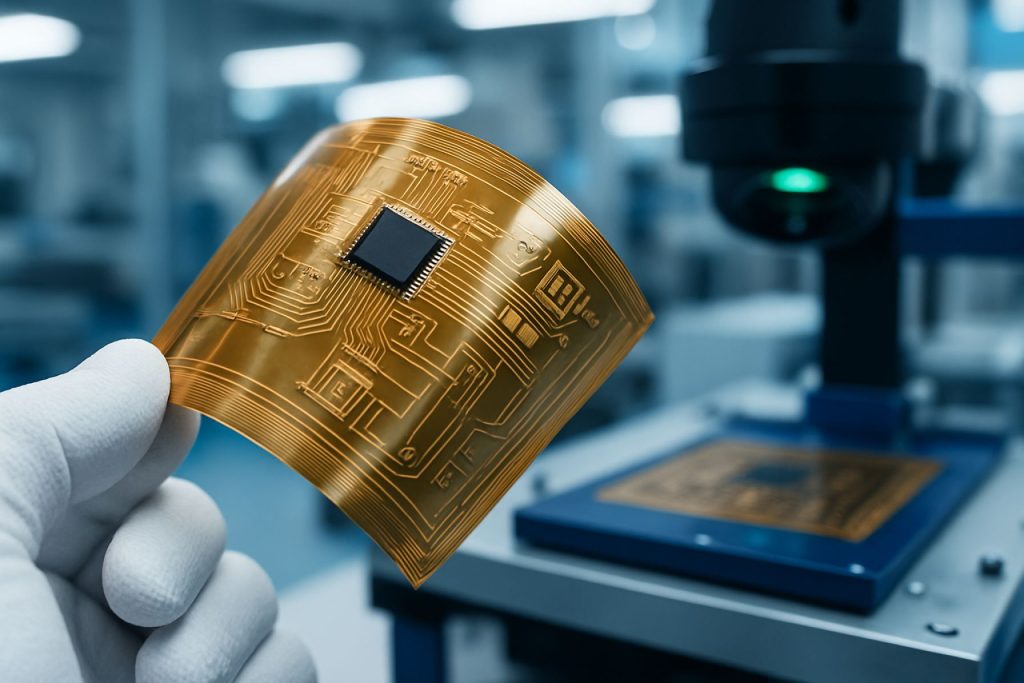
Flexible Electronics Manufacturing in 2025: Unleashing Next-Gen Devices and Market Expansion. Explore How Advanced Materials and Scalable Production Are Transforming the Industry Landscape.
- Executive Summary: Key Trends and Market Drivers in 2025
- Market Size and Growth Forecast (2025–2030): CAGR and Revenue Projections
- Breakthrough Technologies: Materials, Processes, and Integration
- Major Players and Strategic Partnerships (with Official Sources)
- Emerging Applications: Wearables, IoT, Healthcare, and Automotive
- Supply Chain Dynamics and Manufacturing Scalability
- Regulatory Landscape and Industry Standards (e.g., ieee.org)
- Regional Analysis: North America, Europe, Asia-Pacific, and Rest of World
- Investment, M&A, and Startup Ecosystem
- Future Outlook: Opportunities, Challenges, and Disruptive Potential
- Sources & References
Executive Summary: Key Trends and Market Drivers in 2025
Flexible electronics manufacturing is poised for significant growth in 2025, driven by advances in materials science, process innovation, and expanding end-use applications. The sector is characterized by the production of electronic circuits and devices on flexible substrates such as plastic, metal foil, or paper, enabling new form factors and integration possibilities across industries. Key trends shaping the market include the proliferation of wearable devices, the integration of flexible displays in consumer electronics, and the adoption of flexible sensors in automotive and healthcare sectors.
Major manufacturers are scaling up production capacities and investing in next-generation fabrication techniques. Samsung Electronics continues to lead in flexible OLED display manufacturing, supplying panels for smartphones, foldable devices, and emerging applications in automotive dashboards. LG Display is also expanding its flexible OLED and plastic-based display lines, targeting both consumer and commercial markets. In the United States, Kateeva specializes in inkjet printing equipment for flexible OLED mass production, supporting global display makers in improving yield and reducing costs.
