapphire and GaN-on-SiC wafers for both lighting and power device markets. Nichia’s collaborations with global electronics manufacturers are expected to accelerate the adoption of GaN-based solutions in automotive and consumer sectors (Nichia Corporation).
Other notable players include Kyocera Corporation, which is scaling up GaN substrate production, and Ferrotec Holdings Corporation, supplying process equipment and materials for nitride wafer fabrication. These companies are investing in automation, quality control, and supply chain resilience to meet the stringent requirements of emerging applications.
Looking ahead, the sector is expected to see further consolidation and strategic alliances as companies seek to secure raw material sources, optimize manufacturing costs, and accelerate time-to-market for advanced nitride semiconductor devices.
Manufacturing Process Advances: MOCVD, HVPE, and Substrate Developments
The fabrication of nitride semiconductor wafers, particularly those based on gallium nitride (GaN) and aluminum gallium nitride (AlGaN), continues to evolve rapidly in 2025, driven by advances in epitaxial growth techniques and substrate engineering. Metal-Organic Chemical Vapor Deposition (MOCVD) remains the dominant method for high-quality nitride layer deposition, with significant improvements in reactor design, precursor delivery, and in-situ monitoring. Leading equipment manufacturers such as AIXTRON SE and Veeco Instruments Inc. have introduced new MOCVD platforms with enhanced automation, uniformity, and throughput, targeting both power electronics and microLED applications. These systems are increasingly optimized for 200 mm wafer processing, a key trend as the industry seeks to leverage existing silicon infrastructure for cost reduction and scalability.
Hydride Vapor Phase Epitaxy (HVPE) is also experiencing renewed interest, particularly for the production of bulk GaN substrates. HVPE offers high growth rates and is being refined to reduce dislocation densities and improve crystal quality. Companies such as Sumitomo Chemical and Mitsubishi Chemical Group are scaling up HVPE-grown GaN substrate production, aiming to meet the growing demand for native substrates in high-power and RF device markets. The availability of high-quality, large-diameter GaN substrates is expected to further accelerate device performance improvements and yield enhancements over the next few years.
Substrate developments are a critical focus area, with ongoing efforts to address the cost and performance trade-offs between sapphire, silicon carbide (SiC), silicon, and native GaN substrates. Sapphire remains widely used for LED applications due to its cost-effectiveness, with suppliers like Saint-Gobain and Monocrystal expanding capacity and improving crystal quality. For power electronics, SiC substrates—provided by companies such as Wolfspeed—are favored for their superior thermal and lattice properties, though cost remains a challenge. Meanwhile, the push towards GaN-on-silicon is being advanced by players like NexGen Power Systems, leveraging large-diameter silicon wafers to drive down costs for consumer and automotive applications.
Looking ahead, the next few years are expected to see further integration of in-situ process control, AI-driven optimization, and advanced metrology in both MOCVD and HVPE processes. These innovations, combined with substrate breakthroughs, are poised to support the scaling of nitride semiconductor wafer fabrication for emerging applications in 5G, electric vehicles, and solid-state lighting.
Application Segments: Power Electronics, RF Devices, LEDs, and Emerging Uses
Nitride semiconductor wafer fabrication continues to underpin critical advances across multiple application segments, notably power electronics, RF devices, LEDs, and a growing array of emerging uses. As of 2025, the sector is characterized by both technological maturation and rapid expansion into new markets, driven by the unique material properties of group III-nitrides such as gallium nitride (GaN) and aluminum nitride (AlN).
In power electronics, GaN-based wafers are increasingly displacing traditional silicon due to their superior breakdown voltage, high electron mobility, and efficiency at high frequencies. Leading manufacturers such as Infineon Technologies AG and NXP Semiconductors have expanded their GaN device portfolios, targeting applications from electric vehicle (EV) powertrains to fast-charging infrastructure. The transition to 200 mm GaN-on-silicon wafers is underway, with companies like imec and onsemi investing in pilot lines and volume production, aiming to reduce costs and improve device yields.
