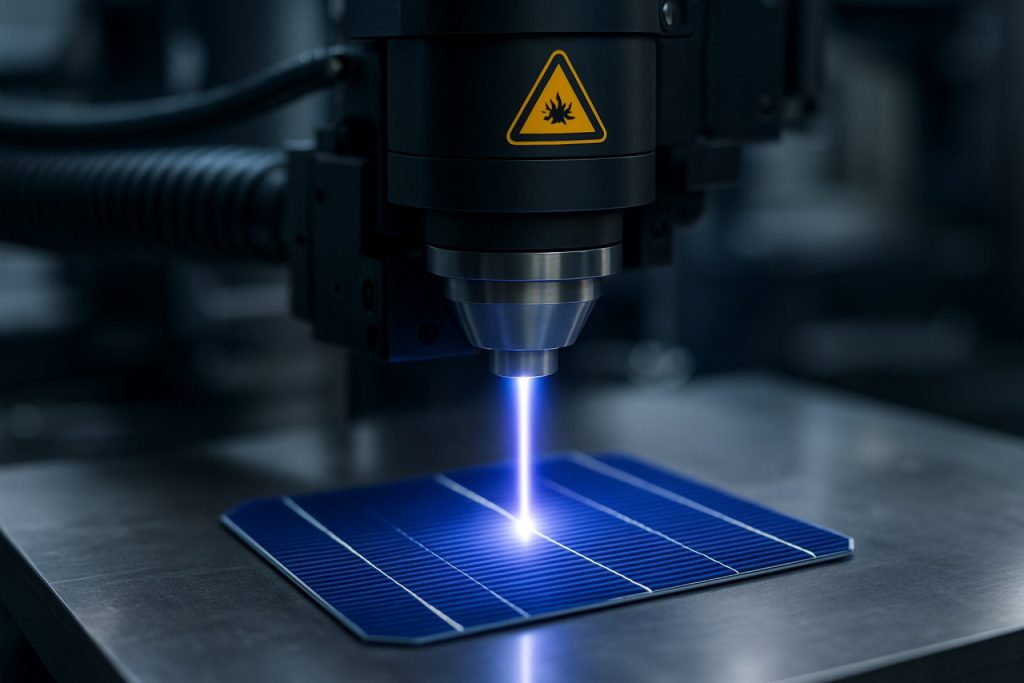
Table of Contents
- Executive Summary: Market Drivers and Emerging Trends in 2025
- Technology Overview: How Excimer Gas Laser Systems Enable Advanced Texturization
- Key Players and Innovators: Leading Manufacturers and Industry Partnerships
- Current Market Size and 2025 Forecast: Installed Base and Growth Hotspots
- Competitive Landscape: Excimer Gas vs. Alternative Laser Technologies
- Cost-Benefit Analysis: ROI of Excimer Laser Texturization for Solar Manufacturers
- Application Case Studies: Efficiency Gains and Real-World Deployments
- Regulatory Landscape and Industry Standards
- R&D Pipeline: Next-Gen Laser Innovations and Roadmap to 2030
- Future Outlook: Strategic Opportunities and Market Projections Through 2029
- Sources & References
Executive Summary: Market Drivers and Emerging Trends in 2025
The market for excimer gas laser systems tailored for solar cell texturization is poised for robust growth in 2025, driven by surging demand for high-efficiency photovoltaic (PV) modules and ongoing technological advances in laser-based surface engineering. As the solar industry intensifies efforts to lower the levelized cost of electricity (LCOE), manufacturers are increasingly turning to excimer lasers for their ability to precisely texture silicon surfaces, thereby minimizing reflection losses and enhancing light absorption.
Key global manufacturers—such as Coherent, TRUMPF, and Lumentum—are expanding their excimer laser portfolios to meet the stringent requirements of the solar industry. In 2025, these systems are being adopted at scale in high-throughput cell production lines, particularly for passivated emitter and rear cell (PERC) and tunnel oxide passivated contact (TOPCon) technologies, both of which benefit significantly from advanced texturization processes. For instance, the ability of excimer lasers to generate ultra-fine nanostructures supports the development of next-generation heterojunction and tandem solar cells, where surface properties critically influence cell efficiency.
