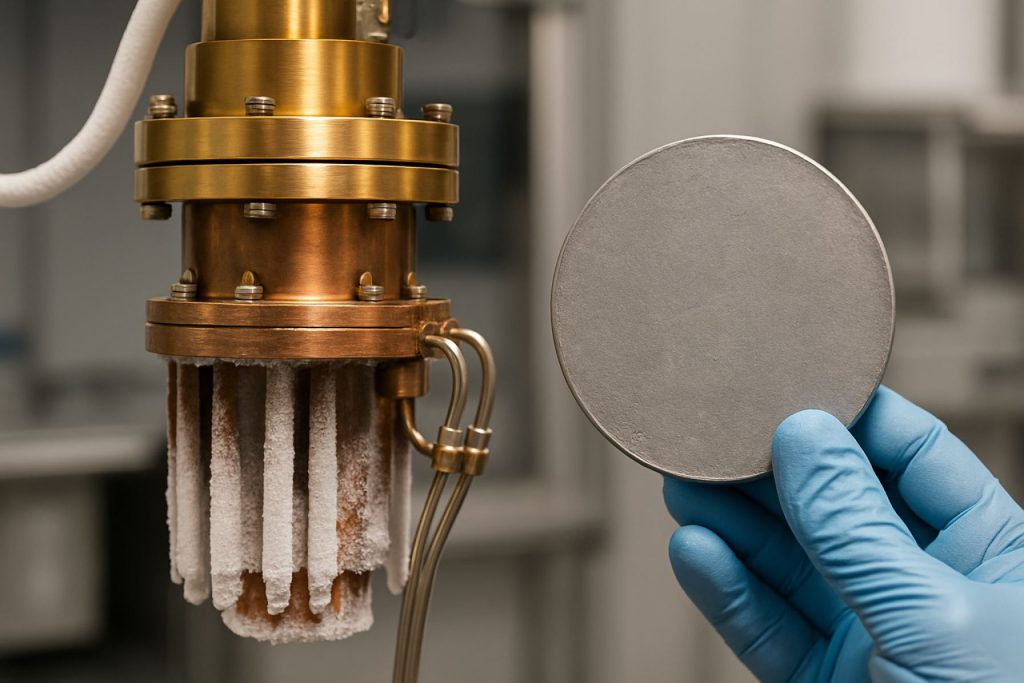
Table of Contents
- Executive Summary: Key Takeaways and 2025 Market Snapshot
- Market Drivers: The Push for Purity and Cryogenic Precision
- Technology Overview: Yttrium Processing at Cryogenic Temperatures
- Innovations in Ultrapure Yttrium Production
- Leading Players and Supply Chain Analysis
- Emerging Applications in Advanced Semiconductors
- Regulatory Standards and Industry Partnerships
- 2025–2030 Market Forecasts: Volume, Value, and Regional Breakdowns
- Challenges, Barriers, and Risk Factors
- Future Roadmap: Disruptive Trends and Strategic Opportunities
- Sources & References
Executive Summary: Key Takeaways and 2025 Market Snapshot
The global market for cryogenic ultrapure semiconductor yttrium processing is witnessing significant advancements and strategic investments as the semiconductor industry intensifies its demand for ultra-high purity materials. As of 2025, leading materials manufacturers are scaling up production capabilities and refining purification techniques to meet the increasingly stringent requirements of advanced node semiconductor fabrication, quantum computing, and photonics applications.
- Market Drivers: The primary impetus for ultrapure yttrium stems from its critical role in producing yttrium-based dielectric materials, phosphors, and high-k gate dielectrics—key components in next-generation logic and memory chips. The rapid evolution toward sub-3nm technology nodes and the proliferation of compound semiconductors have heightened the need for contamination-free dopants and precursors.
- Technological Shifts: Cryogenic processing, leveraging ultra-low temperatures to remove trace metallic and non-metallic impurities, is now a standard for achieving purity levels exceeding 99.9999% (6N and above). Major suppliers are integrating advanced cryogenic distillation and sublimation systems to reduce contamination risks, supporting yield improvement and device reliability.
- Key Players: Companies such as American Elements, Alkor Technologies, and Ferroglobe are actively involved in scaling the production of semiconductor-grade yttrium, with a focus on cryogenic purification and supply chain security. These firms are expanding partnerships with wafer foundries and device makers to ensure end-to-end traceability and compliance with global quality standards.
