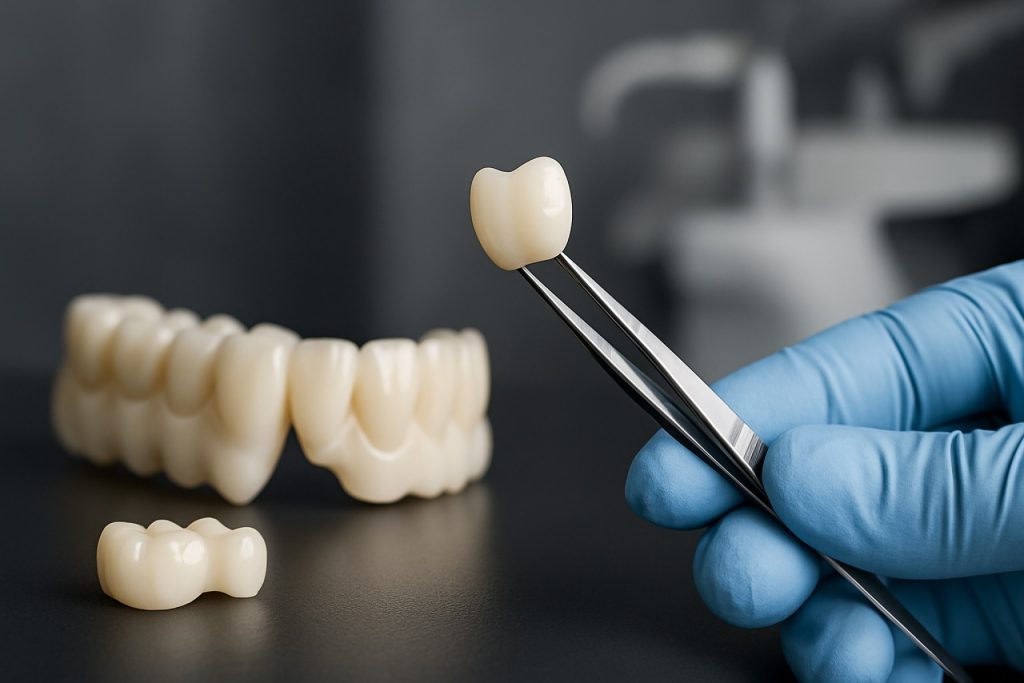
Table of Contents
- Executive Summary: 2025 Outlook and Key Takeaways
- Market Size, Growth Projections & Regional Analysis (2025–2030)
- Breakthroughs in Zirconia Material Science and Manufacturing
- CAD/CAM and Digital Workflow Integration: The New Standard
- Leading Manufacturers & Innovators: Company Profiles and Official Developments
- Cost Structures, Pricing Trends, and Reimbursement Dynamics
- Regulatory Landscape and Quality Standards (FDA, ISO, ADA)
- Sustainability and Environmental Impact in Zirconia Fabrication
- Adoption Drivers: Clinical Outcomes, Patient Preferences, and Dentist Perspectives
- Future Opportunities and Strategic Recommendations for Stakeholders
- Sources & References
Executive Summary: 2025 Outlook and Key Takeaways
The zirconia dental prosthetics sector is poised for continued growth and technological advancement in 2025, building on its established reputation for delivering high-strength, biocompatible solutions for crowns, bridges, and implant abutments. The adoption of digital workflows—particularly CAD/CAM systems—continues to increase, streamlining the design and production process and enabling greater customization and accuracy in prosthetic fabrication. Leading manufacturers, such as Ivoclar, Zirkonzahn, and Dentsply Sirona, are at the forefront of integrating advanced digital milling and sintering technologies, as well as offering new grades of translucent and multilayered zirconia that improve both esthetics and strength.
In the current landscape, dental laboratories and clinics worldwide are increasingly investing in in-house milling systems, responding to clinician demand for faster turnaround times and greater control over prosthetic quality. According to industry data from VITA Zahnfabrik and Amann Girrbach, the trend toward chairside and near-chairside fabrication is accelerating, supported by improved user-friendly software and compact milling units.
Material innovation remains a key driver. Recent introductions, such as high-translucency zirconia and multilayered discs, address the esthetic limitations of earlier generations, allowing for restorations in the visible anterior region without compromising mechanical performance. Companies like Kuraray Noritake Dental and 3M have launched new zirconia products tailored to these demands, emphasizing shade consistency and long-term durability.
