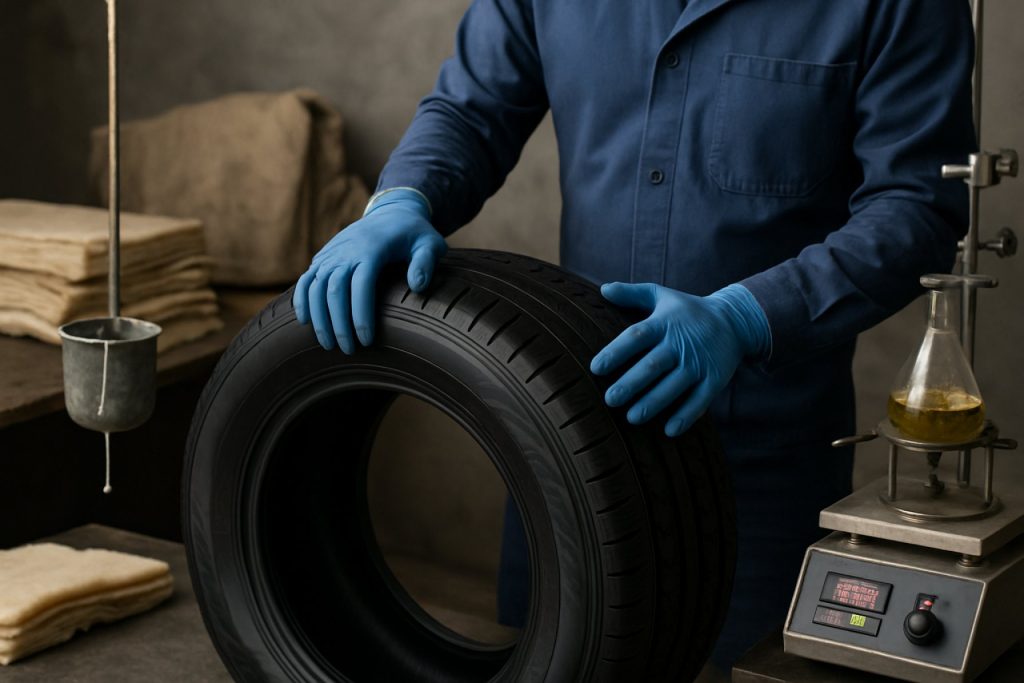
Table of Contents
- Executive Summary: 2025 Market Pulse and Emerging Trends
- Overview of Hevea Vulcanization Kinetics: Science & Industry Impact
- Key Drivers: Innovations Accelerating Vulcanization Kinetics
- Competitive Landscape: Leading Companies and R&D Initiatives
- 2025 Market Forecasts: Growth, Demand, and Global Opportunities
- Technological Breakthroughs: Latest Advances and Patent Highlights
- Sustainability and Regulatory Outlook: Standards, Trends, and Compliance
- Case Studies: Industry Applications and Real-World Performance
- Challenges and Risks: Technical, Economic, and Supply Chain Factors
- Future Outlook: Disruptive Technologies and Strategic Roadmap to 2030
- Sources & References
Executive Summary: 2025 Market Pulse and Emerging Trends
The global demand for natural rubber, primarily sourced from Hevea brasiliensis, continues to drive advancements in vulcanization kinetics analysis in 2025. Vulcanization—the chemical process transforming raw rubber into durable, elastic material—remains central to applications in automotive, industrial, and consumer sectors. The kinetics of vulcanization, particularly for Hevea-derived latex and solid rubber, is under active study as the industry seeks to optimize curing times, improve product performance, and reduce energy consumption.
In 2025, leading producers and research centers are investing in advanced rheological and spectroscopic techniques to better characterize curing behaviors. For example, time-resolved rheometry and in-situ FTIR analysis are increasingly employed to monitor crosslink density evolution, sulfur cure systems, and accelerator efficiency, allowing for more precise process control. These innovations are critical for large-scale processors such as Sri Polyrubbers and Sipm Rubber, who emphasize reduced cycle times and consistent product quality in their manufacturing workflows.
Recent data indicate a shift towards more eco-friendly vulcanization systems, with lower levels of nitrosamines and other hazardous byproducts. Major industry suppliers like Goodyear and Michelin are piloting alternative accelerators and sulfur donors to meet tightening environmental regulations. These changes directly impact the chemical kinetics of vulcanization, prompting further research into activation energies, reaction mechanisms, and optimal compounding strategies.