Material innovation remains a core driver. DuPont and Kuraray are advancing flexible substrates and conductive inks, enabling higher performance and durability for flexible circuits. 3M is developing adhesive and barrier films critical for device reliability and longevity. These material suppliers are collaborating closely with device manufacturers to tailor solutions for specific applications, such as medical patches, smart labels, and flexible photovoltaics.
The automotive sector is emerging as a significant adopter, with companies like Continental integrating flexible touch sensors and lighting into vehicle interiors. In healthcare, flexible biosensors and diagnostic patches are being commercialized by firms such as Nitto Denko, leveraging roll-to-roll manufacturing for scalable production.
Looking ahead, the outlook for flexible electronics manufacturing in 2025 and beyond is robust. Industry bodies such as SEMI and FlexTech Alliance are fostering collaboration across the supply chain, supporting standardization and workforce development. As manufacturing yields improve and costs decline, flexible electronics are expected to penetrate further into mainstream consumer, industrial, and medical markets, with new product launches and partnerships anticipated throughout the next few years.
Market Size and Growth Forecast (2025–2030): CAGR and Revenue Projections
The flexible electronics manufacturing sector is poised for robust expansion between 2025 and 2030, driven by surging demand across consumer electronics, automotive, healthcare, and industrial applications. Flexible electronics—encompassing flexible displays, sensors, batteries, and circuits—enable lightweight, bendable, and conformable devices, fueling innovation in wearables, foldable smartphones, medical patches, and smart packaging.
Major industry players are scaling up production capacities and investing in advanced manufacturing processes such as roll-to-roll printing, inkjet deposition, and hybrid integration. Samsung Electronics continues to lead in flexible OLED display manufacturing, supplying panels for smartphones, tablets, and emerging foldable devices. LG Display is expanding its flexible OLED and signage solutions, targeting both consumer and commercial markets. BOE Technology Group, a key Chinese manufacturer, is ramping up flexible AMOLED production lines to meet global demand, while Royole Corporation focuses on ultra-thin flexible sensors and displays for next-generation electronics.
In the materials domain, companies like DuPont and Kuraray are innovating in flexible substrates, conductive inks, and encapsulation materials, which are critical for device reliability and mass production. Toppan and Nitto Denko are also advancing flexible printed circuit technologies, supporting the integration of flexible components into diverse end products.
Industry associations such as the SEMI and the FlexTech Alliance report that the global flexible electronics market is expected to achieve a compound annual growth rate (CAGR) in the high single digits to low double digits through 2030. Revenue projections for the sector are anticipated to surpass tens of billions of US dollars by the end of the decade, with flexible displays and sensors representing the largest revenue segments. The proliferation of 5G, IoT, and smart healthcare devices is expected to further accelerate adoption and market growth.
Looking ahead, the flexible electronics manufacturing landscape will be shaped by continued investments in R&D, strategic partnerships between material suppliers and device makers, and the scaling of high-throughput, cost-effective production lines. As leading manufacturers and material innovators expand their global footprint, the sector is set to play a pivotal role in the evolution of next-generation electronic devices through 2025 and beyond.
Breakthrough Technologies: Materials, Processes, and Integration
Flexible electronics manufacturing is undergoing rapid transformation in 2025, driven by advances in materials science, scalable processes, and integration techniques. The sector is characterized by the convergence of organic and inorganic materials, roll-to-roll (R2R) processing, and hybrid integration, enabling new applications in wearables, healthcare, automotive, and IoT devices.
A key breakthrough in 2025 is the maturation of solution-processable semiconductors and conductors, such as organic polymers, metal nanowires, and carbon-based materials. Companies like Kuraray and DuPont are advancing polymer substrates and conductive inks, which offer mechanical flexibility and compatibility with large-area printing. Kuraray has expanded its production of high-performance polyimide films, crucial for flexible displays and circuits, while DuPont continues to develop silver nanowire inks for transparent electrodes.
Roll-to-roll (R2R) manufacturing is now a cornerstone of flexible electronics production, enabling high-throughput fabrication of devices on plastic films. Samsung Electronics and LG Electronics have both scaled up R2R lines for flexible OLED displays, with 2025 seeing increased yields and reduced defect rates. These improvements are attributed to better web handling, in-line inspection, and encapsulation technologies. LG Electronics has also demonstrated hybrid integration, combining printed sensors with conventional silicon ICs for smart labels and medical patches.