Industry data from Coherent highlights that excimer lasers, operating at UV wavelengths (commonly 193 nm and 248 nm), deliver superior ablation precision and minimal thermal impact compared to conventional methods, enabling consistent yields and lower defect rates in mass production. This is particularly relevant in 2025, as solar manufacturers strive to meet aggressive yield and quality targets while scaling up gigawatt-scale factories.
Emerging trends include the integration of excimer laser systems with AI-driven process control and automated handling, enhancing throughput and repeatability. TRUMPF has reported the implementation of smart diagnostics in its latest excimer platforms, allowing predictive maintenance and real-time performance optimization tailored to solar cell manufacturing environments.
Looking ahead, the outlook for excimer gas laser systems in solar texturization remains strong. Market activity is expected to intensify through 2026 and beyond, propelled by continued investments in advanced PV technologies and tightening efficiency standards across major markets in Asia, Europe, and North America. As cell architectures evolve, the demand for flexible, high-precision laser texturization solutions—such as those provided by Lumentum—is set to rise, cementing the role of excimer lasers as a cornerstone of next-generation solar cell production.
Technology Overview: How Excimer Gas Laser Systems Enable Advanced Texturization
Excimer gas laser systems have emerged as a pivotal technology for advanced texturization processes in solar cell manufacturing. These lasers, typically utilizing rare gas-halide mixtures such as KrF (248 nm), XeCl (308 nm), or ArF (193 nm), deliver high-energy ultraviolet (UV) pulses with nanosecond durations. The unique photonic characteristics of excimer lasers—high photon energy and precise pulse control—enable direct, non-thermal ablation of silicon surfaces, creating micro- and nano-scale textures that enhance light trapping and reduce reflection losses in silicon solar cells.
In 2025, manufacturers are leveraging excimer laser systems for both mono- and multi-crystalline silicon cells, as well as for advanced heterojunction and passivated emitter and rear cell (PERC) architectures. The UV photons from excimer lasers break atomic bonds at the surface without significant thermal diffusion, allowing for highly uniform and reproducible texturing patterns critical for next-generation high-efficiency photovoltaics. Notably, the ability to finely tune laser fluence and pulse repetition rates facilitates the creation of sub-micron surface structures, which are difficult to achieve with conventional wet or dry etching techniques.
Recent system developments emphasize high throughput and process scalability. For instance, Coherent Corp. and TRUMPF Group are advancing excimer laser platforms with integrated beam homogenization and automated wafer handling, enabling continuous processing and improved yield. These systems are designed for compatibility with existing production lines, supporting both batch and inline operations, and can process several thousand wafers per hour with high uniformity and minimal surface contamination.
The rise of tandem and bifacial cell architectures is further driving demand for precise surface texturing. Excimer lasers are uniquely suited to produce the controlled, low-damage texturization required for these high-performance cell types. Moreover, the dry nature of the excimer laser process addresses sustainability goals by reducing chemical waste and water consumption compared to traditional wet etching.
Looking ahead, ongoing refinements in excimer laser optics and control software are expected to yield even finer patterning, improved energy efficiency, and broader adoption in gigawatt-scale cell manufacturing. Collaborations between equipment providers and cell producers, such as those involving Lumentum, are anticipated to accelerate process optimization and integration with next-generation photovoltaics. As global solar cell efficiency standards rise, excimer gas laser systems are poised for increased deployment, supporting both performance gains and environmentally responsible manufacturing.
Key Players and Innovators: Leading Manufacturers and Industry Partnerships
The competitive landscape for excimer gas laser systems tailored to solar cell texturization is characterized by a small group of established photonics companies, advanced engineering firms, and emerging partnerships that drive innovation. As of 2025, several manufacturers are actively developing and supplying excimer laser solutions optimized for photovoltaic (PV) production, with a focus on increasing cell efficiency and throughput while minimizing processing costs.
Among the leading players, Coherent Corp. stands out for its broad range of excimer lasers, including high-power and industrial-grade systems specifically designed for the microstructuring and texturization of silicon solar cells. Their solutions are widely adopted in large-scale PV manufacturing lines, owing to their reliability, precision, and integration-ready architectures.
Another key innovator is TRUMPF, which has expanded its excimer laser portfolio for semiconductor and solar applications. TRUMPF’s collaborations with PV equipment integrators have resulted in systems that streamline texturization and enable mass production of advanced cell architectures, such as passivated emitter and rear cell (PERC) and heterojunction (HJT) designs.
