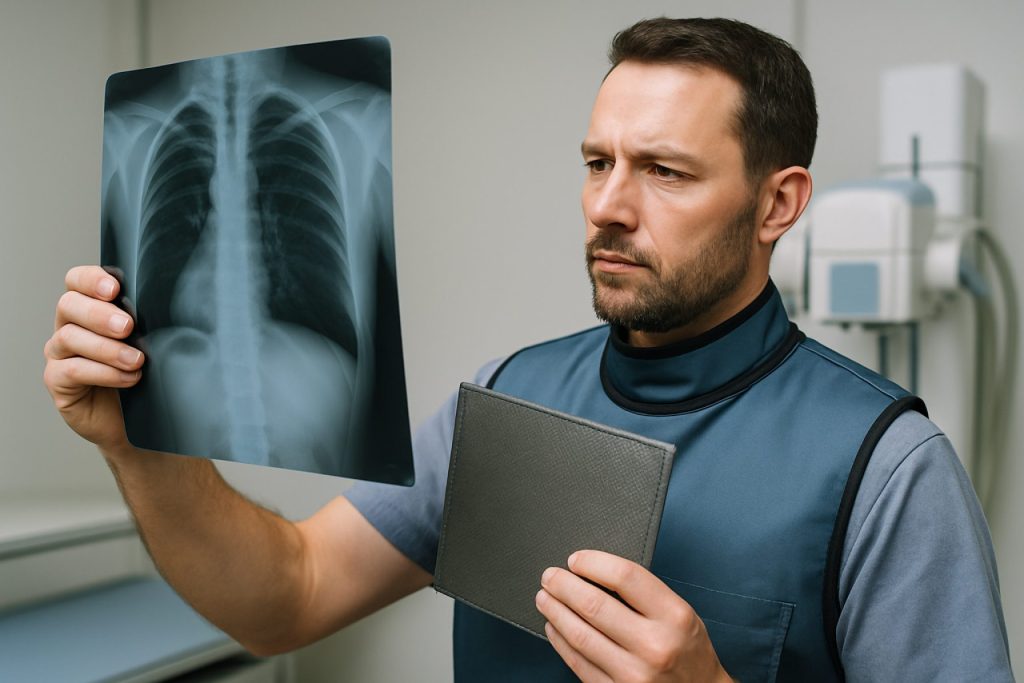
Table of Contents
- Executive Summary: 2025 Industry Overview
- Key Market Drivers and Challenges
- Innovations in Maximum Weight X-ray Shielding Technologies
- Competitive Landscape: Leading Manufacturers and New Entrants
- Global Market Forecasts (2025â2030)
- Regulatory Standards and Compliance Trends
- Emerging Applications in Medical, Industrial, and Defense Sectors
- Sustainability and Environmental Impact of Heavyweight Shielding Materials
- Supply Chain Dynamics and Raw Material Sourcing
- Future Outlook: Disruptive Opportunities and Strategic Recommendations
- Sources & References
Executive Summary: 2025 Industry Overview
The maximum weight X-ray shielding materials segment is poised for significant activity in 2025, driven by evolving regulatory requirements, the expansion of medical imaging infrastructure, and ongoing shifts in material science. Traditionally, high-density lead and lead composites have dominated this sector due to their proven attenuation properties and cost-efficiency. However, increasing environmental and occupational health regulations are prompting stakeholders to investigate and invest in alternative heavy-weight materials such as bismuth, tungsten, and novel polymer-metal composites.
In 2025, high-purity lead remains the industry baseline for maximum weight X-ray shielding, particularly for fixed installations and industrial radiography. Major suppliers like Nuclead and Ecomass Technologies continue to supply lead-based panels, bricks, and specialized shielding components, supporting healthcare, nuclear, and non-destructive testing industries. These companies also report growing interest in lead-alternative solutions, especially for applications where weight is less of a constraint, but toxicity and recyclability are critical concerns.
Tungsten, with its higher density and non-toxic profile, is gaining traction for maximum weight shielding in specialized applications such as oncology vaults, nuclear medicine, and high-energy physics labs. Manufacturers including Plansee and Midwest Tungsten Service are expanding their portfolios of tungsten-based X-ray shielding, leveraging advancements in powder metallurgy and additive manufacturing to produce larger and more intricate components.