Integration of flexible components with rigid electronics remains a technical challenge, but progress is evident. TDK Corporation and Murata Manufacturing are commercializing flexible passive components—such as capacitors and inductors—using ceramic-polymer composites, which can be embedded into flexible substrates. This enables the creation of fully flexible electronic systems, reducing the need for rigid interposers.
In terms of process innovation, additive manufacturing and laser patterning are gaining traction. Xerox has expanded its printed electronics platform, offering digital printing of circuits for rapid prototyping and low-volume production. Laser-based patterning, adopted by Coherent Corp., allows precise structuring of thin films without damaging underlying layers, supporting finer features and higher device densities.
Looking ahead, the outlook for flexible electronics manufacturing is robust. Industry leaders are investing in pilot lines and ecosystem partnerships to accelerate commercialization. The next few years are expected to see broader adoption in automotive interiors, smart packaging, and biomedical devices, as reliability and cost targets are met. The sector’s growth is underpinned by ongoing collaboration between material suppliers, equipment manufacturers, and device integrators, ensuring a dynamic and innovative landscape through the remainder of the decade.
Major Players and Strategic Partnerships (with Official Sources)
The flexible electronics manufacturing sector in 2025 is characterized by a dynamic landscape of established industry leaders, innovative startups, and a growing web of strategic partnerships. These collaborations are driving advancements in materials, processes, and end-use applications, particularly in wearables, medical devices, automotive, and consumer electronics.
Among the most prominent players, Samsung Electronics continues to lead in flexible display technology, leveraging its expertise in OLED and AMOLED panels for smartphones, foldable devices, and emerging applications. The company’s ongoing investments in flexible and foldable display production lines underscore its commitment to scaling up manufacturing capacity and maintaining technological leadership.
Another key player, LG Display, has expanded its flexible OLED production, targeting both consumer electronics and automotive sectors. LG’s partnerships with global automakers and device manufacturers are expected to accelerate the adoption of flexible displays in dashboards, infotainment systems, and next-generation mobile devices.
In the United States, Kateeva specializes in inkjet printing equipment for flexible OLED and printed electronics manufacturing. The company’s collaborations with Asian display giants have enabled mass production of high-yield, large-area flexible panels, supporting the rapid commercialization of foldable and rollable devices.
On the materials front, DuPont is a major supplier of advanced conductive inks, flexible substrates, and encapsulation materials. DuPont’s strategic alliances with electronics manufacturers and research institutions are focused on improving the reliability and scalability of flexible circuits and sensors, particularly for medical and industrial IoT applications.
In Europe, Heliatek is a leader in organic photovoltaic (OPV) films, producing ultra-lightweight, flexible solar modules for integration into building materials and consumer products. The company’s partnerships with construction and automotive firms are expected to drive new use cases for energy-harvesting flexible electronics.
Strategic partnerships are also evident in the automotive sector, where companies like Continental are collaborating with electronics and materials suppliers to develop flexible touch sensors, lighting, and smart surfaces for next-generation vehicle interiors.
Looking ahead, the flexible electronics manufacturing ecosystem is poised for further consolidation and cross-industry collaboration. As demand for flexible, lightweight, and durable electronic components grows, major players are expected to deepen their partnerships with material innovators, equipment suppliers, and end-users, accelerating the commercialization of new products and expanding the market’s reach through 2025 and beyond.
Emerging Applications: Wearables, IoT, Healthcare, and Automotive
Flexible electronics manufacturing is rapidly advancing, enabling a new generation of applications across wearables, IoT, healthcare, and automotive sectors. As of 2025, the industry is witnessing significant investments and product launches, driven by the demand for lightweight, conformable, and durable electronic components.
In the wearables segment, flexible electronics are foundational to the development of next-generation smartwatches, fitness trackers, and health monitoring patches. Companies such as LG Electronics and Samsung Electronics have been at the forefront, integrating flexible OLED displays and sensors into consumer devices. LG Electronics has showcased rollable and bendable display prototypes, while Samsung Electronics continues to commercialize foldable smartphones and is expanding its flexible display technology into wearable health devices.
The Internet of Things (IoT) is another major beneficiary. Flexible printed circuit boards (PCBs) and sensors are enabling the proliferation of connected devices in smart homes, logistics, and industrial automation. TDK Corporation and Murata Manufacturing Co., Ltd. are notable for their development of flexible sensors and components tailored for IoT nodes, focusing on miniaturization and energy efficiency.