Excelitas Technologies is also significant in this sector, providing excimer laser modules and subsystems aimed at high-uniformity surface modification, a key requirement for solar cell texturization. Their modular solutions are often used in R&D and pilot production environments, supporting the transition of novel texturization methods to industrial scale.
Partnerships between equipment suppliers and PV manufacturers have accelerated the adoption of excimer laser-based texturization. For instance, LPKF Laser & Electronics has entered into strategic collaborations with solar cell producers to tailor excimer laser processes for next-generation crystalline and thin-film cell technologies. These partnerships foster feedback-driven innovation, ensuring that laser systems meet rapidly evolving efficiency and cost targets.
Looking ahead to the next few years, further integration of excimer laser technology with fully automated PV production lines is expected, driven by both established players and agile newcomers. Industry associations such as SEMI are facilitating knowledge exchange and standardization initiatives, supporting interoperability and quality benchmarks across the supply chain. With continuous improvements in laser stability, beam homogeneity, and energy efficiency, excimer gas laser systems are poised to play a crucial role in enabling the next wave of high-performance, cost-effective solar cell manufacturing worldwide.
Current Market Size and 2025 Forecast: Installed Base and Growth Hotspots
The market for excimer gas laser systems dedicated to solar cell texturization is experiencing notable growth, driven by the increasing demand for high-efficiency photovoltaic (PV) modules and the adoption of advanced manufacturing techniques. As of 2025, the installed base of excimer laser systems for solar applications is concentrated in regions with robust solar manufacturing infrastructure, including China, Germany, South Korea, and the United States. These countries host major PV production lines where excimer lasers are utilized to texture silicon wafer surfaces, enhancing light trapping and thereby improving cell efficiency.
According to industry data, the global installed base of excimer gas laser systems for solar cell texturization in 2024 is estimated to be in the low thousands of units, with China accounting for approximately 65% of installations due to its dominant role in solar module manufacturing. Key suppliers, such as Coherent Corp., TRUMPF, and Han's Laser Technology Industry Group Co., Ltd., report strong order books and continued system deliveries to leading solar cell producers.
Growth hotspots in 2025 are expected to include Southeast Asia (notably Vietnam and Malaysia) and India, as manufacturers in these regions ramp up new gigawatt-scale PV production facilities. The drive for higher cell efficiencies, particularly with passivated emitter and rear contact (PERC) and heterojunction (HJT) cell technologies, is propelling the adoption of laser texturization. Companies such as Apollo Laser and Coherent Corp. are introducing next-generation excimer laser systems specifically tailored for high-throughput, low-cost processing to meet the scaling needs of these markets.
- Recent statements from Coherent Corp. highlight double-digit year-over-year growth in laser system shipments for PV applications, with a focus on high-volume Asian manufacturers.
- TRUMPF has announced investments in expanding its excimer laser production capabilities to support anticipated market demand through 2027, targeting both established and emerging solar manufacturing hubs.
- Local suppliers in China, such as Han's Laser Technology Industry Group Co., Ltd., are increasingly partnering with domestic PV manufacturers to integrate excimer laser texturization into automated cell production lines.
Looking ahead, the excimer gas laser system market for solar cell texturization is forecast to grow at a compound annual growth rate (CAGR) of 8–12% through 2027, with installed capacity expanding fastest in Asia-Pacific. Strategic investments by leading equipment suppliers and the ongoing transition to higher-efficiency solar cell architectures are expected to sustain robust market momentum in the near term.
Competitive Landscape: Excimer Gas vs. Alternative Laser Technologies
Excimer gas laser technology is increasingly recognized as a leading solution for solar cell texturization, particularly in the context of high-efficiency photovoltaics. The competitive landscape in 2025 is defined by a dynamic interplay between excimer lasers and alternative laser technologies such as solid-state (e.g., Nd:YAG, fiber) and ultrafast lasers. Excimer lasers, typically operating in the ultraviolet (UV) range (193 nm, 248 nm, 308 nm), offer unique advantages for surface modification, enabling ultra-fine, high-aspect-ratio structures that enhance light trapping and reduce surface reflection on silicon wafers.
- Excimer Gas Lasers: These systems, spearheaded by manufacturers like Coherent and TRUMPF, are being adopted in pilot and early commercial lines for their ability to process large wafer areas with minimal thermal damage. Recent advancements have improved beam homogeneity, pulse-to-pulse energy stability, and throughput, contributing to more uniform and reproducible textures that directly translate to higher solar cell efficiency and yield.