Sustainability and regulatory compliance are also gaining prominence. Manufacturers are focusing on optimizing production processes to minimize material waste, improve workflow efficiency, and adhere to evolving international standards. Initiatives by organizations such as Straumann demonstrate the industry’s commitment to responsible sourcing and manufacturing practices.
Looking ahead to the next few years, the outlook for zirconia dental prosthetics fabrication is robust. Continued R&D investment is expected to yield materials with even better optical properties and simplified processing protocols. The integration of artificial intelligence in design, as explored by leading industry players, will further enhance precision and productivity. Overall, zirconia is set to solidify its position as the material of choice in restorative dentistry, with technological, esthetic, and workflow advancements benefiting both clinicians and patients worldwide.
Market Size, Growth Projections & Regional Analysis (2025–2030)
The global market for zirconia dental prosthetics fabrication is poised for robust growth between 2025 and 2030, driven by sustained demand for aesthetic, durable, and biocompatible dental solutions. As of 2025, industry leaders and manufacturers report increased adoption of zirconia-based crowns, bridges, and implant abutments, particularly as digital workflows and CAD/CAM technologies become mainstream in dental laboratories and clinics worldwide.
In terms of market size, leading suppliers such as Ivoclar, Dentsply Sirona, and Kuraray Noritake Dental have noted a consistent uptick in zirconia product shipments year-over-year. This is attributed to the material’s superior strength-to-translucency ratio and versatility across fixed and removable prosthetic applications. According to these manufacturers, North America and Europe remain the largest markets, propelled by high procedural volumes and advanced dental infrastructure. However, the Asia-Pacific region is emerging as the fastest-growing segment, with rising dental tourism in countries like India, Thailand, and South Korea, as well as increasing investments in dental healthcare modernization.
Growth projections through 2030 are optimistic. Industry bodies such as the American Dental Association and FDI World Dental Federation anticipate expansion rates exceeding the broader dental materials sector, supported by the shift from traditional porcelain-fused-to-metal (PFM) restorations to monolithic zirconia alternatives. The development of multi-layered and high-translucency zirconia discs—offered by companies like Amann Girrbach and 3Shape—is further accelerating adoption.
Regionally, Western Europe is expected to maintain strong growth, especially in Germany, France, and the UK, where insurance coverage and public awareness of advanced dental solutions are high. In North America, increased investment in digital dentistry and the expansion of group dental practices support continued market leadership. Meanwhile, in Asia-Pacific, growing middle-class populations and government oral health initiatives are making zirconia prosthetics more accessible.
Looking forward, the outlook for zirconia dental prosthetics fabrication remains highly positive. As manufacturers innovate with faster sintering techniques and improved aesthetics, and as digital integration reduces production times and costs, the global market is set to expand steadily, with regional dynamics shaping adoption patterns and growth rates through 2030.
Breakthroughs in Zirconia Material Science and Manufacturing
Zirconia dental prosthetics fabrication is undergoing rapid transformation in 2025, driven by significant breakthroughs in both material science and manufacturing processes. The continued evolution of zirconia—from early generations with high strength but limited translucency, to modern multi-layered and ultra-translucent forms—has expanded its clinical indications and aesthetic potential. These advances are enabling dental professionals to meet growing patient demands for biocompatible, durable, and natural-looking restorations.
A key development has been the refinement of multi-layered, gradient-shaded zirconia blanks. Manufacturers such as Ivoclar and Zirkonzahn have introduced innovative multilayered discs that mimic the natural gradation of enamel to dentin, improving both esthetics and workflow efficiency. These materials are engineered by varying the concentration of yttria and coloring oxides across the disc, achieving a seamless transition in translucency and strength. In 2025, the latest generations combine 5-6 mol% yttria content, balancing flexural strength (up to 850 MPa) and translucency suitable for anterior restorations, while earlier generations with higher strength (over 1000 MPa) remain favored for posterior applications.
Manufacturing breakthroughs are equally pivotal. The maturation of CAD/CAM milling technologies, including high-speed 5-axis mills from companies like Amann Girrbach, are streamlining prosthetic fabrication with greater precision and reduced production time. Sophisticated nesting software optimizes disc utilization, minimizing material waste. Additionally, the adoption of chairside milling units enables same-day zirconia restorations, a service increasingly promoted by manufacturers such as Dentsply Sirona.