Another notable trend in 2025 is the integration of digital process monitoring and machine learning to predict and control vulcanization kinetics in real time. Automated systems—now being trialed by companies such as Bridgestone—leverage sensor data and kinetic modeling to dynamically adjust curing parameters, minimizing variability and waste.
Looking ahead to the next few years, continued collaboration between rubber producers, technology developers, and end-users is expected to accelerate innovation. The outlook is for adaptive, data-driven manufacturing environments where Hevea vulcanization kinetics are finely tuned for both performance and sustainability. As regulatory and market pressures mount, the industry’s ability to harness advanced analysis and process control will be a key differentiator, setting the stage for more efficient resource use and greener rubber products worldwide.
Overview of Hevea Vulcanization Kinetics: Science & Industry Impact
The kinetics of vulcanization in Hevea natural rubber remains a critical area of research and industrial innovation heading into 2025 and beyond. Vulcanization—the process of cross-linking rubber molecules through additives such as sulfur—directly determines the mechanical, elastic, and durability properties of natural rubber products. The main kinetic parameters of interest include induction time, cure rate, and optimum cure time, all of which are influenced by the composition of the rubber, accelerator systems, temperature, and processing methods. Globally, the relevance of kinetic analysis is heightened by ongoing shifts in both material science and regulatory landscapes, especially as industries seek to optimize energy use, reduce curing times, and improve product performance.
In recent years, manufacturers have increasingly leveraged real-time rheometric methods and advanced statistical models to monitor and control vulcanization kinetics in natural rubber derived from Hevea brasiliensis. For example, automated moving die rheometers are now standard in quality assurance laboratories, enabling precise measurement of torque as a function of time and temperature during the cure process. This has allowed producers such as Sri Trang Agro-Industry and The Goodyear Tire & Rubber Company to achieve tighter specifications on their rubber compounds by adjusting accelerator-to-sulfur ratios and incorporating secondary accelerators or activators to fine-tune kinetics for specific applications.
Recent data indicates that the ongoing transition toward sustainable and bio-based accelerators is influencing the vulcanization profiles of Hevea rubber. For instance, suppliers are experimenting with zinc-free and nitrosamine-free systems that present altered reaction rates and cross-linking densities, necessitating renewed kinetic characterizations. The industry is responding by deploying in-line process analytics and machine learning to predict optimal cure parameters, especially for tire, automotive, and medical goods. Key players such as Michelin and Bridgestone Corporation have publicly committed to sustainable sourcing and processing, which includes ongoing research into alternative vulcanization chemistries that minimize environmental impact without compromising performance.
Looking ahead to the next few years, the industry is expected to intensify its focus on greener vulcanization kinetics. Advances in accelerator chemistry, digital process control, and real-time kinetic modeling will likely enable further reductions in energy consumption and cycle times, improving both cost efficiency and environmental profiles. As regulatory scrutiny on chemical additives tightens, robust kinetic analysis will remain a cornerstone of innovation in the Hevea rubber sector, supporting the development of next-generation, high-performance, and sustainable rubber products.
Key Drivers: Innovations Accelerating Vulcanization Kinetics
The vulcanization kinetics of Hevea-derived natural rubber continue to be a focal point of innovation as the rubber industry seeks enhanced performance, energy efficiency, and sustainability in 2025 and the coming years. Key drivers accelerating these kinetics include advances in chemical formulation, process engineering, and digitalization.
A primary area of innovation is the development of novel accelerator systems. Current research and deployment by major rubber chemical producers are focused on next-generation accelerators that offer faster cure rates and reduced toxicity. For instance, the move away from traditional sulfur-based accelerators toward safer, non-nitrosamine generating systems is being prioritized by manufacturers to comply with evolving health and environmental regulations. Companies such as LANXESS and Eastman Chemical Company are actively developing and commercializing these new chemical solutions, which not only speed up vulcanization but also improve process control and product consistency.
The integration of digital process control and real-time analytics has become another critical driver. Advanced monitoring systems employing machine learning and artificial intelligence are being adopted in manufacturing plants to precisely analyze vulcanization kinetics, enabling dynamic adjustment of temperature, pressure, and timing. This results in optimized cure cycles, reduced energy consumption, and minimized waste. Leading tire and rubber goods manufacturers such as Michelin and The Goodyear Tire & Rubber Company are investing in these digital technologies to enhance both the speed and reproducibility of vulcanization.
