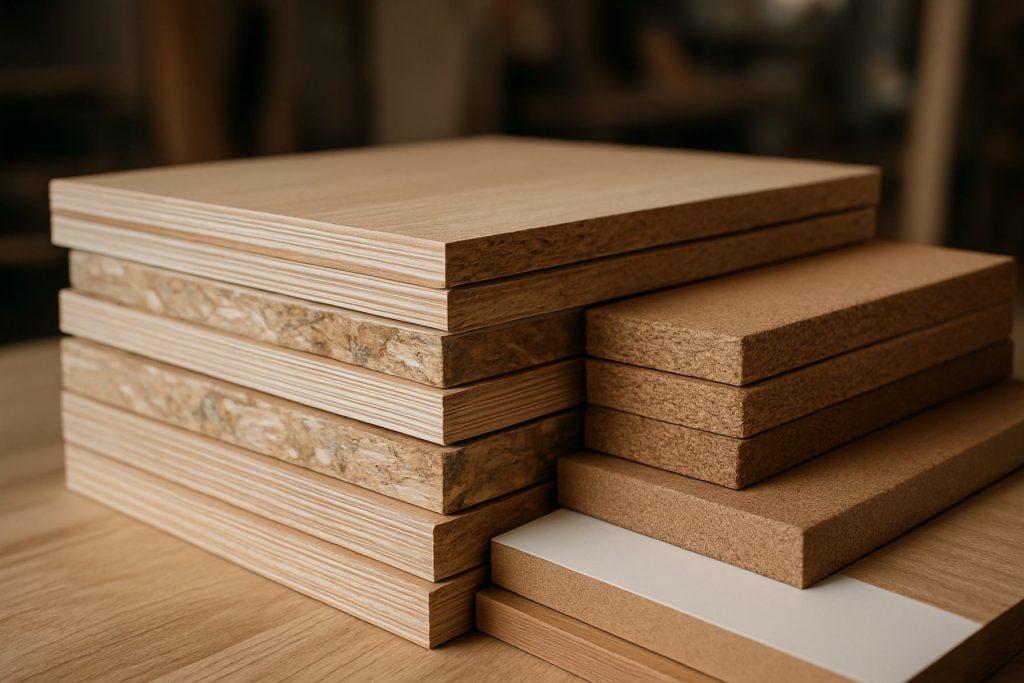
Table of Contents
- Executive Summary: 2025 Snapshot & Key Takeaways
- Technology Overview: Advances in Veneer-Based Nanocomposites
- Market Sizing & Forecast: 2025–2030 Growth Trajectory
- Key Industry Players: Profiles & Strategic Initiatives
- Applications & End-Use Sectors: Construction, Furniture, and Beyond
- Innovation Pipeline: Research, Patents, and Breakthroughs
- Sustainability & Environmental Impact: Certifications and Compliance
- Regulatory Landscape: Standards and Policy Developments
- Investment & Funding Trends: Venture Capital and Public Initiatives
- Future Outlook: Opportunities, Challenges, and Roadmap to 2030
- Sources & References
Executive Summary: 2025 Snapshot & Key Takeaways
In 2025, veneer-based engineered wood nanocomposites are positioned at the intersection of sustainability, performance enhancement, and technological innovation within the wood products sector. This segment leverages thin wood veneers bonded with nanomaterial-enhanced adhesives or coatings, aiming to deliver superior mechanical properties, improved durability, and enhanced functionality compared to conventional engineered wood products. The integration of nanocomposites into veneer-based products aligns with rising demands for eco-friendly, high-performance construction and furniture materials.
Major industry players and research-active manufacturers have reported significant advances in nanotechnology applications for engineered wood in the past year. Companies such as Swiss Krono Group and Kronospan—recognized leaders in engineered wood production—have expanded research partnerships focused on nano-enhanced resins and coatings to improve moisture resistance and structural integrity of their veneer products. These collaborations target both mass-market plywood panels and premium architectural veneers, with pilot projects demonstrating up to 30% improvement in modulus of rupture and modulus of elasticity, according to industry-reported data.
In parallel, organizations like WoodWorks are actively disseminating best practices and technical guidelines for the adoption of advanced nanocomposite wood panels in commercial construction, with a focus on sustainability certification and lifecycle performance. The industry’s move towards formaldehyde-free and bio-based nanomaterials, such as nanocellulose and nano-silica, is gaining traction in response to evolving regulatory frameworks and green building standards.