Meanwhile, new composite materialsâcombining heavy metals with polymers or ceramicsâare emerging as contenders for maximum weight shielding where custom engineering and sustainability are required. Ecomass Technologies is at the forefront, offering metal-polymer blends that deliver high attenuation with reduced environmental risk, targeting defense and medical sectors.
Looking forward, the sector is expected to see continued investment in R&D, with a focus on optimizing material performance, recyclability, and lifecycle cost. Regulatory shiftsâparticularly in Europe and North Americaâare likely to accelerate the transition toward environmentally preferable heavy shielding options. Global supply chain dynamics for raw materials, such as lead and tungsten, will remain a key variable influencing pricing and product availability throughout 2025 and beyond.
In summary, as of 2025, the maximum weight X-ray shielding materials market is sustaining robust demand for traditional solutions while making a measured pivot toward advanced, sustainable, and application-specific alternatives. Industry leaders are responding with expanded product lines and innovation aimed at meeting the dual imperatives of radiation safety and environmental stewardship.
Key Market Drivers and Challenges
The market for maximum weight X-ray shielding materials is experiencing notable shifts in 2025, driven by evolving industry requirements, regulatory changes, and technological advancements. One of the primary drivers is the rapid expansion of healthcare infrastructure globally, particularly in regions upgrading or expanding their radiology and diagnostic imaging capacities. Hospitals and clinics are seeking materials that offer reliable radiation protection for high-energy and high-volume environments, necessitating maximum weight shielding solutions, often based on dense metals such as lead, tungsten, and specialized alloys.
Another critical driver is the growth in nuclear power generation and nondestructive testing (NDT) sectors, where robust shielding is essential for both operational safety and environmental compliance. Countries investing in new nuclear facilities or refurbishing existing ones are increasingly demanding heavy-duty shielding materials for reactor containment, waste storage, and personnel protection. Companies such as AMETEK, Inc. and Nordion are known for supplying shielding solutions to these sectors, supporting this trend.
Regulatory pressure is also shaping the market. Stricter global guidelines for occupational radiation exposure are prompting end-users to upgrade shielding, particularly in medical, industrial, and research settings. Organizations such as the International Atomic Energy Agency (IAEA) are influencing national standards, pushing for higher performance in shielding systems. This is leading to increased R&D investment by manufacturers to deliver products that balance maximum shielding capacity with compliance and usability.
Despite these positive drivers, there are significant challenges. The primary challenge is the weight and handling complexity of traditional materials like lead. While effective, lead poses environmental and health risks, driving both regulatory restrictions and customer demand for alternative solutions. Tungsten, for example, offers higher density but comes at a higher cost and processing complexity. Suppliers such as Radiation Products Design, Inc. and Apollo Shielding are actively working on optimizing fabrication techniques and exploring composite or layered solutions to manage these trade-offs.
Looking ahead, the outlook for maximum weight X-ray shielding materials remains robust, but manufacturers must balance innovation with practicality. The push for alternatives to lead, advances in composite materials, and smarter design for installation and maintenance will likely shape the competitive landscape through the next few years. Collaboration between suppliers, healthcare providers, and regulatory bodies will be crucial to ensure that new solutions meet evolving safety and operational demands.
Innovations in Maximum Weight X-ray Shielding Technologies
In 2025, the landscape of X-ray shielding materials, particularly those designed for maximum weight and performance, is experiencing significant innovation driven by evolving safety standards and the demand for advanced radiation protection solutions. Traditional lead-based barriers, long regarded as the gold standard for X-ray shielding due to their high density and attenuation properties, continue to be widely used in settings such as medical imaging, nuclear facilities, and industrial radiography. However, recent years have seen a surge in research and development focused on both enhancing lead-based products and introducing effective lead-free alternatives.
Leading manufacturers like Radiation Protection Products and MarShield are at the forefront, offering high-density lead panels, bricks, and custom shielding solutions designed to meet maximum weight and strict regulatory requirements. These products are engineered for applications where space constraints demand the highest possible attenuation within the smallest possible footprint. Innovations include modular, interlocking designs that improve ease of installation and adaptability to complex environments.
