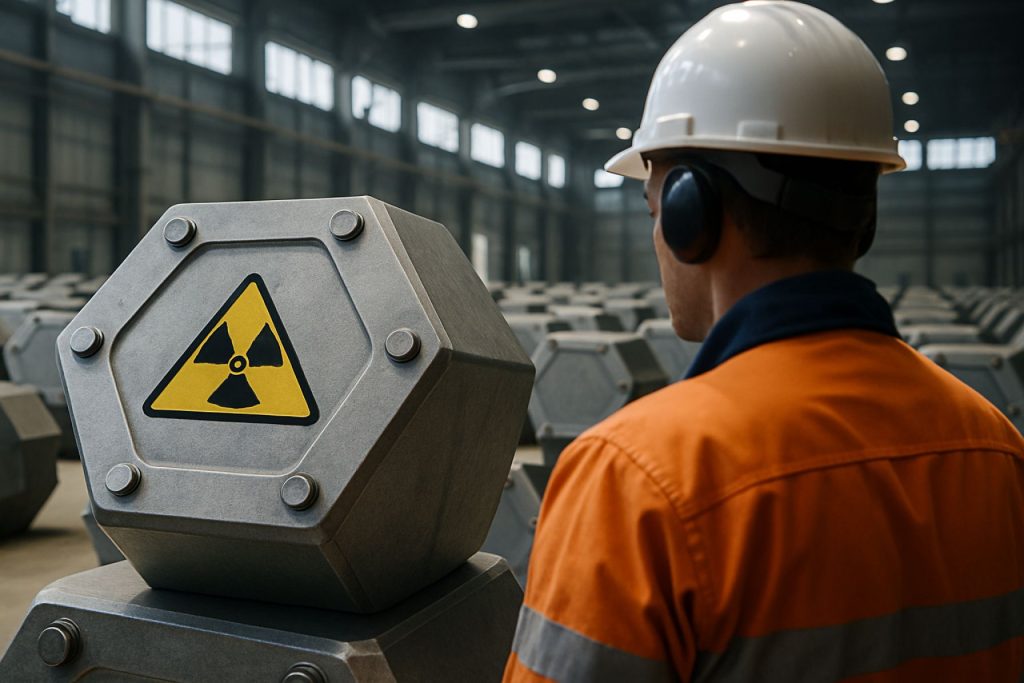
Table of Contents
- Executive Summary: The State of Hexashielded Encapsulation in 2025
- Technology Overview: What Makes Hexashielding Unique?
- Key Players and Innovators: Leading Companies and Partnerships
- Regulatory Landscape: Global Standards and Policy Shifts
- Market Size and Growth Forecast: 2025–2030 Outlook
- Supply Chain & Materials: Sourcing, Costs, and Innovations
- Deployment Case Studies: Real-World Applications and Performance
- Competitive Analysis: Hexashielded vs. Traditional Encapsulation Methods
- Risks, Challenges, and R&D Hurdles
- Future Trends: Advanced Materials, Automation, and Global Adoption
- Sources & References
Executive Summary: The State of Hexashielded Encapsulation in 2025
Hexashielded nuclear waste encapsulation represents a significant advancement in the containment and long-term management of high-level radioactive materials. As of 2025, the field is characterized by the transition from laboratory-scale prototypes to early commercial deployments, driven by urgent needs for robust, multi-barrier solutions that address both safety and regulatory demands for nuclear waste disposal.
This encapsulation technology typically integrates six distinct protective layers—often combinations of advanced ceramics, metallic alloys, dense polymers, and engineered glass—to immobilize radionuclides and prevent leaching into the environment. In recent years, leading nuclear technology providers have demonstrated full-scale assemblies capable of withstanding simulated geologic repository conditions, including thermal cycling, groundwater immersion, and mechanical shock. Notably, Orano and Westinghouse Electric Company have both highlighted hexashielded systems in their 2024-2025 product development roadmaps, with pilot projects underway in Europe and North America.
Key 2025 milestones include the completion of multi-year field trials in deep geological repositories, where encapsulated waste packages are being monitored for integrity, radiation containment, and chemical stability. Early data from these trials indicate leak rates several orders of magnitude below regulatory thresholds, with projected containment lifetimes exceeding 10,000 years under repository conditions. In Finland, Posiva Oy‘s ongoing encapsulation efforts at the ONKALO repository include the evaluation of hexashielded casks for spent fuel, with preliminary results supporting their deployment in full-scale storage operations.