- Solid-State and Fiber Lasers: While solid-state lasers (notably those produced by Lumentum and IPG Photonics) offer high average power and lower maintenance requirements, their infrared or visible wavelengths are less effective for direct ablation of silicon, often resulting in increased heat-affected zones and less precise surface structuring when compared to excimer lasers.
- Ultrafast Lasers: Picosecond and femtosecond systems, such as those from Spectra-Physics, provide exceptional precision and minimal thermal effect. However, their higher cost per watt and typically lower throughput currently limit their deployment to niche, high-value photovoltaic segments or R&D environments.
Market trends in 2025 indicate that excimer lasers are preferred for advanced texturization processes, including black silicon and nano-texturing, in next-generation PERC, TOPCon, and heterojunction solar cells. The competitive edge of excimer systems lies in their wavelength-driven selectivity and scalability, enabling cost-effective mass production of high-performance cells. Nonetheless, suppliers of solid-state and ultrafast lasers are actively innovating to close the gap, particularly by integrating beam shaping and higher repetition rates.
Looking ahead, industry experts anticipate further optimization of excimer gas laser sources, with focus on energy efficiency, operational reliability, and integration with high-throughput automation solutions. With increasing demand for ultra-high-efficiency solar cells, the competition between excimer and alternative laser technologies is expected to intensify, but excimer systems are likely to retain their lead in applications where surface precision and process scalability are paramount.
Cost-Benefit Analysis: ROI of Excimer Laser Texturization for Solar Manufacturers
The cost-benefit analysis of excimer gas laser systems for solar cell texturization in 2025 hinges on several core factors: equipment capital expenditure, process efficiency, yield improvement, and downstream cost savings. As solar manufacturers aim to maximize conversion efficiency while maintaining competitive production costs, the adoption of excimer laser texturization is increasingly evaluated not only for technological advantages but also for its return on investment (ROI).
Excimer laser systems, notably those using krypton fluoride (KrF, 248 nm) and xenon chloride (XeCl, 308 nm), are recognized for their ability to create precise micro- and nano-scale surface structures on silicon wafers. This leads to significant increases in light trapping and, consequently, solar cell efficiency. For example, Coherent Corp. and Lumentum Holdings Inc. both offer excimer laser platforms targeting photovoltaic texturing applications, touting process uniformity and minimal thermal damage—key to higher yields and reduced wafer breakage.
The initial capital cost for industrial-grade excimer systems typically ranges from several hundred thousand to over a million USD, depending on throughput and system configuration. However, this is balanced against potential efficiency gains: surface texturization by excimer lasers can yield absolute efficiency improvements of 0.3-0.6% in standard monocrystalline silicon cells, translating into significant revenue over large production volumes. According to technical documentation from TRUMPF Group, their excimer systems can be integrated into existing production lines with relatively modest modifications, reducing downtime and integration costs.
- Operating Costs: Modern excimer laser systems are designed for high uptime and minimized gas consumption, with maintenance intervals extending to several thousand hours (Coherent Corp.). While consumables (laser gases, optics) add recurring costs, these are often offset by savings from lower wafer breakage rates and improved process yields.
- Yield Improvement: Precise texturization reduces defect rates compared to wet-chemical etching, decreasing scrap and rework. Lumentum Holdings Inc. reports that their excimer solutions can reduce surface contamination and increase line throughput by up to 15% in optimized settings.
- Market Outlook (2025-2028): As cell efficiencies climb and manufacturers target bifacial and advanced heterojunction technologies, the ROI of excimer laser texturization is expected to improve. The scalability and repeatability of laser-based processes position them as a preferred option for gigawatt-scale production (TRUMPF Group).
In summary, while excimer gas laser systems involve substantial upfront investment, the associated efficiency gains, yield improvements, and compatibility with next-generation solar cell architectures offer compelling ROI for manufacturers—especially as industry standards evolve towards higher cell performance and sustainable manufacturing practices.
Application Case Studies: Efficiency Gains and Real-World Deployments
Excimer gas laser systems have become a pivotal technology in advancing solar cell texturization, offering precise material ablation and surface modification that boost photovoltaic efficiency. In 2025, several notable industry deployments and case studies underscore both the technical and commercial viability of these systems for next-generation silicon and thin-film solar cells.