Another transformative trend is the integration of digital workflows, encompassing intraoral scanning, virtual design, and automated sintering. Sintering furnaces with rapid cycles—some under 20 minutes—are shrinking turnaround times while maintaining material integrity. These advancements are complemented by the adoption of artificial intelligence in design automation, further personalizing prosthetic outcomes and enhancing fit.
Outlook for the next few years anticipates incremental improvements in translucency, color matching, and fracture toughness, as well as the introduction of bioactive and antibacterial surface modifications. Leading manufacturers are investing in research to develop zirconia compositions that support improved soft-tissue integration and long-term stability. As regulatory frameworks and digital adoption solidify, zirconia’s dominance in monolithic and layered dental prosthetics is expected to strengthen, making it a cornerstone of restorative dentistry through the remainder of the decade.
CAD/CAM and Digital Workflow Integration: The New Standard
The integration of CAD/CAM (computer-aided design and computer-aided manufacturing) technology and comprehensive digital workflows has become the new standard in zirconia dental prosthetics fabrication as of 2025, driving a paradigm shift across dental laboratories and clinics worldwide. CAD/CAM systems, combined with advanced digital scanning and design software, facilitate highly precise, reproducible, and efficient workflows—attributes that meet the escalating demand for zirconia-based restorations.
In recent years, adoption rates of CAD/CAM systems for zirconia prosthetics have reached unprecedented levels. Major dental technology manufacturers such as Dentsply Sirona and Ivoclar have reported rapid expansion of their digital product portfolios, focusing explicitly on zirconia-compatible solutions. For example, Dentsply Sirona’s CEREC system and Ivoclar’s PrograMill milling units are now optimized for high-strength translucent zirconia blocks, enabling efficient chairside or laboratory fabrication of crowns, bridges, and implant-supported restorations.
A 2024 market update from Amann Girrbach highlighted that more than 80% of newly established European dental labs are equipped with digital zirconia production workflows. This reflects a broader global trend as digital solutions continue to displace traditional manual methods, which are labor-intensive and prone to inconsistencies. Industry leaders such as Zirkonzahn and 3Shape also emphasize seamless software-to-mill integrations, reducing the risk of errors and improving turnaround times.
The workflow typically begins with intraoral scanning or laboratory digitization of impressions, followed by computer-based design of zirconia frameworks. Milling is then performed using high-precision CAM units, often under automated, quality-controlled environments. Post-milling, sintering furnaces—optimized for rapid cycles—are utilized to achieve the required physical properties of zirconia. Companies like VITA Zahnfabrik continue to develop innovative zirconia materials and color systems specifically tailored for digital workflows.
Looking ahead, the next few years are expected to bring further automation, AI-driven design optimization, and cloud-based collaborative platforms for multi-site dental teams. Industry stakeholders anticipate ongoing investments in faster, more accurate scanning and milling equipment, as well as the development of next-generation zirconia materials with superior translucency and strength. The widespread integration of CAD/CAM and digital workflows is set to further elevate the standard of zirconia prosthetics, offering patients highly aesthetic, durable, and individualized restorations with reduced turnaround times.
Leading Manufacturers & Innovators: Company Profiles and Official Developments
The landscape of zirconia dental prosthetics fabrication in 2025 is defined by rapid technological advancements and the emergence of new industry leaders, as well as the ongoing innovation efforts of established manufacturers. Zirconia, known for its superior mechanical properties and biocompatibility, continues to be the material of choice for crowns, bridges, and implant-supported restorations. The global demand for zirconia-based prosthetics is accelerating, driven by dental practices’ shift toward digital workflows and patient preferences for highly aesthetic, metal-free solutions.
Among the foremost innovators in this sector, Ivoclar has maintained its position through the continuous release of advanced zirconia materials and streamlined CAD/CAM fabrication systems. Their IPS e.max ZirCAD portfolio, frequently updated, remains a benchmark for translucency and strength in monolithic prosthetics. As of 2025, Ivoclar continues to expand its digital ecosystem to integrate intraoral scanning, design, and milling, thereby reducing turnaround times for dental labs and clinics.
Dentsply Sirona stands out for its comprehensive chairside solutions, including the CEREC system and high-performance zirconia blocks. The company’s 2024-2025 initiatives focus on improving the speed and accuracy of same-day restorations, with a strong emphasis on sustainability and waste reduction in their manufacturing processes. Their latest multilayered zirconia blocks offer enhanced color gradients, closely mimicking natural teeth and improving patient satisfaction.