The outlook for 2025 and beyond suggests acceleration in product commercialization, driven by investments in manufacturing scale-up and the rising cost-competitiveness of nanomaterials. Leading veneer and engineered wood manufacturers are expected to introduce new lines of nanocomposite panels targeting both structural and non-structural applications. Market adoption is likely to be most rapid in regions with progressive building codes and high sustainability requirements, including North America and Europe.
Key takeaways for stakeholders include the necessity to monitor advancements in nanomaterial sourcing, regulatory compliance, and end-user acceptance. Strategic alliances between wood manufacturers, nanotechnology suppliers, and construction industry organizations will be essential to realizing the full market potential of veneer-based engineered wood nanocomposites in the coming years.
Technology Overview: Advances in Veneer-Based Nanocomposites
Veneer-based engineered wood nanocomposites represent a significant advancement in the engineered wood sector, integrating nanoscale materials—such as nanocellulose, nano-silica, and nanoclays—into traditional veneer-based panels. This fusion aims to enhance mechanical strength, dimensional stability, water resistance, and fire retardancy, while still leveraging the renewable nature of wood. As of 2025, the technology is moving from laboratory-scale innovation towards pre-commercial and pilot manufacturing, driven by sustainability imperatives and market demand for high-performance, eco-friendly materials.
Current developments focus heavily on nanocellulose—derived from wood pulp—which is being incorporated into adhesives and coatings for plywood, laminated veneer lumber (LVL), and cross-laminated timber (CLT) products. Nanocellulose improves bonding between veneers, leading to panels with higher modulus of rupture (MOR) and modulus of elasticity (MOE). For instance, several research initiatives are ongoing at leading engineered wood manufacturers and suppliers, with pilot projects targeting the integration of nanocellulose as a bio-based reinforcement in veneer panels. Companies such as UPM-Kymmene Corporation and Metsä Group have publicly signaled interest and investments in nanocellulose technologies, aiming for scalable, industrial adoption in the coming years.
Nano-silica and nanoclay additives are also being explored for their barrier properties, imparting improved fire resistance and reduced moisture uptake. Prototype panels tested in 2024–2025 demonstrate approximately 20–30% higher resistance to water absorption and enhanced thermal stability compared to conventional veneer-based panels. The inclusion of nanomaterials, however, requires adaptation of existing manufacturing processes to ensure even dispersion and to mitigate potential health and safety risks for workers, a priority highlighted by industry bodies such as the APA – The Engineered Wood Association.
Manufacturers are also investigating environmentally friendly resin systems compatible with nanomaterial additives, aiming to reduce formaldehyde emissions and meet stricter regulatory standards anticipated in Europe, North America, and Asia-Pacific through 2027. Ongoing collaborations between engineered wood companies and chemical suppliers, such as BASF SE, are expected to accelerate the commercialization of these next-generation panels.
Looking ahead, veneer-based engineered wood nanocomposites are projected to move towards market-ready production lines by 2026–2027, with a focus on sustainable construction, furniture, and transport applications. The outlook is shaped by the dual drivers of performance enhancement and regulatory compliance, positioning nanocomposite panels as a transformative solution within the wood products industry.
Market Sizing & Forecast: 2025–2030 Growth Trajectory
The market for veneer-based engineered wood nanocomposites is set to experience dynamic growth from 2025 through 2030, fueled by rising demand for sustainable construction materials and advancements in nanotechnology integration. These composites, which incorporate nanomaterials such as nanocellulose or nano-silica into traditional veneer-based engineered wood products, are gaining traction due to their enhanced mechanical strength, durability, and resistance to moisture and fire.
In 2025, the adoption of nanocomposite technologies in engineered wood is moving beyond the pilot and demonstration phases, with several key manufacturers scaling up production. Companies like Roseburg Forest Products and Weyerhaeuser have publicly stated intentions to explore advanced material integration, including nanotechnology applications, to improve their veneer-based product lines. In parallel, organizations such as the Engineered Wood Products Association of Australasia are supporting innovation through technical standards and industry collaboration.
Global demand is being driven by increasing regulatory restrictions on traditional construction materials and a shift toward renewable, high-performance composites. The Asia-Pacific region is expected to be a significant market, particularly due to large-scale infrastructure development and urbanization in China and Southeast Asia. North America and Europe are anticipated to follow, leveraging strong green building initiatives and the advanced wood products sector.