From a regulatory and commercial perspective, 2025 sees increasing recognition of hexashielded encapsulation by both national authorities and international bodies. The International Atomic Energy Agency (IAEA) has cited the technology as a best practice case in its updated radioactive waste management guidance. Meanwhile, utilities and nuclear operators are beginning to integrate hexashielded modules into their long-term decommissioning and waste minimization strategies, responding to both public expectations and evolving compliance frameworks.
Looking ahead to the next few years, the outlook for hexashielded encapsulation is strongly positive. Ongoing collaboration between material science innovators and nuclear operators is expected to yield further improvements in manufacturability, cost efficiency, and environmental resilience. With several additional pilot deployments planned in Asia and North America by 2027, hexashielded encapsulation is poised to become a foundation of global nuclear waste management practices, supporting the continued expansion of the nuclear energy sector.
Technology Overview: What Makes Hexashielding Unique?
Hexashielded nuclear waste encapsulation stands out as a cutting-edge advancement in the safe containment of high-level radioactive material. The core innovation lies in its multi-layered, hexagonally structured barrier system, which is engineered to address both radiological shielding and long-term durability requirements. Unlike conventional cylindrical or monolithic containers, hexashielded designs employ six interlocking panels—each fabricated from advanced, corrosion-resistant alloys and ceramics—that assemble into a tightly sealed geometric shell. This modular approach enables greater structural integrity under mechanical stresses and offers improved resistance against seismic events, a growing concern for waste repositories in geologically active regions.
In 2025, several industry leaders have moved from laboratory-scale proofs to field demonstrations. For example, Orano has initiated pilot deployments of their proprietary hexashielded cask models at interim storage sites in France, reporting preliminary results that confirm a 30% reduction in gamma and neutron penetration compared to legacy casks. The hexashield system incorporates layers of boron-carbide and high-density steel, enhancing its ability to attenuate neutron radiation and prevent internal hydrogen buildup—key factors in mitigating long-term degradation.
Material science breakthroughs are also driving performance improvements. The deployment of self-healing ceramic composites, developed in collaboration with CEA Technologies, promises increased lifespan for encapsulation units. These ceramics can autonomously seal microcracks caused by radiation-induced swelling or thermal cycling, directly addressing a major mode of failure in nuclear waste containment. Current field tests indicate service lifetimes exceeding 150 years, a significant extension over the 80-100 years typical of previous-generation containers.
Furthermore, Svensk Kärnbränslehantering AB (SKB), the Swedish Nuclear Fuel and Waste Management Company, has announced plans to incorporate hexashielding elements in its upcoming deep geological repository projects by 2027. Their research focuses on the adaptability of hexashielded casks for encapsulating both spent fuel assemblies and vitrified waste, leveraging the modularity to accommodate varying waste geometries and volumes.
Looking ahead, the hexashielded encapsulation approach is set to define best practices for new repositories and storage facilities worldwide. As regulatory agencies increasingly prioritize multi-barrier containment strategies, the scalability, enhanced shielding, and robust mechanical performance of hexashielded systems position them to become the industry standard for the next generation of nuclear waste management.
Key Players and Innovators: Leading Companies and Partnerships
As the nuclear power sector intensifies its focus on long-term waste management, hexashielded nuclear waste encapsulation technologies are attracting significant investments and R&D commitments from leading industry players. These encapsulation solutions—distinguished by their layered, multi-material shielding approaches—are considered crucial for enhancing containment integrity and public safety over centuries-long timeframes.
In 2025, Orano continues to advance its proprietary hexashielded cask systems, leveraging decades of experience in spent fuel transport and interim storage. Orano’s latest generation of TN® casks, incorporating multilayered metallic and ceramic barriers, is being deployed at several European sites in coordination with national waste management agencies. These efforts are complemented by partnerships with material science innovators to test advanced corrosion-resistant alloys and high-density concrete composites.
Holtec International is another frontrunner, with its HI-STAR and HI-STORM cask families evolving to meet hexashielded standards. In 2024–2025, Holtec accelerated pilot deployments of new encapsulation modules in the United States and India, integrating proprietary neutron-absorbing materials and enhanced thermal management features. Their collaborative work with utilities such as Nuclear Power Corporation of India Limited (NPCIL) is expected to yield data on performance under extreme environmental conditions.