3M also remains a significant player, leveraging its extensive R&D capabilities to launch next-generation zirconia materials with improved fracture toughness and translucency. In 2025, 3M is collaborating with dental laboratories to optimize digital workflow integration, supporting both centralized and in-office production models. Their partnerships in software development aim to further streamline the design-to-production pipeline.
Additionally, VITA Zahnfabrik continues to innovate in the field of highly aesthetic zirconia ceramics, with its VITA YZ product line being a staple in digital prosthetics. The company’s recent investments in automation and quality control technologies underscore its commitment to consistency and reproducibility in large-scale prosthetic fabrication.
Emerging manufacturers from Asia are also reshaping the competitive landscape. Companies such as Shofu are scaling up global distribution and introducing cost-effective digital zirconia solutions, responding to increasing demand in both developing and mature markets.
Looking ahead, the sector is poised for further integration of artificial intelligence in design software, and greater adoption of additive manufacturing techniques for zirconia prosthetics. As regulatory standards evolve and patient expectations rise, these leading manufacturers are expected to drive innovation cycles, shaping the trajectory of zirconia dental prosthetics fabrication through 2025 and beyond.
Cost Structures, Pricing Trends, and Reimbursement Dynamics
The cost structures, pricing trends, and reimbursement dynamics within zirconia dental prosthetics fabrication are undergoing significant shifts as of 2025, shaped by advances in materials, manufacturing automation, and evolving payer policies. Zirconia, prized for its biocompatibility and aesthetics, has become a staple in crowns, bridges, and implant-supported restorations, but the economics of its fabrication are complex and highly responsive to technological and market developments.
Production costs for zirconia prosthetics are largely determined by raw material pricing, capital investment in digital manufacturing (notably CAD/CAM milling equipment and 3D printers), labor, and post-processing steps. Major suppliers of dental-grade zirconia, such as Ivoclar and VITA Zahnfabrik, have reported stable pricing for zirconia blanks as large-scale manufacturing and global supply chains increase efficiency. However, the adoption of high-translucency multilayer zirconia and advancements in shading and strength have led to the introduction of premium product lines, which can command higher prices for labs and clinicians.
On the fabrication side, dental laboratories are increasingly investing in digital workflows. Companies like Dentsply Sirona and Zirkonzahn continue to develop integrated CAD/CAM systems, reducing manual labor and turnaround times. This has resulted in cost reductions per unit for standard posterior crowns, as more steps become automated and fewer skilled technicians are needed for routine cases. Nonetheless, the upfront capital costs for digital equipment remain a barrier for smaller labs, potentially driving further market consolidation in the coming years.
Pricing trends in 2025 reflect a dual market: commoditized posterior crowns and bridges, with competitive pricing due to digital production, and premium anterior restorations, where aesthetics and customization allow for higher margins. According to Dentsply Sirona and Ivoclar, the average lab-to-clinic price for a monolithic zirconia crown in mature markets ranges from $100–$200, though complex, multi-unit, or highly aesthetic cases may exceed $400 per unit.
Reimbursement dynamics are also evolving. In North America and parts of Europe, dental insurers are gradually expanding coverage for zirconia-based prosthetics, recognizing their durability and patient preference. However, reimbursement rates often lag behind actual laboratory costs, particularly for advanced or cosmetic indications. Direct-to-consumer aligner and prosthetic providers, such as Straumann, are also influencing market pricing by offering bundled services and leveraging centralized production, which may pressure traditional reimbursement models.
Looking ahead, further automation, larger-scale production, and incremental material innovations are expected to continue reducing per-unit costs, while reimbursement policies may adapt to reflect the clinical value and longevity of zirconia prosthetics. Market leaders are positioning for continued growth, with an eye on both affordability and high-end customization in a rapidly digitalizing dental landscape.
Regulatory Landscape and Quality Standards (FDA, ISO, ADA)
The regulatory landscape for zirconia dental prosthetics fabrication is undergoing significant evolution in 2025, reflecting both the rapid technological progress in material science and the increasing emphasis on patient safety and product consistency. The United States Food and Drug Administration (FDA) continues to classify dental zirconia as a medical device, requiring manufacturers to comply with rigorous premarket notification (510(k)) or premarket approval processes. These regulatory pathways mandate comprehensive demonstrations of biocompatibility, mechanical performance, and long-term safety, as well as conformance to well-established quality system regulations under 21 CFR Part 820, which governs current Good Manufacturing Practices (cGMP) for medical devices. Major suppliers and manufacturers such as Ivoclar and VITA Zahnfabrik prominently highlight their adherence to FDA requirements in their product documentation and marketing materials.