Forecasts for the period 2025–2030 suggest annual growth rates in the engineered wood nanocomposites segment may reach 10–14%, outpacing conventional engineered wood product categories. By 2030, veneer-based nanocomposites are projected to represent a meaningful share of the overall engineered wood market, supported by cost reductions as manufacturing processes mature and supply chains for nanomaterials become more robust. Leading suppliers like SWISS KRONO Group and Kronospan are anticipated to expand their product portfolios, responding to both regulatory pressures and customer demand for higher-performance, sustainable materials.
Looking ahead, collaboration between nanomaterial producers and engineered wood manufacturers will be critical to overcoming technical and scale-up challenges. Industry bodies such as FPInnovations continue to play a pivotal role in standardization and performance testing, ensuring that veneer-based nanocomposites meet building codes and safety requirements. The outlook through 2030 is optimistic, with rapid innovation, regulatory support, and growing end-user acceptance driving market expansion.
Key Industry Players: Profiles & Strategic Initiatives
The veneer-based engineered wood nanocomposites sector has seen accelerated innovation and commercialization in 2025, with established wood products manufacturers and select nanomaterials suppliers driving new product development. Major industry players are leveraging nanotechnology to enhance traditional veneer-based products, focusing on improved mechanical properties, moisture resistance, and sustainability credentials.
Among the leaders, Weyerhaeuser Company has advanced its engineered wood portfolio with pilot-scale testing of cellulose nanofiber (CNF)-reinforced veneer panels. Their initiatives are focused on applications in structural plywood and laminated veneer lumber (LVL), with reported targets of higher strength-to-weight ratios and reduced resin consumption. The company’s public sustainability commitments are aligned with the integration of nanomaterials, aiming for reduced carbon footprint and lifecycle impacts across their construction product lines.
Another key actor, UPM-Kymmene Corporation, continues to invest in research partnerships for bio-based nanocomposite veneers. In 2025, UPM has expanded pilot collaborations with nanocellulose suppliers, aiming to scale up the use of nanofibrillated cellulose (NFC) in decorative and structural panels. The company emphasizes closed-loop manufacturing and recyclability, positioning nanocomposite veneers as an eco-friendly alternative to traditional engineered wood.
In North America, Boise Cascade Company has disclosed ongoing R&D efforts in hybrid veneer composites. Their focus is on integrating nano-silica and nano-clay additives to enhance fire resistance and dimensional stability in LVL products. Boise Cascade’s 2025 strategy includes partnerships with academic institutions and specialized nanomaterial manufacturers to accelerate product validation and certification.
On the nanomaterials supply side, CelluForce and Borregaard remain at the forefront, supplying cellulose nanocrystals (CNC) and microfibrillated cellulose (MFC), respectively, for large-scale industrial trials with engineered wood producers. Both companies have announced capacity expansions in 2025 to meet growing demand for nano-enhanced wood composites.
Strategically, industry leaders are prioritizing certifications for structural and environmental compliance, anticipating stricter building codes and consumer demand for low-emission, sustainable materials. Key players are also investing in digital traceability and process optimization to streamline the integration of nanomaterials into existing veneer-based manufacturing lines. The outlook for 2025 and beyond points to increased commercialization, with further alliances expected between nanomaterial innovators and established wood product brands.
Applications & End-Use Sectors: Construction, Furniture, and Beyond
Veneer-based engineered wood nanocomposites are rapidly gaining traction across diverse end-use sectors, particularly in construction and furniture, with promising outlooks for 2025 and the subsequent years. These advanced materials leverage nanotechnology enhancements—such as nano-silica or nano-clay integration—to deliver superior mechanical properties, improved durability, and enhanced resistance to moisture and biological degradation compared to traditional engineered wood products.
In the construction sector, leading manufacturers are incorporating nanocomposite veneers into structural and non-structural applications. This includes their use in load-bearing panels, decorative claddings, doors, and modular building systems. Companies such as Roseburg Forest Products and Weyerhaeuser are continuously advancing their engineered wood product portfolios, with ongoing research and development to integrate nano-enhanced resins and surface treatments. These efforts are aimed at meeting the growing demand for sustainable, high-performance building materials that conform to increasingly stringent environmental and fire safety standards.