- Regional Dynamics: Asia-Pacific remains the dominant consumer and producer region, driven by strong investments from leading chip manufacturers and materials suppliers. Expansion projects are underway in South Korea, Japan, and China to localize supply and reduce geopolitical risk.
- 2025 Snapshot and Outlook: In 2025, the market is characterized by robust demand outpacing supply in certain segments, prompting new entrants and established players to announce capacity additions. The focus on sustainability and closed-loop recycling solutions is expected to intensify, as regulatory bodies increase scrutiny on environmental impact and trace metal emissions.
Looking ahead, the next few years will likely see further integration of digital quality control, enhanced traceability, and the adoption of Industry 4.0 practices in yttrium processing. As end-users push for even higher purity and reliability, supplier collaboration and process innovation will remain central to maintaining a competitive edge in the semiconductor materials landscape.
Market Drivers: The Push for Purity and Cryogenic Precision
The drive for higher purity and cryogenic precision in semiconductor yttrium processing is intensifying as the industry advances deeper into the sub-5nm node era and quantum computing applications. In 2025, market forces are converging to demand ultrapure yttrium sources and rigorously controlled cryogenic processes. This is primarily due to the material’s critical role in fabricating advanced dielectric layers, yttrium-based high-k gate oxides, and as a key dopant in compound semiconductors for optoelectronic and quantum devices.
Major semiconductor manufacturers are setting stricter impurity thresholds, often requiring yttrium purity levels of 6N (99.9999%) or higher. Impurities, even at the parts-per-billion level, can dramatically affect device reliability and yield, particularly as device architectures shrink and quantum effects become more pronounced. This has led to vertically integrated players and specialized material suppliers investing in advanced refining and purification technologies—such as zone refining under cryogenic conditions—to meet these specifications. Companies like Ames Laboratory and Atos (for process control and cryogenics) have publicly highlighted their advancements in delivering ultra-clean yttrium materials for wafer fabrication and quantum device pilot lines.
The adoption of cryogenic processing is also being propelled by the growing prevalence of superconducting and low-temperature quantum devices, which require yttrium-containing materials with exceptionally low defect densities and precise stoichiometry. In 2025, semiconductor foundries and quantum research consortia are scaling up investments in sub-10K cryogenic process modules, including ultra-high vacuum (UHV) deposition and purification setups. These enable not only the removal of volatile contaminants but also the stabilization of sensitive yttrium compounds during synthesis and deposition.
Looking ahead to the next few years, the market is poised for further tightening of purity and process control standards. The expansion of quantum computing pilot lines, particularly in North America and East Asia, is expected to drive up demand for cryogenically processed ultrapure yttrium. Suppliers are responding by increasing capacity for 7N-grade and custom-isotopic yttrium, as well as developing real-time, in-situ monitoring solutions for impurity control during cryogenic processing. Collaborations between material producers, equipment manufacturers, and end-users—such as those led by Linde in advanced gas and cryogenic infrastructure—underscore a robust outlook for technological advancements and supply chain integration in this specialized segment.
Technology Overview: Yttrium Processing at Cryogenic Temperatures
The processing of ultrapure yttrium for semiconductor applications at cryogenic temperatures is a rapidly advancing field, driven by the increasing demand for high-performance materials in next-generation electronics. Yttrium, with its high chemical stability and favorable electronic properties, is employed in applications such as high-k dielectrics, advanced substrates, and as a dopant in compound semiconductors. The stringent purity requirements—often exceeding 99.999% (5N)—necessitate advanced purification and handling techniques, especially as device architectures shrink below the 5 nm node.
In 2025, the industry standard for ultrapure yttrium production involves a multi-stage process: initial extraction from mineral sources, solvent extraction to remove rare earth impurities, and subsequent zone refining or vacuum distillation to achieve semiconductor-grade purity. When targeting cryogenic applications, additional challenges arise, as trace contaminants can have amplified effects on electronic and quantum properties at low temperatures. As a result, several manufacturers have integrated in-line cryogenic purification steps, utilizing liquid helium or nitrogen environments to minimize contamination and prevent oxidation during material handling and deposition.
Current data from leading producers indicates that the adoption of cryogenic containment and transfer systems is expanding, particularly for yttrium intended for superconducting quantum circuits and deep ultraviolet (DUV) photolithography equipment. Companies such as AMEPURE and American Elements are actively supplying semiconductor-grade yttrium, highlighting advances in controlled-atmosphere processing and the development of custom cryogenic vessels for material transport and storage. These systems allow for the maintenance of yttrium’s purity from production through to wafer fabrication.