Globally, the International Organization for Standardization (ISO) provides the universally recognized framework for zirconia dental prosthetic materials through standards such as ISO 6872:2019, which covers requirements and test methods for dental ceramic materials. In 2025, adherence to ISO 13485:2016, which specifies requirements for a quality management system specific to the medical devices industry, remains a cornerstone for both manufacturers and dental laboratories. This is complemented by ongoing updates to harmonize material testing, traceability, and sterilization best practices. Companies including Dentsply Sirona and Amann Girrbach publicly commit to alignment with ISO standards, recognizing the importance of international acceptance and cross-border regulatory recognition for their zirconia products.
The American Dental Association (ADA) continues to play a pivotal role in 2025 by establishing performance, safety, and labeling standards tailored to the U.S. dental community. ADA’s Seal of Acceptance and material-specific guidelines are frequently referenced by clinicians and laboratories when selecting zirconia materials and workflows. The ADA also collaborates with the FDA and ISO committees to ensure that evolving standards reflect both the latest clinical evidence and practical realities in dental prosthetics.
Looking ahead to the next few years, the regulatory environment is expected to further emphasize digital traceability, real-time quality monitoring (especially in CAD/CAM workflows), and expanded requirements for supplier transparency in the zirconia supply chain. As digital dentistry and additive manufacturing become increasingly prevalent, regulators and industry bodies are expected to introduce new guidance and potentially updated standards to ensure continued patient safety and product efficacy. This ongoing evolution will require close collaboration between manufacturers, dental professionals, and regulatory agencies to maintain trust and innovation within the zirconia dental prosthetics market.
Sustainability and Environmental Impact in Zirconia Fabrication
Sustainability and minimizing environmental impact are increasingly vital concerns in the dental materials industry, including the fabrication of zirconia dental prosthetics. As of 2025, the sector is responding to regulatory pressures, growing awareness among dental professionals, and patient expectations for environmentally responsible care.
Zirconia fabrication traditionally involves energy-intensive processes such as high-temperature sintering and extensive material machining. Leading manufacturers are now adopting more sustainable practices to reduce their ecological footprint. For instance, Ivoclar and VITA Zahnfabrik have highlighted the optimization of their production lines to lower energy consumption and minimize waste. Advances in pre-sintered zirconia blanks allow for more efficient milling, reducing the volume of discarded material and overall energy requirements.
Another significant trend is the implementation of closed-loop water systems for cooling and dust suppression during CAD/CAM milling, which limits water usage and prevents contamination of local water supplies. Companies such as Dentsply Sirona are also investing in recycling initiatives, where offcuts and milled residues are collected for potential reprocessing or safe disposal, in line with tightening European and international waste regulations.
On the materials side, the drive to develop zirconia with lower firing temperatures continues. This not only conserves energy but also reduces the carbon footprint associated with prosthetic fabrication. Research and development efforts focus on optimizing powder formulations and sintering protocols. According to statements from Zirkonzahn, new product lines aim to achieve full density and strength at lower temperatures, which is anticipated to become an industry standard within the next few years.
Furthermore, supply chain sustainability is under scrutiny. There is a push toward sourcing zirconia powders from certified suppliers with transparent mining and refinement practices, a move supported by organizations like 3M that emphasize responsible sourcing of raw materials.
Looking ahead, the dental prosthetics sector is expected to see broader adoption of life cycle assessment (LCA) tools to quantify and communicate the environmental impact of zirconia prosthetics. This data-driven approach will guide both manufacturers and dental laboratories in making greener choices and meeting evolving regulatory and market demands.
Adoption Drivers: Clinical Outcomes, Patient Preferences, and Dentist Perspectives
The adoption of zirconia dental prosthetics continues to accelerate into 2025, driven by a combination of superior clinical outcomes, evolving patient preferences, and the growing confidence of dental professionals. Zirconia’s unique properties—primarily its high strength, biocompatibility, and aesthetic versatility—have led to its widespread use in crowns, bridges, and implant-supported restorations, replacing traditional materials such as metal-ceramics and lithium disilicate in many cases.