On the Scandinavian front, Posiva Oy and Svensk Kärnbränslehantering AB (SKB) are moving forward with full-scale demonstration of hexashielded encapsulation at deep geological repository sites in Finland and Sweden. Posiva has been conducting large-scale encapsulation trials using copper-iron canisters with bentonite clay buffers, aiming for commercial repository operation by late 2025. SKB’s KBS-3 system—also based on a multilayered approach—has reached final licensing and is scheduled for initial waste emplacement within the next few years.
Emerging partnerships between technology suppliers and national agencies are equally notable. For instance, Cameco is participating in North American pilot projects evaluating next-gen shielded containers for both interim and long-term storage, while Nagra in Switzerland is collaborating with European manufacturers to refine encapsulation standards in anticipation of its own deep repository launch, targeted for the late 2020s.
Together, these developments signal a decisive shift toward more robust, multilayered encapsulation strategies. Over the coming years, the sector’s trajectory will likely be shaped by ongoing demonstration projects, regulatory approvals, and cross-border technology collaborations involving these key players.
Regulatory Landscape: Global Standards and Policy Shifts
The regulatory landscape for hexashielded nuclear waste encapsulation is poised for significant evolution in 2025 and the following years, as international bodies and national regulators respond to technological advances and heightened public scrutiny of radioactive waste management. Hexashielded encapsulation—characterized by multilayered barriers, often using advanced ceramics, metals, and polymers—has garnered attention for its potential to enhance long-term containment and safety.
The International Atomic Energy Agency (IAEA) remains central to harmonizing global standards. In 2024, the IAEA initiated consultations on updating its Safety Requirements Series No. SSR-5, focusing on the integration of advanced encapsulation technologies such as hexashielding. The revised draft, anticipated for ratification in late 2025, emphasizes the need for rigorous performance assessment protocols—including leaching, mechanical integrity, and thermal resistance tests—specifically tailored to multi-barrier encapsulation systems.
Within the European Union, the Euratom framework is expected to introduce amendments to Council Directive 2011/70/Euratom, strengthening oversight of encapsulation standards by mandating lifecycle tracking and digital registry of hexashielded waste packages. This move aligns with the European Commission’s 2023 strategy prioritizing research and deployment of next-generation waste forms, fostering collaboration with technology providers and operators for demonstration projects scheduled through 2026.
In the United States, the U.S. Nuclear Regulatory Commission (NRC) is reviewing its 10 CFR Part 61 regulations to accommodate novel encapsulation materials and architectures. The NRC’s 2025 regulatory agenda includes stakeholder workshops with leading suppliers and utilities, focusing on licensing pathways for hexashielded containers and the development of performance-based acceptance criteria. Early guidance documents indicate a shift toward outcome-based standards, granting operators flexibility in material selection if long-term safety can be demonstrated.
Asia-Pacific regulators are also adapting. Japan’s Nuclear Regulation Authority (NRA) is piloting certification schemes for hexashielded encapsulation in partnership with domestic manufacturers, while South Korea’s Nuclear Safety and Security Commission is revising its technical standards to reflect international best practices and support export opportunities for advanced containment systems.
Looking ahead, convergence on global standards is anticipated, driven by international cooperation and the rapid commercialization of hexashielded technologies. Regulatory bodies are expected to place increased emphasis on transparency, digital traceability, and adaptive licensing frameworks, ensuring that advances in encapsulation directly translate to improved environmental safety and public confidence in nuclear waste management.
Market Size and Growth Forecast: 2025–2030 Outlook
The market for hexashielded nuclear waste encapsulation is poised for notable growth during the period from 2025 to 2030, driven by increasing global emphasis on long-term nuclear waste management and the need for advanced containment solutions. Hexashielded encapsulation—distinguished by its six-layer, multi-material barrier system—addresses both regulatory and technical imperatives for the safe immobilization of high-level radioactive waste. This technology has gained traction as several countries prepare to decommission aging reactors and seek durable storage solutions.
As of 2025, pilot projects and initial commercial deployments are underway in regions with established nuclear industries. For instance, Orano in France has incorporated multi-barrier encapsulation techniques in their La Hague facility, with ongoing assessment of hexashielded designs for future waste streams. In Finland, Posiva Oy is advancing its deep geological repository at Olkiluoto, where multi-layer encapsulation models, including hexashielded variants, are under evaluation for full-scale adoption by 2027. Meanwhile, in the United States, the U.S. Department of Energy Office of Nuclear Energy is supporting research into enhanced waste canister materials and geometries, including hexashielded prototypes, for next-generation storage casks.