Simultaneously, the sector is witnessing a push toward composite and lead-free shielding materials that can match or even surpass the performance of traditional lead in terms of weight-to-shielding ratio. Companies such as MarShield and Radiation Protection Products are investing in proprietary blends of tungsten, bismuth, and high-density polymers. These alternatives offer benefits such as reduced toxicity, easier disposal, and comparable shielding effectiveness, especially in environments where maximum weight can be leveraged for enhanced protection.
Data from industry leaders suggest that the adoption rate of advanced shielding materials is accelerating, particularly in markets like diagnostic radiology and nuclear medicine, where regulatory scrutiny is intense and facility footprints are growing. The next few years are expected to bring further integration of smart materialsâsuch as those incorporating nanotechnology or adaptive structural featuresâaimed at dynamically improving attenuation without increasing weight or thickness. In tandem, digital modeling and simulation tools are being used to optimize barrier design for maximum efficiency and weight effectiveness.
Looking ahead through 2025 and beyond, the sector is poised for continued growth and diversification. As regulatory agencies in North America, Europe, and Asia increasingly emphasize workplace safety and environmental sustainability, demand for both maximum weight and innovative, non-lead X-ray shielding materials is set to rise. This will likely drive further collaboration between manufacturers, end-users, and regulatory bodies to refine and standardize the next generation of high-performance shielding solutions.
Competitive Landscape: Leading Manufacturers and New Entrants
The competitive landscape for maximum weight X-ray shielding materials in 2025 is shaped by a mix of long-standing industry leaders and innovative new entrants. Established manufacturers such as Radiation Products Design, Inc., Mayco Industries, and AMRAY continue to set benchmarks in the production of high-density lead and lead-alternative shielding solutions. These companies maintain extensive distribution networks and invest in consistent product quality, regulatory compliance, and customized services for medical, industrial, and nuclear applications.
In 2025, the demand for higher-density shielding materialsâcharacterized by maximum weight and attenuation capacityâremains robust, particularly in radiology, nuclear medicine, and non-destructive testing sectors. Radiation Products Design, Inc. has focused on expanding its range of lead and composite-based panels and barriers, addressing both traditional requirements and emerging needs for more environmentally friendly alternatives. Similarly, Mayco Industries leverages its vertically integrated manufacturing to offer custom lead bricks and sheets, critical for applications needing maximum mass per unit area.
European manufacturers such as AMRAY and Radiation Protection LĂŒneburg GmbH are prioritizing innovation in non-lead shielding, leveraging heavy metals and polymer composites to meet stringent EU environmental directives. This trend is expected to accelerate through 2025 and beyond as healthcare facilities and industrial users seek to balance performance with sustainability.
New entrants and niche players are gaining traction by introducing advanced materials and manufacturing techniques. Companies specializing in tungsten-based composites and bismuth-based solutions are emerging, offering products with higher density than conventional lead, thus achieving superior attenuation at maximum weights. For instance, Ecomass Technologies develops high-gravity compounds that are lead-free and customizable, appealing to OEMs and end-users with unique or challenging shielding requirements.
Looking forward, the competitive landscape is expected to evolve with increasing investment in R&D, particularly around novel composites, digital manufacturing, and recycling of shielding materials. While established manufacturers like Radiation Products Design, Inc. and Mayco Industries retain significant market share, agile new entrants focusing on high-density, eco-friendly alternatives are likely to capture growing segments of the market through 2025 and into the later decade.
Global Market Forecasts (2025â2030)
The global market for maximum weight X-ray shielding materials is poised for significant developments from 2025 through 2030, driven by advancements in healthcare infrastructure, industrial radiography, and nuclear energy applications. These high-density shielding materialsâprimarily lead and its composites, as well as emerging alternatives such as tungsten and bismuthâare critical for environments requiring maximum attenuation of ionizing radiation.
Current estimates indicate that the demand for maximum weight X-ray shielding materials will grow steadily, particularly in regions investing in hospital expansions, radiological equipment upgrades, and nuclear facility modernization. The healthcare sector remains a primary driver, as advanced imaging procedures and radiation therapy equipment become more widely deployed. Companies like Radiation Products Design, Inc. and Gamma-Service Recycling GmbH continue to supply high-density lead sheets and custom shielding components for these applications.