From a clinical perspective, zirconia prosthetics offer significantly enhanced fracture resistance and longevity compared to earlier ceramic materials. Recent data from leading manufacturers show survival rates for monolithic zirconia crowns exceeding 95% at five years, which rivals or surpasses alternatives. The material’s low plaque affinity and favorable tissue response further contribute to reduced complications, particularly in implant-supported applications (Zirkonzahn). These clinical outcomes are compelling for both dentists and patients seeking durable, long-lasting solutions.
Patient preferences have also shifted notably in favor of zirconia. The demand for highly aesthetic, metal-free restorations is growing, as patients increasingly seek dental prosthetics that mimic the translucency and color of natural teeth. Modern multi-layered and high-translucency zirconia blocks enable the fabrication of restorations that meet these aesthetic expectations without compromising strength (Ivoclar). Additionally, concerns over potential allergies or sensitivities to metal alloys have pushed more patients and practitioners toward zirconia-based options.
Dentists’ attitudes are evolving in tandem with these trends. The proliferation of advanced digital workflows—combining intraoral scanning, CAD/CAM design, and high-precision milling—has made zirconia prosthetics easier and faster to fabricate. Dental professionals report increased satisfaction with the fit and predictability of zirconia restorations, as well as reduced chairside adjustment times (Dentsply Sirona). Educational initiatives and clinical studies by manufacturers and professional bodies have further bolstered dentists’ confidence in adopting zirconia solutions.
Looking ahead to the next few years, these adoption drivers are expected to strengthen as zirconia material science advances, offering even greater translucency and strength, and as digital dentistry becomes increasingly mainstream. The synergy of patient-driven demand for aesthetics and safety, robust clinical evidence, and supportive digital infrastructure will continue to propel zirconia dental prosthetics as a preferred choice for restorative and implant dentistry globally.
Future Opportunities and Strategic Recommendations for Stakeholders
The zirconia dental prosthetics sector is poised for significant growth and transformation in 2025 and the coming years, driven by technological advancements, evolving patient expectations, and shifts in global dental care delivery. Stakeholders—including manufacturers, dental laboratories, clinicians, and material suppliers—must recognize and strategically address emerging opportunities to remain competitive and responsive to market needs.
One of the most promising opportunities lies in the continued adoption and refinement of digital workflows, particularly CAD/CAM (computer-aided design/computer-aided manufacturing) technologies. Leading manufacturers such as Ivoclar and Dentsply Sirona are enhancing their digital ecosystems, offering integrated solutions that streamline zirconia prosthetic design and fabrication for both dental labs and chairside applications. In 2025, further integration with artificial intelligence (AI) for automated design optimization and real-time quality control is expected to boost both efficiency and accuracy, thereby reducing turnaround times and costs.
Material innovation will also play a crucial role. Suppliers such as Kuraray Noritake Dental and VITA Zahnfabrik are investing in new grades of translucent zirconia with improved strength and esthetics, responding to increasing demand for highly natural-looking restorations. The introduction of multilayered zirconia discs and blocks, which provide gradient shading and mechanical properties, enables laboratories to deliver lifelike prostheses with minimal post-processing, further enhancing workflow efficiency.
On the regulatory and sustainability front, organizations like American Dental Association are placing greater emphasis on biocompatibility, traceability, and eco-friendly manufacturing processes. Stakeholders who invest in sustainable sourcing, waste reduction, and recyclable packaging for zirconia products are likely to gain a competitive advantage as environmental considerations become more central to procurement decisions.
Strategically, stakeholders should focus on the following recommendations:
- Expand investment in digital workflow training and support to maximize the return on advanced CAD/CAM systems.
- Collaborate with material suppliers to co-develop tailored zirconia solutions for specialized clinical indications, such as implant-supported prostheses and pediatric applications.
- Monitor and prepare for evolving regulatory standards around safety, labeling, and environmental impact, integrating such requirements into product development from the outset.
- Leverage partnerships with dental service organizations and group practices, which are consolidating purchasing power and influencing material selection trends globally.
The outlook for zirconia dental prosthetics fabrication is robust, with opportunities for growth underpinned by digitalization, material science innovation, and rising demand for high-quality, esthetic restorations. Stakeholders who proactively adapt to these trends are well-positioned to capitalize on the expanding global dental prosthetics market in 2025 and beyond.