- Green chemistry initiatives: Biobased and low-carbon additives are increasingly used to accelerate vulcanization while improving the environmental footprint of Hevea rubber products. These innovations align with sustainability commitments by major industry players.
- Nanotechnology: Incorporation of nanomaterials, such as nano-silica or nanoclays, is being explored to enhance heat transfer and crosslinking efficiency, thereby accelerating kinetics and providing superior mechanical properties.
- Process intensification: Advances in continuous mixing and high-frequency heating (e.g., microwave or induction techniques) are being piloted to further reduce vulcanization time and energy requirements.
Looking ahead to the next few years, these innovations are anticipated to deliver faster, cleaner, and more controlled vulcanization of Hevea rubber, with industry-wide adoption driven by economic and regulatory imperatives. Ongoing collaboration between chemical suppliers, tire manufacturers, and technology providers will remain crucial in translating laboratory breakthroughs into large-scale, commercial reality.
Competitive Landscape: Leading Companies and R&D Initiatives
The competitive landscape for Hevea vulcanization kinetics analysis in 2025 is shaped by a dynamic interplay of established rubber manufacturers, specialty chemical companies, and innovation-focused technology providers. As the global demand for high-performance natural rubber continues to rise—driven by growth in automotive, industrial, and medical sectors—key players are intensifying their research and development (R&D) efforts to optimize the vulcanization process, improve material properties, and reduce environmental impact.
Among the industry leaders, The Goodyear Tire & Rubber Company and Compagnie Générale des Établissements Michelin are at the forefront, investing heavily in advanced vulcanization studies. These companies are leveraging kinetic modeling and real-time process analytics to fine-tune sulfur curing systems and accelerator compositions, aiming for greater consistency and reduced cycle times. In 2025, both companies are reported to have pilot lines equipped with in-line rheometers and spectroscopic tools, enabling continuous monitoring of vulcanization kinetics to align with quality and sustainability objectives.
On the supplier side, LANXESS AG and Evonik Industries AG are leading the way in the development of specialty additives and accelerators tailored for Hevea-based compounds. Their R&D initiatives focus on environmentally friendly alternatives to conventional accelerators, aiming to comply with evolving regulatory requirements and customer sustainability goals. Recent technical updates from these companies highlight the deployment of kinetic analysis to screen and validate new vulcanization agents, ensuring efficient cross-linking while minimizing the formation of nitrosamines and other hazardous byproducts.
In Asia, Sri Trang Agro-Industry Public Company Limited and Sime Darby Plantation Berhad are notable for integrating kinetic analysis into their upstream and midstream operations. These companies are collaborating with academic institutions and equipment manufacturers to refine latex compound recipes and optimize the vulcanization process parameters. Their ongoing projects for 2025 and beyond prioritize energy efficiency and waste reduction by leveraging predictive kinetic modeling.
Looking ahead, the next few years will likely see intensified collaboration between raw material producers, additive suppliers, and end-users. Digital transformation and adoption of Industry 4.0 solutions are set to further enhance the granularity and speed of kinetic data analysis, supporting faster product development cycles and more sustainable production methods. As regulatory and market pressures mount, companies that invest in advanced vulcanization kinetics analysis will be better positioned to deliver consistent, high-performance Hevea products while addressing environmental and health concerns.
2025 Market Forecasts: Growth, Demand, and Global Opportunities
The global market for Hevea-based natural rubber continues to experience robust growth, with vulcanization kinetics analysis emerging as a critical factor in process optimization and product innovation in 2025. As the tire, automotive, and industrial rubber goods industries seek to balance quality, efficiency, and sustainability, accurate and rapid analysis of vulcanization kinetics has become essential for both upstream raw material suppliers and downstream manufacturers.
In 2025, the adoption of advanced kinetic modeling—particularly real-time differential scanning calorimetry (DSC) and rheometric measurements—has expanded at major production facilities. Industry leaders such as The Goodyear Tire & Rubber Company and Michelin are investing in in-line monitoring systems to track vulcanization progress, seeking to minimize energy consumption and optimize cure cycles for Hevea-based compounds. These investments are driven by the need to meet increasingly stringent performance specifications as well as environmental regulations.