For RF devices, especially in 5G and satellite communications, GaN-on-SiC (silicon carbide) wafers remain the standard due to their high thermal conductivity and power density. Wolfspeed, Inc. (formerly Cree) and Qorvo, Inc. are prominent suppliers, with ongoing investments in expanding SiC substrate and GaN epitaxy capacity. The demand for high-frequency, high-power RF amplifiers is expected to accelerate as 5G infrastructure densifies and new satellite constellations are deployed.
In the LED segment, GaN-on-sapphire and GaN-on-Si wafers remain foundational for both general lighting and display backlighting. OSRAM and Seoul Semiconductor continue to innovate in high-brightness and micro-LED technologies, with micro-LEDs poised for commercialization in next-generation displays and augmented reality devices. The focus is on improving wafer uniformity and defect reduction to enable mass production of smaller, more efficient emitters.
Emerging uses for nitride semiconductor wafers are rapidly gaining traction. AlN and AlGaN wafers are being explored for deep ultraviolet (DUV) LEDs, critical for sterilization and sensing applications. Companies such as HexaTech, Inc. (now part of AMD) are scaling up bulk AlN substrate production. Additionally, GaN’s potential in quantum computing, high-frequency photonics, and power IC integration is attracting significant R&D investment from both established players and startups.
Looking ahead, the nitride semiconductor wafer fabrication ecosystem is expected to see continued capacity expansion, process innovation, and diversification of substrate materials, supporting the evolving needs of power, RF, optoelectronic, and emerging quantum and photonic device markets.
Regional Analysis: Asia-Pacific Leadership and Global Expansion
The Asia-Pacific region continues to dominate the global nitride semiconductor wafer fabrication landscape in 2025, driven by robust investments, advanced manufacturing infrastructure, and a concentration of leading industry players. Countries such as Japan, South Korea, China, and Taiwan are at the forefront, leveraging their established semiconductor ecosystems and government-backed initiatives to accelerate innovation and capacity expansion.
Japan remains a pivotal hub, with companies like Sumitomo Chemical and Mitsubishi Chemical Group maintaining leadership in gallium nitride (GaN) and silicon carbide (SiC) wafer production. These firms are investing in next-generation substrates and epitaxial technologies to meet the surging demand for power electronics and RF devices. Japan’s focus on quality and process innovation continues to set global benchmarks, particularly in high-purity, large-diameter wafers.
South Korea is rapidly scaling its presence, with Samsung Electronics and LG investing in compound semiconductor fabs and R&D. These companies are targeting applications in 5G, automotive, and energy-efficient devices, with a particular emphasis on vertical integration and supply chain security. The Korean government’s strategic support for semiconductor self-sufficiency is expected to further boost domestic nitride wafer production through 2025 and beyond.
China’s expansion is marked by aggressive capacity build-up and technology acquisition. Firms such as San’an Optoelectronics and China Aerospace Science and Industry Corporation are scaling up GaN and AlN wafer output, supported by substantial state funding and local ecosystem development. China’s focus on indigenizing key materials and equipment is expected to narrow the technology gap with established players, with new fabs coming online in 2025 to serve both domestic and export markets.
Taiwan, home to Epistar and TSMC, continues to be a global center for LED and power device wafer fabrication. Taiwanese firms are investing in advanced epitaxy and substrate technologies, with a growing emphasis on GaN-on-Si and SiC platforms for next-generation power and RF applications. Collaborative efforts between industry and academia are fostering innovation and workforce development, ensuring Taiwan’s competitiveness in the evolving market.
Looking ahead, the Asia-Pacific region is expected to consolidate its leadership in nitride semiconductor wafer fabrication, with ongoing investments in capacity, R&D, and supply chain resilience. As global demand for high-performance power, RF, and optoelectronic devices accelerates, the region’s integrated approach and technological advancements will continue to shape the industry’s trajectory through the remainder of the decade.