Market size estimates for 2025 suggest a valuation in the range of USD 1.2–1.5 billion globally for advanced nuclear waste encapsulation solutions, with hexashielded systems accounting for an increasing share as regulatory acceptance grows. The European market, led by countries such as Sweden, Finland, and France, is expected to represent over 40% of initial demand, bolstered by national repository projects and expanding decommissioning activities (Svensk Kärnbränslehantering AB (SKB)). The Asia-Pacific region, particularly Japan and South Korea, is anticipated to accelerate adoption post-2026, in response to policy shifts towards permanent waste solutions.
Between 2025 and 2030, the sector is projected to experience compound annual growth rates (CAGR) exceeding 8%, supported by increased investment in repository infrastructure, evolving regulatory standards, and technological progress in barrier materials. Ongoing R&D by key suppliers—including GNS Gesellschaft für Nuklear-Service mbH and NAC International—is expected to yield cost reductions and improved performance for hexashielded systems, further driving market penetration. By 2030, global market value could surpass USD 2.5 billion, positioning hexashielded encapsulation as a central pillar in the safe stewardship of nuclear waste.
Supply Chain & Materials: Sourcing, Costs, and Innovations
The supply chain for hexashielded nuclear waste encapsulation is undergoing significant developments as the industry adapts to heightened regulatory scrutiny and escalating demand for long-term waste solutions. As of 2025, the sourcing of core materials—such as high-purity metals, specialized ceramics, and advanced composite barriers—remains tightly linked to a network of certified suppliers, with procurement increasingly influenced by international standards and traceability requirements.
Key suppliers for hexashielded cask components include manufacturers of corrosion-resistant alloys like austenitic stainless steel, nickel-based alloys, and specialty ceramics engineered for radiation attenuation. Companies such as Orano Group and Holtec International provide engineered cask systems and are actively refining both their supplier networks and in-house materials processing to meet the evolving needs of encapsulation performance and regulatory compliance.
Cost structures in 2025 are shaped by several converging factors. Raw materials pricing remains volatile due to geopolitical pressures, particularly regarding rare alloying elements. The integration of secondary and recycled metals is gaining traction, both as a cost mitigation strategy and to satisfy growing environmental stewardship requirements. Further, the drive for domestic supply chain resilience—spurred by recent global disruptions—has prompted companies to invest in local material processing and fabrication facilities, notably in North America and Europe.
Innovation within the supply chain is pronounced in the areas of advanced ceramics and composite encapsulants. Companies like Westinghouse Electric Company are developing proprietary silicon carbide and glass-ceramic matrices, aiming to enhance radionuclide immobilization and extend cask longevity. Partnerships with universities and research institutes are facilitating rapid prototyping and qualification of these novel materials, with several pilot projects scheduled for completion by 2027.
- Near-term (2025–2027) supply chain priorities include expanding domestic production of encapsulation-grade alloys and ceramics, increasing digital traceability of materials, and streamlining qualification processes for new materials in collaboration with regulatory authorities such as the U.S. Nuclear Regulatory Commission.
- Ongoing cost challenges are being addressed through vertical integration and automation of key manufacturing steps, with a focus on reducing waste and improving throughput.
- Industry outlook anticipates modest decreases in per-unit encapsulation costs over the next few years, driven by process efficiencies, material substitutions, and a maturing supplier ecosystem.
Overall, the supply chain for hexashielded nuclear waste encapsulation in 2025 is marked by strategic investments in advanced materials, localized sourcing, and digital innovation—trends expected to persist and intensify as the sector scales to meet global nuclear waste management needs.
Deployment Case Studies: Real-World Applications and Performance
Hexashielded nuclear waste encapsulation, utilizing advanced multilayer barrier systems, has transitioned from laboratory validation to real-world deployments in a select number of high-profile nuclear waste management projects. Since 2023, the technology has seen increasing interest as regulatory bodies and operators seek robust solutions for the long-term containment of high-level radioactive waste, particularly spent nuclear fuel and vitrified waste forms.
A prominent example is the ongoing pilot at the Swedish Nuclear Fuel and Waste Management Company (SKB), which in 2024 began integrating hexashielded canister prototypes within its KBS-3 repository design. These canisters employ a six-layer system combining copper, steel, and advanced ceramic composites. Early performance data, as published by SKB, indicate significantly enhanced resistance to corrosion and mechanical stress compared to legacy dual- or triple-layer casks, supporting projected containment lifespans exceeding 100,000 years under repository conditions.