Asia-Pacific, particularly Thailand, Indonesia, and Malaysia, remains the dominant source of Hevea natural rubber, accounting for over 70% of global output. Regional organizations, including the Association of Natural Rubber Producing Countries, report that upstream processors are adopting kinetic analysis as part of quality control frameworks to improve batch consistency and maximize yield. As demand from electric vehicle (EV) manufacturers and sustainable product lines rises, producers are leveraging vulcanization kinetics data to tailor rubber formulations for specific end-user requirements.
On the technology front, 2025 marks a turning point for automation and data integration in vulcanization monitoring. Companies specializing in industrial automation, such as Siemens, are collaborating with rubber processors to implement sensor-driven feedback loops and AI-based analytics that further refine kinetic modeling of Hevea vulcanization. This enables real-time decision making, reducing scrap rates and enhancing product uniformity.
Looking ahead to the next few years, the outlook for Hevea vulcanization kinetics analysis is one of continued sophistication and market integration. The convergence of digitalization, sustainability imperatives, and evolving end-user demands is expected to spur further investment in laboratory and in-line kinetic analysis platforms. Stakeholders anticipate broader standardization of testing protocols and reporting metrics, with global organizations and manufacturers streamlining best practices to support circular economy goals and regulatory compliance.
Overall, 2025 is set to be a pivotal year for the commercialization and strategic deployment of vulcanization kinetics analysis in the Hevea rubber sector, reinforcing its role as a cornerstone of competitive advantage and operational excellence.
Technological Breakthroughs: Latest Advances and Patent Highlights
Hevea vulcanization—the crosslinking process transforming natural rubber latex into durable products—remains a cornerstone of the elastomer industry. In 2025, technological breakthroughs are reshaping the kinetics analysis of this process, driven by advances in instrumentation, digitalization, and sustainable chemistry. Leading industry players are intensifying their focus on optimizing vulcanization kinetics for both performance and environmental compliance.
Recent years have seen the widespread adoption of real-time rheological analysis and high-throughput screening to monitor cure kinetics in natural rubber compounds. State-of-the-art moving die rheometers and rotational rheometers, such as those deployed by The Goodyear Tire & Rubber Company and Michelin, allow for precise modeling of scorch time, optimum cure time, and crosslink density. These tools, paired with advanced software, enable rapid feedback, process optimization, and reduction of waste.
A key area of patent activity in 2023-2025 centers on novel accelerators and eco-friendly crosslinking agents. Major manufacturers—including SIBUR and LANXESS—are developing new vulcanization chemistry that minimizes nitrosamine formation and reduces toxic byproducts. Some patents focus on synergistic blends of secondary accelerators and zinc-free activators, reflecting both tightening regulations and market demand for sustainable rubber products.
Digital transformation is driving another wave of innovation. Companies like Bridgestone Corporation are integrating machine learning algorithms and data analytics platforms to predict vulcanization behavior from raw material properties and process parameters. These predictive models are being used to adjust formulations in real time, shortening development cycles and optimizing end-use properties.
Further, the application of in-situ spectroscopic techniques (such as FTIR and Raman) is enabling non-destructive, on-line monitoring of crosslink formation during vulcanization. This approach, pursued by research arms of major rubber producers, accelerates quality assurance and supports the scaling of next-generation Hevea-based materials.
Looking ahead to the next few years, the industry outlook points to continued patent activity around bio-based accelerators and energy-efficient curing methods (including microwave and radiation vulcanization). The combination of digital process control and green chemistry is expected to further advance both the precision and sustainability of Hevea vulcanization, keeping industry leaders at the forefront of global elastomer markets.
Sustainability and Regulatory Outlook: Standards, Trends, and Compliance
The analysis of vulcanization kinetics in Hevea brasiliensis (natural rubber) is undergoing significant transformation as sustainability and regulatory compliance become central to global rubber production and processing. In 2025, regulatory frameworks are increasingly targeting both the chemical additives used in vulcanization and the energy consumption of the process, reflecting broader environmental and safety concerns. The European Union, for instance, continues to update its REACH regulations, which restrict certain accelerators and curing agents traditionally employed in rubber vulcanization due to their potential health and ecological impacts. This regulatory pressure is prompting rubber manufacturers to adopt alternative, less hazardous accelerators and to optimize kinetic profiles for reduced byproduct formation and improved energy efficiency.