Supply Chain and Raw Material Dynamics
The supply chain and raw material dynamics for nitride semiconductor wafer fabrication are undergoing significant transformation as the industry responds to surging demand for high-performance electronics, power devices, and optoelectronics in 2025 and beyond. Gallium nitride (GaN) and aluminum nitride (AlN) wafers, in particular, are at the center of this evolution, with their supply chains shaped by both upstream material availability and downstream processing capabilities.
A critical factor in nitride wafer fabrication is the secure and consistent supply of high-purity raw materials, notably gallium, aluminum, and high-quality substrates such as sapphire, silicon carbide (SiC), and bulk GaN. The global gallium supply remains concentrated, with primary production dominated by a handful of companies in Asia and Europe. For instance, Samsung and Sumitomo Chemical are among the key players in the production and processing of GaN substrates, leveraging proprietary hydride vapor phase epitaxy (HVPE) and ammonothermal growth techniques to improve wafer quality and yield.
The supply chain for sapphire and SiC substrates, essential for GaN epitaxy, is also consolidating. Kyocera and Showa Denko are recognized for their vertically integrated operations, spanning from raw material synthesis to finished wafer products. These companies are investing in capacity expansion and automation to address bottlenecks and reduce lead times, especially as electric vehicle (EV) and 5G infrastructure markets drive up demand for power and RF devices.
Aluminum nitride wafer supply is more niche but growing, with HexaTech (now part of ams OSRAM) and Toyota Tsusho advancing bulk AlN crystal growth and wafering technologies. These efforts are crucial for next-generation UV optoelectronics and high-frequency applications, where material purity and defect density are critical.
Geopolitical factors and trade policies continue to influence the nitride semiconductor supply chain. The industry is witnessing increased efforts toward regionalization and supply chain resilience, with companies in the US, Japan, and Europe seeking to localize critical material production and reduce reliance on single-source suppliers. For example, Wolfspeed (formerly Cree) is expanding its SiC and GaN wafer manufacturing footprint in the US, aiming to secure domestic supply for power electronics.
Looking ahead, the outlook for nitride semiconductor wafer supply chains in 2025 and the following years is one of cautious optimism. While capacity expansions and technological advancements are expected to alleviate some constraints, the sector remains sensitive to raw material price volatility and geopolitical shifts. Strategic partnerships, vertical integration, and investment in recycling and alternative material sources are likely to shape the competitive landscape as the industry scales to meet the demands of electrification, connectivity, and advanced photonics.
Challenges: Yield, Cost, and Scalability Barriers
Nitride semiconductor wafer fabrication, particularly for gallium nitride (GaN) and aluminum gallium nitride (AlGaN) devices, faces persistent challenges in yield, cost, and scalability as the industry moves through 2025 and into the coming years. These barriers are central to the economics and feasibility of expanding nitride-based technologies into mainstream applications such as power electronics, RF devices, and advanced optoelectronics.
A primary challenge remains the high defect density in nitride wafers, especially when grown on foreign substrates like sapphire or silicon. Threading dislocations, which can exceed 108 cm-2 in conventional processes, directly impact device reliability and yield. While native GaN substrates offer lower defect densities, their production is limited by high costs and small diameters, typically not exceeding 4 inches as of 2025. Leading manufacturers such as Ammono and Sumitomo Chemical have made progress in bulk GaN crystal growth, but scaling to larger wafer sizes remains a significant technical and economic hurdle.
Cost is further exacerbated by the complexity of epitaxial growth techniques like metal-organic chemical vapor deposition (MOCVD) and hydride vapor phase epitaxy (HVPE). These processes require precise control and expensive precursors, contributing to high capital and operational expenditures. Companies such as Kyocera and Ferrotec are actively developing advanced MOCVD reactors and process optimizations to improve throughput and uniformity, but the cost per wafer remains significantly higher than for silicon-based technologies.