Healthcare applications are seeing a surge in flexible, skin-adherent electronics for continuous physiological monitoring. Royole Corporation and Nitto Denko Corporation are actively developing flexible substrates and sensor arrays for medical patches and diagnostic devices. These technologies are being integrated into remote patient monitoring systems, with the potential to improve chronic disease management and early detection.
In the automotive sector, flexible electronics are being adopted for interior displays, lighting, and sensor integration. Continental AG and DENSO Corporation are investing in flexible touch panels, OLED displays, and in-cabin environmental sensors. These innovations support the trend toward smart, connected vehicles and advanced driver-assistance systems (ADAS).
Looking ahead, the outlook for flexible electronics manufacturing remains robust. Industry leaders are scaling up production capacities and refining roll-to-roll manufacturing processes to meet growing demand. The convergence of material science advancements and scalable fabrication techniques is expected to further reduce costs and expand the range of applications through 2025 and beyond.
Supply Chain Dynamics and Manufacturing Scalability
The supply chain dynamics and manufacturing scalability of flexible electronics are undergoing significant transformation as the sector matures in 2025. Flexible electronics—encompassing flexible displays, sensors, photovoltaics, and wearable devices—require specialized materials, novel fabrication processes, and robust integration strategies. The industry is characterized by a complex, multi-tiered supply chain involving material suppliers, equipment manufacturers, contract manufacturers, and end-product OEMs.
Key material suppliers such as Kuraray and DuPont continue to expand their portfolios of high-performance polymers, conductive inks, and barrier films, which are foundational for roll-to-roll (R2R) and sheet-to-sheet (S2S) manufacturing. Kuraray has invested in scaling up production of polyvinyl alcohol (PVA) and other specialty films, while DuPont has introduced new generations of stretchable and transparent conductive materials tailored for flexible circuits and displays.
On the equipment side, companies like Meyer Burger Technology AG and Roland DG Corporation are advancing R2R printing and coating systems, enabling higher throughput and improved yield for flexible substrates. These advancements are critical for scaling up production to meet growing demand in consumer electronics, automotive, and medical sectors.
Contract manufacturers such as Flex Ltd. and Jabil Inc. are playing a pivotal role in bridging the gap between prototyping and mass production. Both companies have expanded their flexible electronics manufacturing capabilities, leveraging global supply chain networks and advanced automation to support rapid scaling and customization. Flex Ltd. has established dedicated innovation centers for printed and flexible electronics, while Jabil Inc. is integrating flexible hybrid electronics (FHE) into its high-volume manufacturing lines.
Despite these advances, the sector faces ongoing challenges in supply chain resilience, particularly regarding the sourcing of specialty materials and the qualification of new suppliers. Geopolitical tensions and logistics disruptions continue to impact lead times and costs. Industry consortia such as SEMI are working to standardize materials and processes, aiming to reduce fragmentation and improve interoperability across the value chain.
Looking ahead, the outlook for manufacturing scalability is positive, with major OEMs and suppliers investing in capacity expansion and digitalization. The adoption of digital twins, AI-driven process control, and end-to-end traceability is expected to further streamline production and enhance supply chain visibility. As flexible electronics move toward mainstream adoption in 2025 and beyond, the ability to rapidly scale manufacturing while maintaining quality and cost competitiveness will be a defining factor for industry leaders.
Regulatory Landscape and Industry Standards (e.g., ieee.org)
The regulatory landscape and industry standards for flexible electronics manufacturing are evolving rapidly as the sector matures and applications proliferate across consumer electronics, healthcare, automotive, and industrial markets. In 2025, regulatory bodies and standards organizations are intensifying efforts to harmonize requirements, ensure product safety, and facilitate global market access for flexible and printed electronics.
A cornerstone of standardization in this field is the work of the IEEE, which continues to develop and update standards relevant to flexible electronics, such as those governing flexible circuit reliability, interconnects, and testing methodologies. The IEEE’s standards, including those for flexible hybrid electronics (FHE), are increasingly referenced by manufacturers and integrators to ensure interoperability and quality. In parallel, the International Electrotechnical Commission (IEC) is advancing standards for printed electronics, focusing on material characterization, environmental testing, and performance metrics, which are critical for applications in medical devices and automotive components.