Industrial radiography and non-destructive testing are also expanding, especially in Asia-Pacific and North America, fueling the need for robust shielding solutions. The adoption of alternative materialsâsuch as tungsten-based and bismuth-based compositesâis expected to accelerate, driven by regulatory scrutiny over lead toxicity and the push for more sustainable manufacturing. Companies like Plansee Group are scaling up production of tungsten alloys, which offer superior density and attenuation properties compared to traditional materials.
From a regulatory perspective, stricter global standards on environmental and occupational safety are anticipated to influence material selection and market dynamics. This could spur innovation in lead-free and recyclable shielding solutions, which several manufacturers are already developing. For instance, Ecomass Technologies is investing in non-toxic, high-density polymer composites as viable alternatives for specific shielding applications.
Looking ahead to 2030, the market outlook suggests a gradual transition: while traditional maximum weight shielding materials like lead will remain dominant due to cost-effectiveness and established supply chains, the share of advanced alternatives is expected to increase. The evolution of medical and industrial imaging technologies, coupled with tightening regulations, will likely shape purchasing decisions and R&D investments. Overall, the sector anticipates moderate to robust growth, with innovation centered on both performance and sustainability.
Regulatory Standards and Compliance Trends
As the demand for maximum weight X-ray shielding materials grows across medical, industrial, and nuclear applications, regulatory standards and compliance frameworks are evolving rapidly in 2025. The landscape is shaped by stricter international and national guidelines targeting safety, environmental impact, and performance, with a pronounced focus on both lead-based and alternative heavy-weight shielding materials.
In the medical sector, the International Electrotechnical Commission (IEC) and the U.S. Food and Drug Administration (FDA) have updated guidelines requiring that X-ray shielding productsâincluding doors, curtains, barriers, and panelsâmeet enhanced attenuation efficiency and labeling requirements. The IEC 61331 standard, which defines requirements for protective devices against diagnostic X-radiation, has seen renewed emphasis on verification of attenuation values and clear documentation of lead equivalency across various thicknesses and material compositions. This is particularly significant for suppliers such as Radiation Protection Products and NELCO Worldwide, who are actively aligning their manufacturing and testing protocols to these updated benchmarks.
Environmental regulations are also influencing compliance trends, especially regarding the use and disposal of lead. The European Unionâs Restriction of Hazardous Substances (RoHS) directive and ongoing adaptation of the REACH regulation are pushing manufacturers toward validated non-lead alternatives, as well as rigorous lifecycle documentation for leaded products. This shift is exemplified by companies like Bar-Ray Products, which has expanded its portfolio of lead-free and composite shielding solutions to ensure both regulatory compliance and market access.
In industrial and nuclear contexts, standards set by bodies such as the American National Standards Institute (ANSI) and the International Atomic Energy Agency (IAEA) are being updated to address maximum weight shielding in transportation casks, storage containers, and facility barriers. Emphasis is placed on traceability of materials, certification of attenuation properties at higher energies, and compliance with safe handling protocols for heavy and dense materials. Suppliers such as MarShield are increasingly required to provide comprehensive compliance documentation, including independent laboratory testing results and detailed chain-of-custody records.
Looking ahead, the outlook for regulatory standards in maximum weight X-ray shielding points to continued tightening of safety, sustainability, and transparency requirements. As the industry innovates with new high-density materialsâsuch as tungsten, bismuth, and proprietary compositesâregulatory agencies are expected to further refine testing methods and classification schemes, paving the way for safer, more sustainable shielding solutions worldwide.
Emerging Applications in Medical, Industrial, and Defense Sectors
In 2025, the deployment of maximum weight X-ray shielding materialsâthose incorporating heavy metals and high-density compositesâcontinues to expand across medical, industrial, and defense sectors, driven by the need for enhanced radiation protection against high-energy sources. The medical field remains the largest consumer, with the proliferation of advanced imaging modalities such as CT, PET, and interventional radiology requiring robust shielding materials to safeguard staff and sensitive equipment. Major manufacturers like Radiation Products Design and Gaven Industries supply lead-based and lead-alternative panels tailored for hospital construction and retrofits, responding to updated regulatory requirements and the trend toward larger, multi-modality imaging suites.