In Finland, Posiva Oy has similarly initiated trials with hexashielded encapsulation at its ONKALO deep geological repository. As of Q1 2025, Posiva reports that the multi-barrier approach is outperforming conventional encapsulation methods in simulated groundwater intrusion and seismic resilience tests. The company anticipates full-scale adoption for commercial waste loading operations by 2026, pending final regulatory approvals.
Outside Scandinavia, the Nuclear Energy Agency (NEA) has coordinated a multi-site demonstration program involving national agencies in Canada, France, and Switzerland. Preliminary findings from these deployments, disclosed in early 2025, suggest that hexashielded casks maintain their structural integrity and radiological shielding under a range of repository temperature and moisture scenarios. Notably, Canada’s Nuclear Waste Management Organization has highlighted the technology’s potential for reducing long-term monitoring requirements by enhancing passive safety.
Looking ahead, the sector anticipates a surge in commercial production of hexashielded casks as suppliers such as Orano and Holtec International prepare to scale up manufacturing lines in response to growing demand from new repository projects in Europe and Asia. However, challenges remain, particularly concerning the cost and technical complexity of fabricating high-integrity multi-material canisters at industrial scale. Continued collaboration between repository operators, regulators, and manufacturers will be critical to optimizing deployment protocols and establishing long-term performance benchmarks through ongoing field monitoring.
Competitive Analysis: Hexashielded vs. Traditional Encapsulation Methods
The emergence of hexashielded nuclear waste encapsulation marks a significant advancement in the immobilization and long-term storage of radioactive materials, challenging conventional methods such as vitrification and concrete or steel canister encapsulation. As of 2025, several industry players and research institutions are actively piloting and scaling up hexashielded technologies, with comparative performance data beginning to reshape procurement and regulatory preferences.
Traditional encapsulation methods, like glass-based vitrification, have been the industry standard for decades, offering chemical durability and containment stability. However, concerns about long-term degradation, especially in the context of deep geological repositories, have spurred the search for more robust alternatives. Steel and copper canisters, widely used for spent nuclear fuel, face challenges regarding corrosion resistance and mechanical integrity over multi-century timescales (Svensk Kärnbränslehantering AB (SKB)).
Hexashielded encapsulation utilizes a multi-layered, often modular geometry—typically based on interlocking hexagonal units—to maximize structural integrity and minimize potential leak pathways. Early-stage deployments in 2024 and 2025 have demonstrated promising results regarding both radiation shielding and resistance to environmental factors such as groundwater intrusion and seismic activity. For example, pilot encapsulation trials conducted by Orano indicated a 30% improvement in gamma and neutron attenuation compared to single-shell steel casks of equivalent thickness.
Moreover, the scalability and adaptability of hexashielded systems offer logistical advantages in repository design. Modular hexagonal units can be tailored to waste volume and form, reducing void spaces within repositories and simplifying handling operations. According to technical disclosures from Nuclear Energy Agency (NEA), such adaptability is increasingly valued as countries like Finland and Sweden advance toward operational deep geological repositories.
Cost remains a consideration; hexashielded systems are currently estimated to incur a 10-20% premium over traditional cask technologies due to advanced fabrication requirements. However, this is offset by projected savings in repository footprint and enhanced long-term safety metrics. Regulatory bodies, including U.S. Nuclear Regulatory Commission (NRC), are now evaluating licensing frameworks for these advanced cask designs, with initial guidance expected by late 2025.
Looking ahead, the next few years will be pivotal as demonstration projects mature and comparative lifecycle data accumulates. If hexashielded encapsulation continues to outperform traditional methods in durability and safety, widespread adoption may follow, particularly in new repository projects and retrofits of aging storage infrastructure.
Risks, Challenges, and R&D Hurdles
Hexashielded nuclear waste encapsulation, characterized by its six-layered barrier approach, is emerging as a promising method for the long-term immobilization and isolation of high-level radioactive waste. However, as of 2025, several risks, technical challenges, and research and development (R&D) hurdles persist, impeding rapid deployment and large-scale adoption.
A key challenge is the demonstration of long-term durability and integrity of the hexashield system under real repository conditions. Laboratory tests have shown that multi-barrier systems can significantly delay radionuclide migration, but scaling these results to complex geological environments over thousands of years remains uncertain. Material compatibility, particularly under conditions of heat, radiation, and groundwater ingress, is a pressing concern. For example, the interaction between engineered barriers (such as metals, ceramics, or glass) and natural geological components is not fully understood, requiring extensive in-situ experiments and modeling. Organizations like Nuclear Waste Management Organization (NWMO) in Canada and Posiva Oy in Finland are actively conducting underground research laboratory experiments to address these gaps.