In the United States, the U.S. Food and Drug Administration (FDA) is actively engaging with flexible electronics manufacturers, particularly those developing wearable medical devices and implantable sensors. The FDA’s regulatory framework is adapting to address the unique challenges posed by flexible substrates, biocompatible materials, and novel device architectures. The agency is expected to release updated guidance on flexible medical electronics by late 2025, reflecting input from industry consortia and academic partners.
Environmental and sustainability regulations are also shaping manufacturing practices. The European Union’s European Commission is enforcing stricter requirements under the RoHS and REACH directives, compelling manufacturers to minimize hazardous substances in flexible electronic components and ensure traceability of materials. These regulations are prompting leading companies such as Samsung Electronics and LG Electronics to invest in greener materials and closed-loop recycling processes for flexible displays and sensors.
Industry alliances, such as the SEMI Flexible Hybrid Electronics (FHE) initiative, are playing a pivotal role in pre-competitive standardization, roadmapping, and best practice dissemination. SEMI’s collaborative efforts with manufacturers, material suppliers, and equipment vendors are expected to yield new process and reliability standards by 2026, supporting the scale-up of roll-to-roll and additive manufacturing techniques.
Looking ahead, the regulatory and standards environment for flexible electronics manufacturing will continue to tighten, with a focus on safety, sustainability, and cross-border harmonization. Companies that proactively engage with standards bodies and adapt to evolving requirements are likely to gain a competitive edge as the market expands through 2025 and beyond.
Regional Analysis: North America, Europe, Asia-Pacific, and Rest of World
The global landscape for flexible electronics manufacturing in 2025 is marked by dynamic regional developments, with North America, Europe, and Asia-Pacific (APAC) leading innovation and scaling production, while the Rest of World (RoW) regions are gradually increasing their participation. Each region exhibits distinct strengths, driven by local industry clusters, government initiatives, and the presence of major manufacturers.
North America remains a hub for research and high-value manufacturing in flexible electronics, particularly in the United States. The region benefits from a robust ecosystem of technology companies, research universities, and government-backed initiatives. Companies such as DuPont and 3M are at the forefront, leveraging advanced materials and process innovations for applications in wearables, medical devices, and automotive sectors. The U.S. government continues to support flexible hybrid electronics through programs like the NextFlex Manufacturing USA initiative, fostering collaboration between industry and academia. In Canada, firms like Innovia Films contribute to the supply chain, particularly in specialty substrates.
Europe is characterized by strong public-private partnerships and a focus on sustainability and advanced manufacturing. Germany, the Netherlands, and the UK are notable centers, with companies such as Merck KGaA (specialty chemicals and materials) and Heliatek (organic photovoltaics) driving innovation. The European Union’s Horizon Europe program continues to fund flexible electronics R&D, emphasizing energy efficiency and circular economy principles. The region is also seeing increased investment in printed electronics for smart packaging and IoT applications.
Asia-Pacific dominates in terms of manufacturing scale and supply chain integration. South Korea, Japan, China, and Taiwan are home to leading display and semiconductor manufacturers. Samsung Electronics and LG Electronics are global leaders in flexible OLED displays, with ongoing investments in next-generation production lines. In China, BOE Technology Group and TCL Technology are expanding capacity for flexible panels and printed electronics, supported by government incentives and a vast supplier network. Japan’s Fujifilm and Panasonic continue to innovate in flexible sensors and substrates.
Rest of World regions, including parts of Latin America and the Middle East, are emerging as new markets for flexible electronics, primarily through partnerships and technology transfer. While local manufacturing is limited, countries such as Israel and Brazil are investing in R&D and pilot production, aiming to participate in global value chains over the next few years.
Looking ahead, regional strengths are expected to persist, with Asia-Pacific maintaining manufacturing leadership, North America and Europe focusing on high-value applications and innovation, and RoW regions gradually increasing their footprint through targeted investments and collaborations.
Investment, M&A, and Startup Ecosystem
The flexible electronics manufacturing sector is experiencing robust investment activity and a dynamic startup ecosystem as of 2025, driven by surging demand for bendable displays, wearable devices, and next-generation sensors. Major electronics manufacturers and material suppliers are strategically investing in capacity expansion, technology partnerships, and acquisitions to secure their positions in this rapidly evolving market.