In industrial settings, sectors such as non-destructive testing, oil and gas, and nuclear power are intensifying their reliance on maximum weight shielding. Here, heavy metal-based materialsâincluding lead, tungsten, and proprietary alloysâare essential for enclosing high-output X-ray sources and protecting workers during pipeline inspections, cargo screening, and nuclear maintenance. Companies including Nuvia and Envirotect are actively supplying modular shielding walls and mobile barriers, designed for flexibility and rapid deployment in diverse industrial environments.
Defense applications are seeing particularly robust innovation, with militaries worldwide integrating advanced X-ray shielding into mobile command centers, field hospitals, and armored vehicles. As portable and high-energy X-ray systems become more prevalent in security screening and battlefield diagnostics, the demand for maximum weight shielding materialsâoften incorporating tungsten or depleted uranium for extreme performanceâis growing. Defense contractors and suppliers such as AMETEK and Ultraray Group are developing custom shielding solutions to meet the stringent requirements of military clients, including weight-to-protection optimization and resistance to harsh operational environments.
Looking ahead, the outlook for maximum weight X-ray shielding materials is shaped by ongoing advancements in material engineering and regulatory shifts. Efforts to reduce lead usage due to toxicity concerns are spurring the rapid adoption of tungsten composites and other non-toxic heavy metal alternatives, without compromising shielding effectiveness. Moreover, the integration of digital planning tools and modular construction methods facilitates more precise and efficient implementation of heavy shielding in both permanent and temporary installations. Overall, the next few years are poised to see further diversification of both material types and applications, with established and emerging suppliers alike responding to global demand for safer, more adaptable radiation protection solutions.
Sustainability and Environmental Impact of Heavyweight Shielding Materials
The sustainability and environmental impact of maximum weight X-ray shielding materials, particularly those incorporating lead and other heavy metals, is a critical area of focus in 2025 and will remain so in the coming years. Traditional heavyweight shielding materials, such as lead sheets and lead-based composites, have long been valued for their effective attenuation of X-ray and gamma radiation. However, environmental and health concerns regarding the mining, processing, use, and disposal of lead have prompted manufacturers, healthcare providers, and regulators to seek safer and greener alternatives.
Regulatory pressures are intensifying, with agencies in North America, Europe, and Asia tightening restrictions on lead content in medical and industrial shielding products. This is driving both established manufacturers and new entrants to prioritize the development of lead-free or reduced-lead solutions. For example, Ecomass Technologies and Radiation Products Design, Inc. are offering tungsten, bismuth, and polymer-based composites as non-toxic alternatives to conventional lead shielding. These materials are engineered to maintain or exceed the attenuation performance of lead while minimizing environmental hazards throughout the product lifecycle.
In 2025, heavyweight shielding products utilizing recycled metals and polymers are gaining traction, aligning with global sustainability mandates and circular economy principles. Companies such as Radiation Products Design, Inc. report increased demand for shielding solutions that incorporate recycled content, thus reducing the extraction of virgin resources and the associated environmental footprint. Additionally, end-of-life management programs are becoming more common, with manufacturers facilitating the collection and recycling of used shielding materials to prevent them from entering landfills or causing contamination.
- Research and pilot projects in the next few years are expected to expand the use of high-density, lead-free materials such as tungsten-polymer and bismuth-based composites, which offer both high shielding effectiveness and improved environmental profiles.
- The adoption of digital imaging and lower-dose radiology equipment, promoted by groups like Varian Medical Systems, is also indirectly reducing the need for maximum weight shielding in certain settings, further contributing to sustainability goals.
Looking ahead, industry outlook indicates that regulatory and customer-driven sustainability requirements will continue shaping material selection and lifecycle management in the heavyweight X-ray shielding sector. Innovations in material science, product recyclability, and responsible sourcing are expected to drive further reductions in the environmental impact of these essential protection products while maintaining their critical shielding characteristics.