Industry leaders such as The Goodyear Tire & Rubber Company and Michelin are publicly committed to minimizing the environmental footprint of their natural rubber supply chains. These companies are investing in advanced kinetic modeling and in-line monitoring technologies, enabling real-time analysis of vulcanization kinetics and more precise control of process variables. This not only ensures compliance with tightening regulations but also supports the development of “green” rubber compounds with lower sulfur and nitrosamine-releasing accelerator content.
In addition, bodies such as the International Energy Forum and International Rubber Research and Development Board have highlighted the importance of energy-efficient processing methods. New reactor designs and the adoption of microwave and ultrasound-assisted vulcanization are being tested to reduce energy consumption and emissions during the crosslinking process. These innovations, coupled with the use of bio-based modifiers and renewable chemical inputs, are expected to shape compliance strategies for manufacturers in both established and emerging markets through 2025 and beyond.
Standardization efforts are also intensifying. The International Organization for Standardization (ISO) is updating technical standards related to rubber vulcanization, focusing on traceability, safe use of accelerators, and the verification of kinetic parameters critical to sustainability claims. Manufacturers supplying to global automotive and medical sectors, in particular, are expected to demonstrate robust compliance with these evolving standards, including transparent life-cycle assessments and third-party product certifications.
Looking ahead, the intersection of kinetic analysis with digitalization—such as AI-driven process optimization and blockchain traceability—will likely accelerate industry’s ability to meet stringent sustainability and regulatory benchmarks. Stakeholders across the value chain are therefore expected to prioritize continuous improvement in vulcanization kinetics, balancing regulatory demands with commercial viability and environmental stewardship.
Case Studies: Industry Applications and Real-World Performance
Hevea brasiliensis, the primary source of natural rubber, remains central to the global elastomer industry. The kinetics of vulcanization—transforming raw Hevea latex into durable, elastic material—continues to be a focus for industrial optimization, especially as manufacturers pursue greater efficiency and product consistency. In recent years, case studies from leading tire producers and rubber product manufacturers have highlighted advanced kinetic analysis methods and real-world performance results, setting benchmarks for 2025 and the near future.
One notable implementation is the adoption of real-time rheometric monitoring in large-scale tire manufacturing. Companies such as Michelin and Goodyear have integrated dynamic mechanical analysis and moving die rheometry into production lines. These techniques enable precise control over vulcanization time and temperature, reducing the risk of under- or over-cured products. Data from these systems show a significant reduction in scrap rates and improved batch-to-batch uniformity, aligning with the industry’s push for sustainability and waste minimization.
In Asia, where the majority of Hevea cultivation occurs, vertically integrated companies such as Sri Trang Agro-Industry are collaborating with global chemical suppliers to refine accelerators and activator systems tailored for local latex characteristics. Their field trials in 2023–2024 demonstrated that optimized sulfur and accelerator ratios, combined with kinetic modeling, shortened cure times by up to 12% without compromising mechanical properties. This approach is expected to gain further traction in 2025 as processor margins tighten and energy costs remain volatile.
Meanwhile, automotive and industrial goods manufacturers like Continental are leveraging digital twin simulations and in-line spectroscopic monitoring to predict kinetic behavior and adjust formulations in real time. This has led to improved predictability of final product properties, such as tear strength and resilience, as well as faster new product development cycles. Real-world case studies from 2024 show that such methods can reduce time-to-market for new compounds by several months.
The outlook for Hevea vulcanization kinetics analysis in 2025 and beyond is shaped by continuing digitization and data-driven process control. The integration of machine learning tools into kinetic modeling is anticipated to further fine-tune process parameters, enhancing both product performance and resource efficiency. As regulatory and sustainability demands intensify, industry leaders are expected to accelerate investments in advanced kinetic monitoring and control systems, ensuring Hevea-based products remain competitive and high-performing in a rapidly evolving market.
Challenges and Risks: Technical, Economic, and Supply Chain Factors
The analysis of vulcanization kinetics for Hevea brasiliensis (natural rubber) is critical for optimizing processing efficiency, product quality, and sustainability in 2025 and the coming years. However, several challenges and risks persist across technical, economic, and supply chain dimensions, affecting both research and industrial application.