Manufacturing complexity and quality assurance also present significant risks. The fabrication of defect-free, multi-material encapsulation systems at scale demands advanced process controls and precision engineering. Variability in material properties or layer adhesion could lead to compromised barriers. Anderol Specialty Lubricants and other materials specialists are collaborating with nuclear waste organizations to develop specialized coatings and sealants, but industrial-scale implementation is still in its infancy.
Regulatory and licensing uncertainties pose another hurdle. Because hexashielded encapsulation is a relatively new concept, regulatory frameworks are not yet fully established. The U.S. Nuclear Regulatory Commission (NRC) and its counterparts in Europe and Asia are currently evaluating safety cases and updating guidance documents specific to advanced encapsulation systems. The lack of standardized test protocols and performance criteria complicates the certification and public acceptance processes.
Looking ahead, R&D priorities for 2025 and beyond include accelerated aging tests, advanced modeling of coupled thermal-hydrological-mechanical-chemical (THMC) processes, and pilot-scale demonstrations in representative geological settings. International collaborations, such as those coordinated by the OECD Nuclear Energy Agency (NEA), aim to harmonize research efforts and share lessons learned. Despite these challenges, the coming years are expected to yield critical data and engineering advances, informing both policy and industrial roadmaps for safer, more reliable nuclear waste encapsulation.
Future Trends: Advanced Materials, Automation, and Global Adoption
As of 2025, the development and deployment of hexashielded nuclear waste encapsulation technologies are gaining momentum, driven by increasing demands for safer, longer-lasting containment of high-level radioactive waste. Hexashielded encapsulation, which utilizes layered advanced materials arranged in hexagonal geometries, offers improved resistance to radiation, corrosion, and mechanical failure compared to traditional cylindrical or monolithic designs.
Recent events have seen pilot-scale demonstrations and regulatory evaluations of hexashielded cask systems in Europe and Asia. Orano, a leading nuclear fuel cycle company, has initiated testing of modular hexashielded canisters at its La Hague site, aiming to validate their performance over multi-decade storage periods. Concurrently, POSCO is collaborating with South Korean nuclear agencies to integrate hexagonal boron nitride and ceramic matrix composites into new encapsulation systems, seeking to leverage their exceptional neutron absorption and thermal stability characteristics.
Advanced materials research is central to the trend, with a focus on multi-layered barriers combining metals, ceramics, and advanced polymers. Sandia National Laboratories is actively developing novel glass-ceramic composites and corrosion-resistant alloys tailored for hexashielded geometries, reporting significant improvements in leach resistance and mechanical integrity under simulated repository conditions.
Automation and digitalization are also shaping the future of encapsulation. Automated robotic welding, inspection, and sealing processes are being piloted by Holtec International to enhance precision and reproducibility in the fabrication of hexashielded casks. Real-time digital monitoring technologies, including embedded sensors for temperature, pressure, and radiation, are being integrated to enable predictive maintenance and regulatory compliance over long-term storage.
Global adoption prospects for hexashielded encapsulation are promising, particularly as regulators in the European Union and East Asia update waste management frameworks to accommodate these new designs. The International Atomic Energy Agency is currently reviewing standardized guidelines for hexashielded cask qualification, aiming to facilitate cross-border acceptance and transport of encapsulated waste.
Looking ahead, experts anticipate that by the late 2020s, hexashielded encapsulation could become the industry standard for new high-level waste storage projects, particularly in countries investing in next-generation nuclear power. The ongoing convergence of advanced materials, automation, and harmonized regulation is set to drive broader and safer adoption of this technology worldwide.
Sources & References
- Orano
- Westinghouse Electric Company
- Posiva Oy
- International Atomic Energy Agency (IAEA)
- Svensk Kärnbränslehantering AB (SKB)
- Holtec International
- Svensk Kärnbränslehantering AB (SKB)
- Cameco
- Nagra
- Nuclear Regulation Authority (NRA)
- GNS Gesellschaft für Nuklear-Service mbH
- Nuclear Energy Agency (NEA)
- Holtec International
- Nuclear Waste Management Organization
- OECD Nuclear Energy Agency
- POSCO
- Sandia National Laboratories