Scalability is another critical barrier. The transition to larger wafer diameters (6-inch and beyond) is essential for cost reduction and compatibility with existing semiconductor fabs. However, issues such as wafer bowing, cracking, and uniformity loss become more pronounced at larger sizes. Pureon and Soraa are among the companies exploring novel substrate engineering and surface preparation techniques to address these issues, but widespread adoption is still in its early stages.
Looking ahead, the industry outlook for 2025 and the next few years suggests incremental improvements rather than disruptive breakthroughs. Collaborative efforts between substrate suppliers, equipment manufacturers, and device makers are expected to yield gradual reductions in defect densities and incremental cost improvements. However, unless significant advances in bulk nitride crystal growth and high-throughput epitaxy are realized, yield, cost, and scalability will continue to constrain the broader adoption of nitride semiconductor wafers in high-volume markets.
Future Outlook: Disruptive Technologies and Long-Term Market Opportunities
The future of nitride semiconductor wafer fabrication is poised for significant transformation as disruptive technologies and evolving market demands shape the industry landscape through 2025 and beyond. Gallium nitride (GaN) and aluminum gallium nitride (AlGaN) wafers are at the forefront, driven by their superior electronic and optoelectronic properties compared to traditional silicon. The next few years are expected to witness accelerated adoption of advanced fabrication techniques, such as hydride vapor phase epitaxy (HVPE), metal-organic chemical vapor deposition (MOCVD), and ammonothermal growth, which promise higher yields, larger wafer diameters, and improved crystal quality.
Key industry players are investing heavily in scaling up production and refining processes. Nichia Corporation, a global leader in nitride materials, continues to expand its manufacturing capabilities, focusing on high-brightness LEDs and power devices. Cree, Inc. (now operating as Wolfspeed) is advancing 200 mm GaN-on-SiC wafer technology, targeting high-frequency and high-power applications in 5G, electric vehicles, and renewable energy. Kyocera Corporation and Sumitomo Chemical are also scaling up their nitride wafer production, with a focus on both substrate and epitaxial wafer supply for global device manufacturers.
Emerging disruptive technologies include the integration of GaN-on-silicon (GaN-on-Si) and GaN-on-silicon carbide (GaN-on-SiC) platforms, which are expected to lower costs and enable mass-market penetration in power electronics and RF devices. The transition to 200 mm wafers is a critical milestone, as it aligns nitride semiconductor manufacturing with mainstream silicon processes, facilitating higher throughput and cost efficiencies. Companies such as ROHM Co., Ltd. and pSemi Corporation (a Murata company) are actively developing GaN-based solutions for automotive and wireless infrastructure, signaling robust demand growth.
Looking ahead, the market is set to benefit from the electrification of transportation, expansion of 5G networks, and the proliferation of high-efficiency power conversion systems. Strategic partnerships and investments in R&D are expected to accelerate innovation, with a focus on defect reduction, larger wafer sizes, and integration with complementary technologies such as silicon photonics. As the ecosystem matures, nitride semiconductor wafer fabrication is likely to become a cornerstone of next-generation electronics, unlocking new opportunities in energy, communications, and advanced sensing applications.
Sources & References
- Sumitomo Chemical
- Ferrotec Holdings Corporation
- Wolfspeed, Inc.
- Soraa
- HexaTech
- Wolfspeed, Inc.
- Sumitomo Electric Industries, Ltd.
- Nichia Corporation
- AIXTRON SE
- Veeco Instruments Inc.
- Mitsubishi Chemical Group
- Monocrystal
- NexGen Power Systems
- Infineon Technologies AG
- NXP Semiconductors
- imec
- OSRAM
- Seoul Semiconductor
- Mitsubishi Chemical Group
- LG
- San’an Optoelectronics
- Epistar
- ams OSRAM
- Toyota Tsusho
- Pureon
- ROHM Co., Ltd.
- pSemi Corporation