The furniture and interiors industry is also a significant adopter of veneer-based engineered wood nanocomposites. Manufacturers are utilizing these materials to produce lightweight, aesthetically versatile, and highly durable furniture components. Enhanced scratch resistance and dimensional stability make nano-enhanced veneers particularly attractive for high-traffic public spaces, office environments, and residential cabinetry. Companies like SVEZA, a global plywood producer, are investing in product innovation to supply the furniture market with value-added, eco-efficient solutions.
Beyond these mainstream arenas, veneer-based nanocomposites are beginning to penetrate specialized sectors such as transportation (interior panels for trains, buses, and aircraft), marine (lightweight, water-resistant boat interiors), and even consumer electronics (durable casings and housings). The flexibility and tunability of nanocomposite veneers allow designers and engineers to address sector-specific requirements—such as reduced weight, improved acoustic performance, or customized aesthetics—thus broadening the scope of applications.
Looking ahead to 2025 and beyond, the outlook for veneer-based engineered wood nanocomposites remains robust. Market drivers include urbanization, the green building movement, and the ongoing quest for renewable materials with extended lifespans. Industry leaders are expected to accelerate investments in nanotechnology-driven product lines, while collaborations with research institutions and cross-sector partnerships will likely catalyze further breakthroughs in performance and application versatility.
Innovation Pipeline: Research, Patents, and Breakthroughs
The innovation pipeline for veneer-based engineered wood nanocomposites is experiencing significant momentum in 2025, driven by relentless research into sustainable construction materials and the pressing need for enhanced performance in wood products. Universities, industrial R&D labs, and global manufacturers are converging on the integration of nanomaterials—such as nanocellulose, graphene, and nano-silica—into traditional veneer-based engineered wood panels, like laminated veneer lumber (LVL) and plywood, to impart superior mechanical strength, water resistance, and fire retardancy.
Several patent filings in 2024–2025 indicate a shift from laboratory-scale to pre-commercialization strategies. Notably, manufacturers such as Huber Engineered Woods and Boise Cascade Company have disclosed proprietary nanocomposite formulations aimed at structural applications with improved life-cycle performance. In parallel, Metsä Wood and Swiss Krono Group are investing in pilot lines for nano-enhanced LVL, seeking to validate upscaling methods and environmental safety.
On the research front, collaborations between leading technical institutes and industry are accelerating. For example, several European consortia are evaluating the use of nanocellulose-infused veneer panels for modular construction, targeting reduced resin content and higher renewable material ratios. Early-stage testing reveals that the incorporation of less than 3% nanocellulose can increase flexural strength by up to 25% compared to conventional LVL, while also reducing emissions of volatile organic compounds (VOCs).
The regulatory landscape is also evolving. Organizations such as the Engineered Wood Products Association of Australasia and the APA – The Engineered Wood Association are engaging with stakeholders to update standards and safety testing protocols, recognizing the unique properties of nanomaterial-modified panels. Certification pathways are expected to be clarified by 2026, which could catalyze broader market adoption.
Looking ahead, the outlook remains promising. Manufacturers are preparing for pilot-scale launches of nano-enhanced veneer panels intended for high-performance building envelopes by late 2025. Ongoing breakthroughs in nanomaterial dispersion and cost-effective processing are expected to reduce barriers to commercialization. As environmental and durability credentials become quantifiable, veneer-based engineered wood nanocomposites are positioned to capture a growing share of sustainable construction projects globally.
Sustainability & Environmental Impact: Certifications and Compliance
In 2025, the sustainability and environmental impact of veneer-based engineered wood nanocomposites remain a central focus for manufacturers and regulatory bodies. These advanced materials, which incorporate nanomaterials such as nanocellulose or nanosilica into wood veneers, are designed to enhance mechanical properties while aiming to reduce environmental burdens compared to solid wood or conventional composites. As demand for sustainable construction and interior materials rises, the sector has increasingly aligned its operations with rigorous environmental certifications and compliance standards.
Key environmental certifications—such as Forest Stewardship Council (FSC) and Programme for the Endorsement of Forest Certification (PEFC)—are now frequently required for veneer sources in engineered wood nanocomposites. Companies like Georgia-Pacific and Weyerhaeuser have committed to sourcing wood from responsible and certified forests, ensuring the traceability of the raw materials used in their composite products. The integration of nanomaterials demands additional scrutiny: eco-toxicity, bioaccumulation, and end-of-life recycling of nanoparticles are areas under current assessment, as outlined in recent initiatives by the Forest Stewardship Council and other bodies.