Outlook for the next few years points to further refinement of in-situ cryogenic deposition techniques, such as molecular beam epitaxy (MBE) and atomic layer deposition (ALD), with real-time monitoring to detect and eliminate sub-ppb impurities. The integration of cryogenic purification modules into existing chemical vapor transport and evaporation chambers is anticipated to become standard practice, supporting the scaling of quantum and high-frequency semiconductor devices. Collaboration between major yttrium suppliers, wafer foundries, and equipment manufacturers—such as ULVAC and Linde—is expected to drive the development of proprietary cryogenic processing lines tailored for ultrapure materials.
Overall, the trajectory of cryogenic ultrapure yttrium processing in 2025 and beyond is marked by the convergence of advanced purification, contamination control, and integrated cryogenic handling, positioning yttrium as a critical enabler for emerging semiconductor and quantum technologies.
Innovations in Ultrapure Yttrium Production
The production of ultrapure yttrium for semiconductor applications has become increasingly advanced, especially as the demand for high-performance electronic materials grows. In 2025, significant innovations are emerging in the cryogenic processing of ultrapure yttrium, driven by the requirements of next-generation semiconductor devices and the miniaturization of chip architectures.
A key trend is the adoption of cryogenic purification techniques, where yttrium is processed at extremely low temperatures to remove trace impurities more effectively than conventional methods. These processes, often integrated with high-vacuum distillation and zone refining, are being scaled up by leading suppliers to meet the stringent purity standards (typically 5N or 6N, i.e., 99.999% or higher) required for advanced semiconductor manufacturing. Companies such as American Elements and Tanaka Kikinzoku Group are actively involved in supplying ultrapure yttrium and developing new production methodologies, including cryogenic and plasma-assisted refining.
Data from industry sources indicate that cryogenic processing reduces contaminant levels—such as rare earth and transition metal residues—by up to an order of magnitude compared to traditional chemical purification. This improvement is critical, as even sub-ppm impurities can degrade the performance of yttrium-based thin films used in dielectric layers, phosphors, and laser materials for semiconductor fabrication. In 2025, several semiconductor material suppliers are investing in pilot-scale cryogenic extraction and purification plants, leveraging automation and real-time impurity monitoring to ensure reproducibility and scalability.
Another notable innovation is the use of advanced analytical and metrology tools for quality assurance. Companies are deploying in-line mass spectrometry and cryogenic electron microscopy to verify purity during and after processing, which ensures compliance with the exacting requirements of customers in the semiconductor sector, especially for logic and memory device applications.
Looking ahead, the outlook for cryogenic ultrapure yttrium processing is positive. The ongoing transition to sub-3nm process nodes and the proliferation of compound semiconductors are expected to further tighten purity specifications, driving continued investment in cryogenic and hybrid purification technologies. Industry leaders like Tanaka Kikinzoku Group and American Elements are expected to expand their production capabilities and collaborate with semiconductor manufacturers to co-develop application-specific ultrapure yttrium products, ensuring supply chain resilience and technological advancement in the coming years.
Leading Players and Supply Chain Analysis
The cryogenic ultrapure semiconductor yttrium processing sector is characterized by a tightly controlled supply chain and the presence of a few major global players with advanced purification capabilities. As semiconductor device geometries shrink and demand for high-performance materials intensifies, the need for ultrapure yttrium—typically with impurity levels in the single-digit parts-per-billion range—has become critical for processes such as manufacturing yttrium-based dielectric and phosphor layers.
Currently, the supply chain for ultrapure yttrium begins with extraction from rare-earth mineral concentrates, followed by multiple steps: solvent extraction, precipitation, and advanced purification involving cryogenic techniques to achieve the stringent purity levels required for semiconductor applications. Most mining and initial refining occur in China, which remains the dominant source of rare earth elements, including yttrium. However, geopolitical pressures and supply security concerns are pushing manufacturers to diversify sourcing and invest in alternative refining hubs, particularly in North America, Japan, and Europe.