Supply Chain Dynamics and Raw Material Sourcing
The supply chain for maximum weight X-ray shielding materials in 2025 is heavily influenced by the sourcing and processing of high-density metals, particularly lead and its alternatives such as tungsten, bismuth, and specialized composites. As global demand for advanced radiation shielding expands in medical imaging, nuclear energy, and industrial radiography, ensuring stable access to these raw materials is a priority for manufacturers.
Lead remains the predominant material for maximum weight X-ray shielding owing to its high atomic number and density, combined with its cost-effectiveness. Key suppliers of refined lead, including Glencore and Nyrstar, play a central role in ensuring a steady flow of raw materials to shield manufacturers. However, environmental regulations and increased scrutiny over lead mining and recycling practices â especially in North America and the European Union â are prompting a gradual pivot toward alternative materials.
Tungsten-based shielding, offered by companies such as H.C. Starck and Plansee, is gaining traction for applications where maximum attenuation is required in smaller form factors or where lead restrictions apply. Tungstenâs supply is closely tied to mining activities in China, which dominates global production and periodically imposes export restrictions or price controls, contributing to supply chain volatility. As a result, manufacturers are seeking diversified sources and strategic partnerships to mitigate risk.
Bismuth, while less dense than lead or tungsten, is valued for its non-toxicity and is increasingly incorporated into composite shielding panels and garments. Its supply chain is highly linked to byproduct recovery from lead and copper refining, with major producers including Nyrstar and Glencore. Fluctuations in base metal markets can thus impact bismuth availability and pricing.
In the near term, the outlook suggests continued efforts to localize raw material processing and recycling. Companies such as Ecosurety are investing in closed-loop recycling initiatives for lead and heavy metals, aiming to stabilize supply and meet stricter regulatory requirements. Additionally, research into hybrid shielding materials and high-density polymers is accelerating, driven by companies seeking to reduce reliance on traditional metals while maintaining performance.
Overall, the next few years will likely see increased investment in supply chain resilience, with emphasis on responsible sourcing, recycling, and diversification to support the evolving needs of the X-ray shielding industry.
Future Outlook: Disruptive Opportunities and Strategic Recommendations
Looking ahead to 2025 and the subsequent few years, the landscape for maximum weight X-ray shielding materials is poised for significant transformation, driven by both technological innovation and evolving regulatory frameworks. Historically, lead has dominated the sector due to its high density and cost-effectiveness. However, concerns about toxicity and environmental hazards have accelerated the search for alternative solutions, especially in high-weight, high-performance applications such as industrial radiography, nuclear facilities, and large-scale medical imaging rooms.
A key disruptive opportunity lies in the development and commercialization of non-lead heavy metal composites and engineered polymers. Companies like Ecomass Technologies are already supplying high-density thermoplastic composites as lead replacements, combining equivalent attenuation properties with superior processability and safety. Such materials are well-suited for applications where maximum weight and shielding effectiveness are critical, but regulatory pressures or operational protocols restrict the use of lead.
Furthermore, suppliers such as Radiation Products Design, Inc. and Bar-Ray Products are expanding their portfolios of high-weight, non-lead X-ray shielding materials, including tungsten, bismuth, and iron-based products. These alternatives offer not only robust attenuation but also improved environmental profiles and compliance with increasingly stringent global regulations concerning hazardous substances.
Strategically, end-users and procurement decision-makers are advised to closely monitor advancements in material science, particularly the emergence of nanostructured composites and additive manufacturing techniques that enable the customization of maximum-weight shielding components. For example, the adoption of 3D printing processes for dense polymer-metal blends could streamline production of complex shielding geometries, reduce waste, and enhance performanceâa trend that established players like Ecomass Technologies are actively exploring.
Moreover, collaboration between manufacturers, healthcare providers, and regulatory agencies will be crucial to harmonize standards, facilitate certification of new materials, and accelerate market adoption. Strategic partnerships across the supply chainâsuch as joint R&D or technology licensingâcan further reduce costs and expand the accessible market for high-weight, high-performance shielding solutions.
In summary, the period from 2025 onward is expected to be marked by a paradigm shift away from traditional lead-based maximum weight shielding, toward advanced, environmentally responsible composites and alloys. Stakeholders who proactively invest in R&D, regulatory compliance, and cross-sector collaboration will be best positioned to capitalize on the disruptive opportunities emerging in this evolving field.