In 2025, regulatory compliance extends beyond forestry. The European Union’s Construction Products Regulation (CPR) and the U.S. Environmental Protection Agency’s (EPA) formaldehyde emission standards (TSCA Title VI) have set strict thresholds on emissions and chemical safety. Major suppliers such as Aiko Group and West Fraser have responded by investing in low-emission resins and improved process controls for their nanocomposite panels. Life Cycle Assessment (LCA) is increasingly required to quantify the environmental impact of nanocomposite products from cradle to grave, supporting Environmental Product Declarations (EPDs) and green building certifications like LEED and BREEAM.
Looking ahead, industry outlook through the next few years anticipates further tightening of both voluntary and mandatory standards. The rise of circular economy principles is pushing manufacturers to design for disassembly and recyclability, with companies such as Stora Enso piloting closed-loop processes for engineered wood products. Moreover, the collaboration between industry and regulatory entities is expected to accelerate the development of new standards specifically addressing the unique characteristics of nanomaterials in wood composites. As the sector matures, transparent supply chains and third-party certification will remain critical for market acceptance and regulatory compliance.
Regulatory Landscape: Standards and Policy Developments
The regulatory landscape for veneer-based engineered wood nanocomposites is rapidly evolving as these advanced materials gain traction in construction, furniture, and specialty manufacturing sectors. As of 2025, regulatory authorities and industry bodies are revisiting standards to better address the unique attributes and potential risks of nanomaterials integrated within wood-based products.
Standardization organizations such as the ASTM International and International Organization for Standardization (ISO) have ongoing initiatives to update or develop new standards for engineered wood products incorporating nanomaterials. For example, ASTM has established committees to address the characterization, safety, and quality of engineered woods, with increasing attention to nanoscale additives and their influence on mechanical and environmental properties.
In North America, regulatory frameworks are being influenced by sustainability targets and environmental health concerns. Agencies such as the United States Environmental Protection Agency (EPA) are monitoring the use of nanomaterials in wood composites, particularly regarding emissions, workplace safety, and end-of-life disposal. These efforts align with broader moves in the engineered wood industry to meet stricter formaldehyde emission limits and promote low-VOC products. The EPA’s TSCA (Toxic Substances Control Act) inventory now includes several nanomaterials, and manufacturers such as Arauco and Weyerhaeuser are closely tracking these requirements as they integrate advanced technologies into their veneer-based offerings.
In the European Union, the European Chemicals Agency (ECHA) and the European Committee for Standardization (CEN) are reviewing technical standards for engineered wood, with discussions on the traceability and assessment of nanomaterial content. The EU’s “Strategy for Sustainable and Circular Textiles” and forthcoming updates to the Construction Products Regulation are expected to indirectly impact nanocomposite wood products by emphasizing lifecycle analysis and material transparency. Leading European manufacturers such as Kronospan are preparing to adapt to these shifts by enhancing product certification and material disclosure practices.
Looking ahead, the next several years will likely see the formal adoption of new harmonized standards and clearer labeling requirements for veneer-based engineered wood nanocomposites. The focus will remain on balancing innovation with environmental and human safety, as regulatory bodies, manufacturers, and international standardization organizations continue to collaborate to ensure responsible deployment of nanotechnology in wood composites.
Investment & Funding Trends: Venture Capital and Public Initiatives
In 2025, investment and funding in veneer-based engineered wood nanocomposites are being shaped by a convergence of sustainability imperatives, technological advancements, and supportive policy environments. Venture capital activity in the sector has intensified, reflecting growing confidence in the capacity of nanotechnology to transform traditional wood products into stronger, lighter, and more versatile construction materials. Several early-stage companies specializing in wood nanocomposite solutions have attracted funding rounds ranging from seed capital to Series B, with a particular emphasis on applications in green building and modular construction.
Major industry players such as Stora Enso and UPM have continued to invest in R&D for nanocellulose- and veneer-based composites, often partnering with startups and academic institutions to accelerate innovation. For instance, Stora Enso has highlighted nanomaterials as a strategic focus area, committing resources to pilot production facilities and collaborative research initiatives. Additionally, UPM has advanced its work on wood-derived nanomaterials, seeking to enhance the performance and sustainability of veneer products.