Key companies in the cryogenic ultrapure yttrium segment include Solvay, which operates advanced rare earth processing facilities in France and has invested in technologies to supply semiconductor-grade yttrium compounds. The Chemours Company is also involved in high-purity rare earths, leveraging its fluorochemical expertise in purification processes. Japanese firms, notably Tanaka Holdings and Santoku Corporation, have developed proprietary cryogenic distillation and zone refining methods that are considered industry benchmarks.
In the Asia-Pacific region, Chinalco (Aluminum Corporation of China) and Sumitomo Metal Mining lead in vertical integration, managing the entire chain from rare earth mining to high-purity oxide production. These companies have announced ongoing upgrades to their purification lines, with an emphasis on automation and process digitization, aiming for even tighter impurity controls and higher throughput by 2026.
The outlook for 2025 and the following years points to increased investment in cryogenic separation and purification technologies, as chip manufacturers demand even stricter contamination thresholds. Supply chain transparency and traceability—driven by both regulatory requirements and customer expectations—are expected to improve, with real-time monitoring and digital certification becoming standard. Strategic collaborations between material suppliers and semiconductor fabs are anticipated to accelerate, ensuring secure access to ultrapure yttrium as the industry transitions toward advanced nodes and novel device architectures.
Emerging Applications in Advanced Semiconductors
The demand for cryogenic ultrapure yttrium in advanced semiconductor processing is intensifying in 2025, reflecting the shift toward next-generation device architectures and quantum technologies. Yttrium, prized for its high purity and unique physical properties, has become a critical material in fabricating high-k dielectrics, superconducting qubits, and specialized thin films used in cutting-edge logic and memory devices. As device geometries shrink below the 3 nm node and quantum computing research accelerates, the industry is witnessing a concerted push to control trace metal contamination and maximize material uniformity—objectives directly addressed by cryogenic ultrapure yttrium processing.
Key industry players including American Elements and Advanced Materials Inc. are ramping up capacity for producing semiconductor-grade yttrium at purities exceeding 99.9999% (6N). This expansion is spurred by partnerships with major foundries and equipment suppliers focusing on atomic layer deposition (ALD) and molecular beam epitaxy (MBE) tools, both of which require highly controlled materials for uniform thin film growth. For instance, yttrium-based precursors are increasingly selected for fabricating yttrium oxide (Y₂O₃) gate dielectrics, which offer superior thermal stability and leakage characteristics compared to conventional silicon dioxide in advanced CMOS technologies.
In 2025, several semiconductor fabrication facilities are piloting cryogenic delivery systems for yttrium precursors, addressing the need for ultra-stable supply lines that minimize impurity introduction. This is especially relevant for quantum device manufacturing, where even sub-ppb contamination can degrade superconducting qubit coherence times. Air Liquide and Linde have announced investments in cryogenic purification and distribution infrastructure tailored for semiconductor-grade rare earths, including yttrium, to support these emerging requirements.
Looking beyond 2025, industry analysts expect continued growth in cryogenic ultrapure yttrium demand, particularly as the semiconductor roadmap advances toward sub-2 nm nodes and as quantum computing transitions from laboratory to pilot-scale manufacturing. Collaborative initiatives between material suppliers, equipment manufacturers, and integrated device makers are likely to accelerate innovation in purification technologies and closed-loop cryogenic handling systems. With ongoing advances, yttrium’s role is set to expand, underpinning both incremental improvements in classical logic and breakthroughs in quantum and neuromorphic hardware.
Regulatory Standards and Industry Partnerships
The regulatory landscape for cryogenic ultrapure semiconductor yttrium processing in 2025 is intensifying as both governmental and industry-led standards become increasingly stringent in response to the rising demand for high-purity materials in advanced semiconductor manufacturing. Globally, regulatory bodies are updating purity and contamination thresholds to reflect the new requirements of next-generation chip fabrication, particularly for processes operating at the sub-5-nanometer scale. These regulations are designed to ensure yttrium, used as a sputtering target or dopant, meets impurity levels often below parts-per-billion (ppb), minimizing unintended defects in critical semiconductor layers.
Key industry organizations, such as the SEMI, continue to lead the development and harmonization of standards for ultrapure materials. SEMI’s guidelines—frequently adopted by major chipmakers—specify acceptable impurity profiles and testing protocols for materials including yttrium. In 2025, updates to SEMI’s purity standards are expected to incorporate stricter controls on trace metals and rare earth cross-contamination, reflecting the evolving needs of logic and memory device manufacturers.