Technical Challenges remain pronounced in real-time monitoring and accurate modeling of vulcanization kinetics. Natural rubber’s composition varies according to clone, plantation practices, and environmental exposure, which impacts reproducibility and complicates kinetic analysis. Advanced characterization techniques—such as real-time rheometry and spectroscopic monitoring—are increasingly adopted, but implementation at industrial scale lags due to the need for specialized equipment and expertise. Furthermore, the shift toward non-conventional accelerators and eco-friendly crosslinking agents introduces new kinetic profiles that require revalidation of existing models, adding to the complexity. Industry feedback underscores the need for standardized protocols to enable data comparability and process optimization (The Goodyear Tire & Rubber Company).
Economic Factors are closely intertwined with technical progress. The volatility of natural rubber prices—driven by weather events, disease outbreaks, and global demand—creates fluctuations in research budgets and capital expenditure for process upgrades. The cost of adopting new kinetic monitoring systems or environmentally safer chemicals can be prohibitive for small and medium-sized enterprises, even as regulatory pressure mounts for greener processes. Additionally, the transition to more sustainable vulcanization pathways may affect product performance, requiring investment in requalification and customer assurance (Michelin).
Supply Chain Risks have become more acute in recent years. The concentration of Hevea rubber production in Southeast Asia makes the industry vulnerable to regional disruptions—from disease (such as South American Leaf Blight) to geopolitical events and logistical bottlenecks. These vulnerabilities can delay the deployment of new kinetic analysis technologies and the sourcing of specialty additives required for advanced vulcanization systems. Leading tire manufacturers have initiated programs to diversify supply chains and invest in digital traceability to help mitigate such risks (Bridgestone Corporation).
Looking ahead, successful mitigation of these challenges will rely on collaborative efforts between producers, technology developers, and end-users. Industry forums and technical consortia are expected to play a larger role in the co-development of standardized testing protocols and open-access kinetic datasets. At the same time, ongoing investments in automation, digitalization, and alternative sources of natural rubber—such as guayule—are likely to shape the sector’s resilience and innovation capacity through 2025 and beyond.
Future Outlook: Disruptive Technologies and Strategic Roadmap to 2030
The future of Hevea vulcanization kinetics analysis is poised for significant transformation, driven by disruptive technologies and a rapidly evolving strategic landscape leading to 2030. As the global demand for natural rubber products continues to grow—especially in automotive, medical, and industrial sectors—the optimization of vulcanization processes is becoming a competitive imperative. In 2025 and the coming years, several advancements are anticipated to reshape this domain.
A key trend is the accelerated integration of real-time monitoring and advanced data analytics into vulcanization lines. Digitalization initiatives among leading rubber manufacturers, such as Michelin and Goodyear Tire & Rubber Company, are already leveraging sensor technologies, enabling precise control of temperature, pressure, and chemical reaction rates during the curing of Hevea-derived rubber. These systems facilitate the collection of continuous, high-resolution process data, allowing for the development of predictive kinetic models that minimize quality variation and energy consumption.
Artificial intelligence (AI) and machine learning algorithms are being deployed to analyze the complex, non-linear kinetics of sulfur cross-linking in natural rubber. This approach enhances the accuracy of cure time predictions and supports adaptive process control strategies. Major technology providers and rubber processors are investing in closed-loop control systems that automatically adjust vulcanization parameters based on real-time feedback, ensuring optimal cross-link density and mechanical properties. By 2027, it is expected that automated, AI-driven vulcanization monitoring will become a standard in high-volume production facilities, according to strategic roadmaps published by industry stakeholders such as Bridgestone Corporation.
Furthermore, the industry is exploring “green” vulcanization chemistries, such as alternative cross-linking agents and bio-based accelerators, to reduce environmental impact. Companies like Sri Trang Agro-Industry and Continental AG have announced R&D investments in eco-friendly compounding solutions, which require new kinetic models to accommodate different reaction pathways and rates. The adoption of these sustainable technologies will necessitate the development of advanced analysis tools that can accurately characterize the kinetics of novel systems, enabling regulatory compliance and market differentiation.
Looking toward 2030, the roadmap for Hevea vulcanization kinetics analysis is expected to emphasize interoperability between production data, laboratory analytics, and supply chain traceability platforms. This convergence will enable a holistic view of product performance, process efficiency, and sustainability metrics—empowering rubber producers to meet increasingly stringent customer and regulatory requirements while maintaining profitability and innovation leadership.