Public initiatives play a significant role in fostering sector growth. In the European Union, the United Nations Economic Commission for Europe (UNECE) and national innovation agencies continue to provide grants and subsidies for the development of advanced wood composites, targeting both emission reduction and circular economy goals. The EU’s Horizon Europe program, for example, has identified engineered biobased materials as a priority area for 2025, with dedicated funding streams for pilot projects and scale-up activities. In North America, similar trends are observed: agencies such as the U.S. Department of Agriculture and Natural Resources Canada are supporting commercialization efforts for wood nanocomposite technologies, including demonstration projects and market development initiatives.
Looking ahead, analysts expect the investment landscape to remain robust through the next few years, propelled by tightening regulations on carbon-intensive building materials and rising demand for renewable alternatives. Strategic partnerships between established timber companies and nanotech ventures are likely to proliferate, with a focus on scaling manufacturing capacities and improving product certifications. As both private and public capital continue to flow into the sector, veneer-based engineered wood nanocomposites are poised for accelerated adoption in mainstream construction and design markets.
Future Outlook: Opportunities, Challenges, and Roadmap to 2030
The future of veneer-based engineered wood nanocomposites is poised for transformative growth by 2030, driven by advancements in nanotechnology, increasing demand for sustainable materials, and evolving construction standards. As of 2025, manufacturers and research institutions are accelerating the integration of nanomaterials—such as nanocellulose, nano-silica, and graphene—into veneer-based composites. These enhancements provide superior mechanical strength, improved fire resistance, and enhanced durability, positioning the materials as attractive alternatives to both traditional engineered wood and non-renewable construction resources.
Global engineered wood leaders are investing in nanocomposite technologies to future-proof their product lines. For instance, Weyerhaeuser and UPM-Kymmene Corporation have signaled ongoing research into bio-based nanomaterials for veneer applications, aiming to capitalize on both performance and sustainability gains. European and Asian manufacturers, including Holzindustrie Schweighofer and Daiken Corporation, are similarly piloting nanotechnology-enhanced plywood and LVL (Laminated Veneer Lumber) products to meet stricter environmental regulations and the rising popularity of green buildings.
Opportunities abound in both developed and emerging markets. The construction sector’s growing emphasis on carbon footprint reduction is fueling interest in high-performance, renewable nanocomposites. These materials are increasingly specified in public infrastructure, modular construction, and high-rise timber buildings. Furthermore, the automotive and furniture industries are exploring veneer-based nanocomposites for lightweight, durable, and aesthetically versatile components. The rapid urbanization in Asia-Pacific and government incentives for sustainable building materials in North America and Europe further accelerate their adoption.
However, several challenges must be addressed over the next five years. Manufacturing scalability remains a primary hurdle, as the uniform dispersion and cost-effective incorporation of nanomaterials at commercial scale require technological advancements and robust supply chains. Health and safety assessments of nanomaterials throughout the product lifecycle are under scrutiny, with regulatory bodies tightening standards to ensure consumer and worker safety. Additionally, the sector must overcome market skepticism, particularly regarding long-term durability and recyclability, to achieve widespread acceptance.
Looking toward 2030, the roadmap for veneer-based engineered wood nanocomposites will likely focus on three pillars: scaling up green nanomaterial supply chains, standardizing testing and certification protocols in collaboration with bodies such as American Wood Council, and investing in automation and digitalization of production processes. Strategic partnerships between material innovators, wood product manufacturers, and regulatory agencies will be crucial to unlock the full potential of these advanced composites, positioning them as cornerstone materials in the next generation of sustainable construction and manufacturing.
Sources & References
- Kronospan
- UPM-Kymmene Corporation
- Metsä Group
- APA – The Engineered Wood Association
- BASF SE
- Roseburg Forest Products
- Weyerhaeuser
- Engineered Wood Products Association of Australasia
- Kronospan
- CelluForce
- Borregaard
- SVEZA
- Huber Engineered Woods
- Metsä Wood
- APA – The Engineered Wood Association
- Forest Stewardship Council
- West Fraser
- ASTM International
- International Organization for Standardization (ISO)
- European Chemicals Agency (ECHA)
- European Committee for Standardization (CEN)
- Holzindustrie Schweighofer
- Daiken Corporation