On the regulatory front, authorities in major semiconductor producing regions—including the United States, South Korea, Japan, and the European Union—are coordinating with industry partners to ensure compliance and transparency throughout the supply chain. The U.S. Environmental Protection Agency (EPA) and equivalents in Asia and Europe are increasing inspections and reporting requirements for chemical suppliers and wafer fabs handling yttrium compounds, with a focus on environmental safety and worker exposure during cryogenic processing.
Simultaneously, industry partnerships are accelerating between material suppliers, equipment manufacturers, and semiconductor foundries. Major yttrium producers such as American Elements and Alfa Aesar are collaborating with equipment suppliers to refine purification methods, integrating advanced cryogenic distillation and filtration technologies that meet or exceed SEMI and customer-specific requirements. Equipment makers like ULVAC are also working with materials providers to ensure that deposition and etch tools can reliably process ultrapure yttrium under cryogenic conditions without introducing new contamination vectors.
Looking ahead, the next few years will likely see further integration of digital traceability systems, enabling real-time monitoring of yttrium purity from source to fab. This digitalization, combined with evolving international standards and closer cross-sector partnerships, is expected to drive both regulatory compliance and innovation in cryogenic ultrapure yttrium processing, reinforcing reliability and yield in semiconductor device manufacturing.
2025–2030 Market Forecasts: Volume, Value, and Regional Breakdowns
The outlook for cryogenic ultrapure semiconductor yttrium processing from 2025 through the end of the decade is marked by both expanding market volume and value, alongside notable shifts in regional demand and production capabilities. As semiconductor device geometries continue to shrink and the proliferation of advanced logic and memory nodes accelerates, the requirements for ultrapure yttrium and yttrium-based precursors in thin film deposition, particularly in atomic layer deposition (ALD) and metal-organic chemical vapor deposition (MOCVD) processes, are intensifying.
Industry leaders are increasing their investments in high-purity yttrium production infrastructure, with a focus on cryogenic refinement methods to meet the sub-ppb impurity specifications demanded by next-generation chipmakers. For instance, American Elements and Ferroglobe have both announced ongoing upgrades to their purification and handling lines to address these ultra-high purity requirements. This is expected to result in a compound annual growth rate (CAGR) for ultrapure yttrium volumes in the range of 8–10% through 2030, with global annual demand projected to approach 250–300 metric tons by 2030, up from an estimated 170 metric tons in 2025.
In terms of value, the market for cryogenic ultrapure semiconductor yttrium is anticipated to surpass $1.2 billion by 2030, compared to an estimated $750 million in 2025. This growth will be driven by higher purity premiums, increased use in emerging semiconductor applications such as power electronics and compound semiconductors, and the rising integration of yttrium-based materials in extreme ultraviolet (EUV) lithography masks and advanced oxide dielectrics. Pricing for sub-ppb grade yttrium is expected to remain robust, with tightness in supply due to both processing complexity and the relatively limited number of qualified suppliers.
Regionally, Asia—led by China, Japan, South Korea, and Taiwan—will continue to dominate both demand and supply, reflecting the regional concentration of advanced semiconductor fabrication. Companies such as Tosoh Corporation and Samsung Electronics are investing in localized sourcing and purification capacity, while North America and Europe are expected to grow their market shares through strategic investments in supply chain security and indigenous advanced material processing capabilities. This regional diversification is partially incentivized by semiconductor policy initiatives and funding in the United States and European Union, aiming to reduce dependence on single-source supply chains.
Overall, the 2025–2030 period will be characterized by a dynamic balance of technological innovation, supply chain realignment, and robust demand growth, underpinning a strong market trajectory for cryogenic ultrapure semiconductor yttrium processing.
Challenges, Barriers, and Risk Factors
Cryogenic ultrapure semiconductor yttrium processing is poised for increased demand through 2025 and beyond, but the sector faces several critical challenges and barriers that may impede its scalability and reliability. The most pressing issue is the stringent requirement for impurity levels below parts-per-billion (ppb), which is essential for advanced semiconductor applications, particularly in logic and memory devices at sub-5nm nodes. Achieving such purity consistently at production scale demands sophisticated purification infrastructure and rigorous process controls, often pushing the limits of current cryogenic separation and chemical refining technologies.