Leading global players such as Samsung Electronics and LG Electronics continue to allocate significant capital towards flexible OLED and advanced display production lines. In 2024, Samsung announced further investments in its Asan plant to boost flexible OLED output, targeting both mobile and automotive applications. Similarly, LG has expanded its Paju facility, focusing on large-area flexible displays for TVs and commercial signage. These investments are complemented by collaborations with material innovators like Kolon Industries, which supplies high-performance polyimide films essential for flexible substrates.
The startup landscape is vibrant, with companies such as Polaris Electronics and FlexEnable attracting venture capital for their proprietary flexible transistor and sensor technologies. FlexEnable, based in the UK, has secured multiple funding rounds to scale up its organic transistor platform, enabling ultra-thin, lightweight displays and biometric sensors. In Asia, startups like Royole Corporation have commercialized fully flexible smartphones and are licensing their technology to global OEMs.
Mergers and acquisitions are shaping the competitive landscape. In late 2024, BOE Technology Group acquired a controlling stake in a domestic flexible electronics startup to accelerate its R&D in foldable and rollable displays. Meanwhile, Japan Display Inc. has entered joint ventures with material suppliers to secure next-generation flexible substrates and inks, aiming to diversify beyond traditional LCDs.
Industry organizations such as the SEMI and the IDTechEx (industry event organizer) are fostering collaboration through consortia and innovation challenges, connecting startups with established manufacturers and investors. These initiatives are expected to accelerate commercialization and standardization efforts.
Looking ahead, the flexible electronics manufacturing sector is poised for continued growth, with investment momentum likely to intensify as new applications in automotive interiors, medical devices, and smart packaging emerge. The interplay between established giants and agile startups will be critical in shaping the sector’s innovation trajectory through 2025 and beyond.
Future Outlook: Opportunities, Challenges, and Disruptive Potential
The future of flexible electronics manufacturing in 2025 and the coming years is marked by both significant opportunities and notable challenges, as the sector matures from research-driven innovation to large-scale commercial deployment. Flexible electronics—encompassing bendable displays, wearable sensors, flexible solar cells, and smart packaging—are poised to disrupt traditional electronics manufacturing paradigms, driven by advances in materials science, roll-to-roll processing, and integration techniques.
Key industry players are scaling up production capabilities to meet anticipated demand. Samsung Electronics continues to lead in flexible OLED displays, with its foldable smartphones and tablets setting benchmarks for durability and mass-market appeal. LG Electronics is also expanding its flexible display portfolio, targeting automotive and signage applications. In the United States, Flex Ltd. is investing in advanced manufacturing lines for flexible circuit boards and wearable medical devices, leveraging its global supply chain expertise.
The opportunities in this sector are vast. The proliferation of the Internet of Things (IoT) and the demand for lightweight, conformable electronics in healthcare, automotive, and consumer sectors are accelerating adoption. For example, Jabil Inc. is collaborating with medical device companies to produce flexible biosensors and smart patches, aiming to address the growing market for remote patient monitoring. Meanwhile, Konica Minolta is advancing printed electronics for smart labels and packaging, enabling real-time tracking and authentication in logistics and retail.
However, challenges remain. Manufacturing yield, material reliability, and cost competitiveness are persistent hurdles. The transition from pilot-scale to high-volume production requires robust quality control and scalable processes. Environmental sustainability is also a concern, as flexible substrates and inks must meet recyclability and safety standards. Industry consortia and standards bodies, such as the SEMI association, are working to establish best practices and interoperability standards to facilitate ecosystem growth.
Looking ahead, the disruptive potential of flexible electronics lies in their ability to enable entirely new product categories and user experiences. As manufacturing technologies mature and costs decline, flexible electronics are expected to penetrate mainstream markets, from rollable TVs to e-textiles and smart medical implants. Strategic partnerships between material suppliers, device manufacturers, and end-users will be critical to overcoming technical and commercial barriers, ensuring that flexible electronics fulfill their promise as a transformative force in the electronics industry.
Sources & References
- LG Display
- Kateeva
- DuPont
- Kuraray
- BOE Technology Group
- Toppan
- Murata Manufacturing
- Xerox
- Coherent Corp.
- Heliatek
- Meyer Burger Technology AG
- Roland DG Corporation
- Flex Ltd.
- IEEE
- European Commission
- Innovia Films
- Fujifilm
- Kolon Industries
- FlexEnable
- Japan Display Inc.
- IDTechEx