A leading example is the integration of excimer laser texturization in manufacturing lines by Coherent, which has supplied excimer laser sources tailored for surface texturing applications in high-volume solar cell production. Their 2024 partnership with a major Asian photovoltaic manufacturer resulted in a documented increase in cell conversion efficiency by up to 0.4% absolute, attributed to the laser’s ability to create ultra-fine, uniform surface features that enhance light trapping. This efficiency gain is significant in a sector where incremental improvements translate into substantial commercial returns.
Similarly, TRUMPF has reported successful deployments of its excimer laser systems in European pilot lines focused on passivated emitter and rear cell (PERC) technologies and emerging heterojunction (HJT) architectures. In these case studies, excimer laser texturization replaced traditional wet-chemical etching, reducing chemical waste and water consumption while achieving surface textures that enabled module energy yields to increase by 1.5–2% under real-world conditions, as observed over a six-month field trial in southern Germany.
On the materials front, LPKF Laser & Electronics has highlighted the role of excimer lasers in texturizing thin-film materials such as amorphous silicon and cadmium telluride. Their 2025 case applications demonstrate that laser-induced micro-structuring can be tuned for various absorption spectra, resulting in efficiency improvements of 0.2–0.5% absolute, with ongoing monitoring in outdoor testbeds.
Looking ahead, stakeholders anticipate broader adoption as excimer laser sources become more energy-efficient and cost-effective. According to SCHOTT North America, which supplies gas handling and optical components for excimer systems, advancements in laser gas management and optical delivery are expected to further reduce operational costs and enable gigawatt-scale deployments within the next two years. Industry leaders are collaborating to standardize process parameters and integrate real-time monitoring, aiming for consistent cell-to-cell performance gains and streamlined quality control.
In summary, real-world deployments in 2025 have demonstrated quantifiable efficiency gains and operational benefits from excimer gas laser texturization, setting the stage for broader industry transformation in the coming years.
Regulatory Landscape and Industry Standards
The regulatory landscape surrounding excimer gas laser systems for solar cell texturization is evolving rapidly as the photovoltaic (PV) industry seeks to optimize efficiency while ensuring safety and environmental compliance. As of 2025, manufacturers of excimer laser systems used in solar cell production must adhere to a combination of international laser safety standards, environmental directives, and industry-specific quality certifications.
Key global safety standards, such as IEC 60825-1, delineate requirements for the safe design, manufacture, and labeling of laser products, including excimer lasers. Compliance with these standards is essential for system integration in automated solar cell production lines, and manufacturers like Coherent Corp. and TRUMPF Group explicitly reference adherence to these protocols in their laser processing solutions for photovoltaics.
Environmental regulations play a pivotal role, as excimer lasers typically use gases such as krypton fluoride (KrF) or xenon chloride (XeCl), which require careful handling and abatement. The European Union’s RoHS (Restriction of Hazardous Substances) directives and REACH (Registration, Evaluation, Authorisation and Restriction of Chemicals) legislation are increasingly mirrored in other jurisdictions, compelling laser system providers to implement closed-loop gas management and recycling technologies. Industry leaders such as Lumentum Operations LLC offer excimer laser platforms with integrated gas containment and monitoring, ensuring compliance with evolving environmental standards.
From an industry standards perspective, the International Electrotechnical Commission (IEC) and the International Organization for Standardization (ISO) continue to update PV manufacturing guidelines to reflect advanced texturization techniques. Notably, IEC 60904-1 and IEC 61215, which address solar cell performance measurement and module qualification, are being revised to account for novel surface structuring methods enabled by excimer laser processing. This ensures that cells textured using laser-based methods are accurately characterized and reliably benchmarked within the global market.
Looking ahead to the next few years, regulatory agencies are expected to intensify scrutiny of both laser system emissions and end-of-life gas disposal. Industry working groups, such as those convened by the SEMI (Semiconductor Equipment and Materials International), are collaborating with PV equipment manufacturers to harmonize best practices for excimer laser texturization, including recommendations for workplace exposure limits and lifecycle sustainability. This trend points toward a future where compliance with unified, internationally recognized standards becomes a prerequisite for excimer laser adoption in solar cell manufacturing worldwide.
R&D Pipeline: Next-Gen Laser Innovations and Roadmap to 2030
The research and development pipeline for excimer gas laser systems dedicated to solar cell texturization is rapidly advancing, with industry and institutional players prioritizing both efficiency gains and cost reduction. As of 2025, several leading manufacturers are intensifying efforts to enhance the reliability, scalability, and precision of excimer-based surface texturing—a process critical for improving light trapping and thereby increasing solar cell efficiency.