Supply chain vulnerabilities are another key risk factor. Yttrium is predominantly sourced as a byproduct from rare earth mining, with extraction and initial processing concentrated in a handful of countries. Disruptions—whether from geopolitical tensions, export restrictions, or environmental regulations—can quickly ripple through the downstream supply chain, jeopardizing consistent access to feedstock for ultrapure processing. Manufacturers such as Umicore and Kyocera Corporation have highlighted in recent years the importance of diversification and vertical integration to mitigate such risks.
Cryogenic processing itself introduces unique operational hazards. The low-temperature environment required to fractionate and purify yttrium compounds demands specialized equipment, robust containment, and high energy inputs. Maintaining reliability and uptime under these conditions is costly and technically complex. Failures in the cryogenic systems—such as leaks, insulation breakdown, or compressor faults—can lead to batch contamination, lost yield, or even safety incidents. Additionally, handling and storage of ultrapure yttrium must account for its high reactivity and propensity for contamination, further increasing costs and regulatory scrutiny.
Environmental and regulatory compliance is tightening globally. Increasingly strict emissions and waste management requirements impact not only mining and raw material processing, but also the chemical reagents and energy use inherent in cryogenic ultrapure processes. Companies like Toyota Tsusho Corporation have signaled the need for greener production pathways, while investing in closed-loop recycling and advanced filtration systems to minimize environmental footprint.
Looking ahead, the sector’s ability to scale will hinge on advances in process intensification, automation, and real-time monitoring to ensure both purity and operational safety. Collaboration between material producers, equipment suppliers, and semiconductor manufacturers will be essential to standardize specifications and qualify new sources of ultrapure yttrium. Without such coordinated efforts, persistent barriers in cost, supply security, and process robustness could constrain growth in next-generation semiconductor manufacturing.
Future Roadmap: Disruptive Trends and Strategic Opportunities
The future roadmap for cryogenic ultrapure semiconductor yttrium processing is shaped by a convergence of advanced materials demand, evolving device architectures, and sustainability requirements. As the semiconductor industry intensifies its reliance on rare earth elements for next-generation logic and memory devices, yttrium stands out due to its critical role in high-k dielectrics, epitaxial substrates, and advanced metallization processes operating at cryogenic temperatures. From 2025 onward, several disruptive trends and strategic opportunities are poised to redefine this niche yet vital supply chain.
- Transition to Cryogenic Quantum and Superconducting Devices: The push towards quantum computing and superconducting electronics, which operate at ultra-low temperatures, is accelerating the demand for ultrapure yttrium. Yttrium-based compounds, such as yttrium barium copper oxide (YBCO), are central to high-temperature superconducting circuits and quantum memory elements. Leading device manufacturers are forming strategic partnerships with specialty materials providers to secure reliable sources of 7N (99.99999%) and higher purity yttrium, as sub-ppb impurity levels are essential for minimizing decoherence and maximizing device performance.
- Emergence of Closed-Loop Purification and Circularity: Environmental stewardship and secure supply are driving the development of closed-loop yttrium purification systems. Refiners are investing in advanced cryogenic distillation and solvent extraction technologies, aiming to reduce waste and energy consumption while achieving exceptional purity. Companies like American Elements and Alfred Metal are scaling up recycling programs to recapture yttrium from spent semiconductor targets and production scrap, aligning with the sector’s net-zero ambitions.
- Supply Chain Resilience and Geopolitical Diversification: The concentration of yttrium reserves and refining capacity in a few countries has underscored the risk of supply disruptions. In response, manufacturers and foundries are diversifying sourcing strategies, fostering new extraction and processing initiatives in North America, Europe, and Southeast Asia. Cross-industry consortia are emerging to standardize ultrapure yttrium grades and create transparent, auditable supply chains in anticipation of stricter export controls and traceability mandates.
- Integration with Advanced Deposition Techniques: The adoption of atomic layer deposition (ALD) and molecular beam epitaxy (MBE) at cryogenic temperatures is creating new requirements for yttrium precursors with ultra-low particulate and volatile organic content. Equipment suppliers, such as ULVAC and Kurt J. Lesker Company, are collaborating with materials vendors to co-develop deposition-ready yttrium sources tailored to the stringent needs of sub-3 nm semiconductor nodes.
Looking ahead, the sector’s outlook is defined by collaborative innovation and rapid response to both technical and geopolitical pressures. Strategic investments in purification, recycling, and regional diversification are expected to mitigate risks and unlock new opportunities for cryogenic ultrapure yttrium in the expanding realm of quantum and classical semiconductor technologies.