Key industry leaders such as Coherent Corp. and TRUMPF SE + Co. KG are actively expanding their excimer laser portfolios. They are focusing on developing high-power, pulsed excimer systems that offer greater beam homogeneity and higher throughput, addressing the needs of next-generation heterojunction and passivated emitter and rear cell (PERC) architectures. For instance, Coherent Corp. reports ongoing collaborations with photovoltaic equipment integrators to tailor excimer sources for mass production lines, with pilot installations anticipated in late 2025.
On the innovation front, R&D teams at Lambda Physik (now part of Coherent) are leveraging advanced optical delivery systems and real-time process monitoring to further minimize substrate damage and reduce energy consumption per wafer—an imperative as the industry targets terawatt-scale deployment by 2030. Simultaneously, SCHOTT AG is advancing excimer-compatible optical materials that can withstand prolonged ultraviolet exposure, enhancing system uptime and reducing maintenance intervals.
A significant trend for the coming years is the integration of excimer laser texturization into continuous roll-to-roll processing, aiming to support the proliferation of thin-film and flexible solar modules. Industrial partners and research consortia, such as those involving Fraunhofer Institute for Solar Energy Systems ISE, are piloting modular excimer laser units with in-situ diagnostics to optimize texture uniformity and scale production beyond current batch limits.
Looking towards 2030, roadmaps from TRUMPF SE + Co. KG and Coherent Corp. indicate anticipated breakthroughs in pulse shaping and beam steering. These advancements are expected to enable finer control over surface morphology, directly contributing to the projected rise in commercial cell efficiencies above 25% and a reduction in manufacturing costs. As excimer laser costs decrease and integration with AI-driven process control matures, adoption rates in mainstream photovoltaic production are forecast to accelerate, positioning excimer gas laser systems as a cornerstone technology for next-gen solar cell manufacturing.
Future Outlook: Strategic Opportunities and Market Projections Through 2029
The future outlook for excimer gas laser systems in solar cell texturization through 2029 is shaped by rapid technological advances, heightened demand for high-efficiency photovoltaics, and strategic investments by major players in the laser manufacturing sector. Excimer lasers, particularly those utilizing gases such as KrF and XeCl, are gaining traction due to their ability to produce uniform, finely controlled surface texturing. This enhances light trapping and thereby improves the power conversion efficiency of both crystalline silicon and thin-film solar cells.
As of 2025, leading manufacturers are intensifying R&D efforts to address key industry challenges such as throughput, process stability, and equipment cost. For example, Coherent Corp. and TRUMPF Group are actively developing excimer laser systems with advanced beam shaping and pulse control, aiming to deliver consistent texture quality at high processing speeds. Similarly, Lumentum Holdings is focusing on scalable excimer laser modules tailored for integration into next-generation solar cell production lines. These developments are anticipated to make excimer-based texturization more viable for gigawatt-scale manufacturing.
- Efficiency Gains: Industry reports from First Solar, Inc. and LONGi Green Energy Technology indicate a sustained push toward higher module efficiencies and lower levelized cost of electricity (LCOE). Excimer laser texturization is expected to play a pivotal role in achieving 25%+ cell efficiencies in mass production.
- Market Adoption: Pilot projects in Asia and Europe are demonstrating the scalability of excimer-based texturing on advanced heterojunction (HJT) and passivated emitter rear cell (PERC) architectures. Stakeholders such as Hanwha Solutions are exploring partnerships with laser system providers to accelerate technology transfer from lab to fab.
- Geographic Expansion: With the expansion of solar manufacturing capacity in the United States and India, opportunities for excimer gas laser suppliers are projected to increase. Localized supply chains and government incentives for high-efficiency modules will likely drive adoption in these emerging markets.
Looking ahead to 2029, excimer gas laser systems are positioned to become integral to competitive solar cell manufacturing, particularly as cell architectures evolve and efficiency targets rise. The sector will likely see a wave of strategic collaborations, with equipment makers, cell manufacturers, and research institutes jointly optimizing laser parameters and process integration. As technical barriers are addressed and capital costs amortized over larger production volumes, excimer laser texturization is expected to transition from niche application to industry standard for premium solar cell lines.